Imagine a material that’s as strong as steel yet surprisingly light, like a featherweight champion with a knockout punch. That’s the magic of titanium-based alloy powders. These tiny, metallic marvels are revolutionizing manufacturing, creating components that are lighter, stronger, and more durable than ever before. But what exactly are these powders, and how do they work their wonders? Buckle up, because we’re about to embark on a deep dive into the fascinating world of titanium-based alloy powders.
What are Titanium-Based Alloy Powders?
At their core, titanium-based alloy powders are finely-ground particles of titanium, a metallic element known for its exceptional strength-to-weight ratio and excellent corrosion resistance. But pure titanium isn’t the whole story. By blending titanium with other elements like aluminum, vanadium, and iron, manufacturers create alloys that boast even more impressive properties. These alloying elements are like spices in a chef’s dish, each adding a unique flavor – in this case, specific characteristics – to the final product.
The resulting titanium-based alloy powders are like microscopic building blocks. Using techniques like 3D printing and additive manufacturing, these powders are fused together layer by layer to create complex, three-dimensional objects. Think of it like building a sandcastle, but with super-powered sand that can withstand incredible forces.
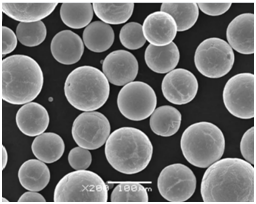
Understanding the Different Types of Titanium-Based Alloy Powders
Not all titanium-based alloy powders are created equal. Each type boasts a unique blend of elements, resulting in a distinct set of properties. Here’s a closer look at some of the most common titanium-based alloy powders:
Alloy Powder | Composition | Key Characteristics |
---|---|---|
Commercially Pure Titanium (CP Ti) | Primarily Titanium (Ti) with minimal amounts of other elements | Excellent corrosion resistance, good ductility (ability to be shaped), biocompatible (compatible with living tissue) |
Ti-6Al-4V (Grade 5) | 90% Titanium (Ti), 6% Aluminum (Al), 4% Vanadium (V) | High strength-to-weight ratio, good weldability (ability to be joined), excellent corrosion resistance |
Ti-6Al-4V (Grade 23) | Similar to Grade 5, but with higher oxygen content | Improved strength at elevated temperatures |
Ti-6Al-4V-ELI (Extra Low Interstitials) | Similar to Grade 5, but with lower oxygen, nitrogen, and carbon content | Improved fracture toughness (resistance to crack propagation) |
Ti-5Al-2.5Fe | 90% Titanium (Ti), 5% Aluminum (Al), 2.5% Iron (Fe) | Lower cost compared to Ti-6Al-4V, good strength and toughness |
Ti-10V-2Fe-3Al | 84% Titanium (Ti), 10% Vanadium (V), 2% Iron (Fe), 3% Aluminum (Al) | High strength and creep resistance (ability to withstand deformation under stress at high temperatures) |
Beta Titanium Alloys (e.g., Ti-17Cu) | Higher percentage of beta-stabilizing elements like copper (Cu) | Excellent high-temperature strength, good formability (ability to be shaped) |
Near Beta Titanium Alloys (e.g., Ti-5Al-5Mo-5V-3Fe) | A balance of alpha and beta stabilizing elements | Offers a combination of high strength, good ductility, and weldability |
This table provides a glimpse into the diverse world of titanium-based alloy powders. As you can see, each type offers a unique set of properties tailored for specific applications.
Application Areas of Titanium-Based Alloy Powder
The potential applications of titanium-based alloy powders are as vast as they are exciting. Here are some key areas where these powders are making a significant impact:
- Aerospace: The incredible strength-to-weight ratio of titanium-based alloy powders makes them ideal for aircraft components like landing gear, airframes, and engine parts. Lighter planes translate to greater fuel efficiency and increased payload capacity.
- Biomedical: The biocompatible nature of certain titanium-based alloy powders, particularly CP Ti, makes them perfect for medical implants like artificial joints, bone screws, and dental implants. These implants offer excellent longevity and compatibility with the human body.
- Automotive: The automotive industry is embracing titanium-based alloy powders for components like connecting rods, suspension parts, and exhaust systems. These lighter components contribute to improved fuel economy and performance.
- Consumer Products: From high-end sporting goods like golf clubs and bicycle frames to designer watches and jewelry, titanium-based alloy powders are finding their way into an expanding range of consumer products. Their unique combination of strength, lightness, and aesthetics makes them a highly desirable material.
- Chemical Processing: Due to their exceptional corrosion resistance, titanium-based alloy powders are well-suited for components used in harsh chemical environments. They can withstand exposure to aggressive chemicals without degrading, making them a reliable choice for the chemical processing industry.
- Defense: The military is leveraging the strength and ballistic protection offered by titanium-based alloy powders to create lighter, more agile armored vehicles and defense components. This allows for increased troop mobility and protection on the battlefield.
These are just a few examples of the many ways titanium-based alloy powders are revolutionizing various industries. As advancements in 3D printing and additive manufacturing technologies continue, we can expect to see even more innovative applications emerge in the future.

Preparation Methods of Titanium-Based Alloy Powders
The creation of titanium-based alloy powders is a fascinating process that involves several key steps:
- Raw Material Selection: The journey begins with the selection of high-quality titanium feedstock, typically in the form of sponge or ingots. These raw materials are carefully chosen to meet specific purity and composition requirements.
- Melting and Alloying: The chosen raw materials are melted in a controlled atmosphere, such as a vacuum or inert gas environment. During this stage, other elements are added to create the desired alloy composition. Precise control over temperature and melting parameters ensures a homogeneous and consistent alloy.
- Atomization: Once molten, the alloy is rapidly atomized. This process involves breaking down the molten metal into tiny droplets, which solidify into spherical powder particles. Different atomization techniques exist, such as gas atomization and plasma atomization, each offering unique advantages in terms of powder size, morphology (shape), and distribution.
- Sieving and Classification: The resulting powder is then sieved and classified to achieve the desired particle size distribution. This ensures consistency and optimal flow properties for use in 3D printing and additive manufacturing processes.
- Quality Control: Throughout the entire production process, rigorous quality control measures are implemented. These measures ensure that the final powder meets strict chemical composition, size distribution, and flowability specifications.
By following these meticulous steps, manufacturers can produce high-quality titanium-based alloy powders that are ready to be transformed into groundbreaking components.
Properties and Characteristics of Titanium-Based Alloy Powders
The properties and characteristics of titanium-based alloy powders are what make them such a valuable material for various applications. Here’s a closer look at some of the key attributes:
- High Strength-to-Weight Ratio: As mentioned earlier, this is the hallmark characteristic of titanium-based alloy powders. They offer exceptional strength while maintaining a low weight, making them ideal for applications where weight reduction is crucial. Compared to traditional materials like steel, titanium-based alloy powders can significantly reduce weight without compromising on strength.
- Corrosion Resistance: Titanium boasts excellent resistance to corrosion, a property that is inherited by many titanium-based alloy powders. This makes them perfect for components that will be exposed to harsh environments, such as seawater or chemicals.
- Biocompatibility: Certain types of titanium-based alloy powders, particularly CP Ti, exhibit excellent biocompatibility. This means they are well-tolerated by the human body and can be used for medical implants without causing adverse reactions.
- High Melting Point: Titanium has a very high melting point, a characteristic that translates to its alloyed powder forms. This makes them suitable for applications that involve high temperatures, such as jet engine components or parts exposed to friction.
- Powder Flowability: For successful 3D printing and additive manufacturing processes, good powder flowability is essential. Titanium-based alloy powders are meticulously engineered to ensure they flow freely and consistently, enabling the creation of complex and intricate geometries.
These properties, combined with the ability to tailor them through alloying, make titanium-based alloy powders a highly versatile material with a vast range of potential applications.
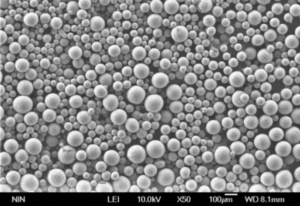
Specifications, Sizes, Grades, and Standards
When selecting titanium-based alloy powders for a specific application, several factors need to be considered. Here’s a breakdown of some key specifications to keep in mind:
- Chemical Composition: Different applications require specific alloy compositions to achieve the desired properties. Manufacturers provide detailed information about the chemical composition of their powders, allowing users to choose the best fit for their needs.
- Powder Size: The size of the powder particles plays a critical role in the 3D printing process. Different printing technologies have specific size requirements. For instance, finer powders are better suited for laser-based additive manufacturing techniques, while larger powders might be appropriate for processes like electron beam melting.
- Powder Morphology: The shape of the powder particles, also known as morphology, can influence the flowability, packing density, and mechanical properties of the final printed component. Spherical powders are generally preferred due to their superior flow characteristics and ability to create dense structures.
- Grades: Many titanium-based alloy powders are available in different grades, each with slight variations in composition and processing parameters. These variations can affect the final properties of the printed component. For example, Ti-6Al-4V Grade 23 offers improved high-temperature strength compared to Grade 5 due to its higher oxygen content.
Standards: To ensure consistency and quality, the production of titanium-based alloy powders adheres to various industry standards. Some of the most prominent standards include:
- ASTM International (ASTM): ASTM publishes a range of standards related to metal powders, including specifications for chemical composition, particle size distribution, and flowability.
- Aerospace Material Specifications (AMS): Developed for the aerospace industry, AMS standards define requirements for metallic materials used in aircraft components. Several AMS specifications cover titanium-based alloy powders for aerospace applications.
- Military Standards (MIL): The military also has established standards for metallic materials, including titanium-based alloy powders, used in defense applications.
By considering these specifications, sizes, grades, and standards, users can select the most appropriate titanium-based alloy powder for their specific needs and ensure successful application in 3D printing and additive manufacturing processes.
Advantages and Limitations of Titanium-Based Alloy Powders
While titanium-based alloy powders offer a multitude of advantages, it’s important to acknowledge their limitations as well. Here’s a balanced perspective:
Advantages:
- Exceptional Strength-to-Weight Ratio: This defining characteristic allows for significant weight reduction in components, leading to improved fuel efficiency in aerospace and automotive applications.
- Superior Corrosion Resistance: Titanium’s natural resistance to corrosion extends to many of its alloyed powder forms, making them ideal for use in harsh environments.
- Biocompatibility: Specific titanium-based alloy powders are biocompatible, enabling their use in medical implants that seamlessly integrate with the human body.
- Design Flexibility: 3D printing allows for the creation of complex geometries with titanium-based alloy powders, opening doors for innovative designs and functionalities.
- Reduced Waste: Compared to traditional manufacturing techniques, additive manufacturing with titanium-based alloy powders can minimize material waste.
Limitations:
- Cost: The production of titanium-based alloy powders can be a complex and energy-intensive process, leading to higher costs compared to some traditional materials.
- Safety Considerations: Titanium powder is classified as a combustible dust, and proper handling procedures are necessary to mitigate fire and explosion hazards.
- Limited Availability: While the availability of titanium-based alloy powders is increasing, some specific alloys or very fine powder sizes might be less readily available compared to more common materials.
- Surface Roughness: Components printed with titanium-based alloy powders can exhibit a slightly rougher surface finish compared to those produced with traditional methods. Post-processing techniques might be required to achieve a smoother surface.
Despite these limitations, the advantages of titanium-based alloy powders are undeniable. As production costs decrease and technology advancements continue, these limitations are likely to become less significant over time.
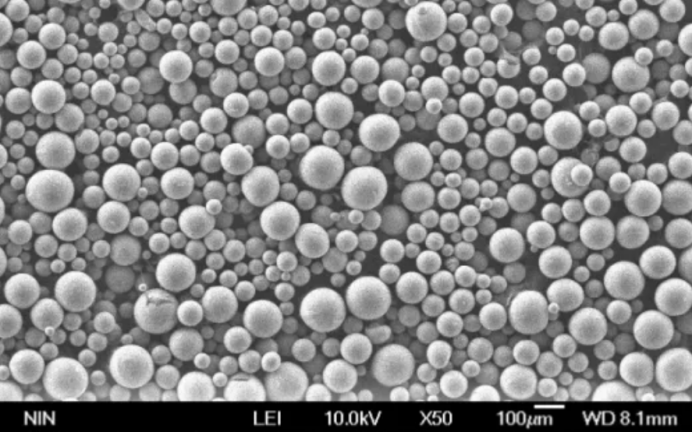
Suppliers and Pricing of Titanium-Based Alloy Powders
The growing demand for titanium-based alloy powders has led to an increase in the number of suppliers offering these materials. Here are some key factors to consider when choosing a supplier:
- Product Portfolio: Ensure the supplier offers the specific type and grade of titanium-based alloy powder required for your application.
- Quality Certifications: Verify that the supplier adheres to relevant industry standards like ASTM or AMS to guarantee consistent quality.
- Experience and Reputation: Choose a supplier with a proven track record in producing high-quality titanium-based alloy powders.
- Pricing and Lead Times: Compare pricing models and lead times from different suppliers to find the best fit for your budgetary and project timelines.
Here’s a table listing some prominent suppliers of titanium-based alloy powders, but this is not an exhaustive list:
Supplier | Location | Website |
---|---|---|
APEX Additive Technologies | United States | https://www.apex.tech/ |
Carpenter Additive | United States | https://www.carpenteradditive.com/ |
Element Materials Technology | United Kingdom | https://www.element.com/ |
EVONIK | Germany | https://corporate.evonik.com/en |
Höganäs | Sweden | https://www.hoganas.com/en/ |
LPW Technology | United Kingdom | https://www.carpenteradditive.com/news-events/lpw-technology-am-metal-powder-manufacturing |
Materialise | Belgium | https://www.materialise.com/en |
Oerlikon Metco | Switzerland | https://www.oerlikon.com/metco/en/ |
Poeton | China | https://www.poeton.co.uk/ |
Praxair Surface Technologies | United States | https://www.linde-amt.com/en |
SLM Solutions | Germany | https://nikon-slm-solutions.com/ |
Pricing: Due to the varying factors like specific alloy composition, powder size, and order quantity, the pricing of titanium-based alloy powders can fluctuate. However, a general range can be helpful for budgeting purposes. Typically, titanium-based alloy powders can range from $100 to $400 per kilogram, with some specialized powders reaching even higher costs. It’s always recommended to contact potential suppliers directly to obtain the most accurate pricing information for your specific needs.
FAQ
In this FAQ section, we’ll address some commonly asked questions regarding titanium-based alloy powders:
Q: Are titanium-based alloy powders safe to handle?
A: Titanium powder is classified as a combustible dust, and proper handling procedures are essential. This includes using appropriate personal protective equipment (PPE) like respirators and eye protection to avoid inhalation or contact with skin and eyes. Additionally, proper ventilation and dust collection systems are necessary to minimize the risk of fire and explosion hazards.
Q: What are the different 3D printing techniques used with titanium-based alloy powders?
A: Several 3D printing techniques are compatible with titanium-based alloy powders. Some of the most popular methods include:
- Laser Beam Melting (LBM): This technique uses a high-powered laser beam to selectively melt and fuse titanium-based alloy powder particles layer by layer, creating a three-dimensional object.
- Electron Beam Melting (EBM): Similar to LBM, EBM employs an electron beam to melt the powder particles. However, EBM takes place in a vacuum environment, allowing for processing of reactive materials like titanium.
- Binder Jetting: This method uses a liquid binder to inkjet individual layers of titanium-based alloy powder particles. The part is then heat-treated to consolidate the powder particles.
Q: What are the future prospects for titanium-based alloy powders?
A: The future of titanium-based alloy powders is incredibly promising. As 3D printing and additive manufacturing technologies continue to evolve, we can expect to see these powders utilized in an even wider range of applications. Advancements in powder production techniques will likely lead to reduced costs and broader availability, further accelerating their adoption across various industries. From creating lighter and stronger components for aerospace and automotive applications to developing innovative medical implants and customized consumer products, the potential of titanium-based alloy powders seems limitless.