Tin alloys powder refers to powder metallurgy forms of tin combined with other metal elements to produce alloys with enhanced properties. Tin is a soft, silvery-white metal that is very light and easy to melt, making it suitable for alloying applications. When processed into a fine powder and compacted into parts, tin alloys can offer advantages like precise dimensional control, uniform composition, and the ability to create more complex component geometries.
Overview of Tin Alloys Powder
Tin alloy powders provide unique advantages for manufacturing industry components and products where specific material properties are needed. Key details include:
- Available as pre-alloyed powders with uniform composition or blended elemental mixes
- Range of alloying elements like copper, antimony, silver, bismuth, zinc, lead
- Particle sizes from under 10 microns to over 150 microns
- Spherical, irregular or mixed particle morphologies
- Loose powder or consolidated preforms for sintering
- Produced by atomization, electrolysis, carbonyl process
- Properties optimized by adjusting composition, powder characteristics
- Sintered into net shape parts through cold/hot compaction and heating
- Provides dimensional precision, stability, material purity, and cost savings
Table 1. Types and Compositions of Common Tin Alloy Powders
Alloy Type | Typical Composition |
---|---|
Tin-Copper | 90Sn/10Cu, 80Sn/20Cu |
Tin-Antimony | 95Sn/5Sb, 90Sn/10Sb |
Tin-Silver | 96.5Sn/3.5Ag |
Tin-Bismuth | 58Sn/42Bi (eutectic) |
Tin-Zinc | 90Sn/10Zn |
Tin-Lead | 60Sn/40Pb (eutectic) |
Table 2. Properties and Characteristics of Tin Alloy Powders
Property | Description |
---|---|
Particle shape | Spherical, irregular or mixed |
Particle size distribution | Typically 10-150 microns |
Tap density | Varies by composition (2-5 g/cc) |
Flow rate | Usually good due to spherical shape |
Compressibility | Moderate based on alloy ductility |
Sintering response | Excellent, achieves 90-95% of wrought density |
Mechanical properties | Modulus, strength, ductility defined by composition |
Thermal properties | Melting point reduced from pure tin (232°C) per alloy content |
Electrical properties | Alloying adjusts conductivity from pure tin |
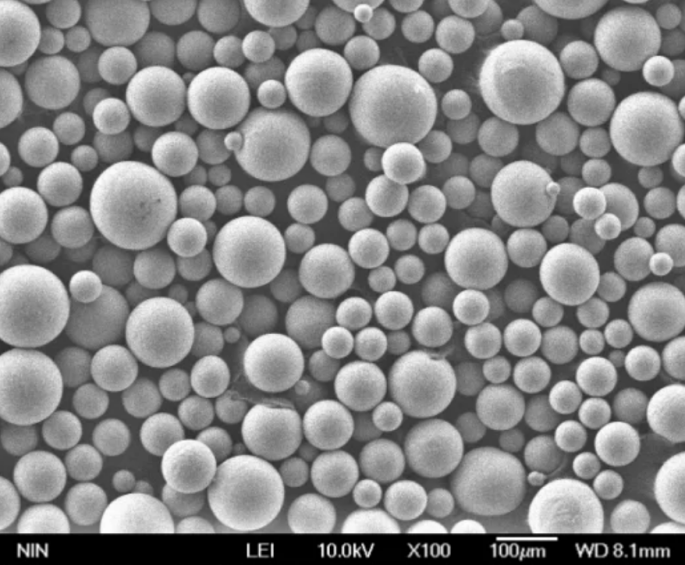
Table 3. Applications and Uses of Tin Alloy Powder Parts
Industry | Applications |
---|---|
Automotive | Bushings, washers, wipers, connectors |
Electronics | Shielding, contacts, terminals, solders |
Industrial | Bearings, gears, seals, fasteners, spacers |
Consumer | Cutlery, zippers, packaging, cosmetics |
Table 4. Specifications and Grades of Tin Alloy Powders
Standard Grade | Composition |
---|---|
Cu90/10 | 90% tin, 10% copper |
Cu80/20 | 80% tin, 20% copper |
Sb5 | 95% tin, 5% antimony |
Sb10 | 90% tin, 10% antimony |
Ag3.5 | 96.5% tin, 3.5% silver |
Zn90/10 | 90% tin, 10% zinc |
Table 5. Suppliers and Pricing
Supplier | Prices |
---|---|
Belmont Metals | $15-25/lb |
Metal Powder Company | $10-35/lb |
SCM Metal Products | $12-30/lb |
Advanced Chemicals | $18-40/lb |
Pricing varies based on alloy composition, particle characteristics, order volume and purity requirements.
Table 6. Comparison of Tin Alloy Powders
Parameter | Loose Powder | Hot Compacted Preform |
---|---|---|
Cost | Lower | Higher |
Lead time | Shorter | Longer |
Customization | Less flexible | More customizable |
Processing | Requires sintering stage | Directly sinterable |
Properties | Variable across parts | Consistent in preform |
Applications | Simple part geometries | Complex shapes, premium uses |
Advantages of Tin Alloy Powder Parts:
- Dimensional precision and stability
- Composition uniformity across large volumes
- Complex geometries achievable
- Near net-shape to minimize machining
- Simultaneous sintering of assemblies
- Enhanced mechanical properties
- High production rate and lower cost
- Powder metallurgy purity in difficult compositions
Limitations of Tin Alloy Powder Parts:
- Higher cost for pre-alloyed powder
- Multi-stage manufacturing process
- Maximum part size restricted by presses
- Lower ductility versus cast alloys
- Larger minimum order quantities
- Limited supplier base for specialty alloys
Composition Options for Tin Alloy Powder
There are a wide range of metals alloyed with tin to enhance specific properties like strength, hardness machinability, melting point, or corrosion resistance when compared to pure tin powder.
Alloying with Copper
Copper is one of the most common alloying elements for tin powder up to 20% addition. Benefits include:
- Increases strength and hardness significantly
- Improves thermal properties
- Enhances corrosion resistance
- Bronze-like gold color for decorative applications
- Brass family alloys mimic wrought material properties
Best balance of strength, ductility, and cost at 10% copper addition as the Cu90/10 grade.
Alloying with Antimony
Antimony additions up to 10% are used to:
- Improve mechanical properties
- Increase hardness for wear resistance
- Maintain strength in higher temperature service
- Provide support for part geometry without distortion
Antimony also acts as a grain refining agent to generate smoother finishes.
Alloying with Silver
A 3-3.5% silver content gives excellent benefits:
- Dramatic increase to elongation and impact energy
- Substantial improvement to fatigue strength
- Enhanced machinability and tool life
- Suppresses tin pest issues in the material
The balance of high ductility and strength makes Ag3.5 commonly used.
Alloying with Bismuth
Bismuth is alloyed with tin across a wide range up to 55% to give:
- Elemental substitution for more toxic lead alloys
- Self-lubricating properties
- Low melting points
- Dimensional stability
- Metal joining applications as fusible alloys
- Low melting solder capability
42% bismuth is eutectic grade for the lowest melting point.
Alloying with Zinc
Zinc at addition levels around 5-10% provides the advantages of:
- Increased hardness and tensile strength
- Improved bearing properties
- Better corrosion resistance
- Brighter white coloration for decorative parts
- Lower cost than other alloying elements
Zinc also controls grain size for more consistent mechanical properties.
Alloying with Lead
Though its toxicity is being reduced, lead is still used to alloy with tin mainly for:
- Improved machinability and self-lubrication
- Lower melting temperatures
- Vibration damping properties
- High density applications like ballasts and weights
40% lead is the eutectic composition for minimal melting point alloys.
Comparison of Production Processes
There are several commercial methods used to manufacture tin alloy powder with different composition flexibility, powder quality and cost considerations.
Table 7. Production Process Comparison
Method | Description | Typical Products |
---|---|---|
Atomization | Molten stream impinged by water or gas | Pre-alloyed spherical powders |
Electrolysis | Electrochemical refinement from ore | Copper-rich powders, irregular |
Carbonyl | Thermal decomposition of carbonyls | Nickel, iron alloys, small lots |
Atomization is the most common process allowing high volume production of consistently spherical alloy powders preferred for pressing and sintering. This flexible method can produce pre-alloyed compositions tailored to application requirements.
Electrolysis is used primarily for copper-containing alloys where raw ore sources are refined into powder form. It has lower costs but less control over powder shape and size distribution.
Carbonyl process decomposes metal compounds into ultrafine, highly pure powders. This method allows unique alloys in smaller batch sizes. Costs are higher with more controlled atmospheres needed.
Applications and Markets
The combination of cost savings, design flexibility, and property enhancements make tin alloy powder products popular across diverse commercial and consumer markets:
Automotive Powder metal bushings, washers, springs and other engine/transmission components allow cost-effective, high production components to achieve lightweighting and performance criteria.
Electrical Contacts Connectors, relays, terminals, and other conductive components utilize tailored tin alloys and copper additions to balance conductivity, hardness and corrosion resistance needed.
Industrial Components Tin-bronze bearings offer oil-free self-lubrication. Silver-tin alloys enhance durability in fasteners, gears and bushings needing to resist wear, galling and high temperature conditions.
Joining Alloys Low melting fusible alloys composed of tin-bismuth or tin-lead enable rapid production of solder joints and mold release applications at relatively low cost.
Consumer Products Cost savings combined with ability to produce complex shapes makes tin alloy powder ideal for cutlery, hand tools, zipper elements, cosmetic cases, electronics housings, and beverage capsules.
Part Design Guidelines
To best leverage the benefits of powdered tin alloys, engineered components should apply these part design guidelines:
- Use near net-shape designs with minimal machining needed
- Maintain uniform wall thicknesses where possible
- Include draft angles for ease of die filling
- Eliminate unnecessary decorative features
- Restrict tolerance requirements to capabilities
- Design interlocking assemblies for sinter bonding
- Consider secondary operations like coining, staking
Following powder metallurgy design principles allows complex, high performance shapes to be produced cost effectively.
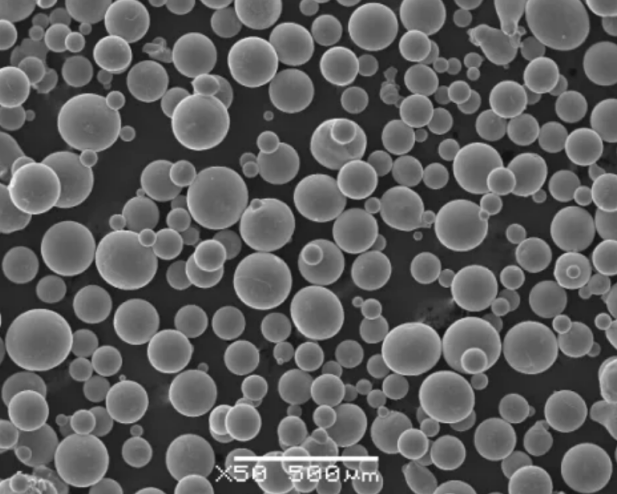
Future Outlook
Ongoing trends influencing tin alloy powder demand:
Automotive Lightweighting Replacing cast zinc and aluminum components with higher strength powdered tin alloys allows additional vehicle weight reduction and fuel efficiency gains.
High Temperature Electronics Development of thermally stable electrical contacts based on copper-tin and nickel-tin is enabling technologies like electric vehicles, avionics and launch systems.
Environmental Regulations Tin alloy compositions are shifting away from toxic lead additions in favor of bismuth and zinc for equivalent functionality.
3D Printing Binder jetting and other additive techniques can leverage lower cost tin alloy powders for novel geometries and rapid part iteration.
Global Supply Chain Expanded availability of sustainable tin ore supplies coupled with localized alloy powder production is accelerating adoption.
FAQs
What are the most common tin alloy powder compositions?
The tin alloys produced in the highest volumes are copper at 10%, antimony at 5%, silver at 3.5%, and zinc at 10%. These balance cost while enhancing specific properties.
What particle size range is typical for pressing applications?
A particle size range between 45 microns to 105 microns provides optimal packing density, surface finish and flow characteristics during die compaction.
What causes dimensional changes during tin alloy powder sintering?
Shrinkage of 10-20% is often observed because of material densification and removal of lubricants. Alloying additions and processing can help control the effects.
Why is powder production of some tin alloys preferred over wrought or casting methods?
Certain compositions like Cu-Sn are immiscible under normal ingot solidification. Powder production allows these alloys to be created uniformly.
How are powder tin parts consolidated prior to sintering?
Cold compaction using presses up to 2000 tons form green preforms close to final dimensions. Binders, lubricants and time enhance densification during pressing.
What post-production operations are commonly used on powder tin alloys?
Infiltration is used to increase density. Coining goes beyond 90% density. Machining, drilling and tapping provide final fabricated precision. Plating improves corrosion or wear resistance.
What effects does alloy composition have on the sintering process?
Higher alloy content lowers the liquidous temperature, increasing liquid phase sintering. More diffusible metals like copper enhance solid state sintering kinetics and densification.
Which tin alloy powder compositions offer the best combination of strength and ductility?
Small additions of copper at 10% coupled with 3% silver creates the best balance of tensile strength above 45 ksi and elongations of 18-25% in powder tin alloys.