Introduction
Tungsten alloy powders are materials made from tungsten mixed with other metals, processed into a fine powder form. Tungsten alloys have very unique properties that make them suitable for many important applications across various industries. This article will provide an overview of tungsten alloy powders, their key properties, manufacturing methods, and main applications.
What is Tungsten Alloy Powder?
Tungsten alloy powder is a material produced by mixing elemental tungsten powder with powdered forms of other metals, then compacting and sintering the powders together. The most common metals alloyed with tungsten include nickel, iron, copper, and cobalt.
Tungsten has the highest melting point of all metals at 3422°C. By alloying it with other metals, new materials can be created that possess enhanced properties over either pure tungsten or the alloying elements alone.
Some key advantages of tungsten alloys include:
- High density – Pure tungsten has a density of 19.3 g/cc, making its alloys much denser than ordinary steel.
- Strength – Tungsten alloys often have very high strength-to-weight ratios. They are stronger than steel while being much denser.
- Hardness – Tungsten alloys are harder than most other metals, allowing them to resist wear even at high temperatures.
- Thermal properties – Tungsten has excellent thermal conductivity and a high melting point, allowing its alloys to withstand very high temperatures.
These unique property combinations make tungsten alloy powders ideal for many demanding applications. The powder metallurgy production process also allows for precise control over alloy compositions.
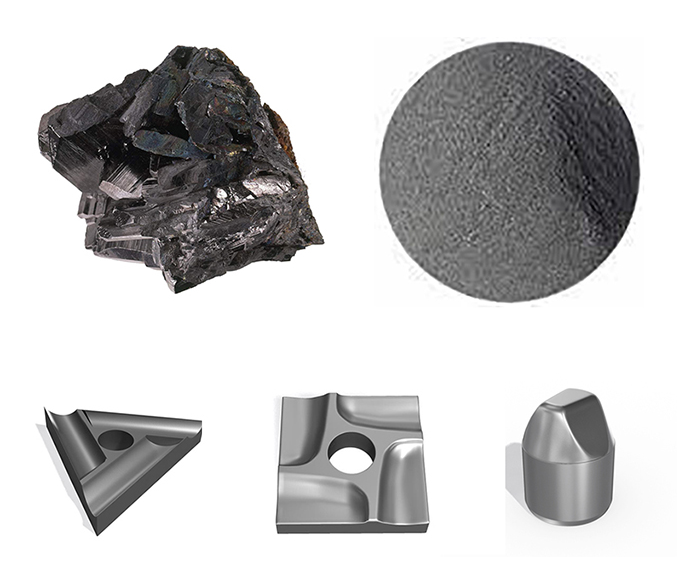
Manufacturing Tungsten Alloy Powder
Tungsten alloy powders are manufactured using advanced powder metallurgy techniques. The production process generally involves:
- Elemental powder mixing – High purity elemental powders of tungsten and the alloying elements are precisely weighed and blended together. Mixing is carried out using tumblers, high energy ball mills, or attritors.
- Compacting – The powder blend is compressed into a compact called a “green body” using techniques like cold isostatic pressing or die compaction. This gives the compact mechanical strength.
- Degassing/sintering – The green bodies are heated in a vacuum furnace to temperatures near the melting point of tungsten. This sinters the powders together into a consolidated form and removes any trapped gases.
- Comminution – Finally, the sintered alloy is crushed and ground to produce the finished powder product at the desired particle size and shape.
Powder metallurgy allows the properties of tungsten alloys to be precisely dialed in by adjusting the elemental composition and powder characteristics. It produces a fine, homogeneous material readily usable across many applications.
Properties of Tungsten Alloy Powder
Tungsten alloy powders exhibit a range of valuable properties stemming from their unique compositions:
- High density – Depending on the exact alloy, densities range from about 10 g/cc to 18 g/cc, significantly more than ordinary alloys.
- Strength – Tungsten alloys have very good strength-to-weight ratios. For example, 93W-4.9Ni-2.1Fe has a tensile strength exceeding 1 GPa.
- Hardness – Vickers hardness values of tungsten alloys generally fall between 200 HV and 500 HV, exceeding common alloy grades.
- Toughness – Certain tungsten alloys like W-Cu and W-Ni-Fe have reasonable toughness to resist cracking and brittle failure.
- High temperature strength – Strength is maintained to very high temperatures. For example, W-Cu retains good strength to over 700°C.
- Thermal/electrical conductivity – Tungsten alloys conduct heat and electricity well, with conductivity controlled by alloying.
- Corrosion resistance – Natural corrosion resistance of tungsten is passed on to its alloys.
These properties allow tungsten alloy powders to perform well across a wide array of demanding applications.
Main Applications of Tungsten Alloy Powder
Thanks to their balanced material properties, tungsten alloy powders are used across the following industries and applications:
Automotive
- Vehicle vibration damping weights – High density balances vehicle tires and damps vibrations.
- Exhaust gas recirculation valves – Withstand high temperatures and resist wear from exhaust gases.
- Fuel cell bipolar plates – Excellent electrical conductivity.
Aerospace
- Aircraft counterweights – Used to balance control surfaces due to high density.
- Radiation shielding – Effectively blocks radiation in space applications.
- Rocket nozzles – Resists extreme heat and corrosion from hot exhaust gases.
Electronics
- Heat sinks – Dissipate heat efficiently from electronics thanks to good thermal conductivity.
- Electrical contacts – Conductive tungsten alloys maintain reliable contact surfaces.
Medical
- Radiation shielding – Shields patients from stray radiation during medical X-ray and CT scan procedures.
- Collimators – Shape and direct radiation beams from equipment like medical linear accelerators.
Defense
- Kinetic energy penetrators – High density and strength make them ideal for armor-piercing ammunition.
- Radiation shielding – Used for nuclear, chemical, and biological protection suits and shelters.
Industrial
- Wear parts – Excellent abrasion and erosion resistance for parts like valves, nozzles, and extrusion dies.
- Welding electrodes – Low thermal expansion and high melt point suit them for arc welding.
- High temperature furnace components – Withstand temperatures exceeding 2000°C.
Sports & Recreation
- Golf club counterweights – Improve swing efficiency through precise weighting of club heads.
- Diving weights – Suitably high density for divers to control buoyancy underwater.
- Fishing weights – Heavy yet compact weights to carry fishing lines deep underwater.
Benefits of Using Tungsten Alloy Powder
Compared to other materials, tungsten alloy powders offer some unique benefits:
- Tailored properties – Alloying additions allow properties like density, strength, and conductivity to be dialed in.
- Precise manufacturing – Powder metallurgy enables precise control over microstructure and composition.
- Design flexibility – Powders can be used in injection molding, 3D printing, and pressing/sintering.
- High performance – Capable of outperforming metals like steel and titanium in specialized applications.
- Cost-effectiveness – Using powders is often more affordable than machining dense tungsten alloys.
Thanks to these advantages, tungsten alloy powders enable high performance parts to be manufactured in a cost-effective manner across diverse industries.
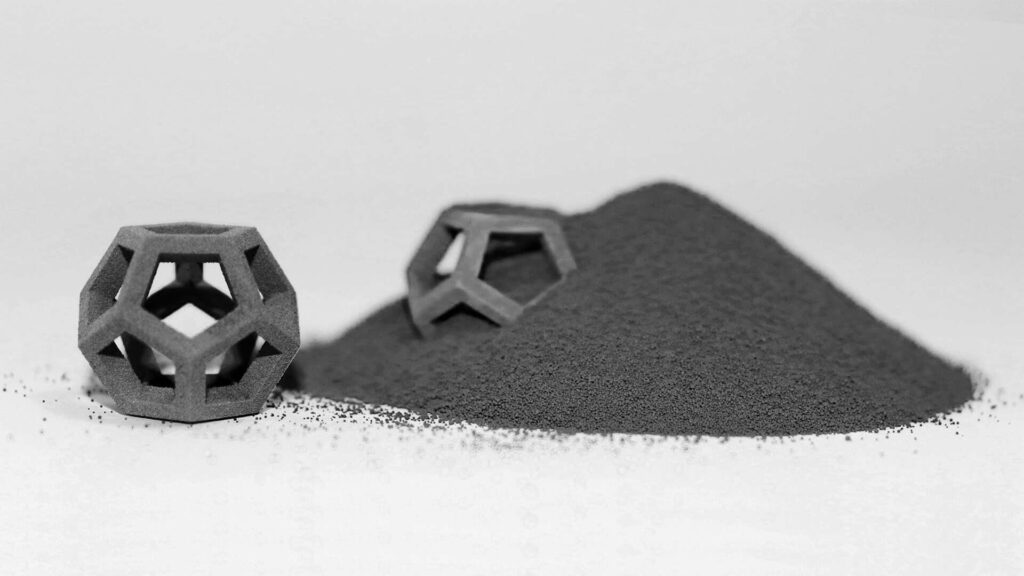
Tungsten Alloy Powder Specifications
Tungsten alloy powders are available under various industry and military specifications that define the expected chemistry, properties, testing methods, and quality assurance requirements. Some common tungsten alloy powder specifications include:
- ASTM B777 – Covers chemical compositions and property limits of W-Ni-Fe, W-Ni-Cu, and W-Cu alloys.
- MIL-T-21014 – Defines tungsten heavy alloy types for defense applications including W-Ni-Fe, W-Ni-Cu, and W-Cu.
- ISO 18119 – International standard covering tungsten alloy powders for cemented carbide production.
- China YB/T 2003 – National standard for tungsten heavy alloy powders used in China.
- JIS H 3201 – Japanese industrial standard for tungsten alloy powders.
- company-specific specifications – Major powder producers also have proprietary specifications.
These specifications help ensure users can purchase standardized, high quality powders for mission-critical parts and components across global supply chains.
FAQ
What are the main alloying elements used with tungsten powder?
The most common metals alloyed with tungsten powder include nickel, iron, copper, cobalt, silver, and molybdenum. Each element imparts different properties to the tungsten alloy.
How are tungsten alloy powders made into final parts?
Common powder-to-part processes include cold pressing and sintering, metal injection molding, hot isostatic pressing, additive manufacturing, and hot extrusion. The powders are formed into a desired shape then densified into a solid part.
What industries use the most tungsten alloy powder?
The major consumers of tungsten alloy powders are the aerospace, automotive, electronics, medical, defense, sporting goods, and industrial sectors. Each utilizes the unique properties of these alloys.
What types of tungsten alloy powders are available?
Popular alloy systems include W-Ni-Fe, W-Ni-Cu, W-Cu, W-Mo, and W-Co. Within each system, a range of compositions are available with varying tungsten contents from 90-98% to balance properties.
How are tungsten alloy powder particle sizes classified?
Common powder size classifications include coarse (-100 mesh), medium (-325 mesh), fine (-400 mesh), and ultrafine (1 micron). Finer sizes allow more consistency in pressed parts but can be more challenging to handle.
What health and safety precautions apply to tungsten powders?
Like other fine metal powders, tungsten alloy powders can be a dust explosion hazard. Proper protective equipment and ventilation is recommended when handling powders to limit exposure. Some alloys also contain nickel which can cause skin sensitization.
What are common applications for tungsten-nickel-iron alloys?
W-Ni-Fe alloys are found in counterweights, radiation shielding, depleted uranium replacements, gyroscope wheels, ballast weights, and projectile/kinetic energy penetrators, among other uses.
How do tungsten alloy powders compare to pure tungsten powders?
Alloying improves the toughness and workability of tungsten. Pure tungsten is extremely brittle. However, alloying lowers the melting point compared to pure tungsten. Selection depends on specific application requirements.
Are tungsten alloy powders environmentally friendly?
Like most metals, tungsten alloys are fully recyclable at end of life. Tungsten is considered a conflict-free metal sourced responsibly from mines worldwide. Some formulations also replace toxic lead or depleted uranium.
know more 3D printing processes
Additional FAQs on Tungsten Alloy Powder
1) How do I choose between W–Ni–Fe and W–Ni–Cu heavy alloys?
- W–Ni–Fe typically offers higher strength and better machinability; W–Ni–Cu provides improved corrosion resistance and is non‑magnetic, useful for certain medical and instrumentation applications.
2) What powder attributes most affect sintered density and strength?
- Particle size distribution (bimodal mixes pack better), high sphericity/low satellites, low oxygen and carbon, narrow PSD (e.g., D10–D90 tailored to process), and clean surfaces. These drive green density and liquid‑phase sintering efficiency.
3) Can tungsten alloy powder be used in additive manufacturing?
- Yes. Gas‑atomized spherical W, W–Cu, and W‑heavy alloy powders are used in LPBF and binder jetting. LPBF demands fine spherical PSD (≈15–45 μm) and elevated preheat; binder‑jetted parts typically require sinter + HIP.
4) How do tungsten heavy alloys compare to lead for radiation shielding?
- W‑heavy alloys achieve similar or higher attenuation with smaller thickness due to higher density (up to ~18.5 g/cc) and are lead‑free, offering better mechanical robustness and environmental compliance.
5) What are best practices for safe handling of tungsten alloy powders?
- Use grounded equipment and explosion‑protected dust collection, maintain inert gas blanketing for ultrafine powders, wear appropriate PPE (P3/N100 respirators), control nickel exposure (if present), and follow NFPA 484 guidance.
2025 Industry Trends for Tungsten Alloy Powder
- Lead‑free shielding surge: Healthcare and NDT sectors increasingly specify W‑heavy alloys to replace Pb, prioritizing recyclability and robustness.
- AM heat management parts: Growth in W–Cu lattice heat sinks for power electronics and aerospace thermal hardware.
- Supply diversification: Expanded secondary sources and recycling to mitigate concentrate volatility from primary producers.
- High‑g counterweights: e‑Aviation and space platforms adopt high‑density W‑Ni‑Fe for compact mass balancing.
- Digital QA: Material passports track powder genealogy, oxygen pickup, and blend‑back ratios in production.
2025 Metric (Tungsten Alloy Powder/Products) | Typical Range/Value | Why it matters | Source |
---|---|---|---|
Density of W‑heavy alloys (ASTM B777 classes) | ~17.0–18.5 g/cc | Shielding and counterweight performance | ASTM B777; supplier datasheets |
Tensile strength (93W–Ni–Fe) | 800–1,200 MPa (sintered + HIP) | Structural capability | ASM Handbooks; vendor data |
Radiation attenuation vs. lead (at 100 keV) | W‑alloy ≈ 1.6–1.9× Pb per mm | Design thickness reduction | IMOA technical notes |
Typical LPBF PSD for W‑alloys | D10–D90 ≈ 15–45 μm | Recoating/melt stability | ISO/ASTM 52907 |
Oxygen spec in AM‑grade W powder | ≤0.05–0.15 wt% O (process‑dependent) | Ductility and crack resistance | OEM specs; ASM |
Indicative price band (W‑heavy alloy powder) | ~$60–$150/kg+ (composition/PSD) | Budgeting and sourcing | Market trackers/suppliers |
Authoritative references and further reading:
- ASTM B777 (W‑Ni‑Fe/Cu heavy alloys) and ISO/ASTM 52907 (AM feedstock): https://www.astm.org and https://www.iso.org
- International Molybdenum & Tungsten associations (ITIA): https://www.itia.info
- ASM Handbook: Powder Metallurgy; Refractory Metals: https://www.asminternational.org
- NFPA 484 (combustible metals safety): https://www.nfpa.org
Latest Research Cases
Case Study 1: Lead‑Free W‑Ni‑Fe Shielding Blocks for Interventional Radiology (2025)
Background: A hospital network sought thinner, durable shielding to replace lead in mobile barriers.
Solution: Adopted 95W–Ni–Fe powder consolidated by liquid‑phase sintering and HIP; surfaces coated with antimicrobial polymer.
Results: 22% thickness reduction for equivalent attenuation at diagnostic energies, improved impact resistance, and 100% recyclability of offcuts; ROI in 18 months via longer service life.
Case Study 2: Binder‑Jetted W–Cu Lattice Heat Sinks for GaN Power Modules (2024)
Background: An e‑mobility Tier‑1 needed compact, high‑conductivity heat spreaders with tailored CTE.
Solution: Binder jetting W–Cu composite powder, followed by H2 sinter and pressure infiltration to reach target Cu fraction; final surface machining.
Results: Effective thermal conductivity 220–240 W/m·K, CTE matched to ceramic substrates, 28% mass reduction vs. solid designs, and 15% lower junction temperature at peak load.
Expert Opinions
- Dr. Peter G. Sanders, Professor of Materials Engineering, Purdue University
Key viewpoint: “Bimodal PSDs and controlled oxygen are the two largest levers in achieving high density and toughness in tungsten heavy alloys.” - Dr. Ulrich Martin, Head of Refractory Metals, Fraunhofer IFAM
Key viewpoint: “AM of W‑based alloys is maturing—preheating and post‑HIP are key for defect mitigation, opening applications in thermal management and shielding.” - Dr. Beverly A. Macfarlane, Radiation Physics Consultant
Key viewpoint: “W‑alloys deliver consistent attenuation with superior mechanical integrity versus lead, simplifying handling and extending lifecycle in clinical environments.”
Citations for expert profiles:
- Purdue University: https://engineering.purdue.edu
- Fraunhofer IFAM: https://www.ifam.fraunhofer.de
Practical Tools and Resources
- Standards and qualification
- ASTM B777 (heavy alloys), MIL‑T‑21014, ISO 18119 (tungsten alloys for carbides), ISO/ASTM 52907 (AM feedstock)
- Powder QC and processing
- LECO O/N/H analyzers: https://www.leco.com
- Sieve/laser diffraction PSD (ASTM B214/B822); tap/apparent density (ASTM B212/B329)
- HIP and vacuum sintering services: https://www.bodycote.com
- Design and simulation
- nTopology for lattice shielding/heat sink designs
- Ansys/COMSOL for thermal and radiation transport modeling
- Market and data
- ITIA tungsten statistics: https://www.itia.info
- USGS commodity summaries (tungsten): https://pubs.usgs.gov/periodicals/mcs
Last updated: 2025-08-21
Changelog: Added 5 targeted FAQs, a 2025 trends table with metrics and sources, two tungsten alloy powder case studies, expert viewpoints with citations, and curated tools/resources.
Next review date & triggers: 2026-02-01 or earlier if ASTM/MIL specs are revised, major OEMs publish new AM parameter sets for W‑alloys, or tungsten powder pricing/availability shifts >10% QoQ.