When it comes to high-performance alloys designed for the most extreme conditions, Hastelloy X Powder stands out as a critical player in the world of metallurgy. Whether you’re an engineer designing components for aerospace turbines, a materials scientist seeking out heat-resistant alloys, or simply someone looking to understand why this material is so important in high-temperature applications, this article will give you the full rundown on Hastelloy X Powder.
In this guide, we will walk you through everything you need to know about Hastelloy X Powder—its composition, characteristics, applications, suppliers, and much more. We’ll break down all the technical aspects into digestible chunks, giving you the details in a way that’s both informative and engaging.
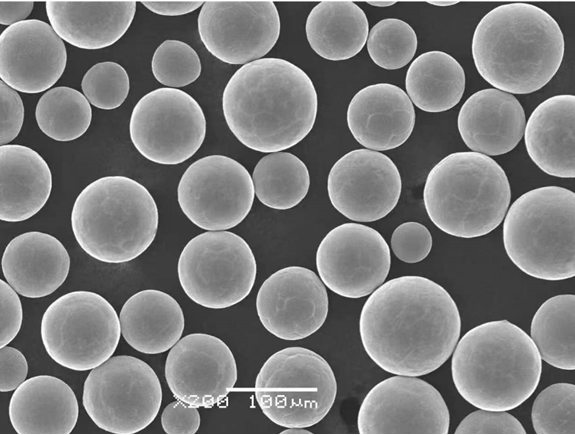
Overview of Hastelloy X Powder
Hastelloy X is a nickel-based superalloy known for its excellent strength and oxidation resistance at high temperatures. The powder form of this alloy is used widely in industries where extreme heat and corrosion resistance are required. One of the standout features of Hastelloy X is its ability to retain its mechanical properties in environments reaching up to 1200°C (2200°F), making it ideal for gas turbine engines, petrochemical equipment, and even furnace applications.
Because of these high-performance characteristics, Hastelloy X Powder is essential in the manufacture of components that must endure prolonged exposure to extreme heat without losing their structural integrity. The powder form allows for greater flexibility in manufacturing processes like additive manufacturing (3D printing), powder metallurgy, and coating applications, where precision and material properties are paramount.
Types of Hastelloy X Powder
When we talk about Hastelloy X Powder, we aren’t just talking about a single formulation. Various types and models exist, each tailored for different applications, compositions, and manufacturing techniques. Here’s a list of ten key Hastelloy X powder models along with their descriptions:
Model | Description |
---|---|
Hastelloy X-100 | Standard version for general applications in high-temperature environments. |
Hastelloy X-200 | Fine particle size powder ideal for additive manufacturing and 3D printing. |
Hastelloy X-FG | Focused on applications requiring higher corrosion resistance in chemical plants. |
Hastelloy X-S | Spherical powder optimized for laser sintering and other powder metallurgy techniques. |
Hastelloy X-C | Designed for superior performance in carburizing environments. |
Hastelloy X-T | Tailored for applications needing extra tensile strength at elevated temperatures. |
Hastelloy X-PM | Powder metallurgy grade designed for hot isostatic pressing and complex part fabrication. |
Hastelloy X-AF | Optimized for aerospace components needing high strength-to-weight ratios. |
Hastelloy X-3D | Specially formulated for 3D printing with superior flowability and consistency. |
Hastelloy X-CT | Corrosion-tolerant variant designed for continuous exposure to sulfur-bearing environments. |
Each of these models offers specific advantages depending on the application at hand, and choosing the right type of Hastelloy X powder can make a world of difference when it comes to performance and longevity in your desired application.
Composition of Hastelloy X Powder
The chemical composition of Hastelloy X is what gives it its high-performance attributes. The alloy primarily consists of nickel with significant amounts of chromium, molybdenum, and iron, as well as smaller quantities of other elements. Here’s a breakdown of the typical composition:
Element | Percentage |
---|---|
Nickel (Ni) | 47-52% |
Chromium (Cr) | 20-23% |
Molybdenum (Mo) | 8-10% |
Iron (Fe) | 17-20% |
Tungsten (W) | 0.2-1% |
Cobalt (Co) | 0.5-2.5% |
Carbon (C) | 0.05-0.15% |
Silicon (Si) | 0.50% max |
Manganese (Mn) | 1% max |
This composition makes Hastelloy X highly resistant to oxidation, carburization, and other types of corrosion, even at elevated temperatures. The combination of nickel and molybdenum provides excellent strength, while chromium enhances oxidation resistance.
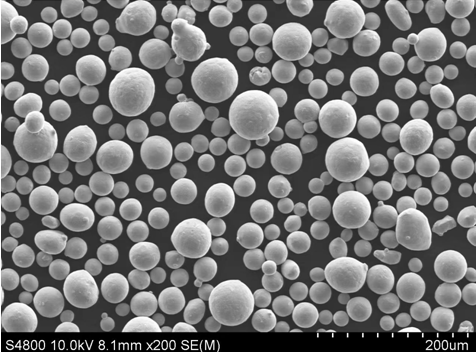
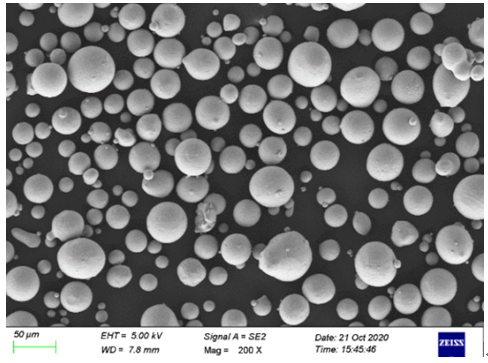
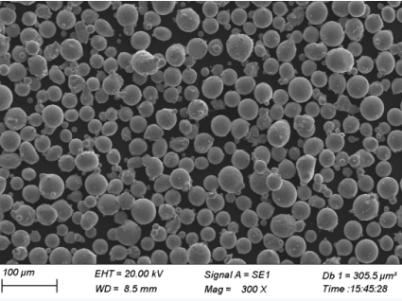
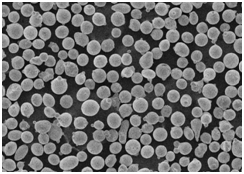
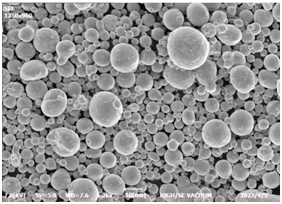
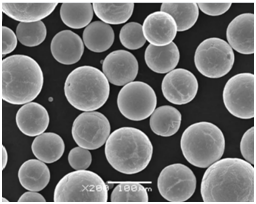
Characteristics of Hastelloy X Powder
So, what sets Hastelloy X Powder apart from other superalloys? Its characteristics can be boiled down to a few key points:
- High-Temperature Strength: Hastelloy X Powder retains its mechanical properties even in extreme heat conditions, up to 1200°C. This makes it ideal for gas turbines and other high-temperature applications.
- Oxidation Resistance: The alloy is highly resistant to oxidation, even under prolonged exposure to high temperatures. This property is essential for components in jet engines, where oxidation can cause material degradation.
- Good Ductility: Despite its strength, Hastelloy X Powder remains ductile, allowing it to be formed into complex shapes without cracking.
- Corrosion Resistance: This alloy shows excellent resistance to a variety of corrosive environments, particularly those containing halides, making it valuable in chemical processing applications.
- Fabrication Flexibility: In powder form, Hastelloy X can be used in a range of fabrication techniques, from traditional powder metallurgy to modern additive manufacturing processes.
Applications of Hastelloy X Powder
The diverse properties of Hastelloy X Powder make it indispensable in a variety of industries. Below is a table showcasing some of the key applications:
Industry | Application |
---|---|
Aerospace | Jet engine components, afterburners, combustion chambers, exhaust systems |
Petrochemical | Heat exchangers, reactors, pipes exposed to corrosive environments |
Power Generation | Gas turbine components, high-temperature furnace parts |
Automotive | Turbocharger rotors, high-performance exhaust systems |
Chemical Processing | Components for reactors, heat exchangers, and other chemical plant equipment exposed to harsh environments |
3D Printing | Complex, heat-resistant parts for aerospace, automotive, and industrial applications using additive manufacturing |
Furnace Equipment | High-temperature furnace components requiring oxidation resistance |
In each of these sectors, the use of Hastelloy X Powder allows for better performance, longer-lasting components, and increased efficiency, especially in high-stress, high-temperature environments.
Specifications and Standards of Hastelloy X Powder
To ensure that Hastelloy X Powder meets the necessary performance criteria, it is produced according to strict standards. Here’s a breakdown of the typical specifications, sizes, and standards associated with this material:
Specification | Details |
---|---|
Powder Size | Available in sizes ranging from 15 µm to 150 µm |
Standards | ASTM B572, AMS 5754, UNS N06002 |
Manufacturing Method | Gas atomization, water atomization, or plasma atomization |
Density | 8.22 g/cm³ |
Melting Point | 1355-1410°C (2471-2570°F) |
Mechanical Properties | Tensile strength: 689 MPa (100 ksi) min at room temperature |
These specifications ensure that the powder can be used across different manufacturing processes, meeting the rigorous demands of industries that rely on high-temperature materials.
Advantages and Limitations of Hastelloy X Powder
Like any material, Hastelloy X Powder has its strengths and weaknesses. Let’s break them down:
Advantages | Limitations |
---|---|
Excellent oxidation and carburization resistance | Higher cost compared to some other nickel-based alloys |
High strength at elevated temperatures | Requires precise processing methods for optimal performance |
Suitable for a range of high-stress environments | Limited machinability due to hardness |
Compatible with additive manufacturing methods | May not be suitable for low-temperature applications |
Good ductility, allowing for complex part shapes | Specialized knowledge required for effective use |
While Hastelloy X Powder is exceptionally well-suited for high-temperature applications, its higher cost and specialized processing requirements mean that it’s not always the best choice for all projects.
Suppliers and Pricing of Hastelloy X Powder
The market for Hastelloy X Powder includes a wide range of suppliers. Below is a table featuring some well-known suppliers along with indicative pricing:
Supplier | Location | Price (per kg) | Availability |
---|---|---|---|
Carpenter Technology | United States | $120-$150 | In stock, custom orders available |
Praxair Surface Technologies | United States | $140-$160 | In stock, large-scale orders possible |
Höganäs AB | Sweden | $130-$160 | Limited stock, custom production |
Kennametal | Global | $135-$155 | Standard and fine powder available |
Metal Powder Company Ltd | India | $110-$140 | Available upon request |
Prices can vary depending on the purity, particle size, and quantity ordered, so it’s always a good idea to reach out to suppliers for specific quotes tailored to your needs.
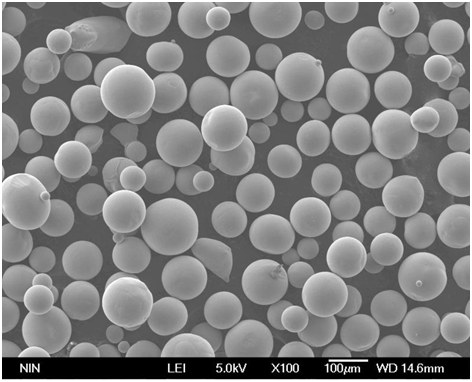
FAQ
Question | Answer |
---|---|
What makes Hastelloy X Powder unique? | Its high resistance to oxidation and carburization at elevated temperatures. |
What industries benefit from Hastelloy X? | Aerospace, petrochemical, power generation, automotive, and 3D printing. |
Is Hastelloy X Powder suitable for 3D printing? | Yes, especially tailored versions like Hastelloy X-3D are optimized for additive manufacturing. |
Can Hastelloy X be welded? | Yes, but careful control of temperature is required to prevent cracking. |
What is the price range for Hastelloy X Powder? | Typically, prices range from $110 to $160 per kilogram depending on specifications. |
Conclusion
Hastelloy X Powder stands as one of the most reliable and high-performing alloys for industries requiring extreme heat resistance, corrosion resistance, and mechanical integrity. Whether you’re crafting components for jet engines or producing highly specialized chemical processing equipment, this alloy powder has proven time and again to deliver the strength and resilience required.
From its wide range of types and models to its flexibility in various manufacturing processes, Hastelloy X Powder remains a key player in the high-temperature alloy market. Just remember, its selection comes with careful consideration of your specific project needs—whether you’re working in aerospace, petrochemical, or additive manufacturing.