Additive manufacturing, often known as 3D printing, has revolutionized manufacturing industries by enabling the creation of complex, custom-designed components. Among the various additive manufacturing techniques, Binder Jetting Additive Manufacturing (BJAM) stands out for its versatility and cost-effectiveness. This article delves deep into the world of Binder Jetting, providing an extensive overview, examining specific metal powder models, and discussing the technology’s applications, advantages, and limitations. Whether you’re a seasoned professional or new to the concept, this guide will walk you through the ins and outs of Binder Jetting, ensuring you have all the information you need.
Overview of Binder Jetting Additive Manufacturing
Binder Jetting is a unique additive manufacturing technique that combines powder-based materials with a liquid binding agent. Unlike other 3D printing methods that use heat to fuse materials, Binder Jetting relies on this binder to create the desired shapes. The process is typically done layer by layer, where the binder selectively “glues” the metal or ceramic particles together, forming a solid object.
Binder Jetting’s ability to work with various materials, from metals to ceramics to sand, makes it a versatile choice. Additionally, the lack of heat application reduces the risk of thermal distortion, making it ideal for complex geometries and delicate structures.
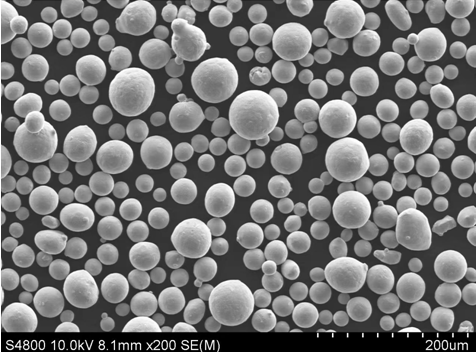
Composition of Binder Jetting Additive Manufacturing
Binder Jetting utilizes a combination of powdered materials and a liquid binder. The powder materials used in Binder Jetting are crucial to the final product’s characteristics. Below is a detailed breakdown of specific metal powder models used in Binder Jetting.
Specific Metal Powder Models in Binder Jetting
Metal Powder Model | Composition | Properties | Characteristics | Applications |
---|---|---|---|---|
Inconel 625 | Nickel-Chromium | High strength, excellent fatigue resistance | Corrosion-resistant, good weldability | Aerospace, marine, chemical processing |
316L Stainless Steel | Iron-Chromium-Nickel | Excellent corrosion resistance, good strength | Ductile, biocompatible | Medical implants, automotive, food processing |
17-4 PH Stainless Steel | Iron-Chromium-Nickel-Copper | High strength, hardness | Precipitation hardened, corrosion-resistant | Aerospace, nuclear, chemical industries |
Cobalt-Chrome | Cobalt-Chromium | High wear resistance, biocompatible | Dense, strong | Dental implants, aerospace, medical devices |
Copper (Cu) | Pure Copper | Excellent electrical conductivity, thermal conductivity | Malleable, ductile | Electrical components, heat exchangers |
Titanium (Ti-6Al-4V) | Titanium-Aluminum-Vanadium | High strength-to-weight ratio, corrosion-resistant | Biocompatible, strong | Aerospace, medical implants, sports equipment |
Aluminum (AlSi10Mg) | Aluminum-Silicon-Magnesium | Lightweight, good strength | High thermal conductivity, ductile | Automotive, aerospace, consumer electronics |
Bronze | Copper-Tin | High corrosion resistance, good machinability | Dense, strong | Artistic sculptures, bearings, bushings |
Tool Steel (H13) | Chromium-Molybdenum | High hardness, wear resistance | Heat-resistant, tough | Tooling, molds, dies |
Nickel Alloy 718 | Nickel-Chromium-Iron | Excellent high-temperature strength, corrosion resistance | Age-hardenable, strong | Aerospace, power generation, oil & gas |
Characteristics of Binder Jetting Additive Manufacturing
The characteristics of Binder Jetting Additive Manufacturing make it distinct from other additive manufacturing techniques. Here’s a breakdown of the key characteristics:
Material Versatility
Binder Jetting works with a wide range of materials, including metals, ceramics, and even sand. This versatility allows for various applications across different industries, from aerospace to dental.
Surface Finish
One of the notable characteristics of Binder Jetting is the ability to achieve a fine surface finish. The layer-by-layer deposition and fine powder particles contribute to smooth surfaces, reducing the need for extensive post-processing.
Production Speed
Binder Jetting is known for its relatively high production speed. Since the process doesn’t require significant thermal energy, it can print large batches of parts quickly, making it suitable for both prototyping and production.
No Thermal Stress
Unlike other methods, such as Selective Laser Sintering (SLS) or Direct Metal Laser Sintering (DMLS), Binder Jetting does not involve high temperatures. This eliminates thermal stress, reducing the risk of warping or distortion in the final product.
Design Flexibility
With Binder Jetting, complex geometries and intricate designs can be easily achieved. This method allows for the creation of internal cavities, lattice structures, and other features that would be challenging to produce with traditional manufacturing.
Applications of Binder Jetting Additive Manufacturing
Binder Jetting Additive Manufacturing finds applications across various industries due to its versatility and ability to produce complex parts. Below is an exploration of some key applications:
Application | Description | Industries |
---|---|---|
Prototyping | Rapid prototyping of parts with complex geometries for testing and validation | Automotive, aerospace, consumer goods |
Tooling and Molds | Production of durable tools and molds used in various manufacturing processes | Injection molding, die casting |
Medical Devices | Manufacturing of custom implants, surgical tools, and dental fixtures | Medical, dental |
Aerospace Components | Production of lightweight, complex parts with high strength and corrosion resistance | Aerospace, defense |
Automotive Parts | Manufacturing of custom and complex parts for automotive applications, such as engine components | Automotive |
Artistic and Decorative Items | Creation of detailed sculptures, jewelry, and decorative items using various metal powders | Art, fashion, home decor |
Heat Exchangers | Production of complex heat exchanger designs with high thermal conductivity materials | HVAC, industrial equipment |
Electrical Components | Manufacturing of components with excellent electrical conductivity, such as connectors and busbars | Electronics, electrical engineering |
Casting Patterns | Production of sand molds and cores for metal casting processes | Foundry, metal casting |
Research and Development | Custom materials and design testing for new products and innovations | R&D, academic institutions |
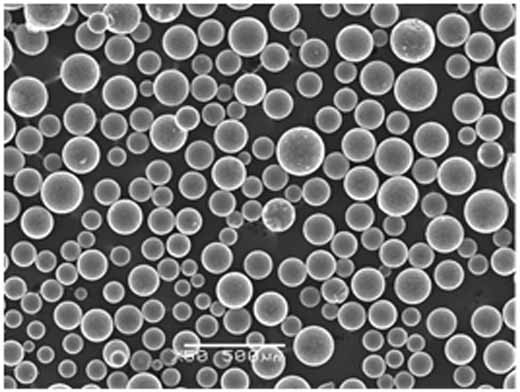
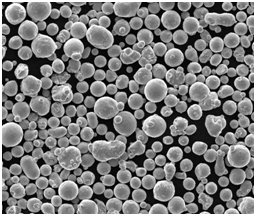
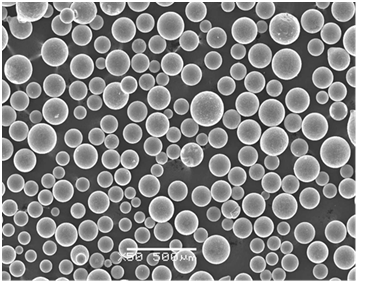
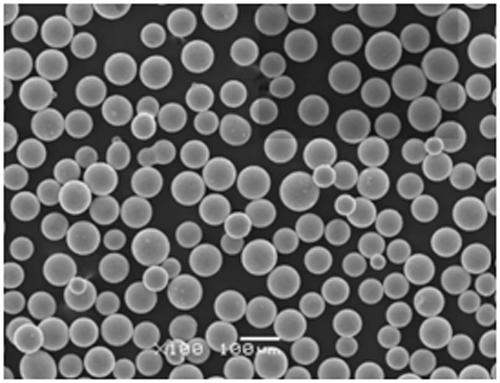
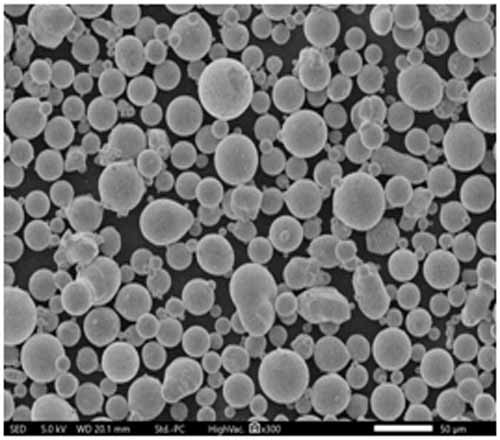
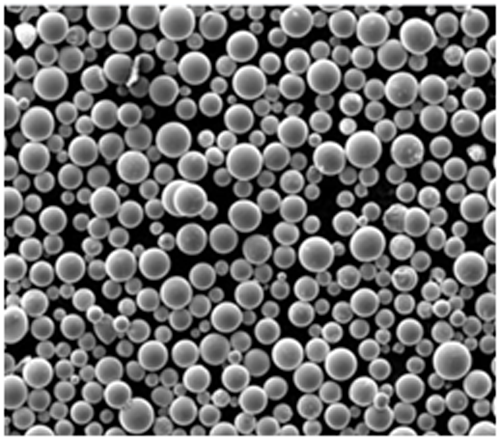
Specifications, Sizes, Grades, and Standards in Binder Jetting
Understanding the specifications, sizes, grades, and standards associated with Binder Jetting is crucial for ensuring that parts meet industry requirements. Below is a detailed table outlining these aspects:
Material | Grade/Standard | Typical Sizes | Specifications |
---|---|---|---|
Inconel 625 | AMS 5666, ASTM B443 | Powder size: 15-45 µm | Density: 8.44 g/cm³, Melting Point: 1290-1350°C |
316L Stainless Steel | ASTM F138, ISO 5832-1 | Powder size: 15-53 µm | Density: 7.99 g/cm³, Melting Point: 1371°C |
17-4 PH Stainless Steel | AMS 5643, ASTM A564 | Powder size: 10-45 µm | Density: 7.80 g/cm³, Hardness: HRC 40-47 |
Cobalt-Chrome | ASTM F75, ISO 5832-4 | Powder size: 10-30 µm | Density: 8.30 g/cm³, Melting Point: 1330-1390°C |
Copper (Cu) | ASTM B124, AMS 4501 | Powder size: 15-60 µm | Density: 8.96 g/cm³, Melting Point: 1083°C |
Titanium (Ti-6Al-4V) | ASTM F1472, AMS 4911 | Powder size: 15-45 µm | Density: 4.43 g/cm³, Melting Point: 1600-1660°C |
Aluminum (AlSi10Mg) | ISO 3522 | Powder size: 20-63 µm | Density: 2.68 g/cm³, Melting Point: 577-660°C |
Bronze | ASTM B584, SAE J463 | Powder size: 20-80 µm | Density: 8.7-8.9 g/cm³, Melting Point: 950-1050°C |
Tool Steel (H13) | ASTM A681 | Powder size: 10-50 µm | Density: 7.80 g/cm³, Hardness: HRC 50-52 |
Nickel Alloy 718 | AMS 5662, ASTM B670 | Powder size: 15-53 µm | Density: 8.19 g/cm³, Melting Point: 1260-1336°C |
Suppliers and Pricing Details
When sourcing metal powders for Binder Jetting, it’s essential to consider reliable suppliers and pricing. The table below provides an overview of potential suppliers and approximate pricing for different
metal powders:
Supplier | Material | Pricing (Approx.) | Notes |
---|---|---|---|
GKN Additive | Inconel 625, 316L SS, Ti-6Al-4V | $100 – $300 per kg | High-quality powders, global supplier |
Höganäs AB | 17-4 PH SS, Aluminum, Bronze | $150 – $400 per kg | Leading metal powder producer, custom formulations |
Carpenter Additive | Cobalt-Chrome, Nickel Alloy 718 | $200 – $500 per kg | Premium materials, aerospace and medical focus |
Sandvik Additive Manufacturing | Tool Steel H13, Copper | $120 – $350 per kg | Advanced materials, extensive R&D capabilities |
LPW Technology | Various metal powders | $180 – $450 per kg | High-performance powders, industry-standard |
Arcam AB (GE Additive) | Titanium alloys, Inconel 718 | $250 – $600 per kg | Specialized in aerospace and medical applications |
AP&C (a GE Additive company) | Aluminum, Stainless Steels | $200 – $500 per kg | Expertise in high-quality spherical powders |
EOS GmbH | Various metal powders | $220 – $550 per kg | Known for consistency and quality |
Renishaw plc | Stainless Steels, Titanium | $190 – $480 per kg | Precision engineering and advanced materials |
TANIOBIS GmbH | Cobalt-Chrome, Nickel Alloys | $210 – $550 per kg | Innovative material solutions, focused on R&D |
Advantages and Limitations of Binder Jetting Additive Manufacturing
Like any manufacturing process, Binder Jetting has its pros and cons. Understanding these can help in deciding whether this method is the right fit for your project.
Advantages
Advantage | Description |
---|---|
Material Diversity | Binder Jetting can use various materials, including metals, ceramics, and sand, offering flexibility in applications. |
No Thermal Distortion | The absence of heat in the process means parts are free from warping or residual stresses, leading to higher accuracy. |
High Production Speed | Suitable for producing large batches quickly, Binder Jetting is efficient for both prototyping and production. |
Excellent Surface Finish | The fine powder particles used result in smooth surfaces, reducing the need for post-processing. |
Complex Geometry | Ideal for creating intricate designs and internal features that are difficult with traditional manufacturing methods. |
Limitations
Limitation | Description |
---|---|
Material Porosity | Parts may require infiltration or sintering to achieve full density, which adds additional steps and costs. |
Mechanical Properties | The mechanical strength of Binder Jetted parts may not match those produced by other methods like DMLS or casting. |
Post-Processing Requirements | While the surface finish is good, some applications may still require additional post-processing, such as machining or infiltration. |
Limited Material Selection | Although versatile, not all materials are suitable for Binder Jetting, particularly high-temperature alloys. |
Cost of Metal Powders | The cost of metal powders, especially for high-quality applications, can be significant. |
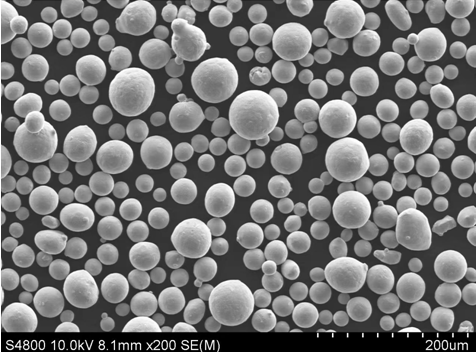
FAQs
To wrap up this comprehensive guide, here’s a FAQ section to address common queries about Binder Jetting.
Question | Answer |
---|---|
What materials can be used in Binder Jetting? | Binder Jetting can use various materials, including metals like stainless steel, Inconel, titanium, ceramics, and sand. |
Is Binder Jetting suitable for mass production? | Yes, Binder Jetting’s high production speed makes it suitable for mass production, especially for complex parts. |
What are the main advantages of Binder Jetting? | Key advantages include material diversity, no thermal distortion, high production speed, and the ability to create complex geometries. |
Are Binder Jetted parts strong enough for industrial use? | While Binder Jetted parts are suitable for many applications, they may require post-processing, such as sintering, to achieve desired mechanical properties. |
How does Binder Jetting compare to other additive manufacturing methods? | Binder Jetting is faster and more cost-effective for certain applications but may fall short in terms of mechanical strength compared to methods like DMLS. |
What post-processing is required for Binder Jetted parts? | Depending on the material, parts may require sintering, infiltration, or machining to improve strength and surface finish. |
Can Binder Jetting be used for medical implants? | Yes, particularly with biocompatible materials like titanium and cobalt-chrome, Binder Jetting is used to create custom medical implants. |
How does Binder Jetting handle complex geometries? | Binder Jetting excels at producing complex geometries, including internal structures and overhangs, without the need for support structures. |
What is the typical cost of metal powders for Binder Jetting? | Metal powders for Binder Jetting can range from $100 to $600 per kilogram, depending on the material and quality. |
Who are the leading suppliers of metal powders for Binder Jetting? | Leading suppliers include GKN Additive, Höganäs AB, Carpenter Additive, Sandvik Additive Manufacturing, and EOS GmbH. |
Conclusion
Binder Jetting Additive Manufacturing represents a versatile and efficient method in the world of 3D printing. With its ability to work with a wide range of materials and produce complex parts with excellent surface finishes, it’s a method that offers significant potential for various industries. However, like any manufacturing process, it has its limitations, particularly concerning material density and mechanical properties. By understanding the full scope of Binder Jetting, from the specific metal powders used to the applications and suppliers involved, you can make informed decisions about its suitability for your projects. Whether you’re in aerospace, automotive, medical, or artistic fields, Binder Jetting opens up a world of possibilities for innovation and production.
For those looking to explore this technology further, connecting with suppliers and diving into specific material properties will be key steps in leveraging Binder Jetting to its fullest potential.