When it comes to high-performance alloys used in extreme environments, Haynes 188 Powder stands out as a leading choice. Whether you’re working in aerospace, power generation, or any other industry requiring materials that can withstand extreme heat, Haynes 188 Powder is renowned for its heat resistance, oxidation resistance, and creep strength. But what makes this powder truly unique, and why should you consider it for your next high-temperature project?
This comprehensive guide will take you through everything you need to know about Haynes 188 Powder. We will explore its composition, properties, applications, and even compare it to other popular metal powders. So, buckle up and let’s dive into the world of cobalt-based superalloys.
Overview of Haynes 188 Powder
Haynes 188 Powder is a cobalt-based superalloy known for its outstanding high-temperature performance. It’s widely used in environments where oxidation resistance and thermal stability are crucial. The powder form of Haynes 188 makes it ideal for additive manufacturing, allowing for the creation of intricate shapes and components with ease.
Key Attributes:
- Excellent oxidation resistance up to 1095°C (2000°F)
- Good high-temperature strength
- Superior thermal fatigue resistance
- Outstanding creep and oxidation resistance
- Ideal for aerospace, gas turbines, and combustion chamber liners
Common Uses:
- Aerospace components like combustors and afterburners
- Power generation applications
- Industrial furnaces and thermal barrier coatings
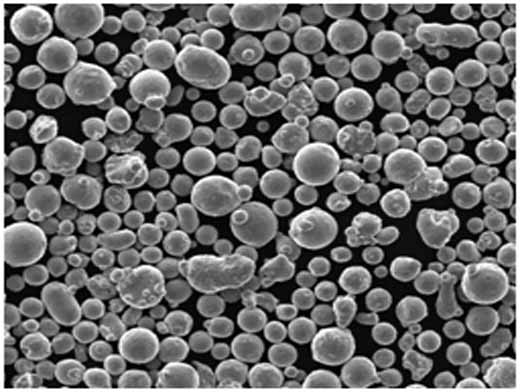
Composition of Haynes 188 Powder
The key to understanding why Haynes 188 Powder performs so well lies in its composition. This cobalt-based alloy is specifically engineered to resist extreme environmental conditions.
Element | Composition (%) |
---|---|
Cobalt (Co) | Balance |
Chromium (Cr) | 22.0 |
Nickel (Ni) | 22.0 |
Tungsten (W) | 14.0 |
Lanthanum (La) | 0.03 |
Carbon (C) | 0.10 |
Silicon (Si) | 0.35 |
Manganese (Mn) | 1.25 |
What makes this composition special?
- Chromium enhances the material’s resistance to oxidation and corrosion.
- Nickel improves the alloy’s overall stability at high temperatures.
- Tungsten adds strength, particularly in high-heat applications.
- Lanthanum boosts oxidation resistance and contributes to the alloy’s longevity.
Each element is strategically included to give Haynes 188 Powder its high-performance capabilities, especially in extreme environments.
Characteristics of Haynes 188 Powder
Now that we know what’s inside Haynes 188 Powder, let’s look at its physical and mechanical characteristics.
Property | Value |
---|---|
Melting Range | 1330°C – 1410°C |
Density | 8.90 g/cm³ |
Tensile Strength at Room Temp | 895 MPa (130 ksi) |
Yield Strength at Room Temp | 430 MPa (62 ksi) |
Elongation | 45% |
Hardness (Rockwell C) | 24 |
Thermal Expansion Coefficient | 12.8 μm/m°C (up to 800°C) |
Thermal Conductivity | 10.7 W/m-K |
Oxidation Resistance | Up to 1095°C |
Notable Characteristics:
- High Strength and Ductility: Offers superior mechanical strength combined with excellent ductility, making it ideal for parts subjected to high stress.
- Thermal Stability: Withstands extreme temperatures without losing its mechanical integrity.
- Creep Resistance: Excellent creep resistance ensures the alloy retains its shape under prolonged exposure to heat.
Applications of Haynes 188 Powder
Thanks to its remarkable properties, Haynes 188 Powder is a go-to choice in industries where heat resistance and oxidation protection are paramount. Let’s explore the specific industries and applications where this superalloy truly shines.
Application | Details |
---|---|
Aerospace | Combustion chambers, afterburners, exhaust nozzles, gas turbines |
Power Generation | Gas turbine blades, hot gas paths, combustion liners |
Industrial Furnaces | Components exposed to high temperatures and oxidative environments |
Additive Manufacturing (3D Printing) | Producing complex shapes for aerospace and power generation applications |
Chemical Processing | Heat exchangers, reactors, and other equipment in corrosive environments |
In the aerospace industry, Haynes 188 Powder is commonly used in the manufacture of combustors and turbine sections of aircraft engines. Power generation plants also rely heavily on this superalloy due to its excellent heat-resistance properties.
Additive Manufacturing:
One of the key benefits of Haynes 188 in powder form is its adaptability to additive manufacturing or 3D printing. This enables the production of intricate, high-performance parts with minimal waste, making it both cost-effective and environmentally friendly.
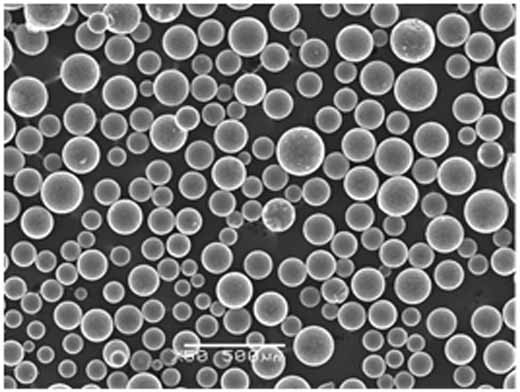
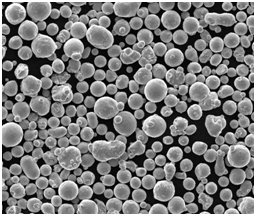
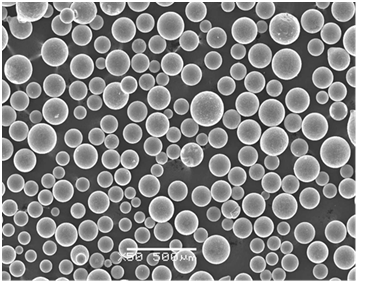
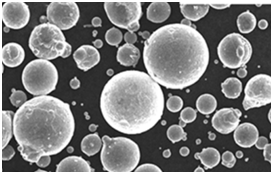
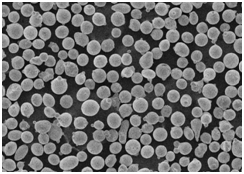
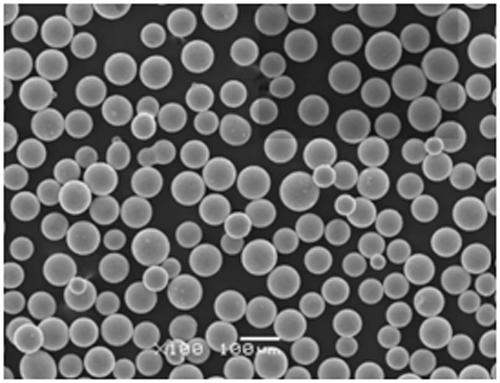
Popular Metal Powder Models: Haynes 188 Powder and Alternatives
Let’s compare Haynes 188 with other popular metal powder models commonly used in high-temperature applications.
Metal Powder | Composition | Notable Properties | Applications |
---|---|---|---|
Haynes 188 | Co, Cr, Ni, W, La | High heat resistance, oxidation resistance | Aerospace, power generation, furnaces |
Inconel 625 | Ni, Cr, Mo, Nb | Excellent corrosion and oxidation resistance | Marine, chemical processing, nuclear reactors |
Inconel 718 | Ni, Cr, Mo, Fe | High strength, fatigue, and creep resistance at elevated temps | Jet engines, spacecraft, turbines |
Haynes 230 | Co, Cr, W, Mo | Good thermal stability, oxidation resistance up to 1200°C | Aerospace, chemical processing, power plants |
Haynes 282 | Ni, Cr, Mo, Ti | Excellent weldability and thermal stability | Gas turbines, combustion liners |
Hastelloy X | Ni, Cr, Fe, Mo, Co | High oxidation resistance and good formability | Jet engine components, furnace applications |
Tungsten Carbide (WC) | W, C | Extreme hardness, high melting point | Cutting tools, wear-resistant applications |
Nickel 625 Powder | Ni, Cr, Mo, Nb | High corrosion resistance, weldability | Chemical processing, marine industries |
Stellite 6B | Co, Cr, W, Mo | Excellent wear resistance, toughness | Cutting tools, saw blades, wear parts |
Cobalt Chrome | Co, Cr | High wear resistance, biocompatibility | Medical implants, dental applications |
Advantages of Haynes 188 Powder
Haynes 188 Powder has many advantages over other high-performance metal powders. Let’s take a closer look at what makes it the superior choice in extreme conditions.
1. High-Temperature Strength
Compared to other alloys, Haynes 188 excels at maintaining its strength in extreme heat. While some materials soften at high temperatures, Haynes 188 can withstand continuous operation up to 1095°C.
2. Oxidation Resistance
The high chromium and nickel content in the alloy gives it excellent resistance to oxidation, even in extreme environments. This is crucial in industries like aerospace and power generation where components are exposed to oxygen-rich atmospheres at high temperatures.
3. Creep Resistance
When compared to other superalloys like Inconel 625 or Hastelloy X, Haynes 188 shows better creep resistance. This means the alloy maintains its structural integrity even under long-term stress at elevated temperatures.
4. Versatility in Additive Manufacturing
As a powder, Haynes 188 is especially suitable for 3D printing, allowing for the production of complex, high-precision parts with minimal waste.
Limitations of Haynes 188 Powder
Of course, no material is perfect. Let’s explore some of the potential limitations of Haynes 188 Powder.
1. Cost
One of the main drawbacks of Haynes 188 Powder is its cost. The presence of cobalt and tungsten makes it relatively more expensive than other superalloys like Inconel 718. However, the longevity and performance benefits often justify the higher price.
2. Weldability
While Haynes 188 can be welded, it doesn’t offer the same level of weldability as some other nickel-based alloys
like Inconel 625. This can be a challenge in applications requiring a lot of welding work.
3. Limited Corrosion Resistance
Although it performs exceptionally well at high temperatures, Haynes 188 isn’t as resistant to corrosion as other alloys like Hastelloy X, particularly in marine or highly acidic environments.
Specifications, Sizes, Grades, and Standards of Haynes 188 Powder
Here are some of the key specifications and standards associated with Haynes 188 Powder.
Specification | Details |
---|---|
Density | 8.90 g/cm³ |
Melting Range | 1330°C – 1410°C |
Standard Sizes | Available in a variety of mesh sizes for 3D printing |
ASTM Standards | ASTM F75, ASTM B637 |
Typical Grades | AMS 5608, AMS 5801, AMS 5943 |
Applicable Standards | ISO 9001:2015, AS 9100D, NADCAP |
Suppliers and Pricing Details of Haynes 188 Powder
When sourcing Haynes 188 Powder, it’s important to look for reputable suppliers to ensure you’re getting a high-quality product. Below are some well-known suppliers along with an estimated price range.
Supplier | Price Range (USD/kg) | Region | Certification |
---|---|---|---|
Carpenter Technology | $150 – $300 | USA | ISO 9001, AS 9100, NADCAP |
Höganäs | $180 – $320 | Europe, Global | ISO 9001, AS 9100 |
Praxair | $170 – $280 | USA, Global | ISO 9001, NADCAP |
EOS | $200 – $350 | Germany, Global | ISO 9001 |
Kennametal | $160 – $310 | USA | AS 9100, ISO 14001 |
Prices vary based on factors like purity, particle size, and supplier certifications. Larger orders typically receive discounts, and additional services like custom blending or mesh sizing may increase the price.
Pros and Cons of Haynes 188 Powder
When deciding whether Haynes 188 Powder is the right material for your project, it’s important to weigh its pros and cons.
Pros | Cons |
---|---|
Exceptional heat and oxidation resistance | Relatively expensive compared to others |
Strong at high temperatures | Limited corrosion resistance |
Creep resistant | Weldability is not as easy as some other alloys |
Ideal for additive manufacturing | Requires specialized handling and processing due to cost |
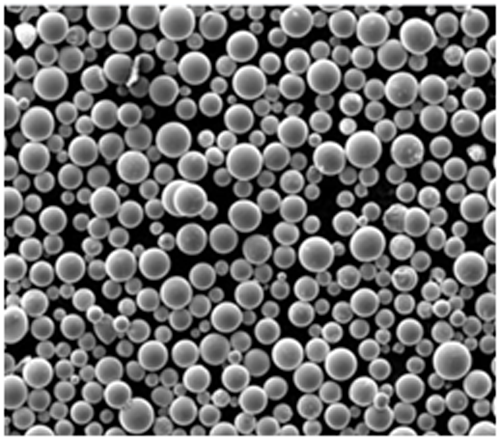
FAQs
Here’s a quick FAQ section to answer some of the most common questions people have about Haynes 188 Powder.
Question | Answer |
---|---|
What is Haynes 188 Powder used for? | It’s used in aerospace, power generation, and industrial furnaces, primarily for high-heat components. |
How does it compare to Inconel 625? | Haynes 188 offers better creep resistance at high temperatures, while Inconel 625 has superior corrosion resistance. |
Can Haynes 188 Powder be 3D printed? | Yes, Haynes 188 Powder is commonly used in additive manufacturing for complex, heat-resistant parts. |
Is Haynes 188 Powder expensive? | Yes, due to its composition (high cobalt and tungsten content), it is generally more expensive than other superalloys. |
What temperature can Haynes 188 withstand? | It can withstand temperatures up to 1095°C (2000°F), making it suitable for extreme environments. |
Is Haynes 188 easy to weld? | While it can be welded, it is not as easy to weld as other nickel-based alloys like Inconel 625. |
Where can I buy Haynes 188 Powder? | You can buy it from suppliers like Carpenter Technology, Höganäs, and EOS. Prices vary depending on supplier and order size. |