Iron-based alloy powders are revolutionizing the metalworking industry, offering a versatile and innovative approach to creating complex, high-performance parts. Imagine having a toolbox filled with tiny metal building blocks, each one possessing unique properties tailored for specific applications. That’s the power of iron-based alloy powders – a universe of possibilities condensed into a granular form.
Understanding the Fundamentals
At its core, iron-based alloy powder is a finely divided metal mixture composed primarily of iron, often blended with other elements like nickel, chromium, or molybdenum. The specific elements and their ratios define the unique characteristics of each powder type. Just like a recipe, the precise combination of ingredients determines the final product’s properties – strength, corrosion resistance, and even printability in 3D printing applications.
Here’s a table summarizing the key details of iron-based alloy powders:
Key Details | Description |
---|---|
Composition | Primarily iron, often alloyed with elements like nickel, chromium, molybdenum, etc. |
Particle Size | Varies depending on application; typically ranges from micrometers to hundreds of microns. |
Production Methods | Water atomization, gas atomization, crushing, milling. |
Applications | Additive manufacturing, metal injection molding, thermal spraying, welding, and more. |
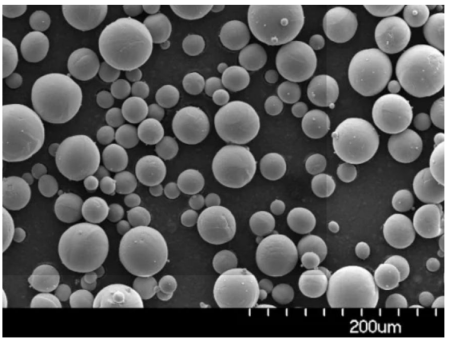
Exploring Different Iron-Based Alloy Powders
The beauty of iron-based alloy powders lies in their diversity. Each type offers a distinct set of properties, making them ideal for various applications. Let’s delve into ten specific models to understand their unique capabilities:
- SAE 316L Stainless Steel Powder: This versatile powder boasts excellent corrosion resistance and is perfect for applications requiring high strength and durability in harsh environments, like chemical processing equipment or marine components. Think of it as a metal workhorse, standing strong against the elements.
- Maraging Steel Powder: Known for its exceptional strength-to-weight ratio, maraging steel powder excels in aerospace and defense applications. Imagine building lightweight yet incredibly strong parts for aircraft or missiles – that’s the magic of maraging steel powder.
- Low-Alloy Steel Powder: As the name suggests, this powder contains minimal alloying elements, making it a cost-effective option for general-purpose applications. It’s the reliable friend in the toolbox, perfect for everyday metalworking needs.
- Tool Steel Powder: Get ready for some serious cutting-edge technology! Tool steel powder is formulated for exceptional wear resistance, making it ideal for creating durable tools and dies. Imagine crafting long-lasting drill bits or punches – that’s the power of tool steel powder.
- Nickel-Iron Powder: This magnetic marvel offers exceptional soft magnetic properties, making it perfect for applications like transformer cores or electromagnetic devices. Think of it as the silent conductor, guiding the flow of electricity efficiently.
- Copper-Iron Powder: Looking for a blend of electrical conductivity and thermal performance? Look no further than copper-iron powder. This unique combination makes it ideal for applications like heat sinks or electrical contacts. Imagine a material that can handle both heat and electricity – that’s the beauty of copper-iron powder.
- Invar 36 Alloy Powder: Dimensional stability is key in certain applications, and that’s where Invar 36 alloy powder shines. With minimal thermal expansion, this powder is perfect for creating components that need to maintain precise dimensions even with temperature fluctuations. Think of it as the unwavering ruler, keeping measurements accurate regardless of the heat.
- Kovar Alloy Powder: Matching thermal expansion coefficients across different materials can be a challenge. Kovar alloy powder comes to the rescue! This specially formulated powder boasts a thermal expansion coefficient that closely matches that of glass, making it ideal for creating glass-to-metal seals in electronic devices. Imagine a seamless bond between glass and metal – that’s the magic of Kovar alloy powder.
- MIM 4600 Stainless Steel Powder: Metal injection molding (MIM) is a revolutionary process for creating complex, near-net-shape metal parts. MIM 4600 stainless steel powder is specifically designed for this application, offering excellent flowability and sinterability for intricate geometries. Think of it as the artist’s palette for MIM, allowing for the creation of intricate and functional metal parts.
- 420 Stainless Steel Powder: Durability and corrosion resistance are hallmarks of 420 stainless steel powder. This powder is often used in additive manufacturing (3D printing) to create functional parts for applications like cutlery, gears, and medical instruments.
Applications of Iron Based Alloy Powders
Iron-based alloy powders transcend their granular form, transforming into a myriad of functional and innovative applications. Here, we explore some of the key areas where these versatile powders are making a significant impact:
- Additive Manufacturing (3D Printing): Iron-based alloy powders are a game-changer in the world of 3D printing. They allow for the creation of complex, near-net-shape metal parts with intricate designs that would be impossible with traditional manufacturing techniques. Imagine printing a customized gear with internal channels for weight reduction – that’s the power of iron-based alloy powders in 3D printing. Compared to traditional methods like machining, 3D printing with iron-based alloy powders offers greater design freedom, reduced waste, and the ability to create lightweight structures.
- Metal Injection Molding (MIM): MIM is another revolutionary process that leverages the power of iron-based alloy powders. Here, the powder is mixed with a binder, molded into the desired shape, and then debindered and sintered to create a high-precision metal part. MIM is particularly well-suited for producing small, complex components with tight tolerances, like gears, sprockets, and medical implants. Compared to traditional processes like casting, MIM offers better dimensional accuracy, the ability to create intricate shapes, and high material utilization with minimal waste.
- Thermal Spraying: This technique involves using iron-based alloy powders to create a protective coating on a substrate material. The powder is melted using a heat source like a plasma torch and then sprayed onto the substrate. Thermal spraying offers several advantages, including improved wear resistance, corrosion resistance, and the ability to rebuild worn or damaged surfaces. Compared to other coating methods like electroplating, thermal spraying with iron-based alloy powders offers greater versatility in terms of material selection, thicker and more durable coatings, and the ability to coat a wider range of substrate materials.
- Welding: Iron-based alloy powders are finding increasing use in welding applications. They can be used as filler metals to join similar or dissimilar metals, offering improved weld strength, corrosion resistance, and reduced distortion compared to traditional welding techniques.
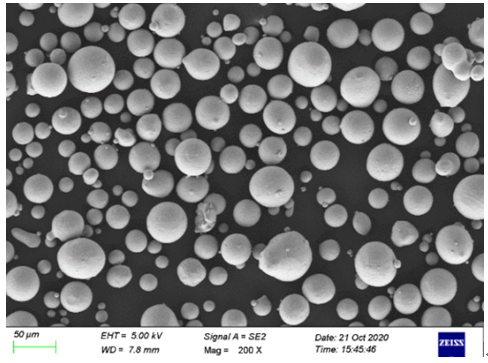
Properties and Characteristics
The unique properties of iron-based alloy powders determine their suitability for various applications. Here’s a table outlining some of the key characteristics to consider:
Property | Description | Importance |
---|---|---|
Particle Size & Distribution | Affects flowability, packing density, and final part properties. | Finer powders offer better surface finish but may be less flowable. |
Sphericity | Refers to the shape of the powder particles. | Spherical particles flow better and pack more densely, leading to improved printability and sinterability. |
Apparent Density | The bulk density of the powder. | Affects material handling and storage requirements. |
Chemical Composition | Defines the final properties of the sintered part. | Different alloying elements provide specific properties like strength, corrosion resistance, or electrical conductivity. |
Melting Point | The temperature at which the powder particles melt. | Plays a crucial role in 3D printing, MIM, and thermal spraying processes. |
Specifications, Sizes, Grades & Standards
The world of iron-based alloy powders is vast, with a wide range of specifications, sizes, grades, and standards to consider. Here’s a table to provide a glimpse into this diverse landscape:
Factor | Description | Example |
---|---|---|
Specifications | Refer to the specific properties and composition of the powder. | ASTM International (ASTM) or International Organization for Standardization (ISO) standards define these specifications. |
Particle Size | Typically ranges from 10 to 150 micrometers, depending on the application. | Finer powders are used for 3D printing and MIM, while coarser powders are used for thermal spraying. |
Grades | May vary based on the level of purity, oxygen content, or flowability. | Higher-grade powders offer improved performance but may come at a higher cost. |
Standards | Ensure consistent quality and performance. | Common standards include ASTM B294 for iron powder and ASTM F3049 for additive manufacturing powders. |
Pros & Cons of Iron Based Alloy Powders
Iron-based alloy powders, like any other material, come with their own set of advantages and limitations. Understanding these trade-offs is crucial for making informed decisions in your metalworking endeavors.
Advantages:
- Design Freedom: Compared to traditional subtractive manufacturing techniques like machining, iron-based alloy powders in 3D printing unlock a world of design possibilities. Complex geometries, internal channels, and lightweight structures become achievable, pushing the boundaries of innovation. Imagine printing a customized engine component with intricate cooling channels for improved performance – that’s the design freedom advantage of iron-based alloy powders.
- Material Efficiency: Traditional manufacturing processes often generate significant waste in the form of scrap metal. Iron-based alloy powders, particularly in applications like MIM, offer a more material-efficient approach. The near-net-shape capability minimizes waste and optimizes material utilization. Think of it as a more sustainable approach to metalworking, reducing environmental impact.
- Mass Customization: The ease and flexibility of 3D printing with iron-based alloy powders make mass customization a reality. Imagine producing a batch of gears, each with slight variations for specific applications – that’s the power of mass customization offered by these versatile powders.
- Near-Net-Shape Manufacturing: Both 3D printing and MIM processes with iron-based alloy powders allow for the creation of parts that are very close to their final desired shape. This minimizes the need for extensive post-processing steps, reducing overall production time and cost. Think of it as getting a part closer to its finished form right from the start, streamlining the manufacturing process.
Limitations:
- Cost: Compared to traditional materials like cast iron or machined steel, iron-based alloy powders can be more expensive, particularly for high-performance grades. This is due to the complex production processes involved and the potential for higher material waste during initial development stages.
- Surface Finish: While 3D printing and MIM with iron-based alloy powders offer significant design freedom, achieving a smooth surface finish can sometimes be challenging. The inherent roughness of the powder particles can translate to a slightly textured surface on the final part. Think of it as a trade-off – complex designs may come with a slightly less smooth finish compared to machined parts.
- Post-Processing: Depending on the application, iron-based alloy powders may require additional post-processing steps like heat treatment or infiltration to achieve the desired final properties. This can add to the overall production time and cost.
- Limited Material Selection: While there is a vast array of iron-based alloy powders available, the selection is not as extensive as with traditional wrought alloys. This may limit options for specific applications requiring unique material properties.
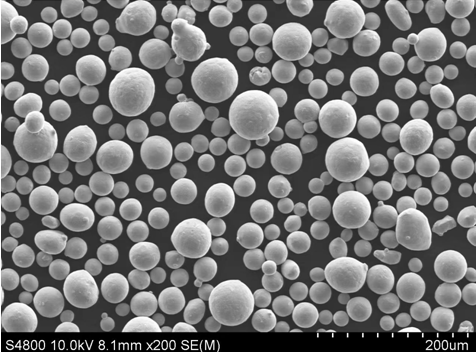
The Verdict: A Well-Informed Choice
Iron-based alloy powders are revolutionizing the metalworking landscape. By understanding their strengths and weaknesses, you can make informed decisions about their suitability for your specific needs. If design freedom, material efficiency, and near-net-shape manufacturing are priorities, then iron-based alloy powders offer a compelling solution. However, if cost is a major concern, or if achieving a perfectly smooth surface finish is crucial, then traditional methods might be a better fit.
Ultimately, the choice comes down to a careful evaluation of your project requirements, balancing the advantages of iron-based alloy powders with their limitations to achieve the best possible outcome.
FAQs
Here’s a table addressing some frequently asked questions about iron-based alloy powders:
Question | Answer |
---|---|
What are the benefits of using iron-based alloy powders over traditional metalworking methods? | Iron-based alloy powders offer greater design freedom, improved material efficiency, and the ability to create near-net-shape parts. |
What are some of the limitations of iron-based alloy powders? | Cost, surface finish requirements, potential for additional post-processing steps, and limited material selection compared to wrought alloys. |
What are the typical applications of iron-based alloy powders? | Additive manufacturing (3D printing), metal injection molding (MIM), thermal spraying, and welding. |
How are iron-based alloy powders produced? | Common production methods include water atomization, gas atomization, crushing, and milling. |
What are some factors to consider when choosing an iron-based alloy powder? | The specific application, desired properties, particle size, chemical composition, and cost. |
By delving into the world of iron-based alloy powders, you’ve unlocked a treasure trove of possibilities for your metalworking endeavors. Remember, careful consideration of their properties, limitations, and various applications will empower you to make informed decisions and create innovative metal parts that push the boundaries of design and functionality.