3D printing, also known as additive manufacturing, allows objects to be created from digital files by depositing material layer by layer. There are many different types of 3D printing technologies available today, each with their own advantages and ideal applications. Choosing the right 3D printing technology for a particular project depends on factors like material capabilities, speed, precision, cost, and more.
Fused Deposition Modeling (FDM)
Fused deposition modeling (FDM) is one of the most common and affordable types of 3D printing. It works by heating thermoplastic filament to a semi-liquid state and extruding it through a nozzle onto a build platform layer by layer. Once a layer cools and hardens, the build platform lowers, and the next layer is printed on top. This process continues until the object is complete.
Advantages of FDM 3D printing:
- Low cost of both printers and materials
- Variety of thermoplastic materials available, like PLA, ABS, PETG, nylon, etc.
- Good strength and thermal properties
- Simple operation and maintenance
Ideal applications of FDM:
- Prototyping
- Tools, jigs, and fixtures
- Toys and hobbyist items
- Functional parts and end-use products
FDM 3D printers are excellent for custom plastic parts at low costs, but they are limited in terms of surface finish and precision. The layered nature of the printing process results in a visible stair-stepping effect on sloping surfaces.
FDM Materials
The most common materials used for FDM 3D printing are:
- PLA – Polylactic acid; biodegradable thermoplastic derived from corn starch. Easy to print and produces low-odor models. More brittle than other plastics.
- ABS – Acrylonitrile butadiene styrene; a durable and moderately flexible thermoplastic polymer. Tends to shrink slightly during cooling which can compromise precision. Emits fumes when printed.
- PETG – Glycol-modified polyethylene terephthalate; combines strength and flexibility for durable printed parts. Resistant to many chemicals and low moisture absorption.
- Nylon – A strong, flexible engineering plastic with excellent properties, but more difficult to print successfully. Often used for functional parts that require strength.
- TPU – Thermoplastic polyurethane; a flexible rubber-like filament used for flexible objects, gaskets, hoses, and more. Difficult to print and requires specific printer setups.
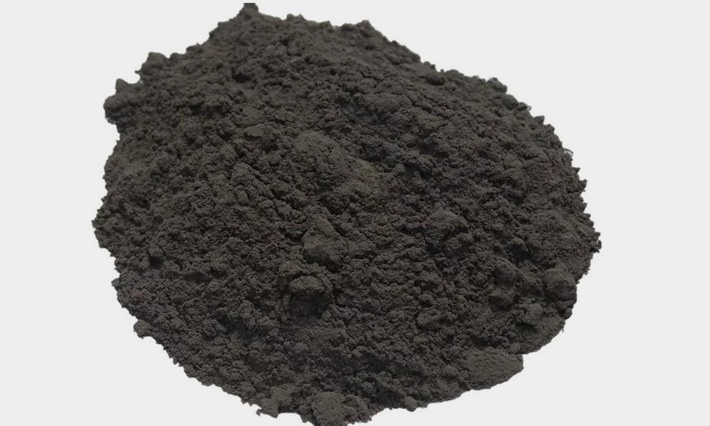
Stereolithography (SLA)
Stereolithography (SLA) 3D printing utilizes ultraviolet (UV) lasers to cure liquid plastic resin layer by layer until an object is formed. An SLA 3D printer contains a vat of photopolymer resin which is selectively cured by a UV laser.
Advantages of SLA printing:
- Very high accuracy and sharp details
- Excellent surface finish quality
- Variety of photopolymer resins available
- Fast printing for small objects
Ideal applications of SLA printing:
- Dental and medical devices
- Jewelry casting patterns
- Highly detailed miniatures
- Precision engineering parts
- Functional prototypes
While SLA 3D printing offers superb part quality, the process can be messy, materials are more expensive, and support structures may be required for some geometries. Post-processing is also required to rinse and cure printed parts.
SLA Materials
Common SLA photopolymer resin materials include:
- Standard Resins – For prototyping and casting masters. Affordable but brittle.
- Tough Resins – Durable plastic-like resins that offer strength and flexibility.
- Dental Resins – Biocompatible resins approved for dental appliances.
- Castable Resins – Designed for sacrificial jewelry casting masters to be lost-wax casted.
- Bio-compatible Resins – For medical devices that interface with the human body.
- Engineering Resins – Heat and chemically resistant materials with advanced mechanical properties.
Material Jetting (MJ)
Material jetting (MJ) 3D printing uses inkjet-style print heads to selectively deposit tiny droplets of UV-curable liquid photopolymers onto a build platform. The liquids quickly solidify and build up layer by layer. Material jetting can create highly detailed and accurate parts with smooth surfaces.
Advantages of MJ printing:
- Very high feature detail resolution
- Excellent surface finish – Smooth and glossy
- Support dissolvable materials available
- Multiple materials can be combined
Ideal applications of MJ printing:
- Detailed medical models
- High fidelity prototypes
- Manufacturing tools like jigs and guides
- Jewelry patterns and casting
Downsides of material jetting include somewhat brittle materials, high equipment costs, and small build volumes on lower-end machines. Material costs are also quite high.
MJ Materials
Material jetting utilizes proprietary photopolymer resins. Some options include:
- Rigid Opaque – For visual models and prototypes
- Rigid Transparent – Clear plastic-like parts
- Rubber-like – Flexible parts with elastic properties
- High Temp – Heat-resistant models and fixtures
- Castable – Resins for jewelry casting patterns
- Bio-compatible – For medical devices and tools
- Ceramic-like – Hard and stiff with a matte finish
Binder Jetting
In binder jetting 3D printing, a liquid bonding agent is selectively deposited to join together powder material layer by layer. The process utilizes two materials – a powder base material and a liquid binder. The binder bonds the powder particles together to form a solid part one thin layer at a time.
Advantages of binder jetting:
- Good material strength and stability
- Porous structures possible
- Large range of material options
- Relatively fast printing
Ideal applications of binder jetting:
- Metal and sand casting
- Full color objects
- Porous functional parts
- Large ceramic parts
The main limitations of binder jetting are rough surface finish and porous material properties. Infiltration is often required to improve strength and finish.
Binder Jetting Materials
Binder jetting can utilize many different base powder materials combined with liquid binders. Material options include:
- Metals – Stainless steel, aluminum, tool steel, Inconel, titanium, precious metals
- Sand – For sand casting molds and cores
- Ceramics – Alumina, zirconia, tricalcium phosphate, glass
- Plastics – Nylon, PBT, TPU, PMMA
- Foundry Sand – For metal casting molds and cores
Directed Energy Deposition (DED)
Directed energy deposition (DED) uses a focused thermal energy source such as a laser, electron beam, or plasma arc to fuse materials by melting them as they are deposited. DED 3D printing allows parts to be fabricated from metal powder or wire.
Advantages of DED printing:
- Good structural integrity of printed metal parts
- Large build volumes possible
- Excellent material properties from printed metals
- Deposition heads can be mounted on multi-axis arms or robotic systems
Ideal applications of DED printing:
- Metal functional parts and end products
- Repairing and adding features to existing metal parts
- Aerospace and aviation components
- Customized metal medical implants
- Automotive parts
Limitations of DED include lower resolution on fine features and slower speeds compared to powder bed fusion techniques. The equipment is also very expensive.
DED Materials
DED is used to print parts from various metals including:
- Stainless Steel – 316L, 17-4, 15-5, etc.
- Aluminum – AlSi10Mg, AlSi7Mg, Scalmalloy, etc.
- Titanium – Ti6Al4V, commercially pure titanium, nickel titanium.
- Tool Steels – H13, D2, M2 High Speed Steel.
- Superalloys – Inconel 625, 718, etc.
- Precious Metals – Gold, silver, platinum.
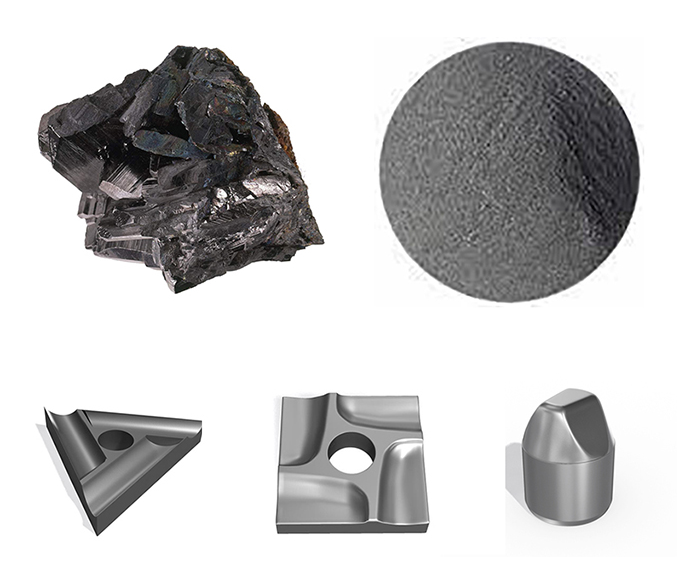
Powder Bed Fusion (PBF)
Powder bed fusion (PBF) 3D printing refers to processes where thermal energy selectively fuses regions of a powder bed layer by layer. The two main PBF technologies are selective laser sintering (SLS) and direct metal laser sintering (DMLS).
Selective Laser Sintering (SLS)
How SLS Printing Works:
- Thermoplastic powder is spread thinly onto a build plate
- A laser scans and sinters powder to fuse it together into a solid part
- The build plate lowers and more powder is spread on top
- Layer by layer sintering continues until the part is finished
Advantages of SLS Printing:
- Good material properties and mechanical strength
- Variety of thermoplastic materials available
- Minimal support structures needed
- Allows complex geometries
Ideal Applications of SLS Printing:
- Functional prototypes
- End-use parts and housings
- Manufacturing tools like jigs and fixtures
- Customized nylon components
Downsides of SLS include porous surfaces, lower resolution on fine features, and smaller build volumes with smaller machines. Material costs can also be high.
SLS Materials
Common SLS thermoplastic materials include:
- Nylon 11 and 12 – Strong, semi-flexible engineering thermoplastics. Most popular SLS plastics.
- TPU 92A – Flexible polyurethane with rubber-like properties.
- PEEK – Heat resistant thermoplastic with excellent mechanical properties.
- Alumide – Nylon composite with aluminum powder, mimics metal.
- CarbonMide – Nylon composite with carbon fibers for strength.
Direct Metal Laser Sintering (DMLS)
How DMLS Printing Works:
- A thin layer of metal powder is spread over a build plate
- A high power laser melts and fuses powder in designated areas
- The plate lowers and more powder is distributed on top
- Layer by layer melting continues until the part is complete
Advantages of DMLS Printing:
- Fully dense metal parts with excellent material properties
- Complex geometries and custom alloys possible
- Minimal support structures required
- Efficient use of expensive metal material
Ideal Applications of DMLS Printing:
- Metal functional prototypes
- Customized medical implants like prosthetics
- Aerospace and automotive components
- Repairing molds by adding metal
- Lightweight custom metal parts like brackets
DMLS is slower for printing larger metal parts and has higher equipment costs than DED processes. Exact alloy compositions can be challenging to verify.
DMLS Materials
DMLS is used to print both common and exotic metal alloys including:
- Stainless Steel – 17-4, 316L, 304L, 15-5, etc.
- Aluminum – AlSi10Mg, AlSi7Mg, Scalmalloy, etc.
- Titanium – Ti6Al4V ELI, Grade 5, Grade 23.
- Tool Steel – H13, P20, D2, M2 High Speed Steel.
- Inconel – Inconel 625, 718.
- Cobalt Chrome – CoCrMo, BioDur CCM Plus, etc.
Continuous Liquid Interface Production (CLIP)
Continuous liquid interface production (CLIP) 3D printing uses an oxygen permeable window below the ultraviolet image projection plane to continuously create models from a pool of UV-curable photopolymer resin.
How CLIP Printing Works:
- UV light shines through an oxygen permeable window into a liquid resin vat
- The build platform lowers to expose cured resin which solidifies above the window
- UV light patterns cure the resin and bottom layers fuse to the platform
- Continuous pulling out of cured resin allows very fast print speeds
Advantages of CLIP Printing:
- Extremely fast printing – up to 100x faster than SLA
- Productive manufacturing technology
- Excellent surface finishes and fine details
- Low operating costs compared to SLA
Ideal Applications of CLIP Printing:
- Mass manufacturing plastic components
- High volume prototyping
- Hearing aid housings
- Dental aligners and appliances
- Plastic enclosures and housings
Limitations include smaller build volumes and fewer material options currently available. But the technology is advancing quickly.
CLIP Materials
Current photopolymer resin materials for CLIP 3D printing include:
- RIGUR® RPS – Rugged and stiff material with heat resistance.
- RIGUR® BPA – Optically transparent material.
- RIGUR® ABA – Multi-purpose plastic material, affordable and easy to print.
Laminated Object Manufacturing (LOM)
Laminated object manufacturing (LOM) works by bonding thin sheets of material together using heat and pressure and then cutting the cross sections of an object layer by layer.
How LOM Printing Works:
- A sheet of paper, plastic, or metal is rolled onto the build platform
- A heated roller laminates the sheet to the prior layer
- A laser or blade cuts the outline of the part cross section
- Excess material is cut away and removed
- Another sheet is added on top and the process repeats
Advantages of LOM Printing:
- Wide range of lamination materials
- Does not require additional support material
- Large objects can be produced
- Relatively low equipment cost
Ideal Applications of LOM Printing:
- Concept models built from layered paper
- Wood objects like furniture and signs
- Cardboard packaging and display components
- Fiber-reinforced composites
Part accuracy and surface finish tend to be lower compared to other 3D printing processes. And the layered material can lead to anisotropic properties.
LOM Materials
Various sheet materials can be used for laminated object manufacturing:
- Paper – Adhesive paper, cardboard, and carton sheets
- Plastics – ABS, polypropylene, polycarbonate
- Metals – Stainless steel, titanium, aluminum
- Composites – Fiberglass, carbon fiber
Multi Jet Fusion (MJF)
Multi jet fusion (MJF) printing utilizes an array of inkjet printheads to selectively deposit fusing and detailing agents onto a powder bed to fully melt and fuse material layer by layer with high precision.
How MJF Printing Works:
- A layer of powder is spread over the build platform
- Printheads deposit fusing and detailing agents
- Infrared lamps melt and fuse powder where fusing agent was deposited
- Unfused powder acts as support until removed later
- Additional layers build up until the part is complete
Advantages of MJF Printing:
- Good accuracy and surface finishes
- Excellent mechanical properties
- Productive printing with fast build speeds
- No support structures needed
Ideal Applications of MJF Printing:
- Functional prototypes with good material properties
- Short-run injection molding production
- Durable and precise end-use parts
- Conformal cooling channels in tooling
Material options are currently limited to a few high-performance thermoplastics from HP. But the technology is advancing rapidly.
MJF Materials
MJF 3D printing utilizes HP’s high performance thermoplastics:
- PA 11 – Nylon engineered for good strength and thermal resist.
- PA 12 – Nylon with superb mechanical properties and ideal for many uses.
- PA 12 GB – Glass bead reinforced nylon 12 for stiffness and dimensional stability.
- PEEK – Exceptional thermoplastic with heat resistance and excellent mechanical properties.
Selective Inhibition Sintering (SIS)
Selective inhibition sintering (SIS) uses a fusing agent to selectively bond powder material layer by layer. An inhibitor is printed to prevent sintering in unwanted areas.
How SIS Printing Works:
- Powder material is spread onto the build platform
- An inkjet deposits an inhibitor to define part contours
- Entire powder bed is evenly exposed to heat or UV light
- Fusing agent causes powder to sinter except where inhibitor prevents it
- Excess powder is vacuumed away after each layer
Advantages of SIS printing:
- Dense metal, plastic or ceramic parts
- No support structures needed
- Unused powder is reusable
- Minimal material waste
Ideal applications of SIS printing:
- Mass customized consumer products
- Customized metal hardware
- Ceramic artware and decor
- Manufacturing assembly jigs
Currently only provided commercially by a few companies such as ExOne, but has potential for greater adoption in the future.
SIS Materials
Several materials can be used for selective inhibition sintering:
- Plastics – Nylon 11 and 12, TPU elastomer.
- Metals – Stainless steel, tool steel, bronze, tungsten carbide.
- Ceramics – Silica sand, alumina, tricalcium phosphate, zirconia.
- Glass – Soda-lime glass, borosilicate glass.
Bottom Line
There are many different 3D printing technologies available, each with unique capabilities. Understanding the key characteristics of each process allows the optimal technology to be selected for a given application based on factorsCopy such as required materials, accuracy, surface finish, build speed, costs, etc. The most common technologies like FDM and SLA are economical choices for concept modeling and prototyping. For short-run production of end-use plastics parts, MJF and SLS offer good mechanical properties with high productivity. Jewelry, medical devices, and advanced engineering components benefit from superb accuracy and surface finish with technologies like material jetting, CLIP, and binder jetting. DED and DMLS open new doors for directly printing functional metal parts for aerospace, automotive, and medical uses. With systems becoming faster, cheaper, and more capable, 3D printing is revolutionizing how products can be designed, customized, and manufactured across almost every industry.
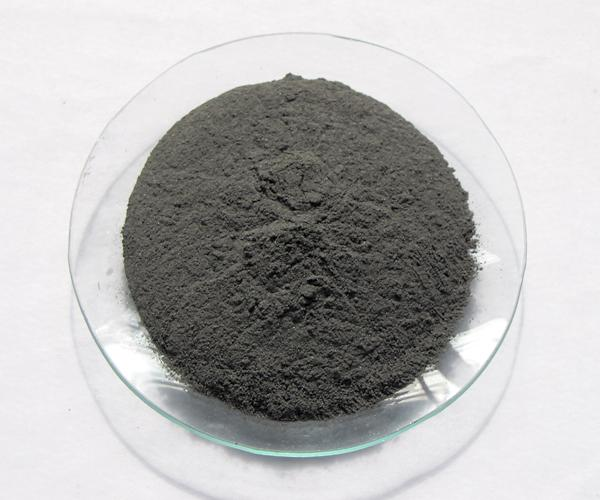
FAQ
What is the most affordable desktop 3D printing technology?
Fused deposition modeling (FDM) is generally the most affordable and accessible desktop 3D printing technology for hobbyists and businesses today. There are many FDM 3D printers available from companies like Creality, Prusa Research, FlashForge, and others that offer good capability at low costs.
What technology provides the best surface finish and detail resolution?
Stereolithography (SLA) and material jetting (MJ) offer the highest quality surface finish, fine feature detail, and overall part accuracy among common 3D printing technologies. However, equipment costs tend to be substantially higher.
Which 3D printing process is best for functional metal parts?
Directed energy deposition (DED) and direct metal laser sintering (DMLS) are two of the leading technologies for 3D printing fully dense and functional metal components. DED builds up parts from welded metal powder or wire, while DMLS selectively melts and fuses metal powder bed layers.
What technology is ideal for mass customized plastic products?
Multi jet fusion (MJF) from HP enables economical short-run production of precision plastic parts with excellent mechanical properties, making it an ideal solution for mass customization and rapid manufacturing. The process is also very fast.
Can ceramic parts be 3D printed?
Yes, several 3D printing technologies support ceramic materials. Binder jetting can print large ceramic objects by bonding together a powder material with a liquid binder. Selective inhibition sintering also allows high density ceramic parts by sintering powder layer-by-layer.
Which 3D printing process is the fastest?
Continuous liquid interface production (CLIP) is the fastest 3D printing technology available today, capable of printing functional plastic parts up to 100x faster than SLA 3D printing. This makes it viable for mass manufacturing applications. Desktop CLIP printers are now available.
know more 3D printing processes
Frequently Asked Questions (Supplemental)
1) How do I choose the right 3D Printing Technology for my application?
- Match requirements to process strengths: complex plastic prototypes (SLA/MJ), durable end-use nylons (SLS/MJF), full‑density metals (DMLS/SLM), large repair/add‑on metal features (DED), fast mass plastic production (CLIP/MJF). Consider material, accuracy, finish, size, speed, certification, and total cost.
2) What are typical tolerances across common technologies?
- With proper calibration: FDM ±0.2–0.5 mm or ±0.5% (whichever is greater); SLA/MJ ±0.1–0.2 mm; SLS/MJF ±0.2–0.3 mm; DMLS/SLM ±0.1–0.2 mm; DED ±0.5–1.0 mm. Geometry, orientation, and post‑processing affect results.
3) Which 3D printing processes support multi‑material or color parts?
- Material Jetting supports multi‑material/color in a single build. Binder Jetting can produce full‑color parts (gypsum/plastic/ceramic systems) and multi‑material via post‑infiltration. Some FDM systems enable dissolvable supports or dual filaments.
4) How do post‑processing steps differ between technologies?
- FDM: support removal, sanding, annealing. SLA/MJ/CLIP: solvent wash, UV cure, support removal, surface finishing. SLS/MJF: depowdering, bead‑blast, dyeing, vapor smoothing. DMLS/SLM: stress‑relief heat treat, support removal, HIP, machining, surface finishing. DED: machining and heat treatment.
5) What are common certification paths for industrial parts?
- Follow ISO/ASTM 529xx standards, process qualification (e.g., ASTM F3302 for metals), machine/material “passports,” and application‑specific approvals (FDA guidance for medical, EASA/FAA MMPDS/AMS specs for aerospace). NDT (CT, dye‑pen, UT) and statistical process control are often required.
2025 Industry Trends and Data
- Green/blue lasers expand aluminum and copper adoption in powder bed fusion; broader material portfolios for conductive parts.
- AI‑assisted in‑situ monitoring becomes standard on metal PBF and high‑end resin systems, reducing scrap and CT reliance.
- End‑use production grows in polymers with MJF/SLS, leveraging automated depowdering and vapor smoothing for injection‑like finishes.
- Hybrid manufacturing rises: DED for repair/cladding plus CNC finishing; LPBF cores joined to wrought skins for certified structures.
- Sustainability focus: Closed‑loop powder handling, gas recirculation, and recycled polymer feedstocks reduce cost and footprint.
KPI (3D Printing Technology, 2025) | 2023 Baseline | 2025 Typical/Target | Relevance | Sources/Notes |
---|---|---|---|---|
Metal PBF chamber O2 (ppm) | ≤1000 | 100–300 | Porosity/oxidation control | Machine OEM guidance |
Metal PBF relative density | 99.3–99.6% | 99.6–99.9% | Mechanical properties | Peer‑reviewed/OEM data |
MJF/SLS polymer throughput | +0–10% YoY | +15–30% YoY | Factory productivity | AMUG/Formnext 2024–2025 |
Surface finish (SLA/MJ, Ra) | 2–6 μm | 1–4 μm | Post‑process reduction | Vendor apps notes |
Powder reuse cycles (metals) | 5–8 | 8–12 | Cost/sustainability | Plant case studies |
AI anomaly detection adoption | Pilot | Common on new systems | QA efficiency | OEM releases |
Green/blue laser availability | Limited | Broadening on Al/Cu | New materials | OEM announcements |
Authoritative resources:
- ISO/ASTM 52900 series (terminology/practice): https://www.iso.org
- ASTM F3302 (metal AM process control): https://www.astm.org
- NIST AM Bench datasets: https://www.nist.gov/ambench
- ASM Handbook, Additive Manufacturing: https://dl.asminternational.org
Latest Research Cases
Case Study 1: AI‑Driven In‑Situ Monitoring Lowers Scrap in DMLS Aerospace Brackets (2025)
- Background: An aerospace supplier needed to reduce internal porosity and rework on Ti‑6Al‑4V brackets.
- Solution: Deployed coaxial melt‑pool imaging and layer‑wise cameras with real‑time AI anomaly scoring tied to parameter guardrails; tightened powder passport (O2 ≤0.08 wt%, PSD 15–45 μm).
- Results: Porosity median fell from 0.35% to 0.12%; CT rejects −40%; yield +9%; mechanical Cpk (YS/UTS) improved to ≥1.5 across three consecutive lots.
Case Study 2: Production‑Scale MJF with Automated Post‑Processing for Consumer Housings (2024)
- Background: A consumer electronics OEM sought injection‑like finishes without tooling for short‑run SKUs.
- Solution: Implemented MJF PA12 with automated depowdering and vapor smoothing; introduced color dyeing and dimensional SPC.
- Results: Cosmetic acceptance rate 98.7%; cycle time −25%; unit cost −14% at 5k–10k batch sizes; tensile properties retained within ±3% after smoothing.
Expert Opinions
- Dr. Brent Stucker, Additive Manufacturing Standards Leader
- Viewpoint: “Process control per ASTM and ISO/ASTM 529xx, combined with digital material/machine passports, is the cornerstone for scaling end‑use AM production.”
- Prof. Ian Gibson, Co‑author of Additive Manufacturing Technologies; Professor, University of Texas at Arlington
- Viewpoint: “Technology selection must balance geometry, material, and downstream finishing—MJF/SLS now rival traditional plastics for many end‑use parts.”
- Dr. Martina Zimmermann, Head of Additive Materials, Fraunhofer IWM
- Viewpoint: “Green/blue lasers materially expand powder‑bed fusion capability for reflective metals, but gas flow dynamics and spatter control remain decisive.”
Affiliation links:
- ASTM AM CoE: https://amcoe.org
- University of Texas at Arlington: https://www.uta.edu
- Fraunhofer IWM: https://www.iwm.fraunhofer.de
Practical Tools/Resources
- Standards: ISO/ASTM 52900/52901/52904/52907; ASTM F3302 for metal AM process control
- Databases: NIST AM Bench (https://www.nist.gov/ambench); Senvol Database (https://senvol.com/database)
- Design tools: nTopology (lattices/DFAM), Autodesk Fusion and Siemens NX (DFAM workflows)
- Simulation: Ansys Additive, Simufact Additive (distortion/scan optimization)
- QA/Monitoring: Layer‑wise imaging and melt‑pool analytics from EOS, SLM Solutions, Renishaw, Nikon SLM; CT scanning for critical parts
- Post‑processing: AMT PostPro vapor smoothing, DyeMansion depowdering/dyeing for SLS/MJF
Last updated: 2025-08-22
Changelog: Added 5 supplemental FAQs; introduced 2025 trends with KPI table and references; provided two case studies on DMLS QA and MJF production; included expert viewpoints with affiliations; compiled practical standards, databases, design, simulation, and QA resources for 3D Printing Technology.
Next review date & triggers: 2026-02-01 or earlier if ISO/ASTM standards are revised, major OEMs release new AI in‑situ acceptance criteria, or green/blue laser PBF capabilities expand to additional alloys and platforms.