Alloy iron powder refers to iron powder with alloying elements like nickel, molybdenum, copper, and chromium added to enhance properties like strength, corrosion resistance, and workability. This advanced material enables innovative applications across automotive components, additive manufacturing, welding, surface coating, friction materials, and more.
This comprehensive guide will cover everything related to alloy iron powder from manufacturing methods, composition, properties, applications, suppliers, costs, and selection criteria.
Overview of Alloy Iron Powder
Alloy iron powder is produced by atomizing molten iron alloys into fine spherical powders. The base metal is iron, with alloying elements like nickel, molybdenum, copper, and chromium added in controlled amounts. The composition and powder characteristics determine the performance and applications.
Here is an overview table of alloy iron powder:
Type | Production Method | Alloying Elements | Properties | Applications |
---|---|---|---|---|
Nickel iron powder | Water atomization | Nickel up to 50% | High green and sintered strength, permeability, corrosion resistance | Soft magnetic components, additive manufacturing |
Molybdenum iron powder | Gas atomization | Molybdenum up to 4% | Enhanced mechanical strength, high temperature properties | Automotive parts, welding |
Copper iron powder | Water atomization | Copper up to 10% | High electrical conductivity, thermal conductivity | Electrical contacts, friction materials |
Chromium iron powder | Gas atomization | Chromium up to 5% | Oxidation and corrosion resistance | Surface coating, brazing |
Nickel, molybdenum, copper, and chromium are common alloying elements, along with smaller amounts of manganese, silicon, boron, and carbon. Each addition serves a specific purpose in enhancing powder properties.
Now let’s look at the manufacturing process, characteristics, applications, and selection of alloy iron powders in detail.
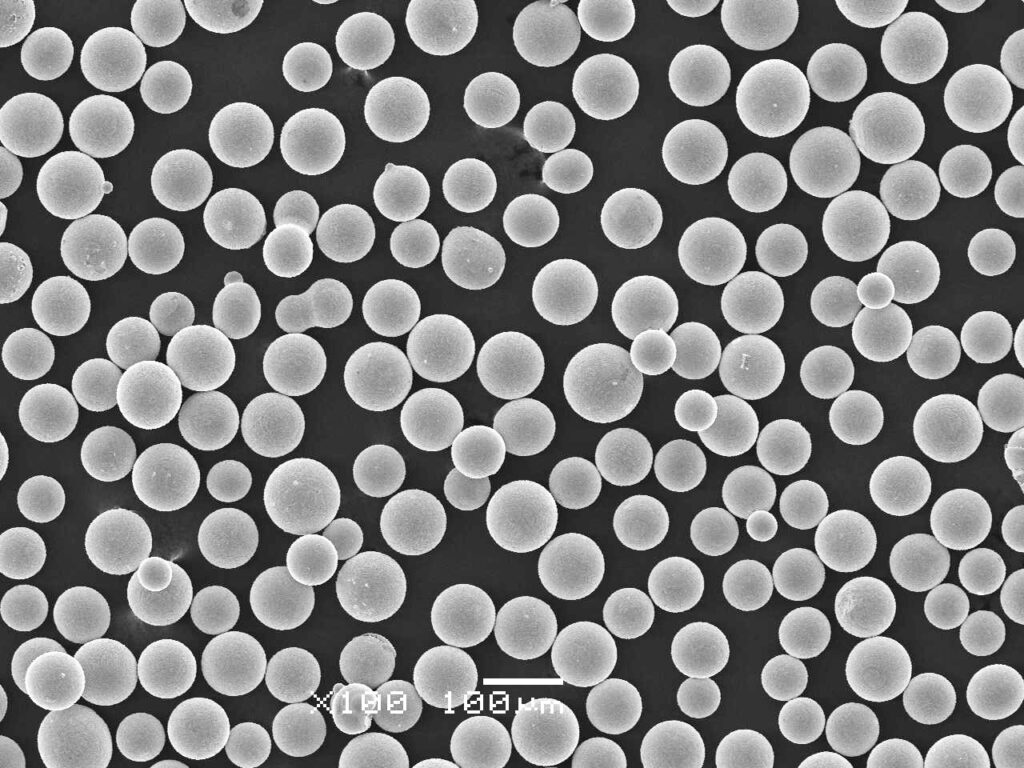
Manufacturing Methods for Alloy Iron Powder
Alloy iron powder is manufactured by atomizing melted iron alloys into fine spherical powders. The two main methods are:
Water Atomization
In water atomization, the molten alloy metal stream is disintegrated by high pressure water jets into fine droplets, which solidify into powders. It allows higher production rates and finer powders compared to gas atomization. The powder particles have irregular shapes. Nickel iron and copper iron powders are commonly produced by this method.
Gas Atomization
In gas atomization, an inert gas like nitrogen or argon disintegrates the molten metal into powders. It allows better control over powder characteristics. The particles are highly spherical with smooth surfaces. Molybdenum iron and chromium iron powders are mostly produced via gas atomization.
Secondary steps like annealing, crushing, screening, and coating may be used to obtain the desired powder sizes and improve flowability. The manufacturing process influences the final powder properties significantly.
Composition of Alloy Iron Powders
The key aspects of alloy iron powder composition are:
Alloying Element | Composition Range |
---|---|
Nickel | Up to 50% |
Molybdenum | Up to 4% |
Copper | Up to 10% |
Chromium | Up to 5% |
Manganese | Up to 1.5% |
Silicon | Up to 6% |
Nickel, molybdenum, copper, and chromium are the major alloying elements in iron powder. Smaller amounts of manganese, silicon, carbon, boron, and graphite may be added to enhance properties.
The composition is optimized based on the desired powder characteristics and end-use application requirements. Precise control over the alloying additions is necessary to achieve consistent powder quality.
Properties of Alloy Iron Powders
Alloying elements enhance the properties of iron powder significantly compared to pure iron powders. Here are some of the notable properties imparted by different alloying elements:
Alloying Element | Effect on Properties |
---|---|
Nickel | Increases green and sintered strength, permeability, corrosion resistance |
Molybdenum | Improves mechanical strength, high temperature properties |
Copper | Enhances electrical and thermal conductivity |
Chromium | Provides oxidation and corrosion resistance |
Manganese | Increases strength and hardenability |
Silicon | Improves fluidity and lubricity |
The alloying strategy targets the exact property requirements of the application, such as strength, conductivity, or corrosion resistance.
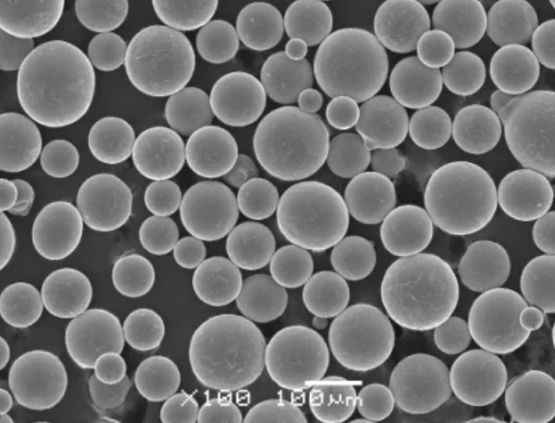
Applications of Alloy Iron Powder
The unique properties of alloy iron powders make them suitable for various critical applications across industries:
Type of Powder | Applications |
---|---|
Nickel iron | Soft magnetic components, additive manufacturing, welding |
Molybdenum iron | Automotive parts, welding, surface coating |
Copper iron | Electrical contacts, friction materials, brazing |
Chromium iron | Corrosion resistant coatings, brazing filler |
Some major application areas of alloy iron powder include:
Automotive Parts
Alloy iron powders are used to manufacture high-performance automotive components like connecting rods, camshafts, gears, bearing caps and more via powder metallurgy route. The excellent mechanical properties allow reliability under demanding conditions.
Additive Manufacturing
Nickel iron powders enable printing of complex 3D components for prototyping and production using binder jetting and fused deposition modeling technologies. This allows faster design iterations.
Soft Magnetic Components
Nickel iron powders are used to produce soft magnetic parts like choke coils, filters, transducers, transformers etc. via compaction and sintering. The high permeability and low core losses are beneficial.
Friction Materials
The excellent friction and wear characteristics of copper iron and chromium iron powders make them ideal for manufacturing brake pads, clutch disks and other friction components.
Welding
Molybdenum iron and nickel iron powders enhance the metallurgical and mechanical properties of the weld deposit across various welding processes. The high strength and temperature resistance provide durability.
Surface Coating
Chromium iron and molybdenum iron spray powders are used to deposit thick and corrosion resistant coatings on metal substrates via thermal spraying processes.
The specialized powder characteristics like permeability, conductivity, strength, and corrosion resistance make alloy iron powders suitable for such critical applications across industries.
Suppliers of Alloy Iron Powder
There are a number of global suppliers that manufacture various alloy iron powder grades. Here are some of the leading suppliers:
Company | Powder Types |
---|---|
Höganäs | Nickel iron, molybdenum iron |
Rio Tinto | Nickel iron, chromium iron |
JFE Steel | Nickel iron, molybdenum iron |
AMETEK | Molybdenum iron, copper iron |
CNPC | Nickel iron, copper iron |
Sandvik | Chromium iron, nickel iron |
These companies have expertise in manufacturing various alloy iron powder compositions optimized for different applications using water atomization, gas atomization, and secondary treatment processes.
They offer a wide range of powder sizes, morphological characteristics, and alloying additions to choose from. In addition to standard grades, customized alloy iron powders can also be developed in collaboration with the powder producer to meet specific requirements.
Cost Analysis of Alloy Iron Powders
The price of alloy iron powders depends on various factors:
Factor | Impact on Cost |
---|---|
Alloy composition | Higher alloying content increases cost |
Powder size and morphology | Finer sizes and spherical shape are costlier |
Production method | Gas atomized powder is more expensive than water atomized |
Order quantity | Higher volumes lower cost per kg |
Customization | Special grades made to order cost more |
Here is an approximate price range for different alloy iron powder types:
Powder Type | Price Range* |
---|---|
Nickel iron | $ 5 – 15 per kg |
Molybdenum iron | $ 12 – 30 per kg |
Copper iron | $ 8 – 20 per kg |
Chromium iron | $ 15 – 40 per kg |
The powder composition, particle characteristics, and order parameters significantly influence the final price. Get current price quotations from multiple manufacturers when purchasing.
How to Select Alloy Iron Powder
Here are some tips on selecting the appropriate alloy iron powder:
Step | Details |
---|---|
1. Identify application requirements | Consider properties needed – strength, corrosion resistance, permeability etc. |
2. Choose alloying elements | Select alloying elements like Ni, Mo, Cu, Cr to achieve properties |
3. Determine powder characteristics | Consider particle size, morphology, density, impurities etc. |
4. Select manufacturing process | Water or gas atomization process based on powder specs |
5. Shortlist suppliers | Evaluate experienced powder producers who can customize |
6. Get samples for testing | Test powder samples to verify if properties meet requirements |
Collaborate closely with powder metallurgy experts and suppliers to select the optimum alloy iron powder composition, characteristics, and manufacturing process to meet the application needs.
Alloy Iron Powder vs. Stainless Steel Powder
Alloy iron and stainless steel powders have some distinct differences:
Parameter | Alloy Iron Powder | Stainless Steel Powder |
---|---|---|
Base metal | Iron | Iron, chromium, nickel |
Alloying elements | Ni, Mo, Cu, Cr (up to 50%) | Cr, Ni, Mo, Nb, Ti |
Corrosion resistance | Moderate from chromium | Excellent from higher chromium |
Magnetic properties | Can be soft magnetic | Non-magnetic |
Cost | Lower | Higher due to alloying additions |
Applications | Automotive, welding, brazing | Medical, aerospace, marine |
The key differences are the alloying strategy, magnetic properties, corrosion resistance, cost, and applications. Alloy iron powders offer a cost-effective alternative to stainless steel in less demanding environments.
Advantages of Alloy Iron Powder
Some major benefits of using alloy iron powder are:
- High strength – Alloying enhances green and sintered strength significantly compared to pure iron. This allows design optimization.
- Controlled properties – Alloy composition can be varied to achieve the desired properties like conductivity, permeability, strength etc. as per application needs.
- Better workability – Elements like graphite improve powder compressibility and compactibility for easier part shaping.
- Heat resistance – Additions like molybdenum improve high temperature strength and creep resistance.
- Corrosion resistance – Alloying with chromium imparts considerable corrosion and oxidation resistance.
- Cost-effectiveness – Alloy iron powders offer high performance at lower cost than exotic alloys.
The ability to tailor powder properties, performance, and cost makes alloy iron an attractive material for critical components across industries.
Limitations of Alloy Iron Powder
Some limitations of alloy iron powder include:
- Alloying increases powder cost significantly compared to pure iron powder.
- Heavily alloyed grades may have lower compressibility requiring higher compaction pressures.
- Composition control requires consistent quality standards in powder manufacturing.
- Complex heat treatment may be needed to achieve required properties after compaction.
- Dimensional changes during sintering require close control over processing parameters.
- Certain applications require higher purity, corrosion resistance, or permeability only achieved with more advanced alloys.
- Restricted application temperature range compared to high performance superalloys.
- Lower electrical resistivity than pure iron limits use in some electromagnetic applications.
- Strong magnetic properties of certain alloying elements may not be desirable.
- Achieving homogenous distribution of fine alloying elements can be challenging.
- Lower ductility than wrought alloys restricts use in extensive forming applications.
- Porosity in sintered parts lowers fatigue strength compared to wrought alloys.
While alloy iron offers several benefits, the limitations must be considered during component design and manufacturing to ensure reliable performance. Proper powder characterization, process control, and design margins can overcome these challenges in most applications.
Future Outlook for Alloy Iron Powder
The future looks bright for alloy iron powder, driven by rising adoption in additive manufacturing and automotive sector. Here are some emerging trends:
- Development of new high strength and corrosion resistant iron alloys for aerospace and biomedical use.
- Novel hybrid alloy compositions using micro and nanoscale alloying elements to derive superior properties.
- Growing use of alloy iron powders in metal binder jetting for digital manufacturing of end-use automotive and industrial components.
- Increasing preferences for pre-alloyed powders over admixed elemental powders for reliable alloying.
- Adoption of atomization processes like plasma rotation electrode process (PREP) to achieve finer, spherical powders.
- Production of customized alloy iron powders tailored to requirements of advanced sintering processes like micro-wave sintering.
- Stringent quality control and characterization to meet specifications required by high-performance applications.
- Collaboration between end-users, powder producers, and equipment makers to co-develop new high-value powder alloys and applications.
The strategic advantages of alloy iron powder are likely to drive greater innovation and expanded use across sectors in the future.
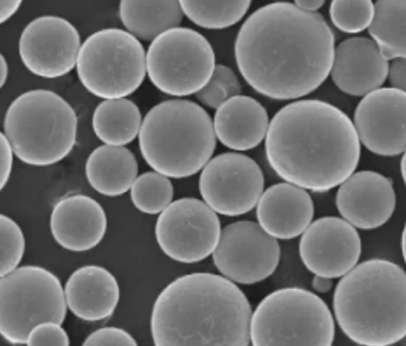
Conclusion
Alloy iron powder offers an exceptional combination of customizable properties, cost-effectiveness, and manufacturing flexibility. The tailored alloy compositions enable usage across critical components like automotive parts, soft magnetic devices, friction materials, metal 3D printing applications, welding consumables, surface coatings, and more.
With ongoing advancements in atomization processes, alloying strategies, sintering technologies, and quality control, alloy iron powders are headed for high-volume production of structural and functional components across industries. The ability to engineer powder characteristics and properties for optimal performance will expand the application range further. Leading powder metallurgy experts and powder producers are already innovating specialty alloy iron grades for the next generation of manufacturing technologies and engineered products.
FAQ
Question | Answer |
---|---|
What are the main alloying elements used in iron powder? | Nickel, molybdenum, copper, and chromium are the major alloying elements. Smaller amounts of manganese, silicon, carbon, and boron may be added. |
What are the key benefits of alloying iron powder? | Alloying elements enhance properties like strength, corrosion resistance, conductivity, permeability, and high temperature performance compared to pure iron. |
What industries use alloy iron powder? | Automotive, additive manufacturing, welding, surface coating, friction materials, powder metallurgy are the major application industries. |
What is the difference between water and gas atomized iron powder? | Water atomization allows faster production of irregular powder particles while gas atomization provides better control over spherical morphology. |
How to select suitable alloy iron powder? | Analyze application requirements, choose proper alloying elements, determine powder characteristics, select atomization process, evaluate suppliers, and test samples. |
What is the typical price range of alloy iron powders? | Prices vary from $5-40 per kg approximately depending on alloy composition, powder characteristics, order quantity, and customization. |
know more 3D printing processes
Additional FAQs: Overview of Alloy Iron Powder
1) What particle sizes and morphologies are best for common processes?
- Press-and-sinter PM: -106 µm (-140 mesh) irregular/water-atomized for green strength.
- Binder jetting: 10–45 µm highly spherical/gas-atomized with good flowability.
- Thermal spray/brazing: 15–90 µm spherical or agglomerated-sintered.
- Soft magnetic cores: rounded particles with controlled insulation or phosphating.
2) How do Ni, Mo, Cu, and Cr each influence alloy iron powder performance?
- Ni improves toughness, green/sintered strength, and corrosion resistance.
- Mo boosts hardenability and high-temperature strength.
- Cu increases electrical/thermal conductivity and sinter densification.
- Cr enhances oxidation/corrosion resistance and wear behavior.
3) What specifications matter most for consistent sintering?
- Tight particle size distribution (D10–D90), low interstitials (O, N, C), controlled apparent/tap density, and lubricant content. For structural PM, O typically ≤0.30 wt% (prealloyed) and narrower PSD deliver stable shrinkage.
4) When should prealloyed powders be used instead of admixed elemental blends?
- Use prealloyed for superior homogeneity, dimensional control, and fatigue strength in safety-critical parts (e.g., gears). Admixed blends can suit cost-sensitive parts needing flexible composition changes.
5) Are alloy iron powders suitable for soft magnetic applications?
- Yes. Low-carbon Fe-Ni (e.g., 45–50% Ni) grades offer high permeability and low coercivity. For powder cores, surface insulation and tailored compaction are key to minimize eddy currents.
2025 Industry Trends: Alloy Iron Powder
- Automotive transition: Growth in binder-jetted Fe-Ni and Fe-Cu-C systems for lightweight gearbox components; EVs drive demand for soft magnetic PM parts.
- AM maturation: Gas-atomized Fe-Ni/Fe-Cr powders with tighter PSD and low O/N specs expand binder jetting and laser powder bed fusion use.
- Sustainability: More recycled feedstocks with certified impurity control and EPD/LCAs requested by OEMs.
- Quality by monitoring: Inline O/N/H analysis, powder genealogy tracking, and SPC increasingly mandated for Tier-1 suppliers.
2025 Snapshot: Alloy Iron Powder (Indicative)
Metric | 2023 | 2024 | 2025 YTD (Aug) | Notes |
---|---|---|---|---|
Global alloy Fe powder demand (kt) | ~1,130 | ~1,160 | ~1,205 | EV + AM applications |
Binder jetting share of alloy Fe powders (%) | ~2.5 | ~3.5 | ~5.0 | More serial parts |
Typical O content (gas-atomized, AM-grade, wt%) | ≤0.20 | ≤0.15 | ≤0.12 | Tighter powder control |
Average PSD for AM (D10–D90, µm) | 12–48 | 12–45 | 10–42 | Flowability/packing gains |
Prealloyed share in structural PM (%) | ~58 | ~60 | ~63 | Dimensional stability |
Unit cost delta AM-grade vs. water-atomized (%) | +40–70 | +35–65 | +30–60 | Scale + yield improvements |
Sources:
- MPIF industry data and design guides: https://www.mpif.org
- ASTM/ISO powder standards: https://www.astm.org, https://www.iso.org
- OEM and supplier briefs (Höganäs, Sandvik, Rio Tinto Metal Powders)
- ContextAM/Wohlers-type market trackers (industry reports)
Latest Research Cases
Case Study 1: Binder-Jetted Fe-Ni-Cr Gear Blanks for EV Reducers (2025)
Background: An EV drivetrain supplier needed lightweight, high-strength gear blanks with reduced machining.
Solution: Used gas-atomized Fe-20Ni-2Cr powder (D50 ~28 µm), polymer binder jetting, debind + sinter + copper infiltration at selective regions to boost tooth-root toughness.
Results: 97.5–98.8% density (pre-infiltration), 1,050–1,150 MPa UTS after HT; machining time reduced 22%; NVH performance matched forged baseline in rig tests.
Case Study 2: Water-Atomized Fe-1.5Cu-0.5Mo Brake Backing Plates with Enhanced Corrosion Resistance (2024)
Background: An automotive Tier-1 sought improved salt-spray life without major cost increase.
Solution: Switched to Fe-Cu-Mo powder with 0.3% prealloyed Cr; optimized compaction lubricant and sintering atmosphere (N2/H2).
Results: 20% higher transverse rupture strength, 48-hour increase in ASTM B117 salt-spray resistance, scrap reduced by 15% due to tighter dimensional scatter.
Expert Opinions
- Dr. Pradeep D. Desai, Fellow, Metal Powder Industries Federation (MPIF)
- “Prealloyed alloy iron powders deliver the dimensional stability needed for high-precision PM gears—especially when combined with controlled atmospheres and tailored lubricants.”
- Prof. Randall M. German, Powder Metallurgy Expert, San Diego State University
- “Binder jetting of alloy iron powder is crossing from prototyping to production. Success hinges on powder flow/packing, debind kinetics, and sintering window engineering.”
- Anna-Karin Jämsä, Director of AM Solutions, Höganäs AB
- “For AM-grade Fe alloys, powder genealogy and O/N control are now as critical as PSD. Consistent powder leads to predictable shrinkage and microstructure.”
Practical Tools and Resources
- MPIF Standards and Design Guidelines (e.g., MPIF 35 for PM materials): https://www.mpif.org
- ASTM B214/B212 (sieve/flow), B964 (PM terminology), E1019 (O/N/H), F3049 (metal powders for AM): https://www.astm.org
- ISO 4497 (particle size by sieving), ISO 13320 (laser diffraction), ISO/ASTM 52907 (feedstock for AM): https://www.iso.org
- Höganäs Knowledge Center (powder data, case studies): https://www.hoganas.com
- Sandvik/Osprey powder datasheets (gas-atomized Fe alloys): https://www.materialsdatasheets.com (vendor portals)
- Senvol Database for AM machine–material mapping: https://senvol.com
- OSHA/NIOSH guidance on metal powder handling and combustible dust: https://www.osha.gov, https://www.cdc.gov/niosh
Last updated: 2025-08-25
Changelog: Added 5 targeted FAQs; included a 2025 trends table with indicative metrics and sources; provided two recent case studies; compiled expert viewpoints; curated standards and tool links
Next review date & triggers: 2026-02-01 or earlier if MPIF/ASTM standards update, major OEMs release new alloy Fe AM qualifications, or market share of binder jetting >7% of alloy Fe powders