Introduction
In recent years, materials science has witnessed remarkable advancements, leading to the discovery and development of innovative substances that have revolutionized various industries. One such remarkable material is Ti6Al4V powder. This article delves into the world of Ti6Al4V powder, exploring its properties, applications, manufacturing process, quality control, safety considerations, and future prospects.
What is Ti6Al4V Powder?
Ti6Al4V powder, also known as Ti-6Al-4V, is an alloy composed of titanium, aluminum, and vanadium. It is renowned for its exceptional strength, low density, and corrosion resistance. The unique combination of these elements makes it a valuable material in numerous applications, from aerospace to medical fields.
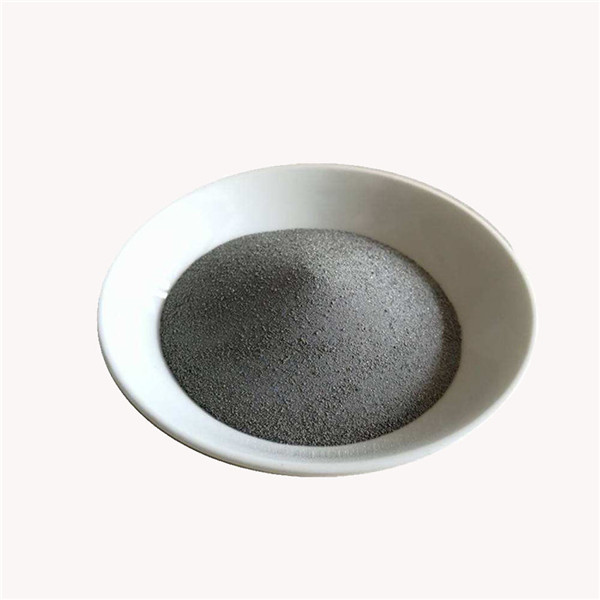
Properties of Ti6Al4V Powder
High Strength-to-Weight Ratio
One of the standout features of Ti6Al4V powder is its extraordinary strength-to-weight ratio. It exhibits excellent mechanical properties, making it suitable for applications where weight reduction is crucial without compromising on strength.
Corrosion Resistance
Ti6Al4V powder showcases impressive corrosion resistance, particularly in harsh environments, such as marine settings or chemical processing industries. This property ensures the longevity and reliability of components made from this alloy.
Biocompatibility
In the medical field, biocompatibility is of utmost importance, and Ti6Al4V powder excels in this aspect. It is commonly used for producing medical implants due to its biocompatibility and ability to integrate with the human body.
Heat Resistance
The alloy’s ability to withstand high temperatures without losing its structural integrity makes it ideal for applications in the aerospace and automotive sectors, where components are subjected to extreme heat.
Weldability
Ti6Al4V powder is easily weldable, allowing for efficient manufacturing and assembly processes. This weldability ensures that complex structures can be fabricated with ease.
Applications of Ti6Al4V Powder
Aerospace Industry
The aerospace sector extensively utilizes Ti6Al4V powder in the production of aircraft components, such as engine parts, landing gears, and structural components. Its lightweight nature and high strength make it a preferred choice for enhancing fuel efficiency and overall performance.
Medical Implants
Medical implants, ranging from orthopedic implants to dental fixtures, benefit from the biocompatibility and corrosion resistance of Ti6Al4V powder. It ensures longevity and reduces the risk of complications in patients.
Automotive Components
In the automotive industry, Ti6Al4V powder finds applications in various components, including exhaust systems, suspension parts, and engine valves. Its ability to withstand high temperatures and corrosive environments makes it invaluable.
Marine Equipment
Due to its exceptional corrosion resistance, Ti6Al4V powder is widely used in marine equipment, such as propellers, underwater structures, and desalination units, ensuring durability in saltwater environments.
Sporting Goods
The sports industry leverages the advantages of Ti6Al4V powder for manufacturing lightweight yet durable sporting goods, such as bicycle frames, golf club heads, and tennis rackets.
Manufacturing Process of Ti6Al4V Powder
Gas Atomization
Gas atomization is a common method for producing Ti6Al4V powder. It involves injecting molten alloy into a high-pressure gas stream, where it solidifies into small spherical particles.
Plasma Atomization
Plasma atomization utilizes a plasma arc to melt and atomize the alloy into powder particles. This method offers better control over particle size and is suitable for high-performance applications.
Mechanical Alloying
Mechanical alloying involves mechanical grinding of elemental powders, resulting in a homogeneous alloy powder with improved properties.
Spark Plasma Sintering
Spark Plasma Sintering is a consolidation technique used to form solid materials from powder particles. It allows for the creation of complex shapes with enhanced density and properties.
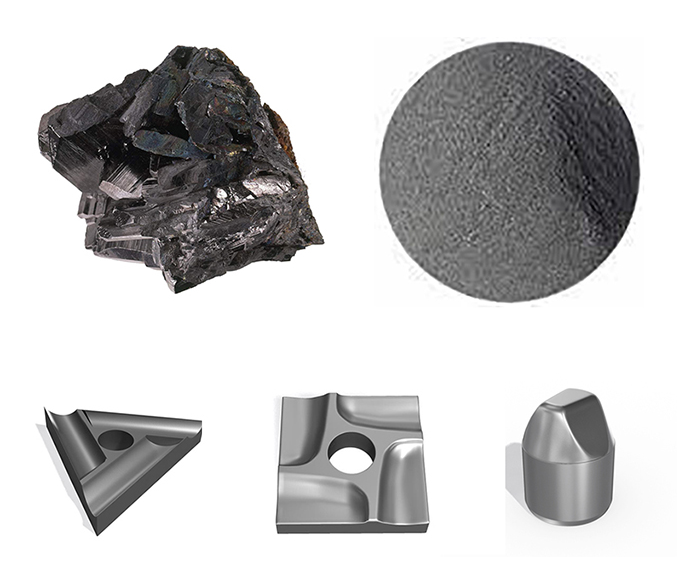
Advancements in Ti6Al4V Powder Production
Additive Manufacturing
Additive manufacturing, or 3D printing, has opened new horizons for Ti6Al4V powder utilization. This process allows for the creation of intricate designs and customized components.
High-Energy Ball Milling
High-energy ball milling is a mechanical processing method that enhances the properties of Ti6Al4V powder by inducing structural changes at the nanoscale.
Alloying Elements
Researchers continue to explore the addition of various elements to Ti6Al4V powder to create new alloy compositions with improved properties, expanding its potential applications.
Quality Control and Testing
Particle Size Analysis
Accurate particle size analysis is crucial for maintaining consistent quality in Ti6Al4V powder. Advanced techniques such as laser diffraction are employed for precise measurements.
Chemical Composition Analysis
Ensuring the correct chemical composition is vital to meet industry standards. X-ray fluorescence and other spectroscopic methods verify the alloy’s elemental composition.
Mechanical Testing
Mechanical testing evaluates Ti6Al4V powder’s mechanical properties, including tensile strength, hardness, ductility, and fatigue resistance. These tests help verify that the powder meets specific performance requirements for its intended applications.
Handling and Safety Precautions
Fire and Explosion Hazards
As with handling any fine powder, Ti6Al4V powder poses a fire and explosion hazard if proper safety measures are not followed. It is essential to store and handle the powder in designated areas with appropriate ventilation and equipment.
Health Risks
Inhalation or skin contact with Ti6Al4V powder can lead to health risks, including respiratory issues and skin sensitization. Workers handling the powder should wear appropriate personal protective equipment (PPE) to minimize exposure.
Future Trends and Prospects
Advancements in 3D Printing
The continuous development of additive manufacturing techniques is expected to drive further adoption of Ti6Al4V powder in various industries. As 3D printing technology improves, it will enable the production of complex components with enhanced efficiency and reduced material waste.
Biomedical Applications
Ti6Al4V powder’s biocompatibility makes it an ideal candidate for more advanced and personalized medical implants. As research in tissue engineering and regenerative medicine progresses, the demand for tailor-made implants is likely to grow.
Improved Alloy Compositions
Ongoing research into the addition of alloying elements to Ti6Al4V powder is expected to lead to the development of new and improved compositions with specialized properties. These innovations will further expand the material’s application scope.
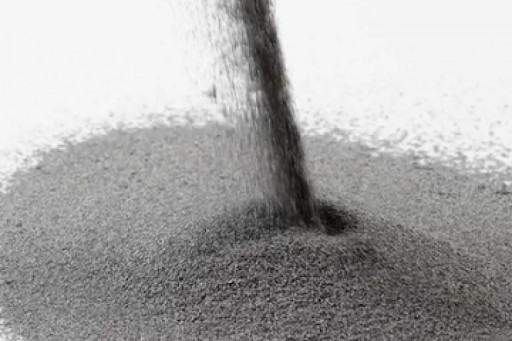
Conclusion
Ti6Al4V powder has emerged as a revolutionary material with exceptional properties and diverse applications. Its high strength-to-weight ratio, corrosion resistance, biocompatibility, and heat resistance have made it a preferred choice in industries ranging from aerospace to medicine. The ongoing advancements in its production methods, including additive manufacturing, ensure a promising future for Ti6Al4V powder, opening up possibilities for new and innovative applications.
FAQs (Frequently Asked Questions)
1. What is Ti6Al4V powder?
Ti6Al4V powder is an alloy composed of titanium, aluminum, and vanadium, known for its high strength, low density, and corrosion resistance.
2. What are the main applications of Ti6Al4V powder?
Ti6Al4V powder finds applications in aerospace, medical implants, automotive components, marine equipment, and sporting goods.
3. How is Ti6Al4V powder produced?
Ti6Al4V powder is produced through methods such as gas atomization, plasma atomization, mechanical alloying, and spark plasma sintering.
4. Is Ti6Al4V powder biocompatible?
Yes, Ti6Al4V powder is biocompatible, making it suitable for medical implants and biomedical applications.
5. What are the safety precautions when handling Ti6Al4V powder?
When handling Ti6Al4V powder, precautions should be taken to prevent fire and explosion hazards, and workers should use appropriate personal protective equipment to minimize health risks.