Introduction to Metal Powders
What if I told you that the secret sauce behind those roaring rocket engines isn’t just the fuel but the very materials they’re made of? Yep, you heard that right! Metal powders, those tiny particles of metallic bliss, are at the heart of high-temperature rocket engines.
But what exactly are metal powders, and why are they so crucial? Imagine a metal so finely ground that it resembles a dust cloud. That’s metal powder for you! But don’t let their tiny size fool you. These powders are the building blocks of some of the most heat-resistant, durable, and high-performing components in the aerospace industry.
Whether it’s nickel, titanium, aluminum, or even some of the more exotic refractory metals, each type of metal powder brings its unique set of properties to the table. These powders are not just any materials; they’re engineered to perfection, designed to withstand the rigors of space travel and beyond.
Now, let’s dive deeper into the specific types of metal powders used in high-temperature rocket engines and see how they contribute to the next giant leap for mankind.
Types of Metal Powders Used in High-Temperature Rocket Engines
When it comes to rocket engines, not all metal powders are created equal. Each type has its distinct properties that make it suitable for different parts of the engine. Let’s explore some of the key players in this high-stakes game.
- Nickel-Based Powders
- NiCrMo (Nickel-Chromium-Molybdenum): Known for its excellent corrosion resistance and high-temperature stability, NiCrMo is often used in combustion chambers and turbine blades.
- Inconel 718: A superalloy that can withstand temperatures up to 700°C, Inconel 718 is highly valued for its creep resistance and ability to maintain mechanical strength in extreme environments.
- Titanium-Based Powders
- Ti-6Al-4V: This alloy is a superstar in the aerospace industry due to its incredible strength-to-weight ratio. It’s perfect for structural components that require both lightness and durability.
- Ti-Al-Nb (Titanium-Aluminum-Niobium): Known for its resistance to oxidation and high-temperature strength, this alloy is often used in the construction of engine casings.
- Aluminum-Based Powders
- AlSi10Mg (Aluminum-Silicon-Magnesium): Lightweight yet strong, AlSi10Mg is commonly used for manufacturing fuel tanks and other structural components in rocket engines.
- AlCu4Mg1 (Aluminum-Copper-Magnesium): With excellent machinability and thermal conductivity, this alloy is often chosen for heat exchangers and cooling systems.
- Refractory Metal Powders
- Tungsten (W): Tungsten’s melting point of 3422°C makes it a prime candidate for use in nozzles and other high-heat areas of the rocket engine.
- Molybdenum (Mo): Another refractory metal, molybdenum is used in components that must endure high stress and heat without deforming.
- Cobalt-Based Powders
- CoCrMo (Cobalt-Chromium-Molybdenum): This superalloy is particularly known for its wear resistance and is used in high-temperature ball bearings and seals.
- Stellite 6B: A cobalt-chromium alloy that offers outstanding resistance to heat and corrosion, making it ideal for valve seats and exhaust valves.
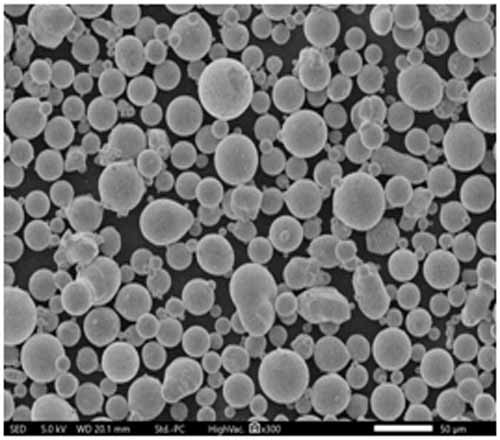
Composition and Properties of High-Temperature Metal Powders
Key Characteristics of Metal Powders in Rocket Engines
What makes these metal powders the superheroes of the rocket engine world? It’s all in their composition and properties. Let’s break down the key characteristics that make these materials indispensable:
- Heat Resistance: The ability to withstand high temperatures without losing structural integrity is paramount. Metal powders like those based on nickel, titanium, and refractory metals excel in this area.
- Strength-to-Weight Ratio: In aerospace, every gram counts. Materials like titanium alloys provide immense strength without adding excessive weight, crucial for maintaining the efficiency of the rocket.
- Oxidation Resistance: Exposure to high temperatures can cause metals to oxidize, leading to degradation. Metal powders with elements like chromium and aluminum form protective oxide layers, enhancing durability.
- Fatigue Resistance: Rocket engines undergo cyclic loading, where parts are repeatedly stressed. Metal powders must have high fatigue resistance to endure these conditions without cracking.
Detailed Composition Analysis
The composition of these metal powders isn’t random; it’s a carefully engineered mix designed to achieve specific performance characteristics. Let’s take a closer look at the elemental composition of some popular metal powders:
Metal Powder | Elemental Composition | Properties | Applications |
NiCrMo | Nickel (60-70%), Chromium (18-22%), Molybdenum (9-12%) | High corrosion resistance, thermal stability | Combustion chambers, turbine blades |
Ti-6Al-4V | Titanium (90%), Aluminum (6%), Vanadium (4%) | Excellent strength-to-weight ratio, fatigue resistance | Structural components |
AlSi10Mg | Aluminum (89-93%), Silicon (9-11%), Magnesium (0.2-0.45%) | Lightweight, good machinability | Fuel tanks, structural parts |
Tungsten | Tungsten (99.95%) | Highest melting point, high density | Nozzles, heat shields |
Each of these powders is tailored to deliver specific properties that make them suitable for particular engine components. For instance, the high chromium content in NiCrMo alloys enhances their oxidation resistance, making them ideal for parts exposed to high temperatures.
Applications of High-Temperature Metal Powders in Rocket Engines
Core Applications
High-temperature metal powders aren’t just sitting pretty—they’re actively contributing to the performance of rocket engines. Let’s explore some of the key applications where these powders truly shine.
- Combustion Chambers
- The combustion chamber is where the magic happens. Here, the fuel ignites, and temperatures skyrocket. Metal powders used in these components must be able to withstand extreme heat without melting or deforming. Nickel-based powders like Inconel 718 are often the go-to choice for these parts due to their excellent thermal stability and corrosion resistance.
- Turbines and Nozzles
- Turbines are the workhorses of the engine, converting thermal energy into mechanical work. The nozzles, on the other hand, direct the exhaust gases to produce thrust. Both of these components operate under extreme conditions, requiring materials like tungsten and molybdenum, which can handle the intense heat and stress.
- Structural Components
- Beyond the hot sections of the engine, structural components like engine casings and fuel tanks need to be both strong and lightweight. Titanium and aluminum-based powders are often used here, providing the perfect balance of durability and weight efficiency.
Case Studies
Let’s look at some real-world examples to see how these metal powders are making a difference in modern rocket engines.
- SpaceX Raptor Engine: The Raptor engine, used in SpaceX’s Starship rockets, incorporates Inconel 718 in its combustion chamber and turbine blades. This superalloy enables the engine to operate at higher pressures and temperatures than traditional rocket engines, contributing to its impressive performance.
- NASA’s RS-25 Engine: Also known as the Space Shuttle Main Engine, the RS-25 has been upgraded with advanced metal powders like titanium aluminides in its turbine blades. These materials help the engine achieve greater efficiency and reliability, crucial for deep space missions.
Specifications, Grades, and Standards
Metal Powder Specifications
When selecting metal powders for rocket engine components, several specifications need to be considered to ensure optimal performance. These include:
- Particle Size Distribution: The size of the metal particles can affect the powder’s flowability, packing density, and sintering behavior. Specifications typically range from microns to millimeters, depending on the application.
- Purity Levels: High-purity powders are essential for ensuring the mechanical properties and performance of the final component. Impurities can lead to defects, reducing the material’s strength and durability.
- Mechanical Properties: Key properties such as tensile strength, hardness, and elongation must meet specific requirements to ensure the material can withstand the stresses it will encounter in service.
Grades and Standards
Metal powders used in rocket engines must comply with stringent industry standards and are available in various grades. Here are some commonly recognized standards:
- ASTM Standards: The American Society for Testing and Materials (ASTM) sets standards for various materials, including metal powders. For example, ASTM B212 covers the standard specification for the preparation of metal powders.
- ISO Standards: The International Organization for Standardization (ISO) also provides guidelines for metal powders, ensuring consistency and quality across the industry.
- Aerospace-Specific Standards: Organizations like SAE International develop standards tailored to the aerospace industry, such as AMS (Aerospace Material Specifications), which covers requirements for metal powders used in high-performance applications.
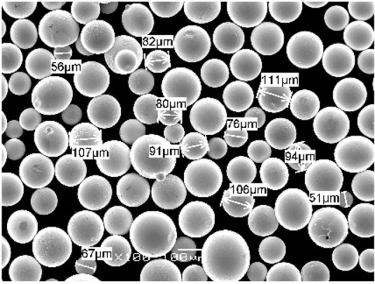
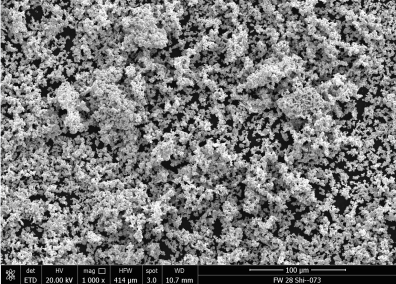
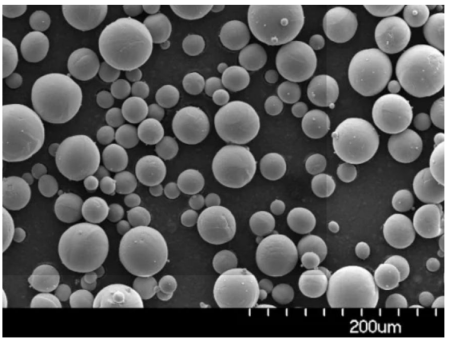
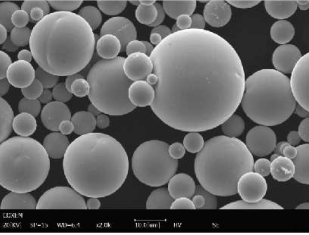
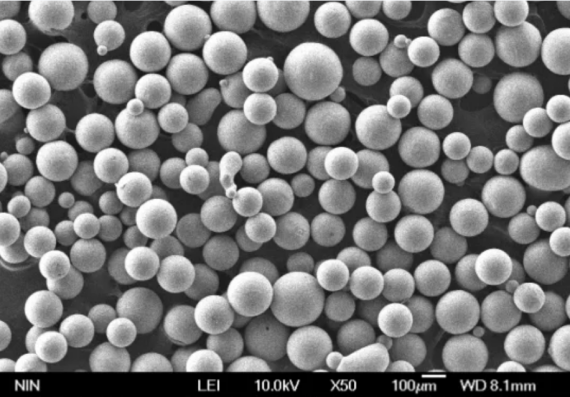
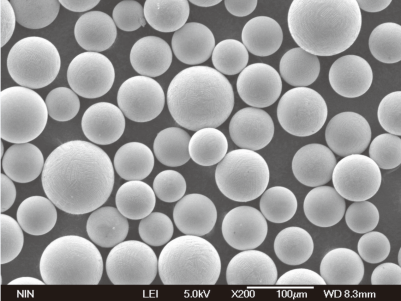
Specification Table
Here’s a detailed comparison of grades, sizes, and standards for commonly used metal powders in rocket engines:
Metal Powder | Grade | Particle Size | Purity | Standards |
---|---|---|---|---|
Inconel 718 | AMS 5662 | 15-45 microns | 99.9% | ASTM B213, AMS 5662 |
Ti-6Al-4V | Grade 5 | 20-60 microns | 99.5% | ASTM F2924, ISO 5832-3 |
AlSi10Mg | A360 | 10-50 microns | 99.8% | ISO 3522, ASTM B209 |
Tungsten | 99.95% Pure | 5-20 microns | 99.95% | ASTM B777, AMS 7848 |
Suppliers and Pricing Details
Overview of the Market
The market for high-temperature metal powders is as dynamic as the aerospace industry itself. With the increasing demand for advanced materials in rocket engines, suppliers are constantly innovating to meet the needs of their customers.
The prices of metal powders can vary significantly based on factors such as material type, purity, and particle size. For instance, refractory metal powders like tungsten are generally more expensive than aluminum or titanium powders due to their complex extraction and processing methods.
Supplier Comparison Table
To help you navigate the market, here’s a comparison of some key suppliers:
Supplier | Location | Metal Powders Available | Price Range (per kg) | Specialties |
---|---|---|---|---|
Praxair Surface Technologies | USA | Inconel 718, Ti-6Al-4V, AlSi10Mg | $50 – $150 | Aerospace-grade powders, custom alloys |
Höganäs AB | Sweden | NiCrMo, CoCrMo, AlSi10Mg | $40 – $130 | High-purity powders, ISO-certified |
Sandvik Materials Technology | Sweden | Tungsten, Molybdenum, Titanium alloys | $70 – $200 | Refractory metals, additive manufacturing |
Carpenter Technology | USA | Inconel, Stellite 6B, Ti-Al-Nb | $60 – $180 | Specialty alloys, aerospace standards |
Advantages and Limitations of High-Temperature Metal Powders
Pros of Using Metal Powders
Metal powders are revolutionizing the aerospace industry, but what exactly makes them so special? Here are some of the key advantages:
- Enhanced Engine Performance: Metal powders allow for the production of components with superior mechanical properties, such as high strength and heat resistance, directly contributing to the overall performance of rocket engines.
- Longevity and Durability: Components made from high-temperature metal powders are less prone to wear and tear, extending the lifespan of rocket engines and reducing the need for frequent maintenance.
- Cost Efficiency: While the initial cost of high-quality metal powders may be high, the long-term savings due to reduced maintenance and improved performance make them a cost-effective choice.
Cons and Challenges
However, like any technology, metal powders have their limitations:
- Manufacturing Complexities: Producing components from metal powders requires advanced manufacturing techniques such as powder metallurgy or additive manufacturing, which can be complex and costly.
- Cost Implications: The cost of raw materials and the specialized equipment needed for processing metal powders can be prohibitive, especially for small-scale operations.
- Availability Issues: Some metal powders, particularly those based on refractory metals, may be difficult to source due to limited availability and high demand in other industries.
Comparison Table
Here’s a comparison of the advantages and limitations of various metal powders:
Metal Powder | Advantages | Limitations |
---|---|---|
Inconel 718 | High-temperature stability, corrosion resistance | Expensive, requires advanced manufacturing techniques |
Ti-6Al-4V | Excellent strength-to-weight ratio, widely available | Prone to oxidation at high temperatures |
AlSi10Mg | Lightweight, good machinability | Lower strength compared to other alloys |
Tungsten | Extreme heat resistance, high density | High cost, difficult to process |
Future Trends in High-Temperature Rocket Engine Materials
Emerging Technologies
The future of high-temperature rocket engine materials is as bright as the rockets they help propel. Several emerging technologies are poised to take the industry to new heights:
- New Metal Alloys and Composites: Researchers are continually developing new alloys that offer even greater heat resistance and mechanical properties. For instance, high-entropy alloys (HEAs) are a promising new class of materials that could revolutionize rocket engine design.
- Additive Manufacturing and 3D Printing: Additive manufacturing, also known as 3D printing, is changing the way we think about manufacturing rocket engine components. By allowing for the creation of complex geometries that would be impossible with traditional manufacturing methods, 3D printing is paving the way for more efficient and lightweight engine designs.
Predicted Developments
Looking ahead, several key trends are likely to shape the future of rocket engine materials:
- Increased Use of Composites: While metal powders will continue to play a crucial role, composite materials that combine metals with ceramics or polymers may offer even greater performance advantages.
- Sustainable Manufacturing: As the aerospace industry grapples with environmental concerns, there will be a greater emphasis on developing sustainable manufacturing processes for metal powders.
- Advanced Coatings: The development of new coatings that can further enhance the performance of metal powders in extreme environments will be another area of focus.
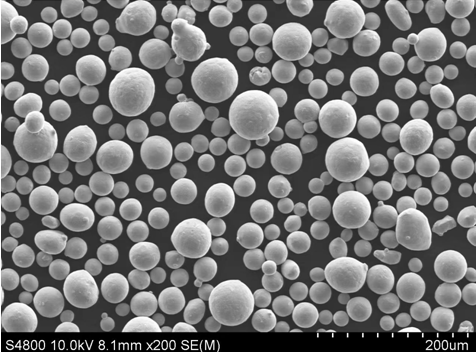
FAQ
Question | Answer | Additional Notes |
---|---|---|
What makes a material suitable for high temperatures? | A material must have a high melting point, excellent thermal stability, and resistance to oxidation and corrosion. | These properties are often achieved through careful alloying and heat treatment processes. |
How do metal powders improve rocket engine performance? | Metal powders allow for the production of components with superior mechanical properties, which directly contribute to the overall performance and efficiency of the engine. | Advanced manufacturing techniques like powder metallurgy are often used to create these high-performance parts. |
What are the challenges in sourcing these materials? | Some metal powders, especially those based on refractory metals, can be difficult to source due to limited availability and high demand in other industries. | The cost and complexity of processing these materials can also be a barrier. |
Are there environmental concerns related to metal powder production? | Yes, the extraction and processing of metal powders can have significant environmental impacts, particularly in terms of energy consumption and waste generation. | However, advances in sustainable manufacturing practices are helping to mitigate these concerns. |