High temperature oxidation of Inconel 939 formed by LPBF
Introduction
Nickel-based super alloys are corrosion-resistant alloys designed for high temperature applications up to 1100 to 1150°C. Due to their high levels of creep resistance, vulcanization and oxidation, these alloys have been widely used in the aerospace and energy industries. They typically contain up to 10 alloying elements, including light elements such as carbon or boron, and heavy refractory elements such as Ta, W, Nb, or Re.
Inconel 939(also known as In939)is a high chromium content super alloy commonly used in turbine blades and blades. This alloy has good weld ability and sufficient strength at operating temperatures up to 950°C. Super alloys similar to In939, such as In718, In625 and Rene 220, form a Cr2O3 layer through the preferential oxidation of Cr, thereby protecting the metal from high-temperature corrosion. The formed oxide layer is usually dense and slow-growing and has a long service life at operating temperatures up to 1000°C. When used, the Cr2O3 layer is subjected to stress, especially under cyclic conditions, which can lead to spalling of the layer.
In this investigation, the oxidation characteristics of In939 parts produced by AM and CM (casting) was studied in detail after exposure at 900°C with 158h using optical microscopeand scanning electron microscopy (SEM) and energy dispersive X-ray spectroscopy (EDX).
Materials
The In939 alloysare produced by both AM (Laser powder bed fusion, LPBF) and CM (casting). The chemical composition of AM and CM In939 alloys is shown in Table 1:
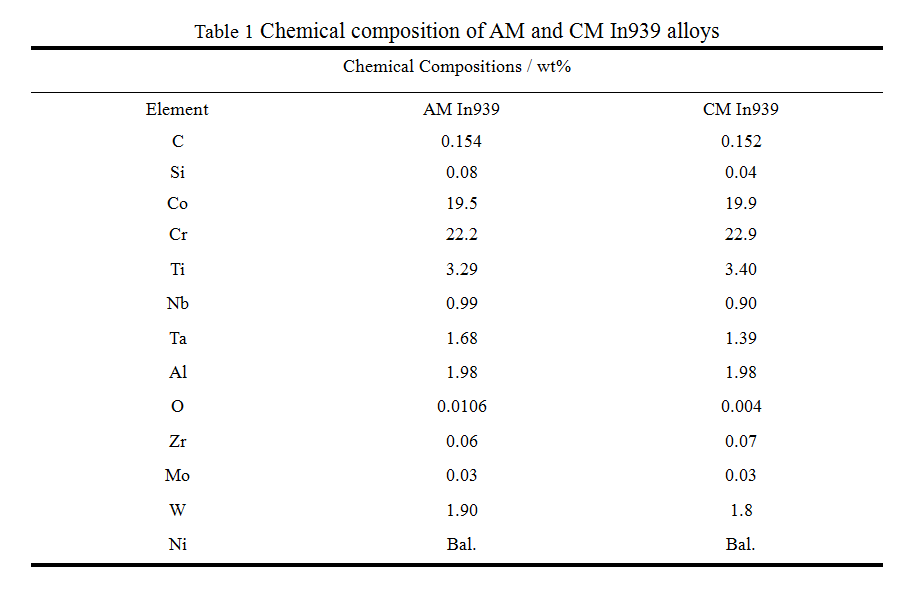
Results and discussion
Figure 1 shows optical micrograph of the etched microstructure of AM In939 with an average size of 100-120 μm.
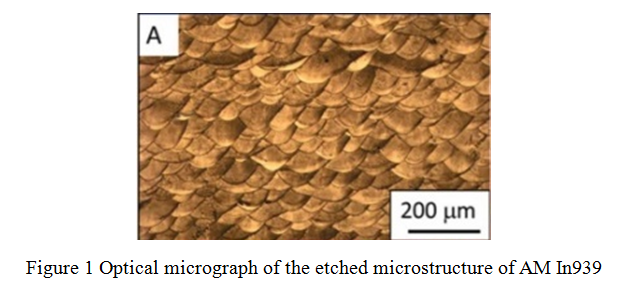
Figure 2 shows the SEM-EDX cross sections of AM-Y-direction, AM-Z-direction and CM In939 samples after oxidationat 900°C with 158h. According to the cross-sectional image, externally grown Cr2O3 layers with an average thickness of 3 μm are present on all samples. The layer is continuous and uniform, and there is no significant difference in the external growth scale between the samples in terms of phase composition and oxide layer thickness due to the microstructure anisotropy. This means that the microstructure anisotropy of AM materials does not affect the oxidation behavior under these conditions:
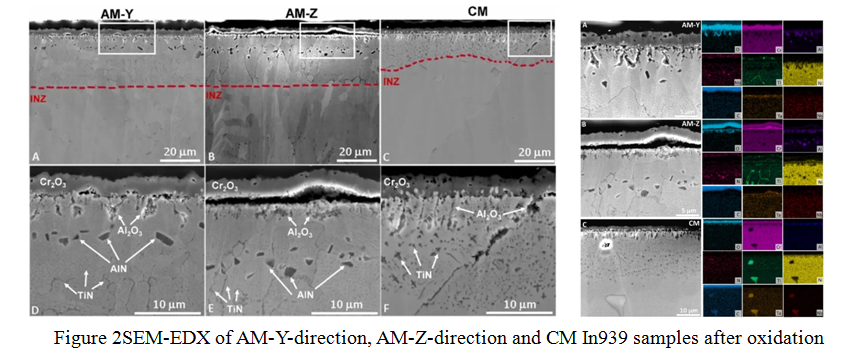
Conclusion
This study focuses on how the corrosion characteristics of In939 produced by additive manufacturing is similar to that of conventionally manufactured (CM) In939 at 900°C, independent of the direction of the oxidized surface with respect to the forming direction. Both the two materials form Cr2O3 layer as a protective oxide layer on the surface of In939.