Are you looking for a durable, high-performance metal powder that can stand the test of extreme environments? Enter Stellite 6 Powder. Whether you’re involved in manufacturing aerospace parts, automotive components, or need something to tackle wear and tear, Stellite 6 Powder might just be the wonder material you need.
In this article, we’ll take a deep dive into Stellite 6 Powder, its composition, characteristics, applications, and more. By the end, you’ll have a solid understanding of why this cobalt-based alloy powder stands out. Plus, I’ll walk you through different Stellite powder models, their specific benefits, and even some pricing details. So, buckle up – it’s going to be a journey through alloys, chemistry, and some good ol’ engineering fun!
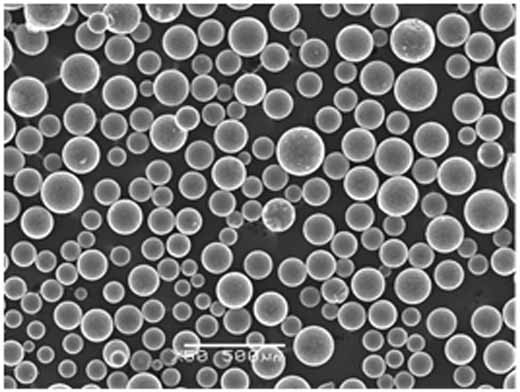
What is Stellite 6 Powder?
To put it simply, Stellite 6 is a cobalt-based alloy powder known for its exceptional resistance to wear, corrosion, and high temperatures. But there’s more to it than just that.
Think of it like a superhero for industrial applications – tough, durable, and capable of withstanding extreme environments where other materials would crumble. It’s the go-to material in industries that demand parts capable of maintaining their integrity in punishing conditions, from high-heat environments to corrosive atmospheres.
But here’s the thing: Stellite 6 isn’t just one-size-fits-all. It comes in several different forms and powder models, each offering unique properties depending on your application. From aerospace to energy, Stellite 6 Powder provides versatility across various sectors.
Why Choose Stellite 6 Powder?
Imagine you need a material that can handle high friction, intense heat, and corrosive chemicals, all while maintaining its strength. That’s where Stellite 6 shines (literally and figuratively). Whether it’s cutting tools, engine components, or turbine blades, this powder offers exceptional performance in conditions that would wear down most metals.
Compared to traditional steel alloys, Stellite 6 is like having a sports car compared to a regular sedan. Sure, both will get you from point A to B, but Stellite does it better, faster, and with way more flair. This makes it ideal for industries where reliability and durability are non-negotiable.
Key Benefits of Stellite 6 Powder:
- High Wear Resistance: Thanks to its hardness and cobalt-based composition, it can withstand friction for extended periods.
- Corrosion Resistance: Stellite 6 maintains its integrity even in harsh environments that would normally corrode other materials.
- Heat Resistance: Withstanding temperatures up to 500°C (932°F), it’s ideal for high-heat applications.
- Versatile Applications: From aerospace parts to automotive components, Stellite 6 can do it all.
- Extended Life Cycle: Components made with Stellite 6 Powder often last significantly longer than those made with other materials, reducing the need for frequent replacements.
Composition of Stellite 6 Powder
Stellite 6 is predominantly a cobalt-chromium alloy with additional elements like tungsten and carbon that enhance its properties. Let’s break it down:
Element | Typical Percentage |
---|---|
Cobalt (Co) | 55-65% |
Chromium (Cr) | 28-32% |
Tungsten (W) | 4-6% |
Carbon (C) | 0.9-1.4% |
Nickel (Ni) | <3% |
Iron (Fe) | <3% |
The cobalt provides the alloy’s toughness and heat resistance, while chromium adds corrosion resistance, making Stellite 6 highly suitable for environments exposed to chemicals or acids. Tungsten further bolsters wear resistance, while carbon contributes to the material’s hardness.
Other Stellite Powder Models:
While Stellite 6 is widely recognized, other Stellite powder variants are designed for specific use cases. Here’s a list of commonly used models:
Model | Composition Differences | Application |
---|---|---|
Stellite 6B | Lower carbon content | Better ductility for aerospace components |
Stellite 12 | Higher tungsten content | Extreme wear resistance, often for cutting tools |
Stellite 21 | Lower chromium, higher nickel | Enhanced machinability, often for engine valves |
Stellite 31 | High chromium and molybdenum | Excellent in corrosive environments |
Stellite F | Added silicon | Improved flowability, used in coatings |
Stellite 25 | Increased carbon content | Stronger hardness, used in turbine blades |
Stellite 706 | Special chromium-carbide blend | High resistance to abrasive wear |
Stellite 711 | Customized composition | Designed for downhole tools in oil industries |
Stellite 300 | Balance of tungsten and nickel | High temperature resilience |
Stellite 700 | Higher iron content | Cost-effective option for non-critical wear applications |
Each model of Stellite Powder has slight variations in its composition to optimize performance in different scenarios, offering an array of choices based on the job at hand.
Characteristics of Stellite 6 Powder
Now that you have a better idea of its composition, let’s talk characteristics. What makes Stellite 6 Powder stand out?
Characteristic | Details |
---|---|
Hardness | 40–45 HRC (can vary depending on heat treatment) |
Density | 8.4 g/cm³ |
Melting Range | 1280-1390°C |
Thermal Conductivity | ~13 W/m·K |
Wear Resistance | High wear resistance, even at elevated temperatures |
Corrosion Resistance | Excellent resistance to various forms of corrosion, including oxidation |
Machinability | Machinable using carbide or ceramic tooling |
Weldability | Can be welded to similar or dissimilar alloys, often used in overlay welding |
Hardness and wear resistance are the two primary reasons why Stellite 6 Powder is in such high demand. Its ability to withstand harsh working environments, like high friction and extreme temperatures, is unmatched. Plus, despite its hardness, it can be machined using specialized tools, making it versatile for various applications.
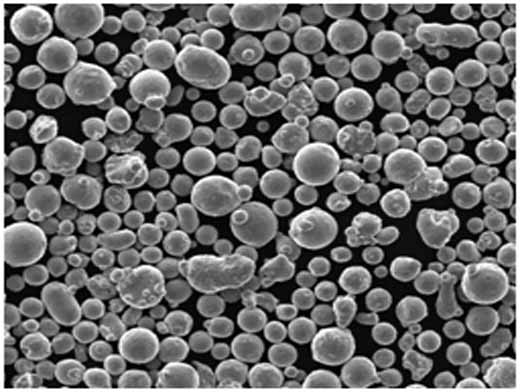
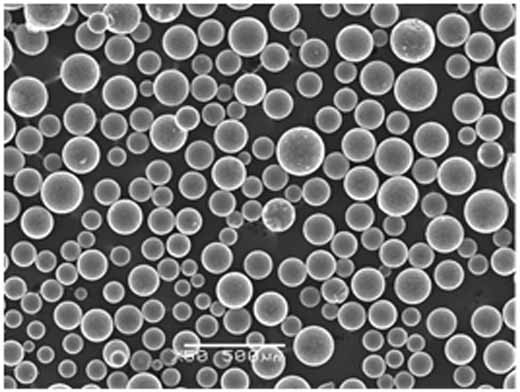
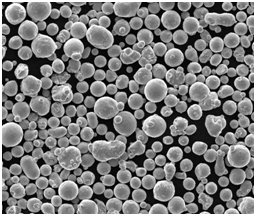
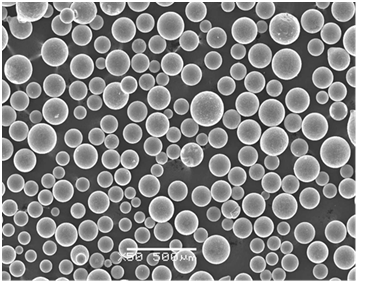
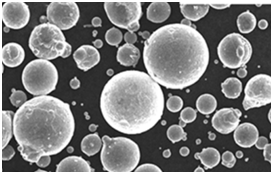
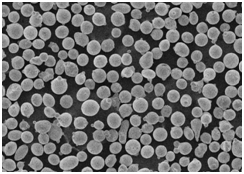
Applications of Stellite 6 Powder
So, where exactly can you use Stellite 6 Powder? Well, the better question might be – where can’t you use it?
From aerospace and oil drilling to energy production and even dental tools, Stellite 6 offers a wide range of applications. Let’s break it down:
Industry | Common Applications |
---|---|
Aerospace | Aircraft engine components, turbine blades, valve seats |
Automotive | Exhaust valves, wear-resistant coatings for critical components |
Oil & Gas | Downhole tools, valve seats, pipeline coatings |
Energy Production | Steam turbine blades, gas turbine components, valve overlays |
Medical/Dental | Cutting tools, surgical instruments, dental burs |
General Engineering | Cutting tools, wear-resistant coatings for equipment |
Marine | Components exposed to saltwater and other corrosive environments |
Aerospace stands as one of the biggest users of Stellite 6 Powder. When you’re dealing with high speeds, high temperatures, and constant friction, materials like Stellite 6 are invaluable.
Similarly, oil and gas industries benefit from its durability in downhole tools, where wear and tear from extreme conditions is a constant issue.
Specifications and Standards for Stellite 6 Powder
If you’re planning on using Stellite 6 Powder, it’s crucial to be aware of the specifications and standards that guide its use. These ensure that the material meets the high-performance criteria needed for industrial applications.
Standard/Specification | Details |
---|---|
ASTM F75 | Specifications for cobalt-chromium alloys used in surgical implants |
ISO 5832-4 | International standard for metallic materials, particularly implants |
AMS 5387 | Aerospace standard for cobalt-based alloys, such as Stellite 6 |
AWS A5.21 | Welding standards for cobalt alloys |
DIN EN ISO 482 | Wear-resistant materials, cobalt alloys for use in hot environments |
Each standard lays down the guidelines that ensure Stellite 6 Powder meets the specific requirements needed for different industries.
Suppliers and Pricing for Stellite 6 Powder
Wondering where to source Stellite6 Powder? And more importantly, what will it cost you? Here’s a breakdown of some suppliers and the approximate pricing.
Supplier | Country | Pricing (Per kg) | MOQ (Minimum Order Quantity) |
---|---|---|---|
Kennametal | USA | $150–$300 | 1 kg |
Oerlikon Metco | Switzerland | $200–$350 | 2 kg |
Sandvik | Sweden | $180–$320 | 1 kg |
Höganäs | Sweden | $170–$300 | 5 kg |
Deloro Stellite | Germany | $160–$320 | 2 kg |
Metal Powder Works | USA | $140–$280 | 1 kg |
As you can see, prices vary depending on the supplier, geographic location, and minimum order quantities (MOQ). It’s worth shopping around based on your specific project needs and the amount of powder you require.
Comparing Stellite 6 Powder with Other Materials
So, how does Stellite 6 fare when compared to other similar materials like Inconel or Hastelloy?
Material | Stellite 6 | Inconel | Hastelloy |
---|---|---|---|
Wear Resistance | High | Moderate | High |
Corrosion Resistance | Excellent | Excellent | Excellent |
Temperature Resistance | High, up to 932°F | Higher, up to 2200°F | High |
Machinability | Fair | Difficult | Difficult |
Weldability | Good | Difficult | Difficult |
Typical Applications | High-wear environments, aerospace | High-temp environments, engines | Chemical processing, oil & gas |
While Stellite 6 excels in wear resistance and moderate heat applications, Inconel might be your better bet if you need something that withstands very high temperatures. On the flip side, Hastelloy is superior when it comes to handling corrosive chemicals, especially in industries like chemical processing.
Advantages of Stellite 6 Powder
Now that we’ve compared Stellite 6 to other materials, let’s sum up its advantages:
- Outstanding Wear Resistance: In environments where friction and wear are a concern, Stellite 6 Powder performs like a champ.
- High Corrosion Resistance: Even in corrosive atmospheres, Stellite 6 holds its ground.
- Elevated Temperature Stability: While it doesn’t beat Inconel for high heat, it’s more than capable of handling most high-temperature situations.
- Durability: With proper application, components made from Stellite 6 Powder tend to have a long life cycle, which can lead to cost savings.
- Versatility: Whether it’s aerospace, oil and gas, or medical devices, Stellite 6 has broad applicability.
Disadvantages of Stellite 6 Powder
No material is perfect, and Stellite 6 does have its limitations. Here are a few things to consider:
- Cost: Stellite 6 can be expensive compared to traditional steels, so it’s not always the best choice for budget-conscious projects.
- Machinability: While it can be machined, it requires specialized tools due to its hardness, which can increase manufacturing costs.
- Temperature Limitation: While it performs well at elevated temperatures, Inconel or other materials might be a better option for ultra-high-temperature environments.
- Weldability: While weldable, precise techniques and expertise are required to ensure optimal performance.
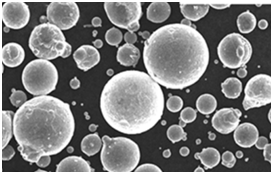
FAQs
Q: What industries commonly use Stellite 6 Powder?
A: Industries that frequently deal with high-wear and high-temperature environments – think aerospace, automotive, oil & gas, and medical – commonly use Stellite 6 Powder. It’s particularly useful for components exposed to extreme friction or corrosive environments.
Q: Can Stellite 6 Powder be machined?
A: Yes, but due to its hardness, machining Stellite 6 Powder requires carbide or ceramic tooling to prevent wear on the cutting tools.
Q: Is Stellite 6 Powder weldable?
A: Absolutely! Stellite 6 Powder is often used in overlay welding to provide a wear-resistant coating on critical parts. Just keep in mind that specialized techniques are needed to ensure a high-quality weld.
Q: How does Stellite 6 Powder compare to Inconel?
A: Stellite 6 offers better wear resistance, whereas Inconel is more suited for extreme high-temperature environments. It all depends on your specific needs.
Q: What is the price range of Stellite 6 Powder?
A: Pricing can range anywhere between $140 and $350 per kilogram, depending on the supplier, quantity, and geographic location. Bulk orders may provide cost-saving opportunities.
Final Thoughts on Stellite 6 Powder
At the end of the day, Stellite 6 Powder is a workhorse in the world of alloys. Its combination of wear resistance, corrosion resistance, and temperature stability makes it a go-to choice for industries that can’t afford downtime due to worn-out parts.
While it does have some limitations – mainly cost and machinability – its benefits far outweigh the drawbacks for critical applications. Whether you’re looking to increase the longevity of turbine blades or need a durable coating for valves, Stellite 6 should be high on your list of materials to consider.
And that’s a wrap on Stellite 6 Powder! Whether you’re a seasoned engineer or someone just dipping their toes into the world of metallurgy, I hope this guide gave you a comprehensive understanding of why Stellite 6 is such a sought-after material in high-performance industries.