When it comes to brazing alloys, especially for industrial applications, BNi-7 powder is a name that often comes up in technical conversations. This powder stands out because of its unique properties, compositions, and applications in various sectors. But what exactly is BNi-7 powder? How is it different from other brazing powders, and what advantages does it offer over its competitors? In this comprehensive guide, we will dive deep into the intricacies of BNi-7 powder, exploring everything from its chemical composition to its real-world applications and advantages.
Buckle up because we’re going to get into the nitty-gritty, answering all your burning questions while comparing it to other powders to see where it shines and where it might fall short.
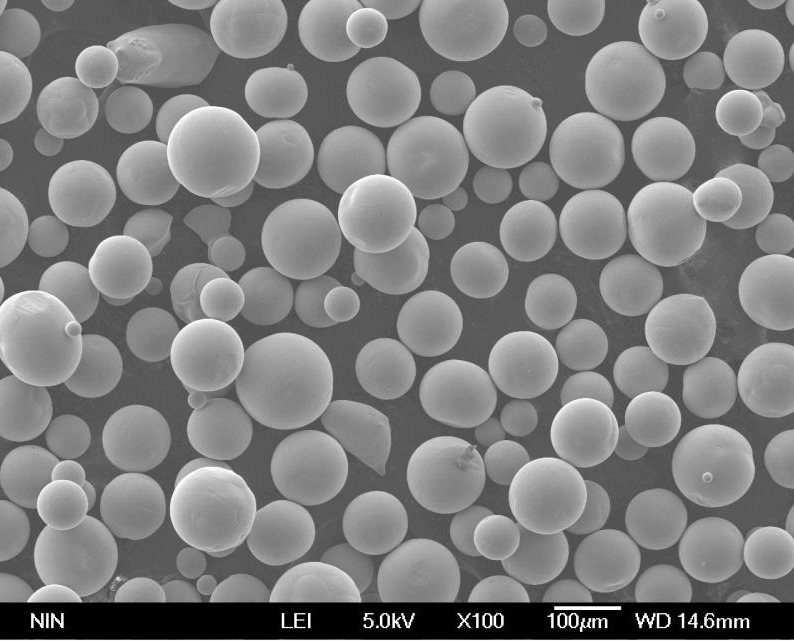
Overview of BNi-7 Powder
BNi-7 powder is a nickel-based brazing filler metal used extensively in high-temperature brazing applications. It is known for its excellent flow characteristics, corrosion resistance, and compatibility with various base materials such as stainless steel, superalloys, and heat-resistant metals. BNi-7 is particularly valued for its low melting point, which makes it ideal for applications that require precise, low-temperature brazing while maintaining strong joints.
What makes BNi-7 powder so special, though? The secret lies in its precise formulation and adaptability in challenging environments where mechanical strength, chemical resistance, and thermal stability are of utmost importance.
Key Features of BNi-7 Powder:
- Nickel-based alloy with a significant amount of boron and silicon.
- Lower melting point compared to other nickel brazing powders.
- Excellent resistance to oxidation and corrosion.
- Ideal for use in aerospace, automotive, and heat-exchanger manufacturing.
- Forms strong, durable joints without requiring extensive heat exposure.
Key Property | BNi-7 Powder |
---|---|
Melting Range | 970°C – 1000°C |
Composition | Ni, Si, B, Fe, C |
Corrosion Resistance | High |
Compatibility | Stainless steel, superalloys, etc. |
Flowability | Excellent |
Composition of BNi-7 Powder
BNi-7 powder boasts a specialized composition that gives it an edge in certain applications. The most significant components in BNi-7 powder are nickel (Ni), silicon (Si), and boron (B). Each element plays a critical role in how the powder performs during brazing and impacts the overall properties of the finished joint.
Composition Breakdown
Element | Percentage Composition (%) | Role |
---|---|---|
Nickel (Ni) | 92 – 93.5 | Provides structural integrity and corrosion resistance. |
Silicon (Si) | 4.5 – 5.5 | Lowers melting point and enhances flow characteristics. |
Boron (B) | 1.4 – 1.8 | Acts as a melting point depressant and improves wettability. |
Carbon (C) | ≤ 0.06 | Controls the microstructure of the joint and hardness. |
Iron (Fe) | ≤ 0.5 | Helps in increasing strength without compromising flow. |
Nickel, the primary component, gives BNi-7 its robustness and resistance to high temperatures and oxidation, while silicon helps the material flow smoothly during brazing. Boron, on the other hand, reduces the melting point and aids in wetting, which is crucial for forming strong, consistent bonds.
Types of BNi-7 Powder and Alternatives
While BNi-7 powder is excellent for specific applications, it’s essential to know its alternatives, especially when you’re comparing options based on cost, performance, or specific environmental needs. Here’s a list of 10 popular brazing powders, including BNi-7, with their specific characteristics:
Brazing Powders and Their Descriptions
Brazing Powder | Composition | Melting Point (°C) | Key Features | Applications |
---|---|---|---|---|
BNi-1 | Ni, Si, B, Fe | 955 – 1005 | Higher strength but higher melting point | Aerospace, high-pressure environments |
BNi-2 | Ni, Cr, Si, B | 970 – 1025 | Strong and corrosion-resistant | Turbine blades, heat exchangers |
BNi-3 | Ni, Si, B | 980 – 1065 | High strength with moderate flow | Stainless steel, high-strength joints |
BNi-4 | Ni, Cr, Si, B | 1000 – 1100 | Excellent flow and resistance | High-temperature and wear-resistant areas |
BNi-5 | Ni, Cr, Si, B | 1050 – 1120 | Superior corrosion resistance | Harsh chemical environments |
BNi-6 | Ni, Cr, Si, B | 1050 – 1100 | Versatile, great for high-temp joints | Industrial furnaces, automotive |
BNi-7 | Ni, Si, B | 970 – 1000 | Low-temp, high flow, excellent corrosion resistance | Aerospace, heat exchangers, electronics |
CuP-7 | Cu, P | 645 – 780 | Lower melting point, excellent for copper | Plumbing, HVAC systems |
Ag-45Cd | Ag, Cd, Zn, Cu | 605 – 620 | High ductility, low melting point | Electronics, precision instruments |
NiCrSi-B-4 | Ni, Cr, Si, B | 980 – 1080 | High strength and ductility | High-strength joints, turbine blades |
While BNi-7 is a standout for low-temperature applications with excellent flow properties, it has strong competition. Powders like BNi-5 are better suited for chemical resistance, while BNi-6 is more versatile in handling a wide range of high-temperature conditions.
Characteristics of BNi-7 Powder
What makes BNi-7 powder so appealing to industries across the board? It’s all about the characteristics.
- Low Melting Point: BNi-7 powder melts at a relatively low temperature (between 970°C and 1000°C). This makes it perfect for applications where you don’t want to expose your materials to excessive heat.
- Excellent Flowability: The composition of BNi-7 allows it to flow smoothly into joints, creating uniform, consistent bonds without requiring too much manipulation.
- Corrosion Resistance: Thanks to its high nickel content, BNi-7 is highly resistant to oxidation and corrosion, even in extreme environments. This makes it ideal for use in high-stress industries such as aerospace and automotive.
- Compatibility with Various Materials: Whether you’re working with stainless steel, superalloys, or heat-resistant metals, BNi-7 can handle it. Its versatility is one of the reasons why it’s widely used in various industrial applications.
Key Characteristics of BNi-7 Powder
Characteristic | Details |
---|---|
Melting Range | 970°C – 1000°C |
Corrosion Resistance | Excellent, especially in high-temperature and oxidative environments |
Flowability | Smooth, easy flow into joints |
Hardness | Moderate hardness, can be improved through heat treatments |
Compatibility | Suitable for stainless steel, superalloys, and other nickel-based alloys |
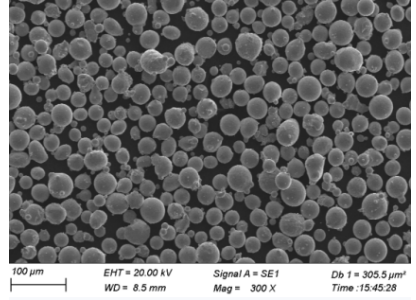
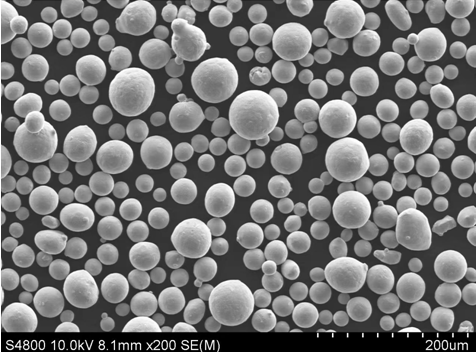
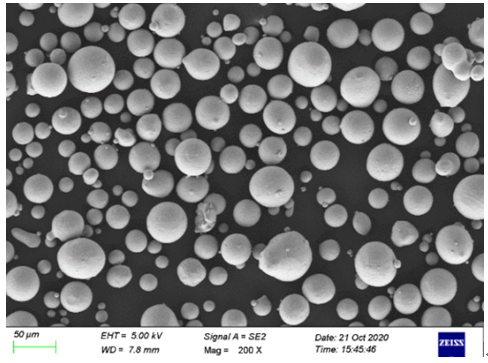
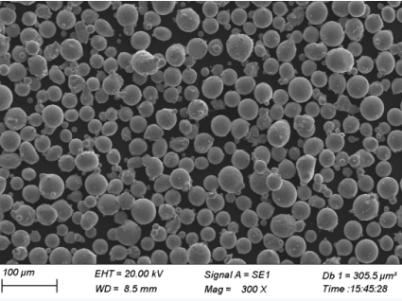
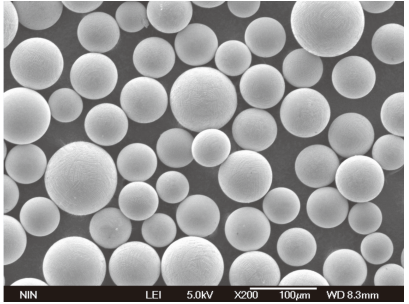
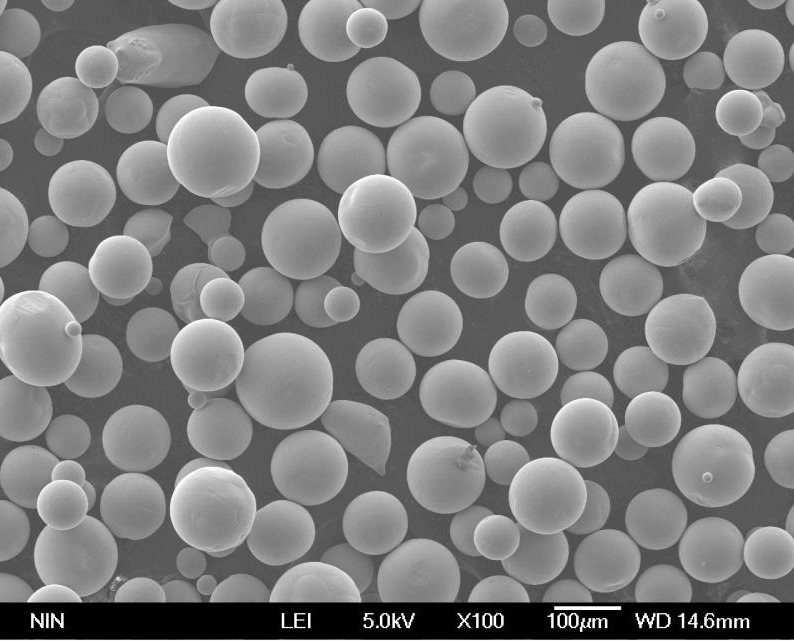
Applications of BNi-7 Powder
BNi-7 powder is the go-to material for a wide range of industrial applications due to its impressive mechanical properties and versatility. From aerospace to electronics, here’s a detailed look at the different uses of BNi-7 powder.
Applications of BNi-7 Powder
Industry | Applications |
---|---|
Aerospace | Brazing turbine blades, combustion chambers, and high-temperature engine parts. |
Automotive | Used in exhaust systems, catalytic converters, and heat exchangers. |
Electronics | Ideal for joining components in electronic devices due to low-temp brazing. |
HVAC Systems | Brazing copper and stainless steel components in heating, ventilation, and air conditioning. |
Medical Devices | Used in precision instruments where strong, corrosion-resistant joints are critical. |
Energy Sector | Essential for brazing components in turbines and heat-exchanger systems. |
Plumbing | Common in plumbing due to its ability to form strong, leak-proof seals. |
BNi-7’s adaptability, low melting temperature, and durability make it the first choice for industries that rely on consistent, high-performance bonds under challenging conditions.
Specifications, Sizes, and Standards
For those working in specialized industries, it’s essential to adhere to specific sizes, standards, and grades when working with BNi-7 powder. This ensures safety, reliability, and consistency in manufacturing processes.
BNi-7 Powder Specifications
Property | Value |
---|---|
Melting Point | 970°C – 1000°C |
Powder Sizes | 325 mesh, 100 mesh, custom sizes available |
Complies With | AWS A5.8, AMS 4777, ISO 17672 |
Powder Forms | Atomized powder, fine grain |
Manufacturers offer a variety of sizes and forms to cater to different brazing techniques and applications. Standard compliance ensures that the powder meets the required industry regulations, making it suitable for aerospace and medical applications.
Suppliers and Pricing
BNi-7 powder is readily available from various suppliers around the world, each offering different price points depending on the quantity, purity, and form of the powder.
Suppliers of BNi-7 Powder
Supplier | Pricing (per kg) | Regions |
---|---|---|
Lucas-Milhaupt | $150 – $250 | North America, Europe |
Harris Products Group | $140 – $240 | Global |
Umicore | $145 – $255 | Europe, Asia |
Johnson Matthey | $135 – $230 | North America, Europe |
Wesco | $130 – $220 | USA, Canada |
Metallisation Ltd. | $145 – $240 | UK, Europe |
Wall Colmonoy | $150 – $260 | Global |
Pricing varies significantly based on the region, purity, and form of the powder. Many suppliers also offer bulk discounts for large industrial orders, making it more economical for large-scale manufacturers.
Advantages of BNi-7 Powder
Let’s cut to the chase—why should you choose BNi-7 powder over others? Here are the main reasons:
Advantages of BNi-7 Powder
- Low Melting Temperature: Compared to other nickel-based brazing alloys, BNi-7 has a significantly lower melting point, reducing the risk of overheating and damaging base materials.
- Corrosion Resistance: The high nickel content ensures exceptional resistance to oxidation and corrosion, especially in high-temperature environments.
- Smooth Flow: Its ability to flow effortlessly into small crevices and form uniform joints makes it ideal for precision work.
- Compatibility: It can bond with various materials, making it versatile for different industries.
- Reduced Heat Exposure: Since it requires less heat to melt, there’s less risk of warping or distorting the materials being brazed.
Disadvantages of BNi-7 Powder
- Cost: BNi-7 powder can be more expensive than some other options, especially copper-based powders, making it less appealing for cost-sensitive applications.
- Not Ideal for High-Temperature Applications: If your project involves extremely high temperatures, you might want to opt for something like BNi-5, which can withstand more heat.
- Limited Hardness: For applications requiring very high hardness, additional treatments may be required to enhance the strength of the joints formed by BNi-7.
BNi-7 Powder Compared to Other Metal Powders
How does BNi-7 stack up against other popular brazing powders in the market? Let’s take a look:
Feature | BNi-7 | BNi-5 | CuP-7 | Ag-45Cd |
---|---|---|---|---|
Melting Point | 970°C – 1000°C | 1050°C – 1120°C | 645°C – 780°C | 605°C – 620°C |
Corrosion Resistance | High | Very High | Moderate | Low |
Cost | Moderate | High | Low | High |
Application Suitability | Aerospace, heat exchangers | Chemical environments | Plumbing, HVAC | Electronics, instruments |
Flowability | Excellent | Moderate | Excellent | Very Good |
BNi-7 Powder vs. Other Metal Powders: Breaking it Down
In comparing BNi-7 to other powders, it’s clear that each option has its pros and cons. For instance, BNi-5 may have a higher melting point and better corrosion resistance, making it more suitable for harsh environments like chemical processing plants. On the other hand, CuP-7 shines in applications like plumbing, where its low melting point and excellent flowability make it an economical choice.
BNi-7 finds its sweet spot in low-temperature brazing applications with a need for robust, corrosion-resistant joints. Compared to Ag-45Cd, which is used in electronics, BNi-7 is far superior in terms of temperature resistance but comes at a higher price point due to the base metals involved.
Pros and Cons of BNi-7 Powder
Understanding the advantages and limitations of BNi-7 powder will help you make an informed decision when choosing the right brazing material for your project.
Advantages of BNi-7 Powder
Advantage | Why It Matters |
---|---|
Low Melting Point | Reduces thermal stress on sensitive materials, preventing warping. |
Superior Flowability | Ensures uniform joints, even in hard-to-reach areas, improving overall quality. |
Corrosion Resistance | Prolongs the life of brazed components, particularly in high-heat and corrosive environments. |
Versatility | Compatible with a wide range of metals, making it usable in various industries. |
Lower Heat Requirement | Minimizes damage to base metals, which is especially critical in precision engineering. |
Limitations of BNi-7 Powder
Limitation | Why It Can Be a Drawback |
---|---|
Higher Cost | Compared to copper-based alloys, BNi-7 can be pricier, affecting large-scale project budgets. |
Not Suitable for Very High Temperatures | If the operating environment exceeds 1000°C regularly, BNi-7 may not hold up as well as other options like BNi-5. |
Limited Hardness | For applications requiring high hardness, additional post-brazing heat treatment might be necessary. |
How to Use BNi-7 Powder: Step-by-Step Guide
If you’re gearing up to use BNi-7 powder in your next project, it’s essential to follow the right brazing procedures to achieve optimal results. While BNi-7 is relatively easy to work with, understanding its nuances can help you get the best possible bond.
Step 1: Surface Preparation
Before brazing, the surface of the base materials must be thoroughly cleaned. This step removes any oxides, oils, or dirt that could interfere with the bonding process. Depending on the materials used, this might involve abrasive cleaning, chemical cleaning, or both.
Step 2: Flux Application
For some materials, applying flux is essential to prevent oxidation during the heating process. However, many applications of BNi-7—particularly in vacuum brazing—don’t require flux because the controlled environment eliminates the need for oxidation prevention.
Step 3: Powder Application
Next, BNi-7 powder is applied to the joint area. This can be done by brushing or sprinkling the powder onto the joint, ensuring even coverage across the entire surface to be bonded. Alternatively, BNi-7 powder is sometimes applied as a paste mixed with a binder for more control in precision applications.
Step 4: Heating
Once the powder is in place, it’s time to heat the assembly. Depending on your setup, this can be done in a furnace, with a torch, or through induction heating. The key is to raise the temperature gradually to ensure even heat distribution, reaching between 970°C and 1000°C, allowing the BNi-7 to melt and flow into the joint.
Step 5: Cooling and Post-Brazing
After the joint has been brazed, allow the assembly to cool naturally. In some cases, post-brazing heat treatments may be necessary to increase the hardness or strength of the bond.
BNi-7 Powder Suppliers and Pricing Comparison
Sourcing high-quality BNi-7 powder is crucial for ensuring the success of your brazing operations. Let’s take a closer look at some key suppliers and their pricing.
Top BNi-7 Powder Suppliers
Supplier | Product Type | Price Range (per kg) | Shipping Regions | Lead Time |
---|---|---|---|---|
Lucas-Milhaupt | Atomized powder, paste | $150 – $250 | North America, Europe | 1-2 weeks |
Harris Products Group | Atomized powder | $140 – $240 | Global | 2-3 weeks |
Wall Colmonoy | Fine powder, custom blends | $150 – $260 | Global | 1-3 weeks |
Johnson Matthey | Fine grain powder | $135 – $230 | North America, Europe | 1-2 weeks |
Wesco | Atomized powder | $130 – $220 | USA, Canada | 1-2 weeks |
Umicore | Powder, customized sizes | $145 – $255 | Europe, Asia | 2-4 weeks |
BNi-7 powder is widely available from suppliers around the world. Prices vary based on factors such as purity, particle size, and bulk quantity. Keep in mind that bulk orders often come with price breaks, and lead times can fluctuate based on demand.
BNi-7 Powder: Applications in Different Industries
BNi-7 powder is incredibly versatile, finding use across various industries, including aerospace, automotive, electronics, and more. Here, we break down some of the most common applications and why BNi-7 is the preferred choice in each case.
1. Aerospace Industry
In aerospace applications, BNi-7 powder is used for brazing turbine blades, engine parts, and combustion chambers. Its low melting point and ability to form strong, oxidation-resistant joints make it a critical material in environments that experience high heat and mechanical stress. The superior flowability of BNi-7 ensures that complex, thin-walled components are brazed without compromising their integrity.
Why BNi-7?
The high nickel content provides excellent resistance to both high temperatures and corrosive environments, which is vital for aerospace components that operate in extreme conditions.
2. Automotive Industry
In the automotive sector, BNi-7 powder is used for brazing components such as catalytic converters, exhaust systems, and heat exchangers. The key advantage here is its ability to form strong, leak-proof joints at relatively low temperatures, which helps prevent thermal distortion in delicate automotive parts.
Why BNi-7?
Its low melting point and corrosion resistance are critical for brazing components that are exposed to exhaust gases and high temperatures over extended periods.
3. Electronics Industry
BNi-7 powder is also widely used in the electronics industry for joining components that require precise, low-temperature brazing. From microelectronics to larger assemblies, BNi-7 ensures strong, reliable joints without damaging sensitive electrical components.
Why BNi-7?
BNi-7’s ability to flow into small, intricate joints without excessive heat exposure makes it perfect for sensitive electronic components.
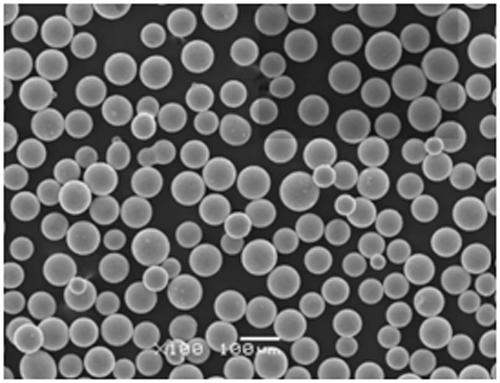
FAQs
1. What is BNi-7 powder used for?
BNi-7 powder is used for high-temperature brazing applications in industries like aerospace, automotive, and electronics. Its excellent corrosion resistance, low melting point, and ability to form strong, durable joints make it ideal for brazing metals such as stainless steel, superalloys, and heat-resistant materials.
2. What are the main advantages of using BNi-7 powder over other brazing powders?
BNi-7 powder offers several advantages, including:
- Lower melting point, which reduces heat stress on base materials.
- Excellent flowability, making it easier to form uniform joints.
- High resistance to corrosion and oxidation, especially in high-temperature environments.
3. Is BNi-7 powder suitable for high-stress environments like aerospace?
Yes, BNi-7 powder is widely used in aerospace applications due to its strong mechanical properties, corrosion resistance, and ability to withstand high temperatures. It’s particularly useful for brazing turbine blades, engine components, and other critical parts.
4. How does BNi-7 powder compare to other nickel-based brazing alloys like BNi-5?
BNi-7 powder has a lower melting point compared to BNi-5, which makes it more suitable for low-temperature brazing applications. However, BNi-5 offers superior corrosion resistance and strength in extreme environments, which is why it’s often used in chemical processing or other high-stress industries.
5. Can BNi-7 powder be used in vacuum brazing?
Yes, BNi-7 powder is ideal for vacuum brazing due to its low melting point and high flowability. In fact, it is commonly used in vacuum brazing applications where the absence of flux is preferred, and a clean, strong bond is required.
6. How should I store BNi-7 powder to maintain its quality?
BNi-7 powder should be stored in a dry, cool environment away from moisture and contaminants. Proper
storage will help preserve its properties, ensuring that it maintains its flowability and brazing quality over time.
Conclusion
BNi-7 powder is a standout material in the brazing world, prized for its low melting point, superior flowability, and resistance to corrosion and oxidation. Whether you’re working in aerospace, automotive, or electronics, this powder can help you create strong, reliable joints with minimal heat exposure, preserving the integrity of your base materials.
With various suppliers offering BNi-7 powder in different forms and sizes, you’ll find plenty of options to suit your specific needs. Just remember to weigh the pros and cons—like the cost versus its outstanding performance—and consider your application’s unique requirements.
Choosing the right brazing material can be the difference between a joint that lasts and one that fails under pressure. And when you need a reliable, high-performance option, BNi-7 powder consistently delivers.