Introduction of Cold sprayadditive technology
- Gas type, e.g. air, nitrogen, helium
- Gas pressure
- Gas temperature
- Particle size
- Feedstock material properties, e.g. density, strength, melting temperature
- Nozzle type
- Substrate
- Deposition kinetics (gun transverse speed, scan velocity, number of passes …)
- Standoff distance, the distance between the cold spray nozzle and the substrate.
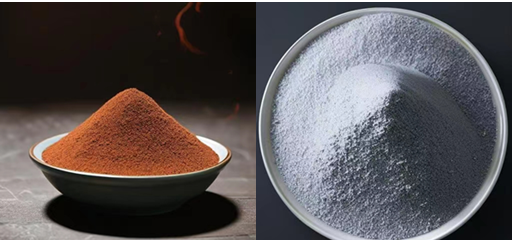
The articles of studies above are cited here:
1.N. Hutasoit, R.A.R. Rashid, S. Palanisamy, A. Du N. Hutasoit, R.A.R. Rashid, S. Palanisamy, A. Duguid, Int. J. Adv. Manuf. Technol. 110 (2020) 2341–2357.
2.S. Singh, P. Singh, H. Singh, R.K. Buddu, Mater. Today Proc. 18 (2019) 830–840.
3.K. Yang, W. Li, X. Guo, X. Yang, Y. Xu, J. Mater. Sci. Technol. 34 (2018) 1570–1579.
4.M.S. Lee, H.J. Choi, J.W. Choi, H.J. Kim, Nucl. Eng. Technol. 43 (2011) 557–566.
5.C. Huang, M. Arseenko, L. Zhao, Y. Xie, A. Elsenberg, W. Li, F. Gärtner, A. Simar, T. Klassen, Mater. Des. 206 (2021) 109826.
6.W. Li, D. Wu, K. Hu, Y. Xu, X. Yang, Y. Zhang, Surf. Coatings Technol. 409 (2021) 126887.
7.Y.J. Li, X.T. Luo, C.J. Li, Surf. Coatings Technol. 407 (2021) 126709.
8.R. Huang, M. Sone, W. Ma, H. Fukanuma, Surf. Coatings Technol. 261 (2015) 278–288.
9.Undisclosed.
10.S. Yin, R. Jenkins, X. Yan, R. Lupoi, Mater. Sci. Eng. A 734 (2018) 67–76.
11.F. Gärtner, T. Stoltenhoff, J. Voyer, H. Kreye, S. Riekehr, M. Koçak, Surf. Coatings Technol. 200 (2006) 6770–6782.
12.Y. Li, Y. Wei, X. Luo, C. Li, N. Ma, J. Mater. Sci. Technol. 40 (2019) 185–195.