When it comes to the world of gas turbine engineering, metal powders play a pivotal role. These powders are essential for manufacturing high-performance turbine components capable of withstanding extreme conditions. Let’s dive into the fascinating realm of gas turbine engineering powder, exploring its types, composition, properties, applications, and more.
Overview
Gas turbine engineering powder is used in the production of turbine components such as blades, vanes, and discs. These components require materials that can withstand high temperatures, stress, and corrosion. The powders used are often composed of superalloys and other high-performance metals.
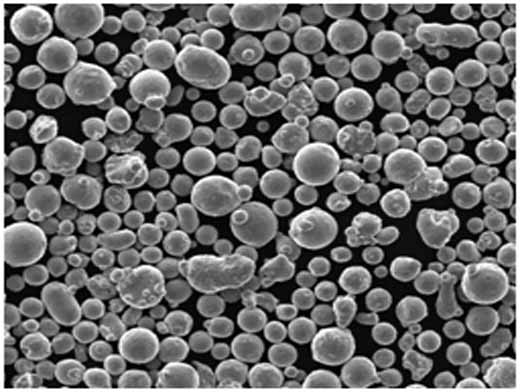
Types of Gas Turbine Engineering Powder
Powder Model | Composition | Properties | Characteristics |
---|---|---|---|
IN718 | Nickel-based superalloy | High strength, corrosion-resistant | Good weldability, oxidation resistant |
Hastelloy X | Nickel-chromium-iron-molybdenum | Heat-resistant, corrosion-resistant | High oxidation resistance |
CoCrMo | Cobalt-chromium-molybdenum | Wear-resistant, biocompatible | High strength, good thermal stability |
Ti-6Al-4V | Titanium alloy | High strength-to-weight ratio | Excellent fatigue resistance |
Rene 80 | Nickel-based superalloy | High creep resistance | Suitable for high-temperature applications |
MarM-247 | Nickel-based superalloy | High temperature strength | Good casting characteristics |
CMSX-4 | Nickel-based single-crystal alloy | Excellent high-temperature strength | Superior creep and oxidation resistance |
Nimonic 263 | Nickel-cobalt-chromium alloy | High strength, corrosion-resistant | Good weldability and formability |
Udimet 720 | Nickel-based superalloy | High tensile and creep strength | Excellent fatigue resistance |
TMS-75 | Nickel-based single-crystal alloy | Superior thermal fatigue resistance | Enhanced mechanical properties |
Composition of Gas Turbine Engineering Powder
Gas turbine powders are often composed of superalloys that include elements such as nickel, cobalt, chromium, molybdenum, aluminum, titanium, and other trace elements. These elements contribute to the powder’s high-temperature capabilities and mechanical properties.
Element | Function |
---|---|
Nickel (Ni) | Base element, provides high strength |
Chromium (Cr) | Corrosion and oxidation resistance |
Cobalt (Co) | Thermal stability and high-temperature strength |
Molybdenum (Mo) | Strengthens the alloy |
Aluminum (Al) | Enhances oxidation resistance |
Titanium (Ti) | Improves strength and toughness |
Tungsten (W) | Increases hardness and strength |
Tantalum (Ta) | Enhances high-temperature strength |
Characteristics of Gas Turbine Engineering Powder
These powders must meet stringent requirements to ensure they can withstand the harsh environments within gas turbines.
Characteristic | Description |
---|---|
High Temperature Strength | Ability to maintain strength at elevated temperatures |
Oxidation Resistance | Ability to resist oxidation at high temperatures |
Corrosion Resistance | Ability to resist chemical degradation |
Creep Resistance | Ability to resist deformation under high stress and temperature over time |
Fatigue Resistance | Ability to withstand cyclic loading without failure |
Weldability | Ease of welding without compromising mechanical properties |
Thermal Stability | Ability to maintain properties under varying thermal conditions |
Wear Resistance | Ability to resist material loss due to friction or mechanical action |
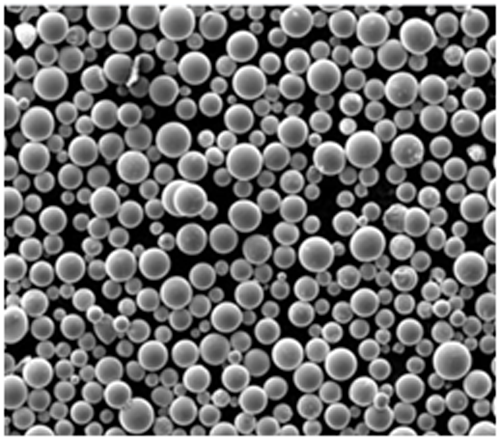
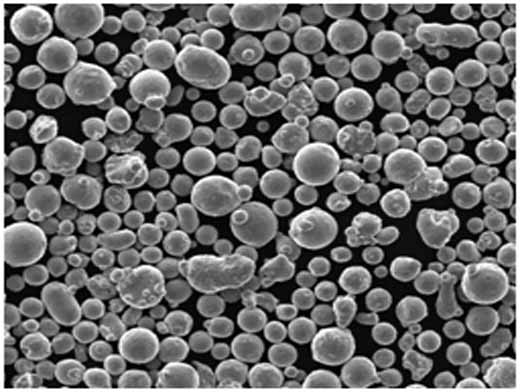
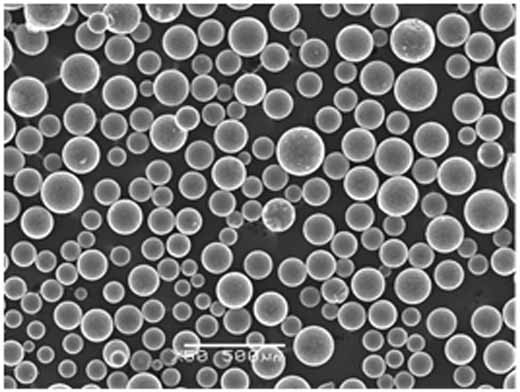
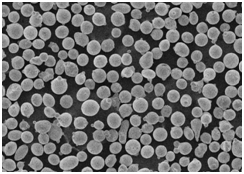
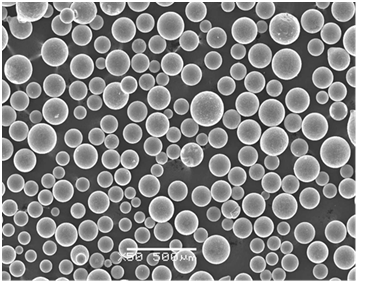
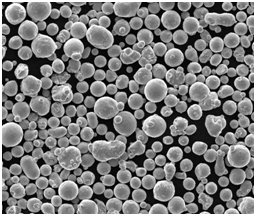
Applications of Gas Turbine Engineering Powder
Gas turbine engineering powders are utilized in various components and industries:
Application | Description |
---|---|
Turbine Blades | Components exposed to the highest temperatures and stresses |
Combustor Liners | Inner lining of the combustion chamber, requiring high oxidation resistance |
Nozzles and Vanes | Guide the flow of hot gases through the turbine |
Turbine Discs | Central part that holds the turbine blades |
Aerospace | Used in jet engines and other aerospace applications |
Power Generation | Used in industrial gas turbines for electricity generation |
Marine | Applied in marine turbines for naval vessels |
Industrial Machinery | Used in high-performance industrial engines |
Specifications, Sizes, Grades, Standards
Specifications of gas turbine powders often align with industry standards and requirements.
Specification | Size (Microns) | Grade | Standards |
---|---|---|---|
IN718 Powder | 15-53 | Grade A | AMS 5662, ASTM F3055 |
Hastelloy X Powder | 10-45 | Grade B | AMS 5754, ASTM B435 |
CoCrMo Powder | 20-63 | Grade C | ASTM F75, ISO 5832-4 |
Ti-6Al-4V Powder | 15-45 | Grade 5 | ASTM B348, AMS 4911 |
Rene 80 Powder | 20-63 | Grade D | AMS 5911, ASTM F3314 |
MarM-247 Powder | 10-50 | Grade E | AMS 5758, ASTM B595 |
CMSX-4 Powder | 20-50 | Grade F | AMS 5895, ASTM F3128 |
Nimonic 263 Powder | 15-53 | Grade G | AMS 5886, ASTM F1602 |
Udimet 720 Powder | 20-63 | Grade H | AMS 5383, ASTM F2871 |
TMS-75 Powder | 10-45 | Grade I | AMS 5917, ASTM F3353 |
Suppliers and Pricing Details
When sourcing gas turbine engineering powders, it’s important to consider reputable suppliers and pricing.
Supplier | Powder Model | Price (per kg) | Location |
---|---|---|---|
Carpenter Technology | IN718 | $200 | USA |
Haynes International | Hastelloy X | $250 | USA |
Praxair Surface Technologies | CoCrMo | $300 | USA |
Oerlikon Metco | Ti-6Al-4V | $350 | Switzerland |
ATI Metals | Rene 80 | $400 | USA |
Precision Castparts Corp. | MarM-247 | $450 | USA |
Sandvik Materials Technology | CMSX-4 | $500 | Sweden |
VDM Metals | Nimonic 263 | $550 | Germany |
Doncasters Group | Udimet 720 | $600 | UK |
AMETEK Specialty Metal Products | TMS-75 | $650 | USA |
Pros and Cons of Gas Turbine Engineering Powder
Understanding the advantages and limitations of different powders can help in making informed decisions.
Powder Model | Pros | Cons |
---|---|---|
IN718 | High strength, corrosion resistance | Expensive |
Hastelloy X | Excellent heat resistance | Difficult to machine |
CoCrMo | High wear resistance | High cost |
Ti-6Al-4V | Lightweight, high strength | Prone to cracking during welding |
Rene 80 | Superior creep resistance | Limited availability |
MarM-247 | High temperature strength | Requires precise casting techniques |
CMSX-4 | Outstanding high-temperature properties | Expensive and complex manufacturing |
Nimonic 263 | Good weldability and formability | Moderate oxidation resistance |
Udimet 720 | Excellent fatigue resistance | High cost of raw materials |
TMS-75 | Enhanced mechanical properties | Limited suppliers |
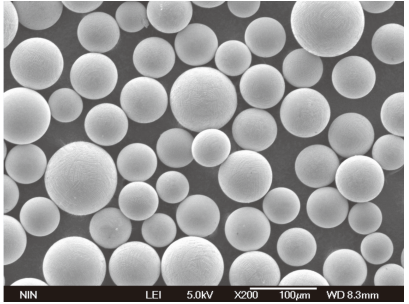
FAQ
What is gas turbine engineering powder?
Gas turbine engineering powder is a high-performance metal powder used in manufacturing components for gas turbines. These powders are typically composed of superalloys designed to withstand extreme temperatures, stress, and corrosion.
What are the primary applications of gas turbine engineering powder?
The primary applications include turbine blades, combustor liners, nozzles, vanes, and turbine discs. These components are used in aerospace, power generation, marine, and industrial machinery.
What are the key properties of gas turbine engineering powder?
Key properties include high-temperature strength, oxidation resistance, corrosion resistance, creep resistance, fatigue resistance, weldability, thermal stability, and wear resistance.
Which elements are commonly found in gas turbine engineering powders?
Common elements include nickel, cobalt, chromium, molybdenum, aluminum, titanium, tungsten, and tantalum.
Who are some reputable suppliers of gas turbine engineering powder?
Reputable suppliers include Carpenter Technology, Haynes International, Praxair Surface Technologies, Oerlikon Metco, ATI
Metals, Precision Castparts Corp., Sandvik Materials Technology, VDM Metals, Doncasters Group, and AMETEK Specialty Metal Products.
Conclusion
Gas turbine engineering powders are integral to producing high-performance turbine components. These powders, made from advanced superalloys, offer exceptional properties to withstand the extreme environments within gas turbines. Understanding the various types, compositions, and applications of these powders can help industry professionals select the right materials for their specific needs. With advancements in technology and materials science, the future of gas turbine engineering powders looks promising, paving the way for more efficient and durable turbine components.
So, whether you’re an engineer, a manufacturer, or simply someone fascinated by the intricacies of turbine technology, understanding gas turbine engineering powders is crucial. They are, after all, the unsung heroes powering our skies and generating electricity that keeps our world running.