When it comes to high-performance alloys, Inconel 625 powder stands out as one of the top choices for demanding environments. This remarkable nickel-chromium-based alloy, known for its superior strength, corrosion resistance, and thermal stability, plays a critical role in industries like aerospace, automotive, and marine engineering. If you’ve ever wondered what makes Inconel 625 powder so special or how it can fit into your next project, you’re in the right place.
This guide dives into everything you need to know about Inconel 625 powder: from its composition and characteristics to various models and applications. You’ll get an insider look into its properties, the best ways to use it, and why it outperforms other metal powders in high-stress environments. Stick around—there’s a lot to explore!
Overview of Inconel 625 Powder
Inconel 625 is a nickel-based alloy renowned for its exceptional mechanical properties. It is designed to perform under extreme conditions, such as high temperature, intense pressure, and corrosive environments. The powder form of Inconel 625 is particularly useful in additive manufacturing (3D printing), where its high strength and corrosion resistance are leveraged in complex geometries.
Key Properties of Inconel 625 Powder
- High Temperature Resistance: Maintains strength and integrity up to 1000°C (1832°F).
- Corrosion Resistance: Outstanding resistance to oxidation, pitting, and crevice corrosion.
- Versatility: Suitable for various manufacturing processes, including welding, 3D printing, and traditional machining.
- Durability: Exhibits excellent fatigue strength, crucial for cyclic stress environments.
The unique combination of these properties makes Inconel 625 powder invaluable for many industrial applications. But before we dive into where and how it’s used, let’s first examine its composition in detail.
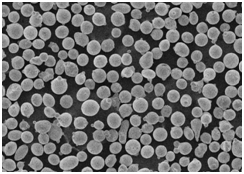
Composition of Inconel 625 Powder
The composition of Inconel 625 powder is what makes it a standout material in high-stress environments. The key components of this alloy are nickel, chromium, molybdenum, and niobium. Each of these elements plays a crucial role in enhancing the overall properties of the material.
Element | Percentage Composition (%) |
---|---|
Nickel (Ni) | 58.0 – 63.0 |
Chromium (Cr) | 20.0 – 23.0 |
Molybdenum (Mo) | 8.0 – 10.0 |
Niobium (Nb) | 3.15 – 4.15 |
Iron (Fe) | ≤ 5.0 |
Cobalt (Co) | ≤ 1.0 |
Carbon (C) | ≤ 0.10 |
Silicon (Si) | ≤ 0.50 |
These elements collectively offer Inconel 625 powder its superior corrosion resistance and mechanical strength. Molybdenum and niobium contribute to its ability to withstand intense pressures, while nickel and chromium enhance its resistance to heat and oxidation.
Models of Inconel 625 Powder
Not all Inconel 625 powders are created equal. There are several models designed for different industrial purposes, each tailored to a specific application. Below are some of the most popular models, complete with descriptions.
Model | Description |
---|---|
Inconel 625 AM | Optimized for additive manufacturing, with consistent particle size and flowability for 3D printing applications. |
Inconel 625 Weld | Engineered specifically for welding processes, offering excellent weldability and high resistance to cracking. |
Inconel 625 Forging | Designed for forging applications, featuring enhanced mechanical properties for high-stress, high-temperature environments. |
Inconel 625 Sheet | Formulated for sheet metal manufacturing, offering superior formability and corrosion resistance. |
Inconel 625 Wire | Ideal for wire-based applications, such as wire arc additive manufacturing (WAAM), due to its excellent tensile strength and durability. |
Inconel 625 Plasma | Designed for plasma spraying applications, offering high bond strength and exceptional thermal resistance. |
Inconel 625 Cast | Tailored for casting processes, ensuring excellent flowability and low porosity in finished parts. |
Inconel 625 Aero | Optimized for aerospace applications, providing unmatched fatigue strength and resistance to thermal cycling in extreme conditions. |
Inconel 625 Marine | Specifically formulated for marine environments, where its superior corrosion resistance against saltwater and chlorides is critical. |
Inconel 625 Auto | Designed for the automotive industry, with excellent fatigue resistance and thermal stability, ideal for turbochargers and exhaust systems. |
Each of these models offers a unique combination of properties that makes them suitable for specific applications. For example, Inconel 625 AM is designed for 3D printing, whereas Inconel 625 Aero is optimized for aerospace applications.
Characteristics of Inconel 625 Powder
What makes Inconel 625 powder the go-to choice for engineers and manufacturers? Let’s break down some of the key characteristics:
1. Corrosion Resistance
Inconel 625 powder excels in environments where other metals would corrode or degrade. Its resistance to pitting, crevice corrosion, and intergranular attack makes it invaluable in industries like marine and chemical processing.
2. High-Temperature Stability
Capable of withstanding temperatures up to 1000°C (1832°F), this material maintains its mechanical properties in extreme conditions. This makes it ideal for use in gas turbines, heat exchangers, and other high-temperature applications.
3. Mechanical Strength
Inconel 625 powder boasts exceptional tensile strength, fatigue resistance, and yield strength. This makes it suitable for components subjected to mechanical stress, such as aerospace engine parts and automotive turbochargers.
4. Versatility in Manufacturing
Whether you’re using traditional casting methods, 3D printing, or welding, Inconel 625 powder is adaptable. Its consistent particle size and flowability make it perfect for a range of manufacturing processes.
5. Weldability
Inconel 625 powder offers excellent weldability, particularly in high-temperature environments where cracking is a concern. This is one reason it’s often used in piping systems and chemical processing equipment.
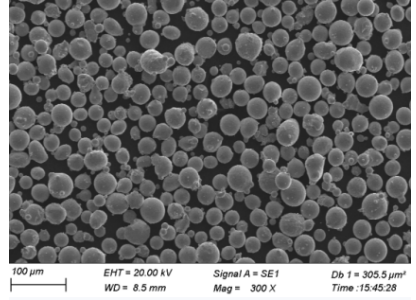
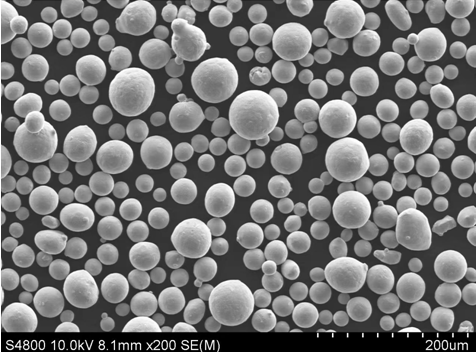
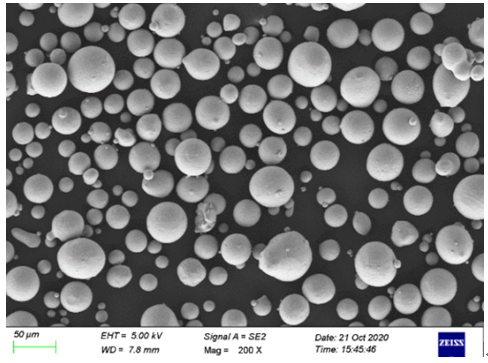
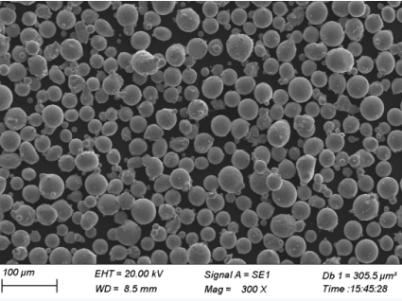
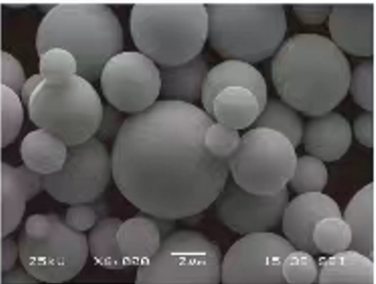
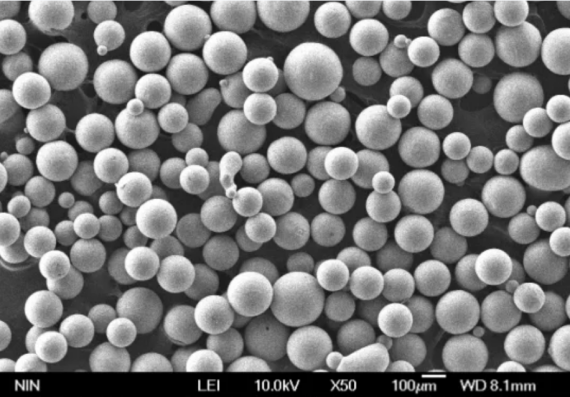
Advantages of Inconel 625 Powder
Now that we know what makes Inconel 625 powder so special, let’s explore its advantages in comparison to other metal powders.
Advantages | Description |
---|---|
Superior Corrosion Resistance | Outperforms stainless steel and other nickel alloys in harsh environments. |
High Fatigue Strength | Ideal for components subjected to cyclical loading, such as aircraft engine parts and turbochargers. |
Temperature Stability | Maintains mechanical properties at temperatures as high as 1000°C (1832°F). |
Versatile Manufacturing | Can be used in additive manufacturing, traditional machining, welding, and more. |
Reduced Maintenance Costs | Its durability in corrosive environments reduces the need for frequent replacements. |
Consistency in Powder Form | Ensures uniform particle size, flowability, and performance in additive manufacturing and plasma spraying. |
In short, Inconel 625 powder is better at handling extreme conditions compared to alternatives like stainless steel or titanium alloys. It’s more durable, requires less maintenance, and performs well across a wide range of applications.
Applications of Inconel 625 Powder
Given its impressive properties, Inconel 625 powder finds use in several critical industries. Below are some of the most common applications, along with a breakdown of why it’s used in each context.
Industry | Application | Reason for Use |
---|---|---|
Aerospace | Jet engines, turbine blades, exhaust systems | High-temperature resistance and fatigue strength make it ideal for aerospace components exposed to extreme conditions. |
Marine | Piping systems, seawater heat exchangers, offshore platforms | Excellent corrosion resistance against seawater, chlorides, and other marine contaminants. |
Automotive | Turbochargers, exhaust manifolds | High-temperature stability and fatigue strength provide long-term durability in high-performance engines. |
Chemical Processing | Heat exchangers, reactor vessels, acid production equipment | Corrosion resistance against harsh chemicals like hydrochloric acid, sulfuric acid, and caustic solutions. |
Power Generation | Heat exchangers, gas turbines, nuclear reactor components | Ability to withstand high temperatures and resist oxidation makes it indispensable in power generation. |
Oil and Gas | Downhole equipment, riser systems, pipelines | Durability in high-pressure, corrosive environments like oil drilling and gas extraction. |
Medical | Prosthetics, surgical instruments, medical implants | Biocompatibility and corrosion resistance make it suitable for long-term exposure to the human body. |
Additive Manufacturing | 3D printing of complex aerospace parts, medical devices, automotive components | Versatility in additive manufacturing due to its consistent particle size and flowability. |
Each of these applications takes advantage of the unique properties of Inconel 625 powder, making it a versatile solution for industries that demand reliability in extreme conditions.
Specifications, Sizes, and Standards of Inconel 625 Powder
To ensure that you are selecting the right type of Inconel 625 powder for your specific needs, it’s essential to understand its different grades, sizes, and standards.
Specification | Description |
---|---|
ASTM B443 | Standard specification for Inconel 625 sheets, strips, and plates. |
AMS 5599 | Aerospace material specification for Inconel 625 sheets and strips. |
ASTM B446 | Standard specification for Inconel 625 bars, rods, and forgings. |
Powder Size Range | 15 – 53 µm (commonly used in 3D printing), 45 – 105 µm (used in plasma spraying and other processes). |
Grade | IN625 (basic), IN625 AM (for additive manufacturing), IN625 Weld (for welding). |
Packaging Sizes | Typically available in 1kg, 5kg, and 25kg containers, though larger bulk quantities can be sourced. |
Choosing the correct specification is vital for meeting industry standards and ensuring the material performs as expected in its intended application.
Suppliers and Pricing of Inconel 625 Powder
When sourcing Inconel 625 powder, pricing can vary depending on the supplier, model, and quantity purchased. Below is a general guide to suppliers and pricing.
Supplier | Location | Pricing (Per kg) | Additional Notes |
---|---|---|---|
Höganäs AB | Sweden | $150 – $300 | Offers a wide range of metal powders, including Inconel 625 for additive manufacturing. |
LPW Technology | United Kingdom | $180 – $350 | Specializes in high-quality powders for 3D printing, with consistent particle size. |
Sandvik Osprey | USA | $200 – $400 | Known for providing metal powders tailored for demanding applications. |
Carpenter Technology | USA | $190 – $380 | Supplies Inconel 625 powder specifically optimized for aerospace and medical applications. |
Praxair Surface Technologies | USA | $160 – $350 | Offers Inconel 625 powder with high flowability, ideal for plasma spraying and additive manufacturing. |
Tekna Advanced Materials | Canada | $170 – $310 | Focuses on plasma atomized metal powders with high purity and spherical shape. |
Pricing for Inconel 625 powder depends on several factors, including the particle size, grade, and quantity purchased. Bulk orders typically result in discounted prices, making it a more economical choice for large-scale industrial applications.
Comparing Inconel 625 Powder with Other Metal Powders
How does Inconel 625 powder stack up against other commonly used metal powders? Let’s take a closer look by comparing its key properties to that of stainless steel powder and titanium powder.
Property | Inconel 625 Powder | Stainless Steel Powder | Titanium Powder |
---|---|---|---|
Corrosion Resistance | Superior | Good | Excellent |
Temperature Stability | Up to 1000°C | Up to 800°C | Up to 600°C |
Mechanical Strength | High | Moderate | High |
Fatigue Resistance | Excellent | Moderate | Good |
Weldability | Excellent | Moderate | Good |
Cost | Higher ($150 – $400/kg) | Lower ($50 – $150/kg) | Moderate ($100 – $300/kg) |
Compared to stainless steel and titanium powders, Inconel 625 powder offers superior corrosion resistance and temperature stability, but at a higher cost. Its exceptional mechanical strength and fatigue resistance make it a better choice for extreme environments, though stainless steel remains a more economical option for less demanding applications.
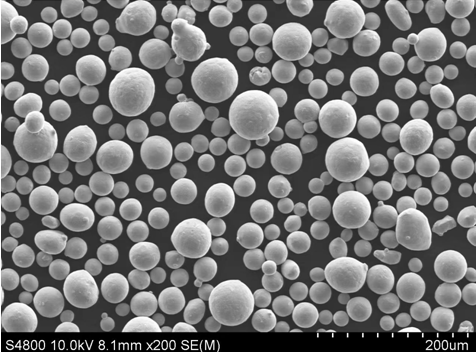
FAQ
Question | Answer |
---|---|
What is Inconel 625 powder primarily used for? | Inconel 625 powder is primarily used in aerospace, marine, and chemical processing industries for its high strength and corrosion resistance. |
Can Inconel 625 be 3D printed? | Yes, Inconel 625 powder is frequently used in additive manufacturing due to its excellent flowability and particle size consistency. |
Is Inconel 625 powder expensive? | Yes, it tends to be more expensive than other metal powders like stainless steel, but its performance justifies the higher cost. |
What are the benefits of using Inconel 625 in marine settings? | Inconel 625 offers superior corrosion resistance in saltwater and chloride-rich environments, making it ideal for marine applications. |
Can I weld with Inconel 625 powder? | Absolutely! Inconel 625 powder is known for its excellent weldability, even in high-temperature environments. |
Conclusion
Inconel 625 powder offers a remarkable blend of high-temperature resistance, mechanical strength, and corrosion resistance, making it a top choice for industries where durability and reliability are non-negotiable. Whether you’re working on a jet engine, a marine structure, or a cutting-edge 3D-printed component, Inconel 625 powder has the properties you need to ensure long-lasting performance.
By understanding its various models, specifications, and applications, you’ll be well-equipped to make the right choice for your specific project. Although it’s more expensive than other metal powders, the investment pays off in reduced maintenance costs, longer product lifespans, and superior performance in extreme environments.