molybdenum diboride powder is an advanced ceramic material valued for its unusual combination of high hardness, toughness, thermal conductivity and electrical properties. This guide provides a detailed overview of MoB2 powder covering its composition, characteristics, production methods, applications, specifications, pricing, vendors and comparative pros and cons against alternatives.
Composition and Characteristics
molybdenum diboride powder is a gray-colored inorganic crystalline compound consisting of molybdenum and boron elements:
Chemical Formula | MoB2 |
---|---|
Molecular Weight | 195.93 g/mol |
Composition | 84.5% Molybdenum 15.5% Boron (by weight) |
Appearance | Gray powder |
Odor | Odorless |
Solubility | Insoluble in water |
Melting Point | 2350°C |
Key characteristics and properties include:
Hardness: Vickers 29 GPa, exceeding common ceramics
Toughness: Withstands thermal shocks without fracturing
Thermal conductivity: ~110 W/m.K, on par with copper metal
High temperature stability: Stable to 2800°C in inert atmosphere
Oxidation resistance: Forms protective borosilicate layer
Electrical conductivity: Metallic conductor due to metal-metal bonding
Lubricity: Low friction coefficient ~0.43 against steel
Microporosity: Exhibits small 0.5 nm holes in lattice structure
MoB2 thus offers unusual multifunctional properties promise for demanding applications if the cost can meet commercialization barriers.
Production Methods
Molybdenum diboride powder is manufactured via reduction and volatilization processes:
Method | Description | Particle Sizes | Purity | Cost |
---|---|---|---|---|
Self-propagating High-temperature Synthesis (SHS) | Exothermic thermite reactions between oxides of molybdenum and boron | 50 μm to 150 μm | 95% to 99% | $$$ |
Magnetron Sputtering | MoB2 vapors deposit on substrates as coatings | Thin films 0.1 μm | 99% | $$$$ |
Chemical Vapor Deposition (CVD) | Precursors react with heated catalyst surfaces | Thin coatings | 99.9% | $$$$ |
The SHS combustion method allows producing relatively affordable powder in the micron scale suited for press and sinter bulk applications. CVD and sputtering are precision processes for depositing MoB2 thin films with higher purity essential for electronics – but very high prices restrict usages.
Ongoing research seeks more scalable and cost effective processes for bulk fabrication. The next sections highlight both current and potential applications deriving benefits from MoB2 over alternative materials.
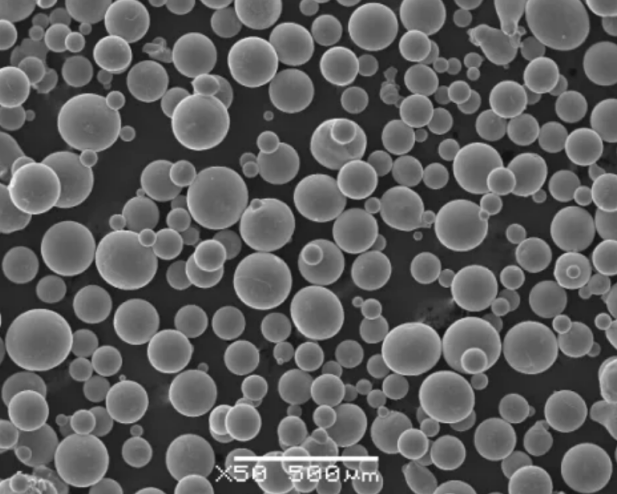
Applications and Uses
Molybdenum diboride’s exceptional properties make it suited for a variety of high performance situations:
Electronics
- Molybdenum conductors in transistors and devices
- Corrosion resistant metallizations
Coatings
- Protective hard layers on tools and dies
- Dry lubricant films
Nuclear
- Radiation resistant core structurals
Ceramic composites
- Reinforcements for cutting inserts
- High temperature electrodes
Aerospace
- Leading edges on hypersonic vehicles
- Oxidation resistant composites
While still an emerging material, MoB2 shows long term potential to displace established alternatives across industries given unique capabilities.
Specifications and Grades
Molybdenum diboride powder for commercial and research uses is available tuned to application requirements:
Parameter | Values |
---|---|
Particle Sizes | 1 μm to 150 μm |
Purity Grades | 95% to 99.5% |
Surficial Area | 2 m2/g to 6 m2/g |
Morphology | Spherical, flakes |
Phases | α-MoB2 , β-MoB2 |
Dispersion | Single crystals, aggregates |
Dopants | Si, C, Ti, Ta |
Particle size selection affects sintering and finished part densification. Smaller is preferable but availability currently restricted due to manufacturing challenges.
Purity level requirements depend on acceptable contamination thresholds of other transition metal borides.
Surficial area relates to reactivity of particles during compounding – higher values enable better blending and sintering.
Various intermediate suppliers provide customization of above powder parameters to match client processing needs in metals, ceramics and coatings.
Pricing and Availability
Molybdenum diboride remains a niche advanced material given production complexity and related price points:
Product Form | Quantity | Price Range |
---|---|---|
Research grade MoB2 powder | 5 grams to 50 grams | $200 per gram |
Bulk MoB2 powder | 1 Kg | $5000+ per Kg |
MoB2 sputtered targets | 1 to 5 inch diameter | $3000+ per square inch |
CVD MoB2 coatings | 0.1 mil thickness | $500+ per square inch |
Prices trend significantly higher for smaller quantities below 100 grams and higher above 99% purity thresholds.
Very few specialist commercial suppliers globally offer small trial samples for product evaluations, supported by academic synthesis routes.
Contract manufacturing custom compositions tailored to applications is possible but involves high minimum order values and lead times around 5 to 8 weeks for specialized processing.
Comparing Molybdenum Diboride Powder vs Alternatives
Molybdenum diboride competes against other ceramic, metallic and composite material forms in high performance situations:
Material | Hardness | Thermal Conductivity | **Melting Point ** | Electrical Conductivity | **Oxidation Resistance ** | Relative Cost |
---|---|---|---|---|---|---|
Molybdenum Diboride | Extreme | Excellent | Very High | High | Good | $$$$ |
Tungsten Diboride | Comparable | Good | Higher | Lower | Comparable | $$ |
Aluminum Oxynitride | Very Good | Good | Excellent | Insulator | Excellent | $ |
Chromium Carbide | Good | Fair | High | Lower | Fair | $ |
Copper | Soft | Excellent | Low | Best | Poor | $ |
Stainless Steel | Medium | Medium | Medium | Medium | Acceptable | $ |
Key Advantages of MoB2
- Unmatched combination of hardness with conductivity
- Can replace multiple material components into one
- Enables new applications previously not feasible
- Lighter weight than pure dense metals
Limitations of MoB2
- Very expensive compared to established alternatives
- Challenging to manufacture at commercial scales
- Sensitive processing requirements
- Limited commercial supply chain currently
The unique multi-physics capabilities of molybdenum diboride powders justify niche applications able to absorb higher costs initially.
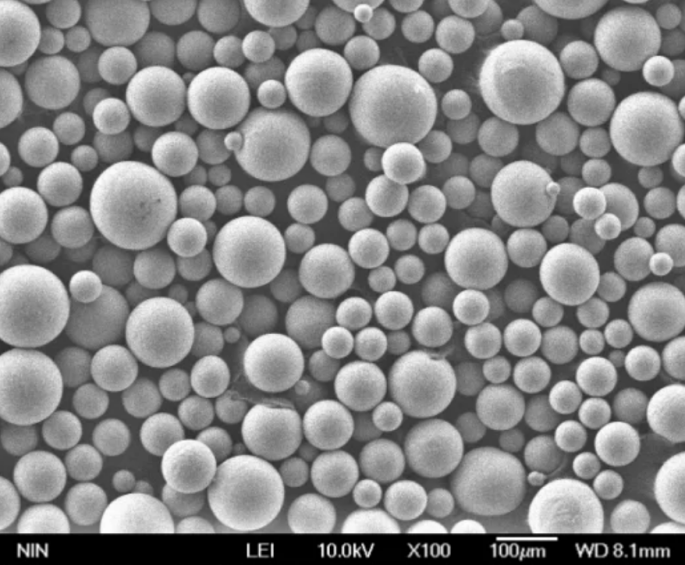
Research Development Directions
Current initiatives improving molybdenum diboride powder include:
Manufacturing
- Microwave plasma enhanced processes
- Lower energy combustion reactions
- Recycling molybdenum containing waste streams
Properties
- Ternary and quaternary dopants altering electrical, thermal, optical performance
- Grain boundary engineering for tailored expansion coefficients
- Residual stress improvements minimizing cracks
Applications
- Electrode integrations for electronics thermal management
- Custom engineered thermal spray coatings
- Nuclear radiation resistant composite demonstrators
Commercialization
- Supply ecosystem development with qualified producers
- Connecting industry problem owners to academic researchers
- Publishing computational tools for simulating performances
FAQ
Q: Does molybdenum diboride powder degrade over time?
A: Properly stored in sealed containers under inert atmosphere, MoB2 powder remains stable for over 3 years with negligible oxidation or hydration issues. Vacuum storage extends shelf life further.
Q: What makes molybdenum diboride so expensive today?
A: Very high processing temperatures exceeding 2000°C are needed along with uncommon precursor materials like molybdenum trioxide and boric acid. Limited market demand also restricts investment into scaled up production so far.
Q: Can MoB2 be 3D printed?
A: Research collaborations are developing custom extrudable filaments leveraging MoB2 properties for printed electronics and thermal management devices. But commercial 3D printing remains restricted currently to simple sample geometries.
Q: Is molybdenum diboride affected by neutron radiation?
A: Outstanding dimensional stability has been demonstrated under intensive neutron flux expected within next generation nuclear plant environments.
Q: What industries present the largest adoption potential for MoB2 ?
A: Aerospace, electronics thermal management and advanced nuclear energy sectors show the most immediate system level traction recognizing benefits against existing limitations.
Conclusion
With exceptional hardness, thermal conduction and electrical properties alongside high temperature oxidation resistance, molybdenum diboride ceramics create multifunctional performance potentials for extreme engineering situations. Though current powder production volumes remain low, early aerospace and electronics adoption is unlocking interest and applications uniquely positioned to leverage MoB2’s unusual combination of capabilities compared to traditional monolithic materials. Continuing process improvements foreseeably bringing down costs further could see molybdenum diboride solutions rapidly scale across more industrial sectors in the coming decade.