Overview of BNi-7 Powder
If you’ve been researching brazing alloys or materials for high-temperature applications, you’ve probably come across BNi-7 powder. It’s a specialized nickel-based brazing alloy, widely used in various industries for its excellent resistance to corrosion and oxidation, along with its ability to form strong, reliable joints. But what exactly makes BNi-7 stand out? And why is it so popular across different fields?
BNi-7 powder is a blend of several elements, including nickel, phosphorus, and boron. These elements combine to create a brazing alloy with a low melting point, making it ideal for precision brazing in delicate and high-temperature environments. Whether you’re working on aerospace components or high-performance engines, BNi-7 provides a versatile solution for your brazing needs.
In this guide, we’ll dive deep into every aspect of BNi-7 powder—from its chemical composition to its real-world applications. We’ll even throw in a few product comparisons and highlight some of the top suppliers so you know exactly where to go when you’re ready to buy.
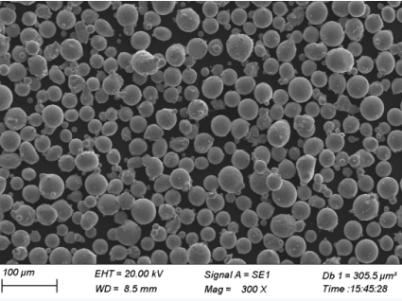
Composition of BNi-7 Powder
Understanding the composition of BNi-7 powder is crucial if you want to fully appreciate its capabilities. The key ingredients in BNi-7 powder include nickel, phosphorus, and boron, which come together to form a unique alloy with desirable properties for industrial applications.
Below is a table summarizing the composition of BNi-7 powder.
Element | Percentage Composition (%) |
---|---|
Nickel (Ni) | 92.8-93.8 |
Phosphorus (P) | 6.8-7.2 |
Boron (B) | 0.03-0.06 |
Nickel (Ni)
Nickel, the primary element, gives BNi-7 its excellent resistance to corrosion and oxidation. It’s the backbone of the alloy, ensuring durability in high-stress environments.
Phosphorus (P)
Phosphorus lowers the melting point of the alloy, making it easier to use in precision brazing operations. It also contributes to the formation of strong, ductile joints.
Boron (B)
Although present in small quantities, boron helps in reducing the melting range even further, allowing the alloy to flow more easily when heated.
Properties and Characteristics of BNi-7 Powder
When selecting a brazing alloy like BNi-7, it’s important to consider its physical and mechanical properties. What makes BNi-7 so attractive to engineers is its combination of a low melting point, high corrosion resistance, and strong mechanical properties.
Let’s break down the key characteristics that define BNi-7 powder.
Property | Value |
---|---|
Melting Point | 875°C – 890°C |
Density | 8.7 g/cm³ |
Corrosion Resistance | Excellent in many environments |
Oxidation Resistance | High, even at elevated temperatures |
Flow Characteristics | Excellent fluidity at melting point |
Joint Strength | High mechanical strength |
Melting Point
BNi-7’s low melting point (around 875°C) allows it to be used in brazing processes where precision is key. This is particularly useful for components that cannot withstand extremely high temperatures.
Corrosion and Oxidation Resistance
One of the standout features of BNi-7 powder is its superior resistance to corrosion and oxidation, even at high temperatures. This makes it ideal for environments where components are exposed to harsh conditions, such as aerospace or chemical processing plants.
Mechanical Strength
Despite its low melting point, the brazed joints formed with BNi-7 are incredibly strong. This mechanical strength ensures that parts bonded with BNi-7 can withstand significant stress, making it suitable for load-bearing applications.
Advantages of BNi-7 Powder
Now that we’ve looked at the composition and properties of BNi-7 powder, let’s explore its advantages over other types of brazing alloys. Why is it considered superior in so many applications?
Advantage | Description |
---|---|
Low Melting Temperature | Easier to work with in precision brazing applications |
Corrosion and Oxidation Resistance | Can be used in harsh environments without degrading |
High Joint Strength | Provides strong, reliable connections between parts |
Excellent Fluidity | Flows well at brazing temperature, ensuring complete coverage |
Versatility | Can be used in various industries including aerospace, automotive, and electronics |
Low Melting Temperature
Compared to other brazing alloys like BNi-5 or BNi-2, BNi-7 has a lower melting temperature, which makes it easier to apply in delicate or heat-sensitive applications. This is particularly useful when working with thin or small components that could warp under excessive heat.
Corrosion Resistance
BNi-7 outperforms many other alloys in environments that are prone to corrosion and oxidation, making it a top choice for chemical processing plants, boilers, and aerospace applications where reliability is critical.
Mechanical Strength
When you need a brazed joint that can handle stress, BNi-7 delivers. Its high mechanical strength makes it a better option for load-bearing applications than softer, weaker alloys.
Comparison of BNi-7 Powder with Other Nickel-Based Brazing Alloys
When choosing a brazing alloy, it’s helpful to compare BNi-7 with other available options to see how it stacks up. Below is a comparison table between BNi-7 and several other nickel-based brazing alloys, such as BNi-1, BNi-2, BNi-3, BNi-4, and BNi-5.
Alloy | Melting Point (°C) | Corrosion Resistance | Joint Strength | Best Applications |
---|---|---|---|---|
BNi-7 | 875-890 | Excellent | High | Aerospace, chemical processing |
BNi-1 | 955-980 | Moderate | Moderate | General-purpose brazing |
BNi-2 | 970-995 | Good | High | High-temperature applications |
BNi-3 | 970-1005 | Excellent | Very High | Gas turbines, engines |
BNi-4 | 995-1010 | High | Very High | Aerospace, high-stress applications |
BNi-5 | 1050-1070 | Low | Very High | Very high-temperature applications |
BNi-7 vs BNi-5
While BNi-5 has a higher joint strength, it also comes with a much higher melting point (1050-1070°C), which makes it more difficult to work with in temperature-sensitive applications. In contrast, BNi-7’s lower melting point makes it a better choice for precision brazing.
BNi-7 vs BNi-2
Compared to BNi-2, BNi-7 has a lower melting temperature but maintains excellent joint strength and corrosion resistance. If your application requires a lower heat load, BNi-7 is generally a better option.
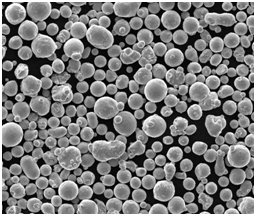
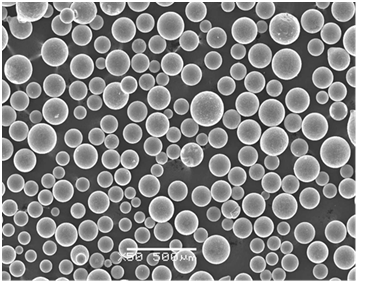
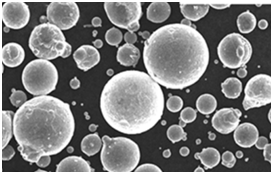
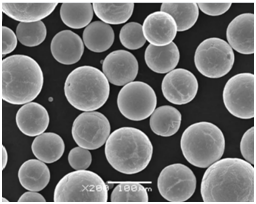
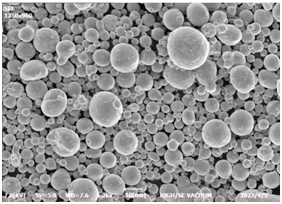

Applications of BNi-7 Powder
BNi-7 is used across a wide range of industries thanks to its unique blend of properties. Let’s explore some of the key applications of BNi-7 powder:
Industry | Application |
---|---|
Aerospace | Joining turbine blades, engine components, heat exchangers |
Automotive | Brazing of exhaust systems, turbochargers, and fuel injectors |
Chemical Processing | Joining components exposed to corrosive chemicals |
Electronics | Brazing of heat sinks, RF shields, and other delicate components |
Power Generation | Brazing components for boilers, turbines, and power plant systems |
Aerospace
In the aerospace industry, BNi-7 is commonly used for brazing critical components like turbine blades and heat exchangers, where high strength and corrosion resistance are essential. These components often operate in extreme environments with high temperatures and corrosive gases.
Automotive
BNi-7 powder is used in the automotive industry for brazing components like exhaust systems, turbochargers, and fuel injectors. The alloy’s ability to withstand high temperatures and resist corrosion makes it perfect for these high-performance applications.
Specifications and Standards for BNi-7 Powder
BNi-7 powder is available
in various grades and sizes, and it conforms to a variety of industry standards. The following table provides an overview of specifications that manufacturers and suppliers typically follow for BNi-7 powder.
Specification | Description |
---|---|
Powder Size | 45-150 µm (typical range) |
Conforming Standards | AWS A5.8, AMS 4777, ISO 17672 |
Packing Size | Available in 1 kg, 5 kg, 10 kg |
Form | Powder, paste, preforms |
Purity | 99%+ Nickel content |
Standards
BNi-7 powder must meet the standards set by organizations like the American Welding Society (AWS) and Aerospace Material Specifications (AMS) to ensure consistent quality and performance. For example, AWS A5.8 is a widely recognized standard for filler metals used in brazing.
Top Suppliers of BNi-7 Powder and Pricing
Finding a reputable supplier for BNi-7 powder is crucial, especially when working on critical applications. Here are some of the top suppliers of BNi-7 powder, along with an approximate pricing guide.
Supplier | Price (per kg) | Form | Minimum Order |
---|---|---|---|
Vesuvius | $200-$250 | Powder, paste | 1 kg |
Wall Colmonoy | $220-$270 | Powder | 5 kg |
Morgan Advanced Materials | $230-$280 | Powder, preforms | 2 kg |
Lucas-Milhaupt | $210-$260 | Powder, preforms | 1 kg |
Pricing
Prices for BNi-7 powder typically range from $200 to $280 per kilogram, depending on the supplier, order size, and form (powder, paste, or preforms). The price can fluctuate based on factors like purity, powder size, and order quantity.
Pros and Cons of Using BNi-7 Powder
Like any material, BNi-7 powder comes with its advantages and limitations. Here’s a breakdown of the pros and cons of using BNi-7 powder in brazing applications.
Pros | Cons |
---|---|
Low melting temperature | Higher cost compared to some alternatives |
High corrosion resistance | Limited to non-ferrous applications |
Strong mechanical properties | Requires specialized handling equipment |
Excellent fluidity and flow characteristics | Can be difficult to obtain in small quantities |
Advantages
BNi-7 excels in corrosion resistance, flow characteristics, and mechanical strength, making it suitable for high-performance applications where precision and durability are key.
Disadvantages
However, it does come with some limitations, including a higher price compared to simpler brazing alloys like BNi-1 or BNi-2. It also tends to be more challenging to source in small quantities, which can be a problem for hobbyists or smaller shops.
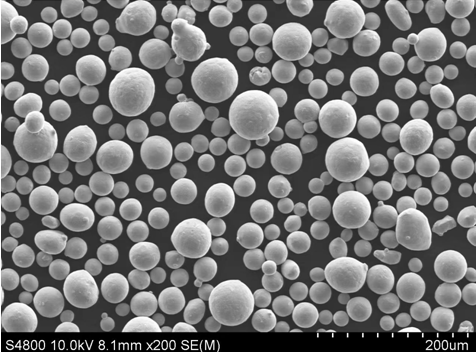
FAQ
Q: What is the main advantage of BNi-7 powder compared to other brazing alloys?
A: BNi-7 powder has a low melting point and high corrosion resistance, making it ideal for high-performance applications where precision and durability are required.
Q: Can BNi-7 powder be used in automotive applications?
A: Yes, BNi-7 is commonly used in the automotive industry for brazing exhaust systems, fuel injectors, and turbochargers.
Q: What is the melting temperature range of BNi-7 powder?
A: The melting temperature of BNi-7 powder ranges from 875°C to 890°C, which is relatively low compared to other nickel-based brazing alloys.
Q: Is BNi-7 powder suitable for high-temperature applications?
A: Yes, BNi-7 can withstand high temperatures and has excellent oxidation resistance, making it suitable for applications such as turbine blades and heat exchangers.
Q: Where can I buy BNi-7 powder?
A: BNi-7 powder is available from major suppliers such as Vesuvius, Wall Colmonoy, Lucas-Milhaupt, and Morgan Advanced Materials.
Conclusion
In summary, BNi-7 powder is a highly versatile brazing alloy that excels in corrosion resistance, oxidation resistance, and mechanical strength, making it ideal for a wide range of industries, from aerospace to automotive. Its low melting point allows for precision brazing, even in temperature-sensitive applications.
Whether you’re brazing turbine blades, exhaust systems, or heat exchangers, BNi-7 delivers consistent, reliable results. While it may come with a higher price tag compared to simpler alloys, its superior properties make it well worth the investment for high-performance, high-stress applications.
If you’re in the market for BNi-7 powder, remember to consider factors like purity, powder size, and supplier reputation. With a wealth of options available, you can find the perfect BNi-7 product to meet your specific needs.