High-strength steel powder is a material that plays a crucial role in various industries, from automotive to aerospace. Its unique properties, combined with technological advancements, have enabled engineers and manufacturers to create components that are not only stronger but also lighter and more durable. In this comprehensive guide, we’ll dive deep into what high-strength steel powder is, its composition, characteristics, applications, and much more. So, whether you’re a seasoned professional or just curious, stick around—this is going to be an informative journey.
Overview of High-Strength Steel Powder
High-strength steel powder is a form of metal powder specifically designed to offer exceptional mechanical properties, such as high tensile strength, hardness, and resistance to wear and fatigue. This powder is typically used in advanced manufacturing techniques like additive manufacturing (3D printing), powder metallurgy, and metal injection molding, where its fine granularity allows for precise and complex shapes to be formed.
High-strength steel powders are produced through various methods, including atomization, which involves the breaking up of molten steel into tiny droplets that solidify into powder form. The powder’s specific composition can be tailored to meet the demands of different applications, ranging from highly durable automotive parts to lightweight aerospace components.
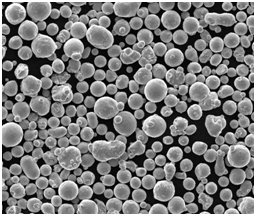
Types of High-Strength Steel Powder, Composition, Properties, and Characteristics
Model | Composition | Properties | Characteristics |
---|---|---|---|
HSLA-100 | Iron, Carbon, Manganese, Nickel, Chromium | High tensile strength, corrosion resistance | Excellent for marine applications, weldable |
CPM 3V | Iron, Carbon, Vanadium | Exceptional toughness, wear resistance | Ideal for cutting tools and wear parts |
Maraging 300 | Iron, Nickel, Cobalt, Molybdenum | High yield strength, good weldability | Suitable for aerospace, high-performance gears |
17-4 PH | Iron, Chromium, Nickel, Copper | High strength, corrosion resistance | Used in aerospace, chemical processing |
Aermet 100 | Iron, Nickel, Cobalt, Chromium | Ultra-high strength, fracture toughness | Used in landing gear, aerospace structures |
H13 Tool Steel | Iron, Carbon, Chromium, Vanadium | High toughness, thermal fatigue resistance | Common in die casting and extrusion tools |
S136H | Iron, Carbon, Chromium | High hardness, corrosion resistance | Used in plastic molds, excellent polishability |
M300 Maraging Steel | Iron, Nickel, Cobalt, Molybdenum | High strength, good ductility | Suitable for high-stress applications |
D2 Tool Steel | Iron, Carbon, Chromium, Vanadium | High hardness, wear resistance | Ideal for stamping and forming tools |
PMD-100 | Iron, Carbon, Molybdenum, Nickel | Balanced toughness and wear resistance | Versatile for automotive and industrial use |
Composition of High-Strength Steel Powder
The composition of high-strength steel powder is carefully engineered to achieve specific mechanical properties. Common elements used in these powders include iron, carbon, chromium, nickel, vanadium, cobalt, and molybdenum. Each element contributes to the powder’s overall performance:
- Iron (Fe): The primary component in steel, providing the base structure.
- Carbon (C): Increases hardness and strength through the formation of carbides.
- Chromium (Cr): Enhances corrosion resistance and hardness.
- Nickel (Ni): Improves toughness and impact resistance.
- Vanadium (V): Increases wear resistance and strength at high temperatures.
- Cobalt (Co): Improves high-temperature stability and magnetic properties.
- Molybdenum (Mo): Enhances strength and hardenability, especially at elevated temperatures.
These elements are combined in varying proportions to create steel powders that meet the needs of specific applications. For example, high carbon content increases hardness, while the addition of chromium can significantly enhance corrosion resistance, making the steel powder suitable for use in harsh environments.
Characteristics of High-Strength Steel Powder
High-strength steel powders are defined by their unique set of characteristics, which include:
- High Tensile Strength: These powders are designed to withstand significant stretching or pulling forces without breaking.
- Corrosion Resistance: Many high-strength steel powders are resistant to rust and other forms of corrosion, making them ideal for use in marine or chemical environments.
- Wear Resistance: High-strength steel powders are often used in applications where the material will face repeated mechanical wear.
- Fatigue Resistance: The ability to endure cyclic loading without failure is crucial for components that experience repetitive stress.
- Hardness: These powders can be treated to achieve very high hardness levels, making them suitable for cutting tools and molds.
- Ductility: Despite their strength, many of these powders maintain good ductility, allowing them to be shaped and formed without cracking.
These characteristics make high-strength steel powders indispensable in industries where durability, precision, and reliability are paramount.
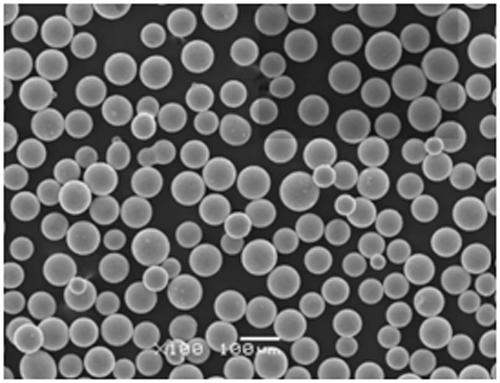
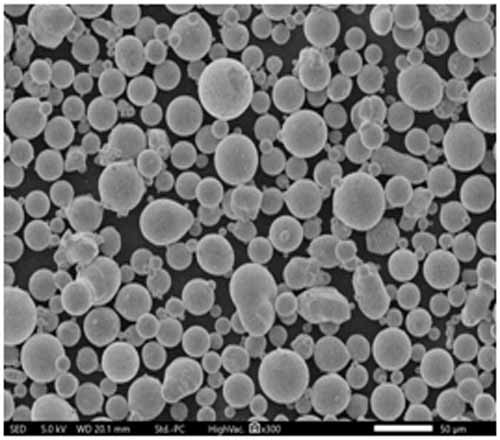
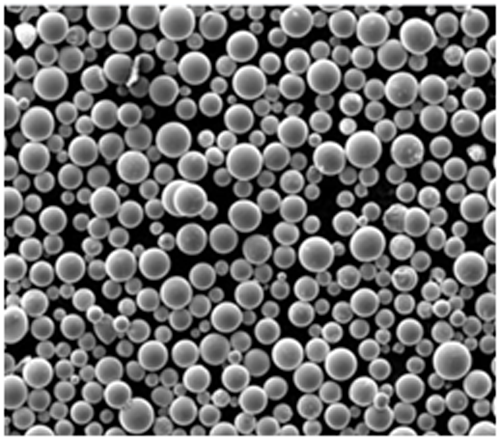
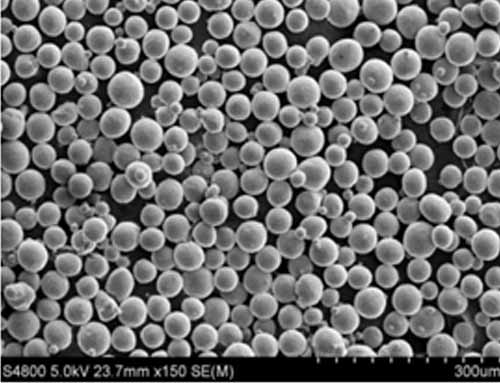
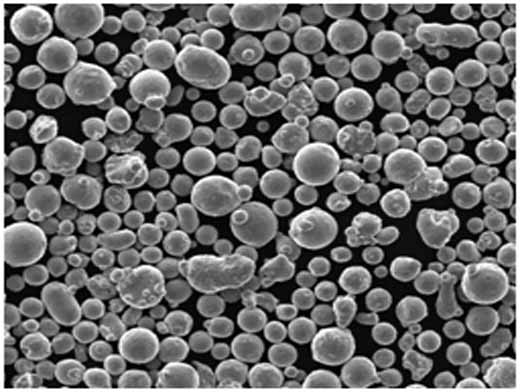
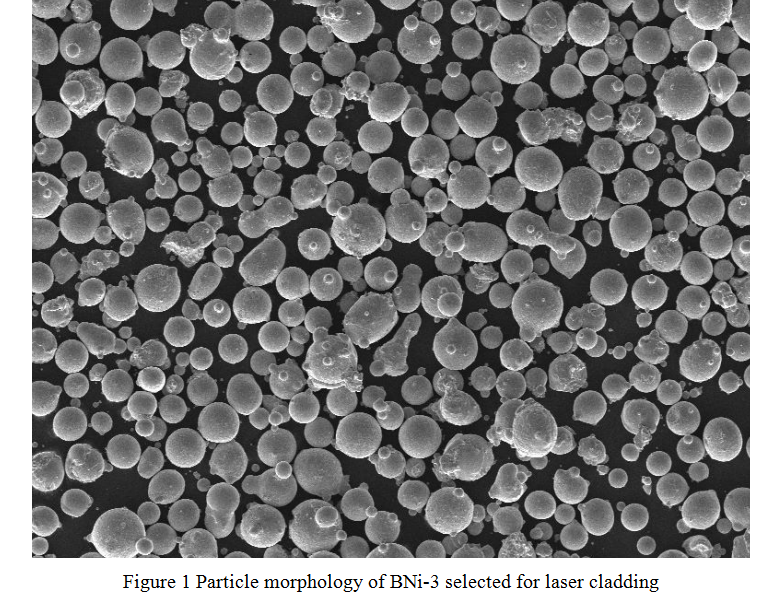
Applications of High-Strength Steel Powder
The versatility of high-strength steel powders allows them to be used across various industries, each benefiting from their unique properties. Here’s how these powders are applied in different sectors:
Automotive Industry:
- High-strength structural components: Used in the production of lightweight yet strong chassis and body parts.
- Engine parts: Provides wear resistance in critical components like camshafts and gears.
Aerospace Industry:
- Landing gear: The ultra-high strength and toughness of specific powders like Aermet 100 make them perfect for landing gear components.
- Structural components: Used in airframes where high strength-to-weight ratios are essential.
Tooling and Molding:
- Die casting molds: Powders like H13 Tool Steel are ideal due to their thermal fatigue resistance.
- Injection molding: S136H steel powder is preferred for plastic molds requiring high polishability and corrosion resistance.
Marine Applications:
- Corrosion-resistant parts: HSLA-100 is commonly used in naval structures due to its excellent weldability and resistance to seawater corrosion.
- Offshore drilling equipment: The combination of strength and corrosion resistance makes these powders ideal for harsh marine environments.
Industrial Machinery:
- Wear parts: CPM 3V steel powder offers superior wear resistance, making it suitable for cutting tools and industrial machines.
- Heavy-duty gears: Used in the manufacturing of gears that require both strength and durability.
Medical Devices:
- Surgical instruments: High hardness and corrosion resistance are crucial in medical tools, making high-strength steel powders a preferred choice.
- Orthopedic implants: The biocompatibility and strength of certain powders make them ideal for load-bearing implants.
Applications and Uses of High-Strength Steel Powder
Industry | Application | Model/Type | Why It’s Used |
---|---|---|---|
Automotive | Structural components | HSLA-100 | High strength, lightweight |
Engine parts | CPM 3V | Wear resistance | |
Aerospace | Landing gear | Aermet 100 | Ultra-high strength, toughness |
Structural components | Maraging 300 | High strength-to-weight ratio | |
Tooling & Molding | Die casting molds | H13 Tool Steel | Thermal fatigue resistance |
Injection molding | S136H | High polishability, corrosion resistance | |
Marine | Corrosion-resistant parts | HSLA-100 | Weldability, seawater resistance |
Offshore drilling equipment | Aermet 100 | Strength, corrosion resistance | |
Industrial Machinery | Wear parts | CPM 3V | Superior wear resistance |
Heavy-duty gears | D2 Tool Steel | Strength, durability | |
Medical Devices | Surgical instruments | 17-4 PH | Hardness, corrosion resistance |
Orthopedic implants | M300 Maraging Steel | Biocompatibility, strength |
Specifications, Sizes, Grades, and Standards
Understanding the specifications, sizes, grades, and standards of high-strength steel powders is essential for choosing the right material for your application. Below is a detailed table summarizing these aspects.
Table: Specifications, Sizes, Grades, and Standards of High-Strength Steel Powders
Model | Specifications | Sizes Available | Grades | Standards |
---|---|---|---|---|
HSLA-100 | Tensile strength: 690 MPa | 5µm – 150µm | Grade 80 | MIL-S-16216K, ASTM A710 |
CPM 3V | Hardness: 58-60 HRC | 10µm – 100µm | Grade A | ASTM A681 |
Maraging 300 | Yield strength: 1930 MPa | 20µm – 120µm | Grade 300 | AMS 6514 |
17-4 PH | Tensile strength: 1170 MPa | 15µm – 125µm | H900, H1025 | AMS 5643, ASTM A564 |
Aermet 100 | Tensile strength: 2070 MPa | 10µm – 150µm | Grade 100 | MIL-S-46119 |
H13 Tool Steel | Hardness: 50-52 HRC | 10µm – 90µm | Grade A | ASTM A681 |
S136H | Hardness: 48-52 HRC | 5µm – 100µm | Grade S136 | DIN 1.2083, GB/T 1220 |
M300 Maraging | Tensile strength: 2050 MPa | 20µm – 120µm | Grade 300 | AMS 6514 |
D2 Tool Steel | Hardness: 55-62 HRC | 15µm – 110µm | Grade A | ASTM A681 |
PMD-100 | Tensile strength: 750 MPa | 20µm – 130µm | Grade 100 | ASTM F75, AMS 5758 |
Suppliers and Pricing Details
Pricing for high-strength steel powders can vary significantly depending on the composition, quality, and supplier. Below is a comparison of some common suppliers and their pricing ranges.
Table: Suppliers and Pricing Details for High-Strength Steel Powders
Supplier | Model | Price per kg (USD) | Minimum Order Quantity (kg) | Shipping Options |
---|---|---|---|---|
Advanced Metal Powders | HSLA-100 | $50 – $75 | 10 | Global shipping, expedited |
SteelTech Supplies | CPM 3V | $80 – $110 | 5 | Domestic and international |
Precision Alloys Inc. | Maraging 300 | $120 – $150 | 2 | Express shipping available |
Metal Powders Direct | 17-4 PH | $60 – $90 | 20 | Bulk discounts, global shipping |
Aerospace Materials Ltd. | Aermet 100 | $200 – $250 | 1 | Customized shipping options |
Tool Steel Solutions | H13 Tool Steel | $70 – $100 | 15 | Domestic only |
Global Powder Metals | S136H | $90 – $130 | 10 | Global shipping, expedited |
Maraging Metals LLC | M300 Maraging | $140 – $180 | 5 | Express shipping available |
Industrial Steel Powders | D2 Tool Steel | $85 – $120 | 8 | Bulk discounts, international |
PowderMet Inc. | PMD-100 | $55 – $80 | 25 | Global shipping, bulk discounts |
Advantages and Limitations of High-Strength Steel Powders
High-strength steel powders offer numerous benefits, but they also come with certain limitations. Here’s a breakdown:
Table: Advantages and Limitations of High-Strength Steel Powders
Advantages | Limitations |
---|---|
High Strength-to-Weight Ratio | Can be more expensive than traditional steel |
Excellent Corrosion Resistance | Requires precise manufacturing processes |
Superior Wear Resistance | May need specialized equipment for handling |
Versatility Across Applications | Limited availability of some specific grades |
Good Fatigue Resistance | Powder preparation and storage can be challenging |
Ease of Alloying and Customization | Potential for porosity in sintered parts |
Environmental Benefits in Manufacturing | Limited recyclability of some high-alloy powders |
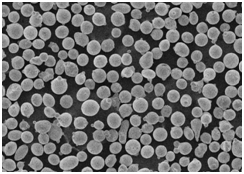
FAQ
Question | Answer |
---|---|
What is high-strength steel powder used for? | It’s used in industries like automotive, aerospace, tooling, marine, and medical for parts that require high strength, wear resistance, and corrosion resistance. |
How is high-strength steel powder made? | It is typically produced by atomization, where molten steel is broken into fine droplets that solidify into powder. |
What are the benefits of using high-strength steel powder? | Benefits include high tensile strength, wear resistance, corrosion resistance, and the ability to form complex shapes. |
Can high-strength steel powder be recycled? | While some high-strength steel powders can be recycled, those with complex alloy compositions may pose challenges. |
Is high-strength steel powder suitable for 3D printing? | Yes, it is widely used in additive manufacturing due to its ability to produce precise and complex components. |
What are the common grades of high-strength steel powder? | Common grades include HSLA-100, CPM 3V, Maraging 300, 17-4 PH, and Aermet 100, among others. |
How does high-strength steel powder compare to traditional steel? | High-strength steel powder offers superior mechanical properties and flexibility in manufacturing but can be more costly and requires advanced processing techniques. |
What industries benefit most from high-strength steel powder? | Industries such as aerospace, automotive, marine, tooling, and medical device manufacturing benefit significantly from using high-strength steel powders. |
How should high-strength steel powder be stored? | It should be stored in a dry, temperature-controlled environment to prevent oxidation and moisture absorption. |
What are the environmental impacts of high-strength steel powder production? | While the production process can be energy-intensive, the ability to create lighter, stronger components can lead to overall energy savings in applications like automotive and aerospace. |
Conclusion
High-strength steel powders are a remarkable innovation in the materials engineering field. Their unique properties make them indispensable across a wide range of industries, from automotive and aerospace to medical devices and industrial tooling. By understanding the various compositions, characteristics, applications, and limitations, professionals can make informed decisions about which high-strength steel powder is best suited for their specific needs.
This guide has aimed to provide a thorough exploration of high-strength steel powders, shedding light on the nuances of their use and helping you navigate the complexities of choosing the right material for your next project. Whether you’re a manufacturer, engineer, or researcher, the detailed insights provided here should serve as a valuable resource in your endeavors.
Remember, when it comes to materials like high-strength steel powder, the devil is in the details—so take your time, consider your options, and choose wisely.