Metal Injection Moulding (MIM) is revolutionizing the manufacturing landscape. Combining the versatility of plastic injection moulding with the strength and integrity of metal, MIM is a cutting-edge technology that offers unparalleled precision and complexity in creating metal parts. Whether you’re a seasoned engineer or simply curious about the intricacies of modern manufacturing, this article will delve deep into the world of MIM, offering insights, technical specifications, and practical applications. So, buckle up and get ready to explore the fascinating universe of Metal Injection Moulding!
Overview of Metal Injection Moulding (MIM)
Metal Injection Moulding (MIM) is a process that merges the benefits of metal powders with plastic injection moulding techniques. This method enables the production of small, intricate metal parts with complex geometries that would be challenging, if not impossible, to create using traditional metalworking techniques.
Key Benefits of MIM:
- High precision and complexity in design
- Efficient mass production capabilities
- Cost-effective for large volumes
- Superior mechanical properties compared to plastic parts
- Wide range of materials can be used
Process Summary:
- Feedstock Preparation: Metal powders are mixed with a thermoplastic binder to form a feedstock.
- Moulding: The feedstock is injected into a mould, forming the desired shape.
- Debinding: The binder is removed from the part.
- Sintering: The metal part is heated to a high temperature, bonding the metal particles together and resulting in a dense, solid component.
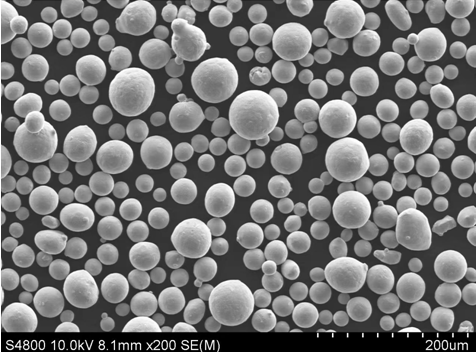
Types of Metal Powders Used in MIM
MIM is versatile and can use various types of metal powders. Below are ten specific metal powder models commonly used in MIM, along with their descriptions:
Metal Powder | Description |
---|---|
316L Stainless Steel | Known for its excellent corrosion resistance and high tensile strength. Ideal for medical and food processing applications. |
17-4 PH Stainless Steel | A precipitation-hardened steel that offers a great combination of strength and corrosion resistance. Used in aerospace and mechanical components. |
Carbonyl Iron Powder | High-purity iron with fine particle size, used for parts requiring high strength and magnetic properties. |
M2 Tool Steel | High-speed steel with excellent wear resistance and toughness. Commonly used for cutting tools and molds. |
Titanium Ti-6Al-4V | Lightweight with high strength and corrosion resistance. Preferred in aerospace, medical implants, and sports equipment. |
Cobalt-Chrome (CoCr) Alloy | Extremely hard and wear-resistant, suitable for dental implants and orthopedic devices. |
Inconel 625 | Nickel-based superalloy known for its high strength and resistance to oxidation and corrosion at high temperatures. Used in aerospace and chemical processing. |
Copper Alloy 90/10 | Known for its excellent thermal and electrical conductivity. Used in electrical components and heat exchangers. |
Nickel 718 | Nickel-chromium alloy that offers high strength and corrosion resistance, especially at high temperatures. Used in turbine engines and nuclear reactors. |
Aluminum Alloy 6061 | Lightweight with good mechanical properties and corrosion resistance. Commonly used in automotive and consumer electronics. |
Composition and Properties of Metal Injection Moulding (MIM)
Understanding the composition and properties of materials used in MIM is crucial for selecting the right metal powder for your application. Below is a detailed table highlighting the composition, properties, and characteristics of some popular MIM materials.
Composition and Properties of MIM Materials
Material | Composition | Properties | Characteristics |
---|---|---|---|
316L Stainless Steel | Fe, Cr, Ni, Mo | Corrosion-resistant, high strength | Non-magnetic, biocompatible |
17-4 PH Stainless Steel | Fe, Cr, Ni, Cu | High strength, corrosion-resistant | Magnetic, can be heat treated |
Carbonyl Iron Powder | Fe | High purity, magnetic properties | High strength, good wear resistance |
M2 Tool Steel | Fe, C, Mo, W, Cr, V | High wear resistance, toughness | Suitable for high-speed applications |
Titanium Ti-6Al-4V | Ti, Al, V | Lightweight, high strength | Biocompatible, corrosion-resistant |
Cobalt-Chrome (CoCr) Alloy | Co, Cr, Mo | Extremely hard, wear-resistant | Biocompatible, corrosion-resistant |
Inconel 625 | Ni, Cr, Mo, Nb | High strength, oxidation-resistant | Suitable for high-temperature applications |
Copper Alloy 90/10 | Cu, Ni | Excellent thermal, electrical conductivity | Good corrosion resistance |
Nickel 718 | Ni, Cr, Fe, Nb | High strength, corrosion-resistant | Excellent at high temperatures |
Aluminum Alloy 6061 | Al, Mg, Si | Lightweight, good mechanical properties | Good corrosion resistance, easy to machine |
Applications of Metal Injection Moulding (MIM)
MIM is used in a wide range of industries due to its versatility and ability to produce high-quality, complex parts. Here’s a look at some of the common applications of MIM:
Industrial Applications of MIM Materials
Industry | Application | Material Used |
---|---|---|
Medical | Surgical instruments, dental implants, orthopedic devices | 316L Stainless Steel, CoCr Alloy, Ti-6Al-4V |
Aerospace | Turbine blades, fasteners, structural components | Inconel 625, Titanium Ti-6Al-4V, 17-4 PH Stainless Steel |
Automotive | Fuel injectors, turbochargers, transmission parts | M2 Tool Steel, 17-4 PH Stainless Steel, Aluminum Alloy 6061 |
Consumer Electronics | Connectors, housings, heat sinks | Copper Alloy 90/10, Aluminum Alloy 6061 |
Defense | Firearm components, tactical gear | Carbonyl Iron Powder, 17-4 PH Stainless Steel, M2 Tool Steel |
Industrial Machinery | Cutting tools, molds, gears | M2 Tool Steel, 17-4 PH Stainless Steel, Carbonyl Iron Powder |
Energy | Nuclear reactor parts, oil and gas components | Nickel 718, Inconel 625, 17-4 PH Stainless Steel |
Jewelry | Watch cases, clasps, decorative items | 316L Stainless Steel, Titanium Ti-6Al-4V |
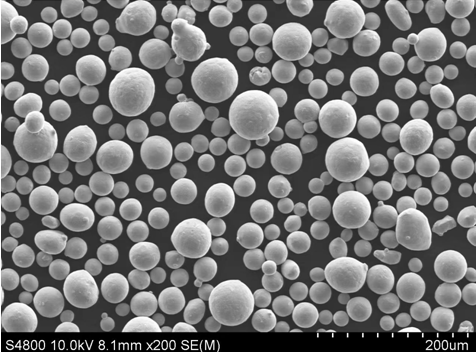
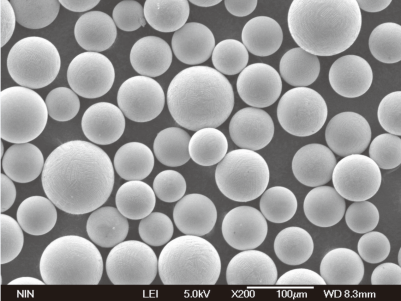
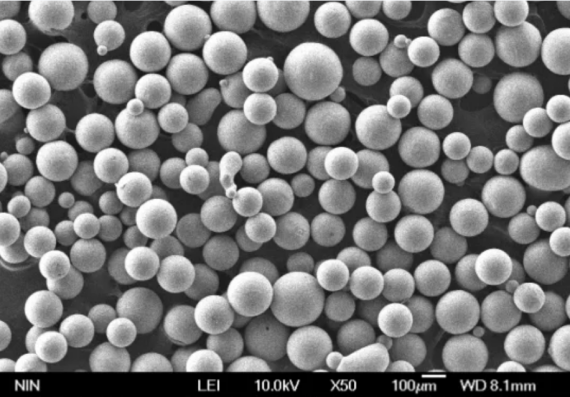
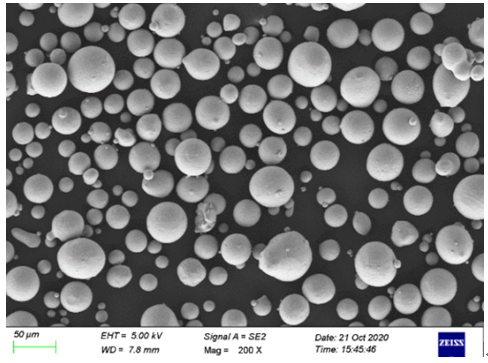
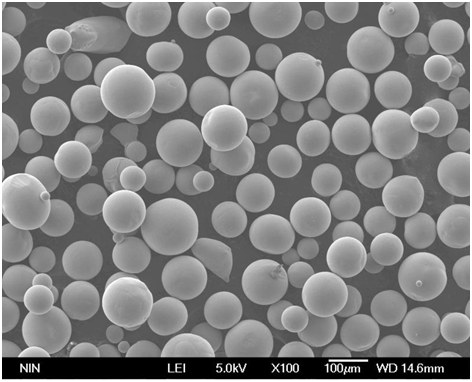
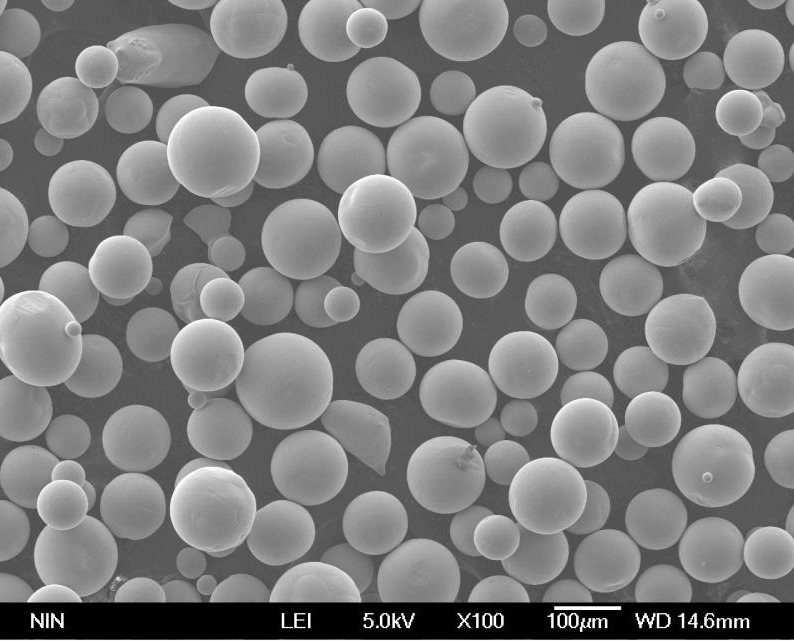
Specifications, Sizes, Grades, and Standards in MIM
When it comes to MIM, specifications, sizes, grades, and standards are critical to ensuring the right fit and performance for each application. Here’s a detailed look at these aspects for some common MIM materials.
Specifications and Standards for MIM Materials
Material | Specifications | Sizes | Grades | Standards |
---|---|---|---|---|
316L Stainless Steel | ASTM A276, ISO 5832-1 | 0.1mm to 100mm | Marine grade | ASTM F138 |
17-4 PH Stainless Steel | ASTM A564 | 0.1mm to 100mm | H900, H1025 | AMS 5643 |
Carbonyl Iron Powder | ASTM A131 | 0.1mm to 50mm | N/A | ASTM A848 |
M2 Tool Steel | ASTM A600 | 0.1mm to 50mm | T1, T2, T4 | ISO 4957 |
Titanium Ti-6Al-4V | ASTM B348 | 0.1mm to 100mm | Grade 5 | ASTM F136 |
Cobalt-Chrome (CoCr) Alloy | ASTM F75 | 0.1mm to 50mm | N/A | ISO 5832-4 |
Inconel 625 | ASTM B443 | 0.1mm to 50mm | N/A | AMS 5666 |
Copper Alloy 90/10 | ASTM B111 | 0.1mm to 100mm | C70600 | ASME SB111 |
Nickel 718 | ASTM B670 | 0.1mm to 50mm | N/A | AMS 5662 |
Aluminum Alloy 6061 | ASTM B221 | 0.1mm to 200mm | T6, T651 | AMS 4150 |
Suppliers and Pricing Details of MIM Materials
Finding the right supplier and understanding the cost implications is vital for any manufacturing process. Below is a table listing some reputable suppliers and indicative pricing for popular MIM materials.
Suppliers and Pricing for MIM Materials
Material | Supplier | Price Range (per kg) | Notes |
---|---|---|---|
316L Stainless Steel | Carpenter Technology, Sandvik | $20 – $30 | Varies with quantity and purity |
17-4 PH Stainless Steel | Allegheny Technologies, Precision Castparts Corp. | $25 – $35 | Prices vary by heat treatment condition |
Carbonyl Iron Powder | BASF, Höganäs AB | $15 – $25 | Dependent on particle size and purity |
M2 Tool Steel | Bohler-Uddeholm, Hitachi Metals | $30 – $45 | Prices fluctuate based on alloying elements |
Titanium Ti-6Al-4V | VSMPO-AVISMA, ATI Metals | $50 – $70 | Price varies with form and grade |
Cobalt-Chrome (CoCr) Alloy | Arcam AB, Carpenter Technology | $80 – $100 | High demand in medical and aerospace |
Inconel 625 | Special Metals, Haynes International | $40 – $60 | Cost depends on form (powder, bar, etc.) |
Copper Alloy 90/10 | Wieland Group, Mueller Industries | $10 – $20 | Prices can vary with copper market |
Nickel 718 | ATI Metals, VDM Metals | $50 – $70 | Price affected by nickel content |
Aluminum Alloy 6061 | Kaiser Aluminum, Hydro Extrusions | $5 – $10 | Widely used, hence competitive pricing |
Comparing Pros and Cons of Metal Injection Moulding (MIM)
Every manufacturing process has its advantages and limitations. Let’s break down the pros and cons of MIM to help you understand where it shines and where it might fall short.
Advantages and Limitations of MIM
Aspect | Advantages | Limitations |
---|---|---|
Design Flexibility | Can produce complex shapes | Limited by part size and weight |
Material Variety | Wide range of metals | Some materials are expensive |
Precision and Tolerance | High precision achievable | Requires precise control of process parameters |
Production Volume | Cost-effective for large volumes | Not economical for low quantities |
Mechanical Properties | Excellent mechanical properties | Properties depend on material and process control |
Surface Finish | Smooth finish achievable | May require post-processing for very fine finishes |
Environmental Impact | Efficient material usage, less waste | Energy-intensive process, especially in sintering |
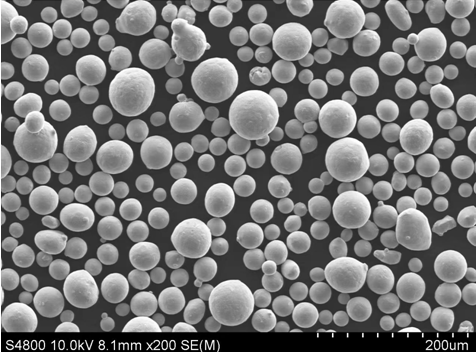
FAQ
Question | Answer |
---|---|
What is Metal Injection Moulding (MIM)? | MIM is a manufacturing process that combines metal powders with plastic injection moulding techniques to create intricate metal parts. |
What are the main benefits of MIM? | MIM offers high precision, complex designs, cost-effectiveness for large volumes, and superior mechanical properties. |
Which industries use MIM the most? | MIM is widely used in medical, aerospace, automotive, consumer electronics, defense, industrial machinery, energy, and jewelry industries. |
What materials can be used in MIM? | A wide range of materials including stainless steels, tool steels, titanium, nickel alloys, cobalt-chrome, and more can be used in MIM. |
How does MIM compare to traditional metalworking? | MIM allows for more complex designs and higher precision than many traditional methods. However, it may be more costly for low-volume production. |
What are the limitations of MIM? | MIM is limited by part size and weight, material cost, and requires precise process control. |
Is MIM environmentally friendly? | MIM uses materials efficiently with less waste, but the process, particularly sintering, can be energy-intensive. |
Conclusion
Metal Injection Moulding (MIM) stands out as a transformative technology in modern manufacturing, offering unparalleled advantages in creating complex, high-precision metal parts. By understanding the materials, process, applications, and limitations of MIM, manufacturers can make informed decisions that drive innovation and efficiency in their operations. Whether you are looking to produce medical implants, aerospace components, or intricate industrial tools, MIM provides a versatile and effective solution. So, dive into the world of MIM and explore how this technology can elevate your manufacturing capabilities to new heights.