In the world of high-performance materials, Inconel 738LC powder stands out as a crucial player, particularly in industries requiring robust mechanical properties at elevated temperatures. Known for its excellent resistance to oxidation, corrosion, and heat, Inconel 738LC has carved out a niche for itself in fields such as aerospace, gas turbines, and power generation. Whether you’re an engineer, a manufacturer, or just curious about this fascinating metal alloy powder, this article is your one-stop guide to understanding everything you need to know about Inconel 738LC powder.
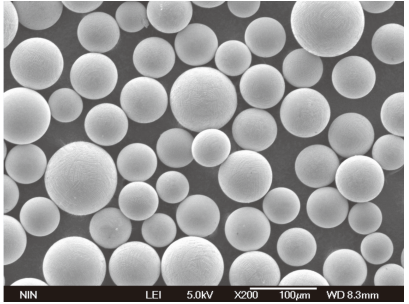
Overview of Inconel 738LC Powder
Inconel 738LC is a nickel-based superalloy designed to withstand extreme conditions of high heat and stress. This makes it an ideal choice for critical components like turbine blades, combustor sections, and other hot gas path components in turbines. The “LC” in Inconel 738LC stands for “Low Carbon,” indicating its modified composition to offer improved mechanical properties and increased resistance to thermal fatigue and oxidation.
What sets Inconel 738LC powder apart is its ability to retain its strength and stability at temperatures exceeding 1000°C, making it an ideal material for Additive Manufacturing (AM), Metal Injection Molding (MIM), and Hot Isostatic Pressing (HIP) processes. Let’s dive deeper into its unique properties, composition, and applications.
Composition of Inconel 738LC Powder
Understanding the composition of Inconel 738LC powder is essential to grasp why it’s so effective under extreme conditions. This nickel-based alloy contains specific elements, each contributing unique properties.
Element | Percentage (%) | Role in Alloy |
---|---|---|
Nickel (Ni) | 59-63 | Provides corrosion and oxidation resistance, base element of the alloy |
Chromium (Cr) | 15.7-16.3 | Enhances high-temperature oxidation resistance |
Cobalt (Co) | 8-9 | Increases strength and oxidation resistance |
Aluminum (Al) | 3.3-3.7 | Provides oxidation resistance and improves strength via precipitation hardening |
Titanium (Ti) | 3.2-3.7 | Contributes to strength through precipitation hardening |
Tantalum (Ta) | 1.4-1.7 | Increases high-temperature strength |
Tungsten (W) | 1.4-1.7 | Enhances creep resistance and strength at high temperatures |
Molybdenum (Mo) | 1.6-2 | Contributes to solid-solution strengthening |
Carbon (C) | 0.09-0.13 | Adds to carbide precipitation for strengthening at high temperatures |
Zirconium (Zr) | 0.05-0.12 | Reduces grain boundary embrittlement |
Boron (B) | 0.005-0.01 | Improves high-temperature ductility |
Each of these elements has been carefully selected to create a superalloy that offers a balance of strength, oxidation resistance, and thermal stability. The low-carbon content (LC) helps prevent carbide precipitation at grain boundaries, which can weaken the material at elevated temperatures.
Characteristics of Inconel 738LC Powder
When it comes to Inconel 738LC powder, its characteristics are key to its high-performance applications. Below are some of the notable features:
1. High Temperature Strength
Inconel 738LC powder maintains its strength even at temperatures exceeding 1000°C, which makes it perfect for applications in gas turbines and aerospace.
2. Oxidation and Corrosion Resistance
The combination of Nickel, Chromium, and Aluminum offers excellent resistance to oxidation, corrosion, and wear, even under extreme operating conditions.
3. Excellent Creep Resistance
With elements like Tungsten, Molybdenum, and Tantalum, this alloy shows great resistance to creep deformation, which occurs over long periods of exposure to high stress and temperature.
4. Fatigue Resistance
Due to its low carbon content, Inconel 738LC powder offers superior fatigue resistance, particularly under thermal cycling conditions, where components are exposed to rapid heating and cooling.
5. Machinability and Weldability
While Inconel 738LC is known for being tough to machine, the powder form allows it to be efficiently processed via additive manufacturing, HIP, and metal injection molding, improving its adaptability in various applications.
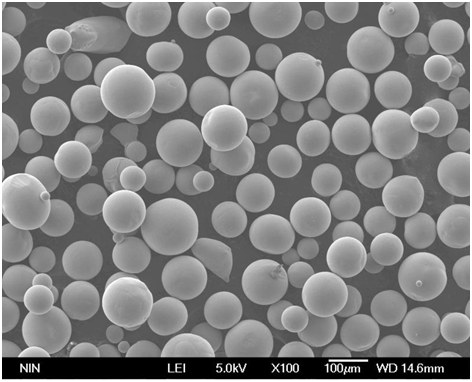
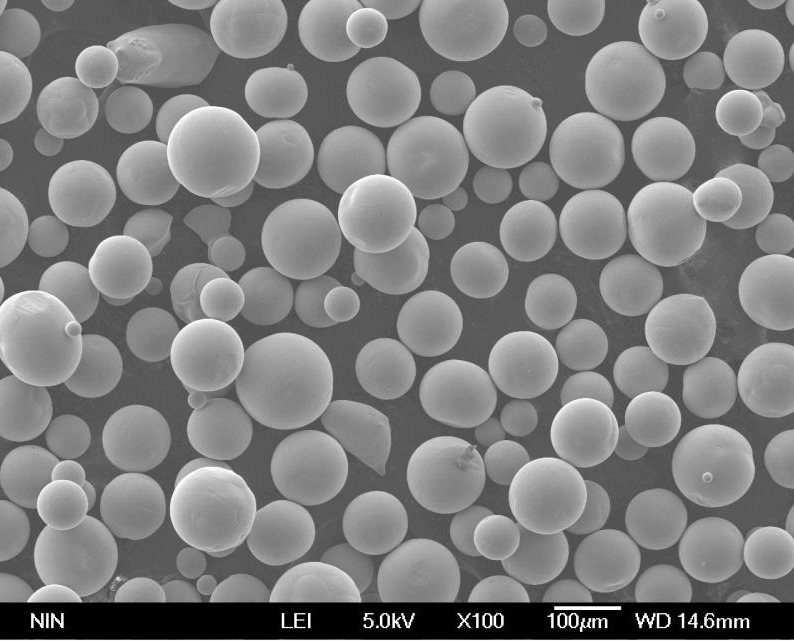
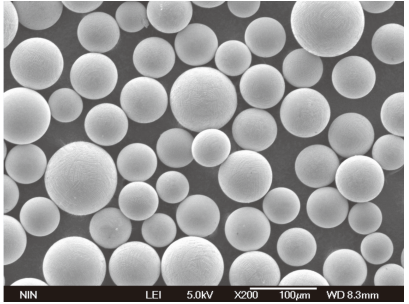
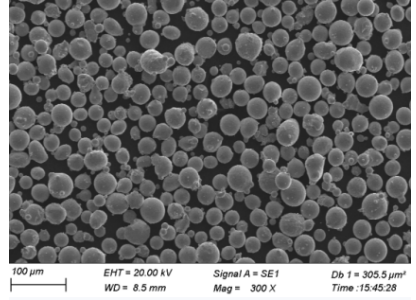
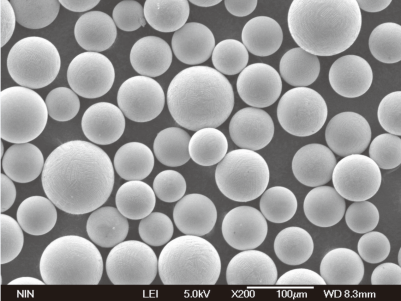
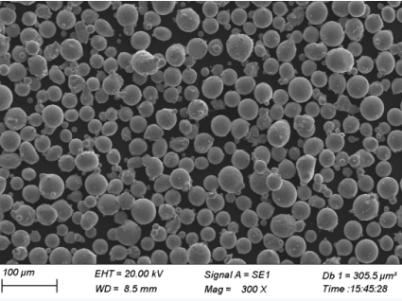
Applications of Inconel 738LC Powder
The Inconel 738LC alloy is widely used in industries that demand materials capable of withstanding extreme stress, temperature, and corrosive environments. Here are some of the most common applications:
Application | Industry | Why Inconel 738LC Is Used |
---|---|---|
Turbine Blades | Aerospace/Power Generation | High-temperature strength and oxidation resistance |
Combustor Sections | Gas Turbines | Thermal fatigue resistance and oxidation resistance |
Hot Gas Path Components | Energy | Superior creep resistance and corrosion resistance |
Aerospace Engines | Aerospace | Withstands high temperatures and mechanical stresses |
Heat Shields | Space Exploration | Heat resistance and ability to retain mechanical properties under stress |
Industrial Gas Turbines | Power Generation | Prolonged service life under extreme operational conditions |
Additive Manufacturing (3D printing) | Manufacturing | Allows intricate designs with high strength and thermal properties |
Metal Injection Molding (MIM) | Manufacturing | Enables efficient production of complex shapes with high precision |
Nuclear Reactor Components | Nuclear Power | Radiation resistance and performance in high-temperature environments |
As you can see, the Inconel 738LC powder has far-reaching applications, proving its versatility across industries where performance and durability are paramount.
Inconel 738LC Powder Models
To give you a more complete view, here are 10 specific models of Inconel 738LC powder that differ in size, form, or specific features:
Model | Description | Size/Grade |
---|---|---|
Inconel 738LC AM | Specifically designed for additive manufacturing, excellent for 3D printing applications | 15-45 µm |
Inconel 738LC-FG | Fine-grade powder for high-precision metal injection molding | 10-25 µm |
Inconel 738LC-HIP | Optimized for hot isostatic pressing to reduce porosity and enhance mechanical properties | 20-53 µm |
Inconel 738LC-3D | High-flow powder for metal additive manufacturing and 3D printing | 15-45 µm |
Inconel 738LC-MIM | Suitable for metal injection molding, offers high strength and complex shape fabrication | 10-25 µm |
Inconel 738LC-W | Powder optimized for welding and repair of high-temperature components | 30-90 µm |
Inconel 738LC-C | Combines high creep resistance with corrosion resistance, suitable for aerospace applications | 20-53 µm |
Inconel 738LC-SLM | Specifically for selective laser melting (SLM) processes | 15-45 µm |
Inconel 738LC-LC | Low-carbon variant, excellent for applications needing reduced carbide formation | 15-45 µm |
Inconel 738LC-HP | High-purity grade for applications requiring ultra-high strength and fatigue resistance | 10-53 µm |
These powder variants are designed for specific manufacturing techniques and applications, providing versatility to suit different industrial needs.
Specifications and Standards for Inconel 738LC Powder
When selecting a material like Inconel 738LC powder, it’s important to ensure it meets industry standards and specifications. Below is a breakdown of some of the most relevant specs:
Specification | Description | Standard |
---|---|---|
ASTM B637 | Standard specification for nickel alloy bars, forgings, and powder | ASTM International |
AMS 5391 | Specification for nickel-based alloy, investment castings | SAE International |
ISO 15156 | Guidelines for materials used in H2S-containing environments | ISO International |
AMS 5663 | Material specification for nickel alloy powder | SAE International |
DIN EN 10204 | Certificate standard for metallic products | DIN International |
ISO 9001:2015 | Quality management system standard for production | ISO International |
These specifications ensure that Inconel 738LC powder meets the highest quality standards and can be used in critical applications requiring high reliability and performance.
Advantages of Inconel 738LC Powder
Why choose Inconel 738LC powder? The following advantages make it the go-to choice for numerous industries:
- Exceptional Heat Resistance: Maintains structural integrity at high temperatures.
- Superior Oxidation and Corrosion Resistance: Performs well in environments with aggressive chemicals or extreme heat.
- High Creep and Fatigue Resistance: Long-lasting under mechanical stress, making it ideal for long-term, high-stress applications.
- Versatile in Manufacturing: Suitable for additive manufacturing, MIM, HIP, and other advanced production techniques.
Disadvantages of Inconel 738LC Powder
Like any material, Inconel 738LC does have its limitations:
- High Cost: Nickel-based superalloys are generally expensive compared to other metals.
- Difficult Machinability: Can be challenging to machine in its solid form, though powder forms offer more flexibility.
- Limited Availability: Given its specialized nature, sourcing can sometimes be challenging.
Pricing and Suppliers of Inconel 738LC Powder
Sourcing Inconel 738LC powder from reliable suppliers is crucial for maintaining high-quality standards. Here’s an overview of some well-known suppliers and typical price ranges:
Supplier | Location | Price per kg | Availability |
---|---|---|---|
Praxair Surface Technologies | USA | $600-$900 | High |
Carpenter Technology | USA | $700-$950 | High |
Höganäs | Sweden | $650-$920 | Medium |
Sandvik | Global | $700-$1000 | High |
Aubert & Duval | France | $680-$920 | Medium |
The pricing can vary depending on the powder grade, form, and specific supplier. Bulk orders or special customization can also affect pricing.
Comparison: Inconel 738LC Powder vs Other Nickel-Based Alloys
To truly understand the advantages of Inconel 738LC powder, let’s compare it to other popular nickel-based alloys:
Alloy | Temperature Resistance | Corrosion Resistance | Cost | Applications |
---|---|---|---|---|
Inconel 738LC | Excellent (up to 1050°C) | Excellent | High | Gas turbines, aerospace engines, hot gas path |
Inconel 625 | Good (up to 980°C) | Superior (chloride resistance) | Medium | Chemical plants, marine applications |
Inconel 718 | Good (up to 700°C) | Good | Medium | Aerospace, power generation |
Hastelloy X | Excellent (up to 1200°C) | Good | High | Jet engines, gas turbines |
As we can see, Inconel 738LC outperforms in terms of high-temperature resistance but comes at a higher cost compared to other nickel-based alloys.
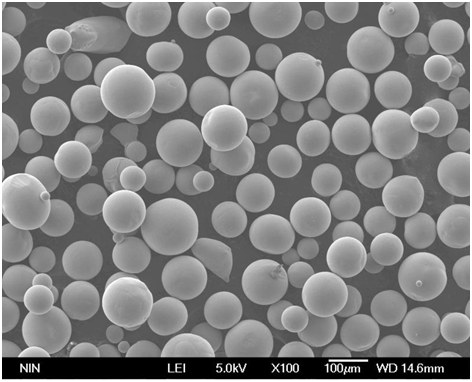
FAQs
Question | Answer |
---|---|
What is Inconel 738LC powder used for? | It is used in high-temperature applications such as turbine blades and aerospace engines. |
Is Inconel 738LC better than Inconel 625? | For high-temperature resistance, yes. However, Inconel 625 is more corrosion-resistant in chloride environments. |
Can Inconel 738LC be 3D printed? | Yes, Inconel 738LC powder is suitable for additive manufacturing processes like SLM and DMLS. |
How does Inconel 738LC resist oxidation? | The high Chromium and Aluminum content forms a protective oxide layer on the surface. |
Is Inconel 738LC expensive? | Yes, its price is higher than many other alloys due to its specialized properties and applications. |
Conclusion
Inconel 738LC powder is an exceptional material for industries requiring high-performance, durability, and resistance to extreme environments. With its unique composition, incredible characteristics, and versatility across applications like additive manufacturing, aerospace, and power generation, it’s clear why this superalloy remains a popular choice in demanding fields. Though the cost may be higher, the long-term performance and reliability of Inconel 738LC powder make it well worth the investment for critical applications. Whether you’re a manufacturer, engineer, or researcher, understanding the ins and outs of this remarkable material ensures you make informed decisions that optimize performance and longevity.