Metal Injection Moulding (MIM) is an advanced manufacturing process used to produce complex, high-precision metal parts. This method combines the versatility of plastic injection molding with the strength and integrity of metal. If you’re curious about how MIM works, its applications, or why it’s becoming a preferred choice in various industries, you’re in the right place. Let’s dive in!
Overview of Metal Injection Moulding
Metal Injection Moulding (MIM) is a process that blends finely powdered metal with a binder material to create a feedstock that can be shaped and solidified using injection molding. The molded part is then sintered to remove the binder and densify the metal, resulting in a final product with excellent mechanical properties and complex geometries.
Key Advantages of MIM:
- High precision and intricate detailing
- High production rates
- Wide range of material choices
- Reduced material waste
- Excellent mechanical properties
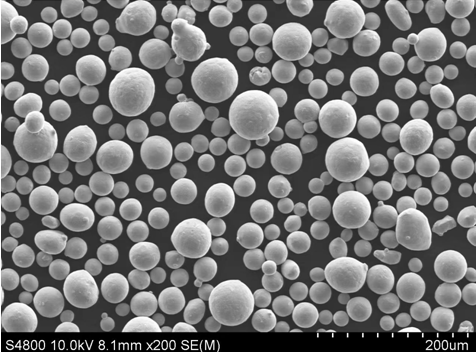
Applications of Metal Injection Moulding:
MIM is widely used across various industries including automotive, medical devices, electronics, aerospace, and consumer products. Its ability to produce complex shapes with high accuracy makes it ideal for small, intricate parts that require strong mechanical properties.
Types of Metal Powders Used in MIM
When it comes to Metal Injection Moulding, the type of metal powder used plays a crucial role in determining the properties of the final product. Here are some commonly used metal powders in MIM:
Metal Powder | Composition | Properties | Characteristics |
---|---|---|---|
Stainless Steel 316L | Fe, Cr, Ni, Mo | Corrosion resistance, high strength | Common in medical and food industry |
Stainless Steel 17-4 PH | Fe, Cr, Ni, Cu | High strength, good corrosion resistance | Used in aerospace, automotive |
Carbonyl Iron | Fe | High purity, excellent magnetic properties | Suitable for electronics, automotive |
Tungsten | W | High density, high melting point | Ideal for aerospace, defense applications |
Titanium Ti-6Al-4V | Ti, Al, V | High strength-to-weight ratio, corrosion resistance | Used in medical implants, aerospace |
Nickel Alloy IN718 | Ni, Cr, Fe | High temperature strength, corrosion resistance | Suitable for gas turbines, aerospace |
Copper Alloy C18150 | Cu, Cr | High electrical and thermal conductivity | Used in electrical components |
Tool Steel M2 | Fe, C, W, Mo | High hardness, wear resistance | Used in cutting tools, dies |
Cobalt-Chromium Alloy | Co, Cr | High strength, biocompatibility | Common in dental, medical implants |
Aluminum Alloy 6061 | Al, Mg, Si | Lightweight, good mechanical properties | Used in automotive, consumer electronics |
Composition and Properties of Metal Injection Moulding
Understanding the composition and properties of MIM materials is crucial for selecting the right type for your application. Here’s a detailed look:
Material | Composition | Properties | Applications |
---|---|---|---|
Stainless Steel 316L | 16-18% Cr, 10-14% Ni, 2-3% Mo, Bal. Fe | Corrosion resistance, good strength | Medical devices, food processing equipment |
Stainless Steel 17-4 PH | 15-17% Cr, 3-5% Ni, 3-5% Cu, Bal. Fe | High strength, corrosion resistance | Aerospace, automotive parts |
Carbonyl Iron | >99% Fe | High purity, magnetic properties | Electronics, automotive components |
Tungsten | >99% W | High density, thermal stability | Aerospace, defense equipment |
Titanium Ti-6Al-4V | 90% Ti, 6% Al, 4% V | Lightweight, high strength | Medical implants, aerospace parts |
Nickel Alloy IN718 | 50-55% Ni, 17-21% Cr, Bal. Fe | High temperature strength | Gas turbines, aerospace components |
Copper Alloy C18150 | 98-99% Cu, 0.5-1% Cr | Conductivity, thermal properties | Electrical connectors, heat sinks |
Tool Steel M2 | 0.75-1.1% C, 4.0-6.0% Mo, 5.5-6.75% W, Bal. Fe | Hardness, wear resistance | Cutting tools, dies |
Cobalt-Chromium Alloy | 60-65% Co, 27-30% Cr | Strength, biocompatibility | Dental implants, orthopedic devices |
Aluminum Alloy 6061 | 0.8-1.2% Mg, 0.4-0.8% Si, Bal. Al | Lightweight, machinability | Automotive parts, consumer electronics |
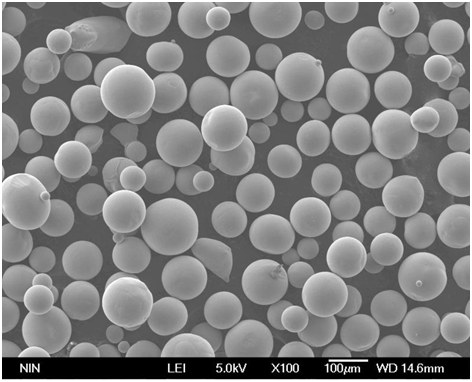
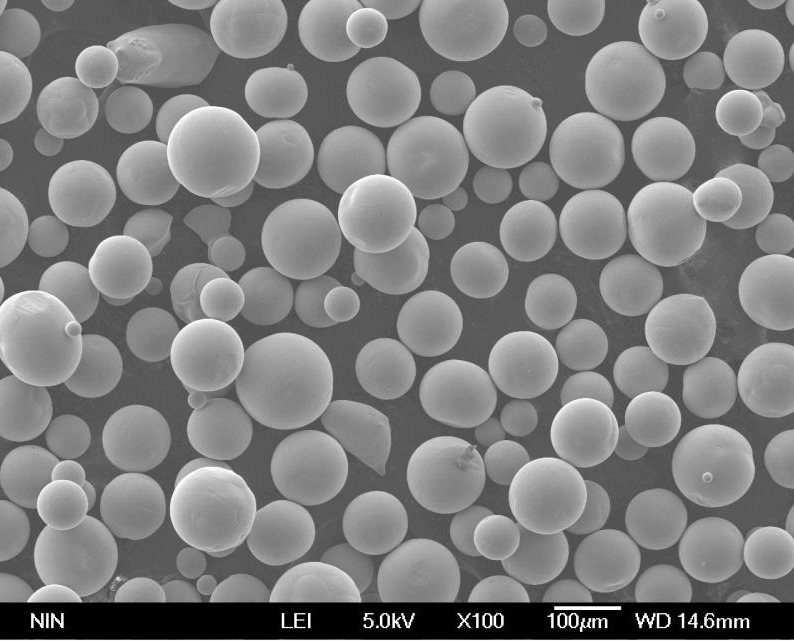
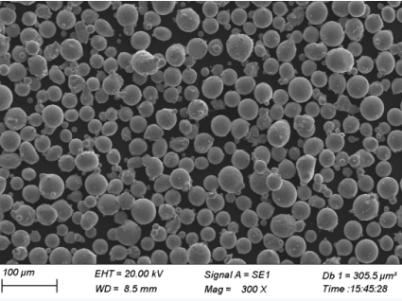
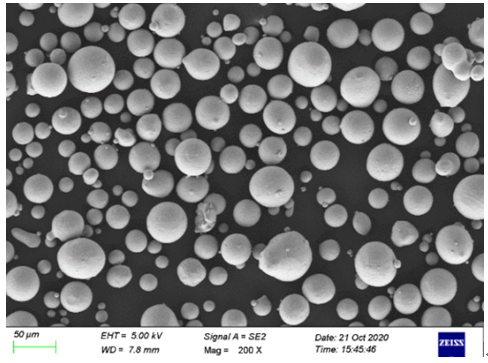
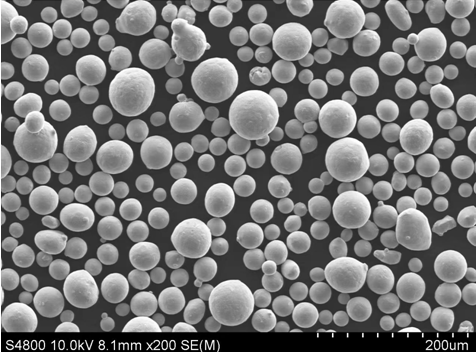
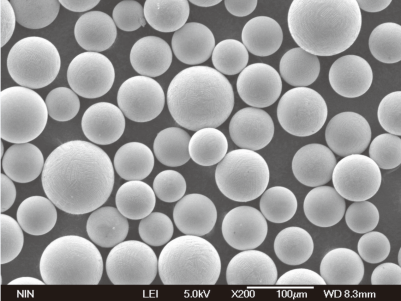
Applications of Metal Injection Moulding
Metal Injection Moulding is versatile and finds applications in various industries. Here’s a table summarizing some key applications:
Industry | Applications |
---|---|
Automotive | Fuel injector components, turbocharger parts, gearboxes |
Medical Devices | Surgical instruments, orthodontic brackets, implants |
Electronics | Connectors, sensors, mobile phone components |
Aerospace | Turbine blades, fuel nozzles, fasteners |
Consumer Products | Watch cases, eyeglass frames, hardware tools |
Defense | Weapon components, armor-piercing projectiles |
Industrial | Cutting tools, pumps, valves |
Specifications, Sizes, and Standards in MIM
Selecting the right specifications, sizes, and standards is crucial for ensuring the final product meets the required performance criteria. Here’s a detailed look:
Specification | Description |
---|---|
ASTM Standards | ASTM F2885-11, ASTM B883-10 for MIM materials |
ISO Standards | ISO 22068, ISO 13320 for powder particle size distribution |
Sizes | Ranges from 0.1 mm to 100 mm in size depending on complexity |
Tolerances | Typically ±0.3% of dimensions, can be as tight as ±0.05% |
Surface Finish | Can achieve Ra 0.8 to 1.6 micrometers depending on material and process |
Density | Typically ranges from 95% to 99% of theoretical density after sintering |
Suppliers and Pricing Details for Metal Injection Moulding
Choosing the right supplier can significantly impact the cost and quality of your MIM components. Here are some notable suppliers along with estimated pricing details:
Supplier | Material | Pricing | Region |
---|---|---|---|
Smith Metal Products | Stainless Steel, Titanium | $0.10 – $0.50 per gram | USA |
Advanced Metalworking Practices | Various metal powders | $0.08 – $0.45 per gram | USA |
Parmatech Corporation | Stainless Steel, Tool Steel | $0.12 – $0.55 per gram | USA |
Indo-MIM | Stainless Steel, Tungsten | $0.09 – $0.50 per gram | India |
ARC Group Worldwide | Nickel Alloys, Copper Alloys | $0.10 – $0.60 per gram | USA |
CNI Manufacturing | Stainless Steel, Aluminum | $0.08 – $0.48 per gram | China |
Kinetics Climax | Tool Steel, Cobalt Alloys | $0.12 – $0.58 per gram | USA |
CMG Technologies | Stainless Steel, Titanium | $0.11 – $0.52 per gram | UK |
GKN Sinter Metals | Stainless Steel, Tool Steel | $0.09 – $0.49 per gram | Germany |
MPP Innovation | Various metal powders | $0.10 – $0.47 per gram | USA |
Comparing Pros and Cons of Metal Injection Moulding
When considering Metal Injection Moulding, it’s essential to weigh its advantages and limitations. Here’s a comparison:
Aspect | Advantages | Limitations |
---|---|---|
Precision | High dimensional accuracy, intricate shapes | Limited to small and medium-sized parts |
Material Efficiency | Low material waste, efficient use of powders | Higher initial material cost |
Mechanical Properties | Strong, durable parts with excellent properties | Sintering process can introduce porosity |
Production Volume | Suitable for high-volume production | Not cost-effective for low-volume production |
Complexity | Can produce highly complex geometries | Limited to certain part sizes and geometries |
Surface Finish | Excellent surface finish achievable | Secondary finishing might be needed for specific applications |
Versatility | Wide range of materials available | Longer lead times compared to traditional methods |
Cost | Cost-effective for large production runs | High initial tooling and setup costs |
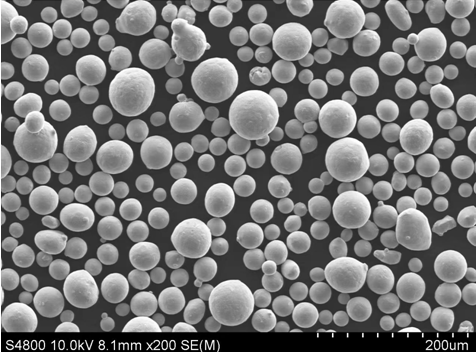
FAQs
Q: What is Metal Injection Moulding (MIM)?
A: Metal Injection Moulding is a manufacturing process that combines metal
powders with a binder to produce highly detailed and complex metal parts using injection molding techniques.
Q: What materials can be used in MIM?
A: Various materials can be used in MIM, including stainless steels, tool steels, titanium alloys, tungsten, nickel alloys, copper alloys, and more.
Q: What are the key advantages of MIM?
A: The key advantages include high precision, complex geometries, high production rates, reduced material waste, and excellent mechanical properties.
Q: What industries commonly use MIM?
A: MIM is used in automotive, medical devices, electronics, aerospace, consumer products, defense, and industrial applications.
Q: What are the typical sizes and tolerances achievable with MIM?
A: Sizes can range from 0.1 mm to 100 mm, with tolerances typically around ±0.3% of dimensions, and as tight as ±0.05% in some cases.
Q: How does the sintering process affect MIM parts?
A: Sintering removes the binder and densifies the metal, which can introduce porosity but also significantly enhances the mechanical properties of the parts.
Q: Is MIM cost-effective for low-volume production?
A: No, MIM is generally not cost-effective for low-volume production due to high initial tooling and setup costs. It is more suited for high-volume production runs.
Q: Can MIM produce parts with high surface finishes?
A: Yes, MIM can achieve excellent surface finishes, though some applications may require secondary finishing processes for optimal results.
Q: Are there any limitations to the geometries that can be produced with MIM?
A: While MIM can produce highly complex geometries, it is limited to certain part sizes and may not be suitable for very large parts.
Q: What should I consider when selecting a supplier for MIM parts?
A: Consider factors such as material expertise, production capacity, pricing, regional location, and the supplier’s track record in delivering high-quality MIM parts.
Conclusion
Metal Injection Moulding is a versatile and highly efficient manufacturing process that offers numerous benefits for producing complex and high-precision metal parts. From automotive to aerospace, its applications are vast and varied, making it a valuable technique in modern manufacturing. By understanding the types of materials, specifications, and advantages of MIM, you can better assess whether this process is suitable for your specific needs.
Whether you’re considering MIM for its precision, material efficiency, or ability to produce complex geometries, it’s clear that this innovative process has a lot to offer. As technology and materials continue to advance, the potential for Metal Injection Moulding will only grow, opening up new possibilities in manufacturing and design.