Overview: Understanding NiCrBSi Powder
Nickel-chromium-boron-silicon (NiCrBSi) powder is a vital material in industrial applications due to its impressive combination of properties, such as excellent wear resistance, corrosion resistance, and high-temperature performance. NiCrBSi powders are often used in thermal spray coatings, particularly for parts that are exposed to extreme operating conditions. These powders are widely utilized in sectors like aerospace, oil and gas, and manufacturing, where durability and longevity of components are paramount.
In this guide, we’ll take a deep dive into the world of NiCrBSi powder. We will explore its composition, specific metal powder models, key properties, applications, advantages, and disadvantages. We will also provide tables to compare types, compositions, grades, and pricing. Let’s jump right into it!
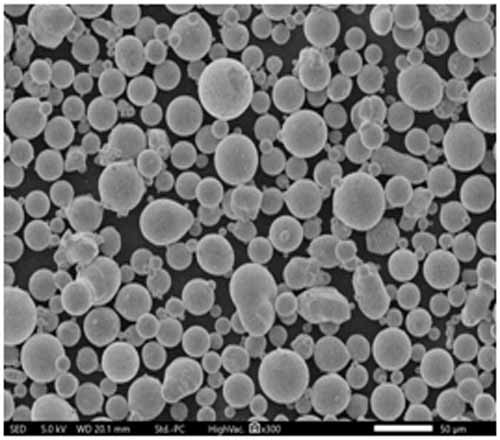
Composition of NiCrBSi Powder
NiCrBSi powder is composed of a mixture of metals and metalloids, mainly nickel (Ni), chromium (Cr), boron (B), and silicon (Si). Each of these elements contributes to the overall performance of the powder in various ways:
- Nickel (Ni): Provides corrosion resistance and toughness.
- Chromium (Cr): Improves oxidation resistance and enhances wear performance.
- Boron (B): Acts as a melting point reducer and a hardening agent.
- Silicon (Si): Adds to the oxidation resistance and improves flowability during thermal spraying.
The specific ratios of these components can vary, influencing the overall properties and suitability for different applications.
Common Compositions of NiCrBSi Powder
Component | Range (%) | Function |
---|---|---|
Nickel (Ni) | 60-80 | Corrosion resistance, ductility |
Chromium (Cr) | 10-20 | Wear resistance, oxidation resistance |
Boron (B) | 1-4 | Hardness, reduction of melting point |
Silicon (Si) | 3-5 | Flowability, oxidation resistance |
Carbon (C) | 0.5-1 | Enhances hardness and toughness |
The above table illustrates a typical composition range for NiCrBSi powders. These percentages can be fine-tuned depending on the required performance, environment, and specific industrial needs.
Characteristics of NiCrBSi Powder
NiCrBSi powder exhibits several key characteristics that make it a preferred choice for surface coatings and repair applications. Let’s explore the most significant characteristics:
- Excellent Wear Resistance: Due to the presence of hard phases, such as borides and carbides, NiCrBSi coatings provide outstanding wear resistance. This is particularly important for components exposed to abrasion, erosion, or sliding wear.
- High-Temperature Stability: NiCrBSi powders can withstand temperatures up to 1000°C, making them suitable for high-temperature applications like turbine blades or furnace parts.
- Corrosion and Oxidation Resistance: The combination of nickel and chromium provides excellent protection against corrosive environments, including exposure to acids and salts.
- Self-Fluxing Properties: NiCrBSi powders have self-fluxing characteristics due to the boron and silicon content, which allows the material to form a uniform, defect-free coating during thermal spraying.
- Bonding Strength: The powders exhibit strong adhesion to base materials, ensuring that coatings remain intact even in harsh operating conditions.
Key Characteristics of NiCrBSi Powder
Characteristic | Description |
---|---|
Wear Resistance | High due to hard phases (borides, carbides) |
Temperature Resistance | Withstands up to 1000°C |
Corrosion Resistance | Excellent due to nickel and chromium content |
Oxidation Resistance | High resistance to oxidation in high-temperature environments |
Self-Fluxing | Allows smooth, defect-free coatings |
Bonding Strength | Strong adhesion to substrates, minimal risk of delamination or cracking |
Specific Metal Powder Models of NiCrBSi
When selecting the appropriate NiCrBSi powder, it is essential to consider specific models that match your application. Each model may vary slightly in composition or particle size, influencing its performance. Below are 10 popular NiCrBSi powder models with their descriptions:
- Metco 16C
- Description: Known for its excellent wear and corrosion resistance, Metco 16C is ideal for high-temperature environments such as gas turbines. It has a high chromium content to further enhance its oxidation resistance.
- Applications: Turbine blades, boiler tubes, and petrochemical equipment.
- Praxair NiCrBSi-180
- Description: A versatile powder with a medium particle size. It provides a balance of hardness and toughness, making it suitable for general-purpose coatings.
- Applications: Agricultural machinery, mining equipment, and pump components.
- Höganäs AMPERIT 578
- Description: Offers higher boron content, resulting in superior hardness and wear resistance. Commonly used in extreme wear environments.
- Applications: Hydraulic cylinders, valves, and oilfield tools.
- Deloro 50
- Description: A popular powder due to its fine particle distribution. Deloro 50 is favored for thermal spraying and laser cladding, providing excellent surface finish.
- Applications: Printing rolls, paper industry equipment, and cutting tools.
- Powder Alloy 1276F
- Description: Features high flowability, making it ideal for plasma spraying. It forms dense, high-quality coatings with minimal porosity.
- Applications: Automotive parts, aerospace components, and chemical processing equipment.
- Wall Colmonoy 88F
- Description: Known for its self-fluxing properties, Wall Colmonoy 88F can be applied using various thermal spray techniques, offering excellent wear and corrosion resistance.
- Applications: Glass molds, forming tools, and food processing machinery.
- Oerlikon Metco 12C
- Description: With high chromium and silicon content, Metco 12C is optimized for environments where oxidation and corrosion are significant concerns.
- Applications: Furnace parts, exhaust systems, and heat exchangers.
- Praxair NiCrBSi-400
- Description: This powder features a coarser particle size for thicker coatings. It is often used in applications requiring significant wear protection.
- Applications: Crusher hammers, mining screens, and rail tracks.
- Sandvik 9562
- Description: Sandvik 9562 is a versatile NiCrBSi powder that excels in laser cladding applications due to its excellent flow characteristics and uniform particle distribution.
- Applications: Drilling equipment, offshore rigs, and heavy machinery.
- AMPERIT 595.4
- Description: A fine-grained NiCrBSi powder offering superior surface finish and hardness. It is suitable for precision components in demanding industries.
- Applications: Aerospace, medical devices, and power generation turbines.
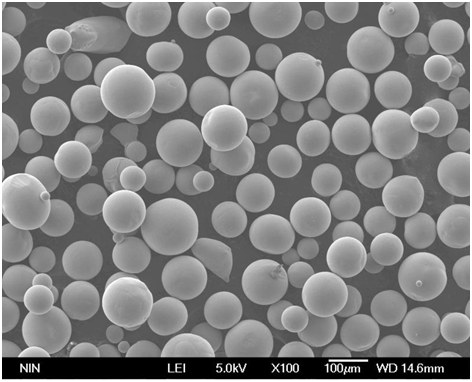
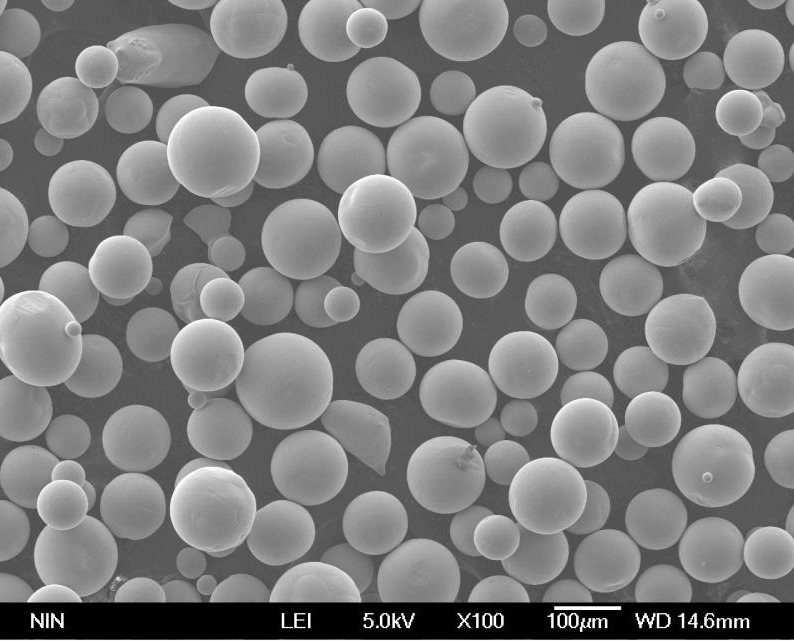
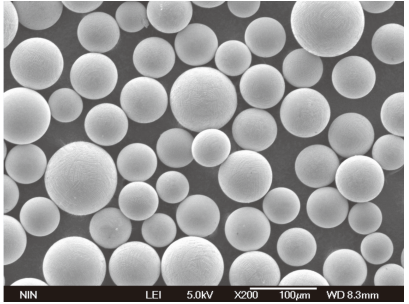
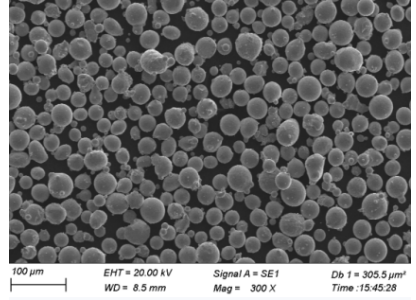

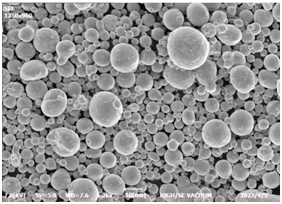
Advantages of NiCrBSi Powder
NiCrBSi powder stands out in the world of thermal coatings due to a number of distinct advantages:
1. Versatility in Application
NiCrBSi powders can be applied using various thermal spraying techniques like plasma spraying, high-velocity oxy-fuel (HVOF), and laser cladding. This makes it adaptable across multiple industries and applications.
2. Enhanced Durability
The unique combination of elements results in coatings that resist wear, corrosion, and oxidation, significantly extending the life of parts and components exposed to harsh environments.
3. High Bonding Strength
Coatings made from NiCrBSi powders form strong bonds with base materials, making them less likely to peel or crack, even under extreme conditions.
4. Cost-Efficiency
Due to their long-lasting nature, NiCrBSi coatings reduce the need for frequent part replacements, lowering overall maintenance costs for industrial operations.
Applications of NiCrBSi Powder
NiCrBSi powder is used in a wide range of industries, primarily for protective coatings. Below is a table illustrating common applications of NiCrBSi powder across various sectors.
Table 3: Applications of NiCrBSi Powder by Industry
Industry | Applications |
---|---|
Aerospace | Turbine blades, exhaust systems, heat shields |
Oil and Gas | Valves, drilling tools, pipeline components |
Automotive | Engine components, cylinder heads, fuel injectors |
Manufacturing | Cutting tools, machine parts, extrusion dies |
Energy | Power generation turbines, boiler tubes, heat exchangers |
Food Processing | Mixers, slicers, forming tools |
Paper and Printing | Printing rolls, dryer cylinders |
Mining | Crusher hammers, drilling equipment, conveyor systems |
Petrochemical | Reactors, flanges, storage tanks |
Grades and Specifications of NiCrBSi Powder
Different grades of NiCrBSi powders are available depending on the composition and particle size. These grades are typically standardized by manufacturers to meet the specific needs of various industries.
Table 4: Common Grades of NiCr BSi Powder
Grade | Particle Size (μm) | Melting Point (°C) | Application |
---|---|---|---|
NiCrBSi-180 | 45-106 | 980-1050 | General-purpose coatings |
NiCrBSi-250 | 63-150 | 950-1020 | Wear-resistant coatings |
NiCrBSi-400 | 150-250 | 920-1000 | Heavy-duty coatings |
NiCrBSi-88F | 15-53 | 980-1060 | Thin coatings for high-precision parts |
Pricing and Suppliers of NiCrBSi Powder
Pricing for NiCrBSi powder depends on several factors, including grade, particle size, and quantity. The cost typically ranges between $50 to $200 per kilogram depending on the specifications.
Table 5: Suppliers and Pricing for NiCrBSi Powder
Supplier | Grade Available | Price (per kg) | Contact Info |
---|---|---|---|
Höganäs | AMPERIT 578 | $150-$180 | www.hoganas.com |
Praxair | NiCrBSi-180, NiCrBSi-400 | $100-$140 | www.praxair.com |
Wall Colmonoy | 88F, 50 | $120-$170 | www.wallcolmonoy.com |
Oerlikon Metco | Metco 16C, Metco 12C | $130-$200 | www.oerlikon.com |
Sandvik | 9562 | $80-$150 | www.home.sandvik |
Comparing NiCrBSi Powder to Other Thermal Spray Powders
When it comes to comparing NiCrBSi powder with other thermal spray powders, there are clear distinctions in terms of performance, cost, and applications.
Table 6: NiCrBSi vs Other Common Thermal Spray Powders
Parameter | NiCrBSi Powder | WC-Co Powder | Aluminum Oxide Powder |
---|---|---|---|
Wear Resistance | Excellent (due to borides) | Outstanding | Moderate |
Corrosion Resistance | High (nickel and chromium content) | Moderate | Low |
Oxidation Resistance | High | Moderate | Low |
Temperature Resistance | Up to 1000°C | Up to 800°C | Up to 650°C |
Cost | Medium ($80-$200 per kg) | High ($200-$400 per kg) | Low ($30-$60 per kg) |
Pros and Cons of NiCrBSi Powder
NiCrBSi powder has its share of strengths and weaknesses, depending on the application and environment.
Table 7: Advantages and Disadvantages of NiCrBSi Powder
Advantages | Disadvantages |
---|---|
Exceptional wear and corrosion resistance | Can be more expensive than simpler powders |
Excellent high-temperature performance | Requires specialized equipment for thermal spraying |
Versatile in applications across many industries | Some grades may have limited availability |
Strong bonding to base materials | Careful control of process parameters is necessary |
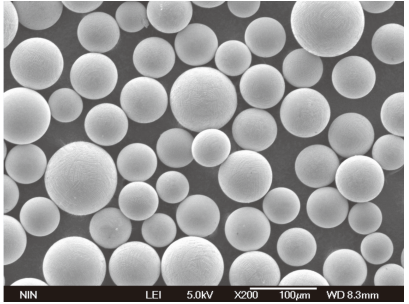
FAQ
Question | Answer |
---|---|
What are the primary uses of NiCrBSi powder? | NiCrBSi powder is used in protective coatings for components in aerospace, automotive, and oil industries. |
How is NiCrBSi powder applied? | It is applied through thermal spraying techniques such as plasma spraying, HVOF, or laser cladding. |
Why is NiCrBSi powder considered versatile? | It offers excellent wear, corrosion, and temperature resistance, making it suitable for various environments. |
What is the cost range for NiCrBSi powder? | Depending on the grade and supplier, NiCrBSi powder costs between $80 to $200 per kilogram. |
Can NiCrBSi powder be used in high-temperature applications? | Yes, NiCrBSi powders can withstand temperatures up to 1000°C. |
How long do NiCrBSi coatings last? | Coatings made from NiCrBSi can last several years depending on the operating environment and maintenance. |
Are NiCrBSi powders environmentally friendly? | NiCrBSi powders are generally considered eco-friendly as they help extend the life of parts, reducing waste. |
Conclusion
NiCrBSi powder stands out as a highly versatile, durable, and corrosion-resistant material. It finds widespread applications across industries where components are exposed to harsh conditions. By offering superior wear resistance, strong bonding, and high-temperature stability, NiCrBSi powders provide a cost-effective solution for extending the life of equipment and reducing maintenance costs.
Whether you’re dealing with extreme wear in mining equipment or high-temperature environments in aerospace, selecting the right grade and supplier of NiCrBSi powder can significantly enhance performance and efficiency.