Atomized metals refer to metal powders that have been reduced to microscopic particles through atomization. This process involves turning bulk liquid metal into a spray of tiny droplets, which solidify into fine spherical powders. Atomized metals play an important role across various industries due to their unique properties and capabilities.
Applications of Atomized Metals
Atomized metal powders provide several key advantages over conventional metal forms:
- High surface area – Their small size and spherical shape gives atomized powders a very high surface area to volume ratio, allowing superior contact and interaction.
- Easy to compact – The powders can be pressed into a wide range of shapes with high green density, allowing efficient manufacturing.
- Improved performance – Parts made from atomized powders often demonstrate better mechanical properties.
- Custom alloys – Precise control over chemistry is possible by atomizing custom alloys.
These characteristics make atomized metals suitable for manufacturing parts via powder metallurgy, thermal spraying, metal injection molding, and additive manufacturing. Some of the major applications include:
Powder Metallurgy
Powder metallurgy utilizes compressed and sintered metal powder to produce precision net-shape components. The fine particles allows for excellent flow and compaction when pressed into a die. Parts can be made to tight dimensional tolerances without machining, minimizing material waste. Common powder metallurgy parts include automotive transmission gears, connecting rods, and self-lubricating bearings.
Thermal Spraying
In thermal spraying, atomized powders are fed through a heated gun to produce a molten or semi-molten spray deposit on a surface. This allows the fast application of thick, protective metal coatings onto parts. Thermal spraying with atomized metals is used to coat engine cylinders, hydraulic shafts, bridges, and other industrial components needing wear/corrosion resistance or insulation.
Metal Injection Molding
Metal injection molding (MIM) combines powder metallurgy and plastic injection molding to manufacture small, complex parts. Atomized powders are mixed with a polymer binder, injection molded, then sintered. MIM can produce intricate net-shape components like gears or medical implants at high volumes with minimal finishing.
Additive Manufacturing
Selective laser sintering, direct metal laser sintering, and binder jetting rely on atomized metal powders to 3D print parts layer-by-layer. Light, porous structures with complex geometries can be built additively. Atomized metals are ideal for producing one-off prototypes, custom dental crowns, aerospace components, and biomedical implants via additive manufacturing.
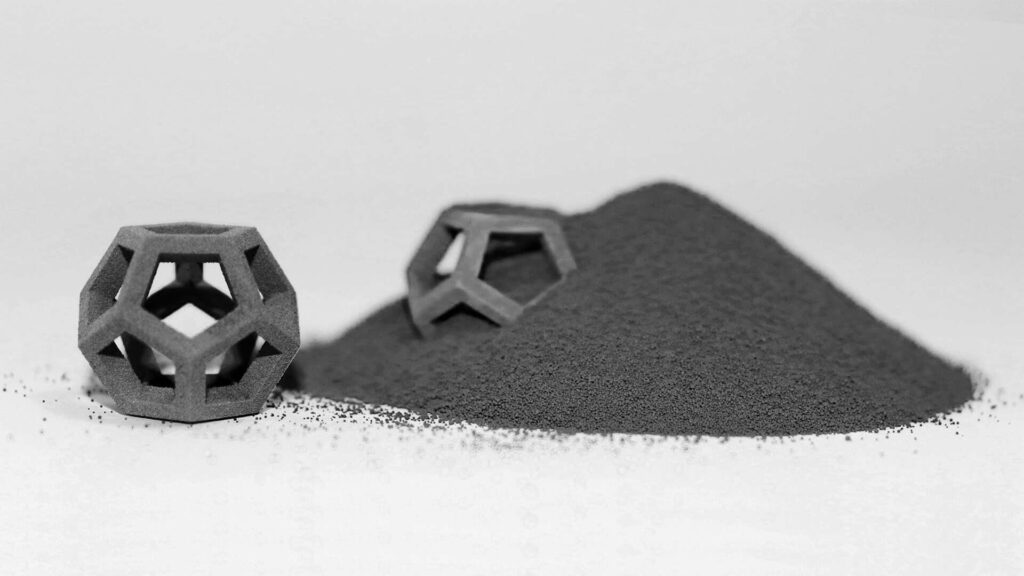
Methods of Producing Atomized Metal Powders
There are several techniques used to produce atomized metal powders on an industrial scale:
Gas Atomization
Gas atomization is the most common method. The metal is melted and poured into a tundish with a ceramic nozzle at the bottom. High pressure inert gas (usually nitrogen or argon) is injected at the nozzle, breaking up the molten stream into a spray of fine droplets. The droplets solidify rapidly into spherical powders as they fall and cool. Different gas pressures and nozzle designs yield powders from 10 – 150 microns in size.
Water Atomization
In water atomization, the molten metal stream is disintegrated by high pressure water jets. The water quenches the droplets rapidly, resulting in irregularly shaped powders. Water atomization can produce a higher yield of finer particles under 10 microns compared to gas atomization. However, powders may be contaminated with oxygen from the water.
Centrifugal Atomization
Here, molten metal is fed to a spinning disc or multiple spinning cups. Centrifugal force throws off ligaments of liquid metal that break into droplets and solidify into powders. This method allows higher production rates than gas atomization but yields less spherical particles.
Ultrasonic Gas Atomization
Applying ultrasonic vibrations to the molten metal stream in a gas atomizer results in a finer droplet spray and smaller particle size distribution. The sound waves enhance disintegration and dispersion of the metal. However, scale up to industrial production is difficult.
Electrode Induction Gas Atomization
An electric current is passed directly through the molten metal stream via an inductive coil right before gas atomization. This induction heating boils and agitates the metal, creating more uniformly sized and spherical powders. It allows control of particle size and morphology.
The proper atomization technique is chosen based on alloy, desired powder characteristics, purity requirements, and production volume.
Properties of Atomized Metal Powders
Atomization produces powders with unique composition and physical attributes that determine their performance. Key characteristics include:
- Particle size – Generally 10 – 150 μm. Smaller sizes have higher surface area. Larger sizes pack better and deform less during compaction.
- Particle shape – Gas atomization creates highly spherical particles ideal for powder pressing. Water atomized particles are more irregular.
- Particle size distribution – Narrower distributions allow maximum powder density during packing with few voids.
- Composition – Chemistry and microstructure is controllable. Rapid cooling often creates non-equilibrium meta-stable phases.
- Purity – Inert gas atomization prevents oxidation. Trace oxygen or nitrogen can embrittle particles.
- Flowability – Spherical morphology gives excellent flow behavior. Critical for even filling of die cavities during compaction.
- Apparent density – Higher densities improve pressing characteristics and sintering behavior. Ranges from 40-65% theoretical density.
- Tap density – After mechanical tapping/agitation, powders can achieve >65% theoretical density. Indicates compressibility.
- Hausner ratio – Lower ratios (~1.25) show ease of powder flow during processing. High ratios (~1.4) suggest cohesion and poor flow.
These powder qualities are tailored to meet the requirements of the specific application through careful control of the atomization process.
Benefits of Using Atomized Metal Powders
Atomized metals provide several important advantages over other starting materials in manufacturing:
- Produce highly durable and consistent parts efficiently
- Generate less scrap vs metal machining processes
- Enable small, complex component geometries
- Provide alloy compositions not easily produced by ingot metallurgy
- Offer flexibility through additive manufacturing methods
- Allow ultrafine microstructures for enhanced properties
- Result in more uniform microstructures throughout a part
- Give outstanding surface finish, density, tolerance, and repeatability
- Permit near-net-shape fabrication, minimizing machining
- Provide novel non-equilibrium metallic phases
The unique characteristics of atomized metals make them ideal feedstock for critical applications in automotive, aerospace, electronics, medical, and defense industries. Their precision and performance often cannot be achieved via conventional metal processing routes.
Advancements in Atomized Metal Production
Recent developments in atomization technology are expanding capabilities and uses of metal powders:
- Microwave plasma torches can superheat metal above its boiling point, creating ultrafine nanoparticles under 100 nm during atomization.
- Controlled atomization and cooling allows production of amorphous metal powders with superior properties.
- Multi-nozzle gas atomization generates novel particle shapes like hollow spheres or flakes.
- Dynamic gas flow adjustment modifies particle size distribution and morphology on-the-fly.
- Ultra-high velocity acceleration atomization makes nanocrystalline composite powders.
- Integrated atomization-sintering systems are lowering costs and improving quality.
- Smooth particle coating in-flight via vapor deposition is enabling better powder flow and packing.
- Advanced modeling of droplet formation and solidification is optimizing the atomization process.
- Specialized nozzles allow atomization of highly reactive alloys like aluminum and magnesium with minimal oxidation.
Continuing research and progress in atomized metal powder production will unlock further applications and capabilities.
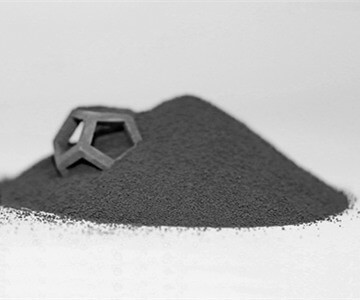
Major Producers of Atomized Metal Powders
Most atomized powders are produced by a small number of major metal powder suppliers:
- Hoeganaes Corporation – Part of the GKN Group, largest metal powder maker, wide range of atomized powders.
- Sandvik Osprey – Leading powders for additive manufacturing, specialty in nickel superalloys.
- Praxair Surface Technologies – Important supplier to thermal spray industry, offers custom alloys.
- Hoganas – Major ferrous powders for PM parts, specialist in diffusion-alloyed steels.
- Rio Tinto Metal Powders – Significant producer of titanium and specialty alloy powders.
- AMETEK Specialty Metal Products – High volume steel and copper atomized powders.
- CNPC Powder Group – Major producer of aluminum and alloy powders.
- Mitsui Mining & Smelting – Japanese supplier of copper, iron, and tin powders.
- Bühler Group – Global leader in die casting and atomizing equipment.
- Makin Metal Powders (UK) Ltd – Major manufacturer of Al, Cr, Ni superalloy powders.
Most of these companies can tailor particle size, shape, and chemistry to meet specific needs.
Challenges With Atomized Metal Powders
While possessing clear advantages, atomized metals also come with some inherent challenges:
- High production costs – Require expensive raw materials, capital equipment, and high purity inert gases.
- Limited sizes available – Gas atomization works best for powders 25-150 μm. Other methods required for ultrafine or coarse particles.
- Oxygen pickup – Atomization and handling can introduce trace oxygen contamination, especially in reactive alloys.
- Lower tap densities – Irregular powder shapes decrease maximum density after compaction.
- Dust hazards – Fine powders pose explosion and inhalation risks requiring special handling.
- Raw material purity – Impurities and inclusions can carry over from liquid metal, affecting final properties.
- Agglomeration – Particle satellites and agglomerates lower powder flowability.
- Porosity in compacts – Densest packing still contains microscopic pores that can trap contamination.
- Residual stress – Rapid cooling and shrinkage during solidification causes stresses in particles.
- Oxidation of compacts – Sintering must be done under vacuum or inert atmosphere to prevent oxidation.
- Dimensional change – Shrinkage of 10-20% during solid-state sintering can lead to warpage and distortion.
While these difficulties can be managed with proper powder production, handling, and part processing methods, they remain an impediment in certain powder metallurgy applications.
Future Outlook for Atomized Metal Powders
The unique properties of atomized metal powders make them well-suited for fabricating high performance components across virtually all industries. With continued research and process refinement, atomized metals will play an expanding role in enabling lighter, stronger and more complex metal parts.
Key trends that will shape the future of atomized metal powders:
- Growing adoption in 3D printing as costs decrease.
- Tighter particle size control and particle modification to improve powder performance.
- Development of novel high strength alloys exclusively through powder metallurgy.
- Expanded use in biomedical components like implants and prosthetics.
- Continuous alloy development for customized microstructures and properties.
- Automation and on-site atomization to cut costs for metal AM users.
- Nanoparticle atomization for extremely fine-grained and enhanced properties.
- Increased focus on recycling metal powders.
- Multi-metal printing and composites broadening usable alloys.
- Special surface coatings to enhance powder properties and sintering.
- High purity systems minimizing gaseous contamination.
Atomized metal powders will enable stronger, lighter, higher performance, and more complex metal components. Ongoing metallurgical and processing developments will open new opportunities across manufacturing industries.
FAQ
What are the most commonly atomized metals?
The most commonly atomized metals are:
- Iron and steel alloys like stainless steel
- Copper and copper alloys such as brass
- Aluminum alloys including aluminum-silicon
- Nickel-based superalloys and cobalt alloys
- Titanium and titanium alloys
What is the typical size range of atomized powders?
Gas atomized powders range from around 10 microns to 150 microns diameter. Water atomized powders can reach as small as 3 microns. Special processes can generate nanoparticle powders under 1 micron.
What industries use atomized metal powders?
Key industries utilizing atomized metal powders include aerospace, automotive, electronics, biomedical, defense, and additive manufacturing. The powders allow light, strong, complex metal parts.
What are the main benefits of gas atomized powders?
Gas atomized powders have a spherical morphology that provides good flow and compression during die compaction. They also have low oxygen contamination.
How are metal powders handled safely?
Metal powders are explosion hazards so precautions are taken during handling. Workers wear respirators to avoid inhalation. Powders are kept covered and sealed to prevent dust accumulation.
Why are inert gases like nitrogen used to atomize metals?
Inert gases prevent reaction between the molten metal and air to avoid oxidation. Nitrogen is used most commonly due to lower cost than argon.
What are metal injection molding and metal binder jet 3D printing?
Both processes involve first forming “green” parts from metal powder mixed with an organic binder. The binder is then removed and the powders are sintered into a final, dense metal part.
How are metal powders recycled?
Unused metal powders can be blended with new powders or directly re-atomized. Parts and 3D printed components are often shredded and re-atomized into powder feedstock.