Gas turbines are marvels of modern engineering, powering everything from electricity generation to jet engines. A critical component of these systems is the atomizing air system, which ensures efficient combustion by finely dispersing fuel into the combustion chamber. This article delves deep into the complexities of gas turbine atomizing air systems, exploring their composition, characteristics, applications, specifications, and more. Whether you’re an engineer, a student, or just an enthusiast, this guide will provide you with detailed insights into this fascinating topic.
Overview of Gas Turbine Atomizing Air System
A gas turbine atomizing air system is designed to enhance the combustion process by atomizing the fuel into fine droplets. This ensures a more efficient and complete combustion, leading to better performance, lower emissions, and improved fuel economy. The system uses compressed air to break up the fuel into tiny particles, allowing for more effective mixing with the air in the combustion chamber.
Key Functions of Atomizing Air System
- Improves Fuel Combustion: By creating a fine mist of fuel, the system ensures that the fuel burns more completely.
- Reduces Emissions: Better combustion leads to lower levels of pollutants such as NOx and CO.
- Enhances Efficiency: More complete combustion means more energy is extracted from the fuel, improving overall efficiency.
- Extends Engine Life: Efficient combustion reduces the buildup of carbon deposits, which can wear down engine components.
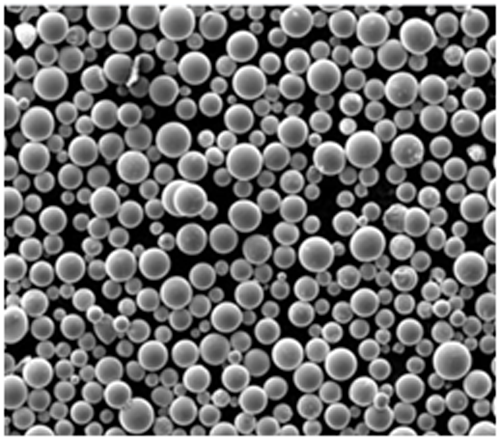
Composition of Gas Turbine Atomizing Air System
The atomizing air system is composed of several key components, each playing a vital role in the atomization process. Let’s break down the main parts:
- Air Compressor: Provides the high-pressure air necessary for atomization.
- Fuel Nozzle: The device where fuel and air mix and atomization occurs.
- Air Manifold: Distributes compressed air evenly to the fuel nozzles.
- Control Valves: Regulate the flow of air and fuel to ensure optimal mixing and combustion.
Detailed Table of Components
Component | Description | Material | Function |
---|---|---|---|
Air Compressor | Compresses air to high pressure | Stainless Steel | Provides high-pressure air for atomization |
Fuel Nozzle | Mixes air and fuel, atomizing the fuel | Inconel, Titanium | Ensures fine fuel mist for efficient combustion |
Air Manifold | Distributes air evenly to nozzles | Aluminum, Steel | Uniform air distribution |
Control Valves | Regulate air and fuel flow | Brass, Stainless | Maintains optimal air-fuel mixture |
Characteristics of Gas Turbine Atomizing Air System
Understanding the characteristics of the atomizing air system is crucial for optimizing its performance. Here are some of the key traits:
- Pressure and Flow Rates: The system operates at high pressure and flow rates to ensure effective atomization.
- Material Durability: Components are made from high-strength materials to withstand extreme temperatures and pressures.
- Precision Control: Advanced control systems regulate the air-fuel mixture with high precision.
Performance Characteristics Table
Characteristic | Description | Importance |
---|---|---|
Pressure Range | Typically between 20-100 psi | Ensures proper atomization |
Flow Rate | Varies based on engine size and design | Matches fuel supply with engine demands |
Material Strength | High-temperature and pressure-resistant | Longevity and reliability |
Control Precision | High accuracy in regulating air-fuel ratio | Optimizes combustion efficiency |
Applications of Gas Turbine Atomizing Air System
The applications of gas turbine atomizing air systems are vast, spanning across various industries. Here’s a look at where these systems are commonly used:
Application Areas
Industry | Application | Benefits |
---|---|---|
Power Generation | Gas turbine power plants | Improved efficiency, lower emissions |
Aviation | Jet engines | Better fuel economy, reduced emissions |
Oil and Gas | Offshore platforms, drilling rigs | Reliable power, efficient combustion |
Marine | Ship propulsion systems | Enhanced fuel efficiency, reduced pollution |
Industrial | Combined heat and power systems (CHP), manufacturing | Cost savings, better energy utilization |
Specifications of Gas Turbine Atomizing Air System
When it comes to specifications, different gas turbine atomizing air systems vary based on their design and intended application. Here’s a detailed look at the specifications:
Specifications Table
Specification | Details | Standard |
---|---|---|
Operating Pressure | 20-100 psi | ASME, ISO |
Air Flow Rate | Varies (e.g., 10-1000 CFM) | OEM standards |
Material | Stainless Steel, Inconel, Titanium | ASTM, SAE |
Control System | Electronic, Pneumatic | IEC, ANSI |
Nozzle Orifice Size | 0.2-1.0 mm | OEM standards |
Suppliers and Pricing Details
When sourcing components for gas turbine atomizing air systems, it’s essential to consider the suppliers and their pricing. Here’s a comparison of some key suppliers:
Suppliers and Pricing Table
Supplier | Component | Price Range | Location | Lead Time |
---|---|---|---|---|
ABC Compressors | Air Compressor | $5,000 – $20,000 | USA | 4-6 weeks |
XYZ Nozzles | Fuel Nozzle | $1,000 – $5,000 | Germany | 6-8 weeks |
LMN Manifolds | Air Manifold | $2,000 – $8,000 | China | 3-5 weeks |
DEF Controls | Control Valves | $500 – $3,000 | Japan | 2-4 weeks |
Comparing Pros and Cons of Different Systems
Different gas turbine atomizing air systems have their own set of advantages and limitations. Here’s a comparison to help you understand the pros and cons:
Advantages and Limitations Table
System Type | Advantages | Limitations |
---|---|---|
High-Pressure Systems | Better atomization, efficient combustion | Higher cost, more complex maintenance |
Low-Pressure Systems | Simpler design, lower cost | Less efficient atomization, higher emissions |
Electronic Control Systems | Precise control, better performance | Higher initial investment, complex repairs |
Pneumatic Control Systems | Simpler operation, reliable | Less precise control, can be less efficient |
Specific Metal Powder Models for Gas Turbine Atomizing Air System
Metal powders are often used in various components of gas turbine atomizing air systems due to their high strength and resistance to extreme conditions. Here are ten specific metal powder models and their descriptions:
Metal Powder Models
- Inconel 718 Powder
- Description: High-strength, corrosion-resistant nickel-chromium alloy.
- Applications: Fuel nozzles, turbine blades.
- Ti-6Al-4V Powder
- Description: Titanium alloy with excellent strength-to-weight ratio.
- Applications: Compressor blades, casings.
- Stainless Steel 316L Powder
- Description: Corrosion-resistant steel with good mechanical properties.
- Applications: Air manifolds, control valves.
- Hastelloy X Powder
- Description: Nickel-based alloy with high oxidation resistance.
- Applications: Combustion liners, turbine discs.
- Cobalt Chrome (CoCr) Powder
- Description: High wear and corrosion resistance.
- Applications: Turbine blades, combustion chambers.
- Aluminum 7075 Powder
- Description: High-strength aluminum alloy.
- Applications: Air manifolds, structural components.
- Inconel 625 Powder
- Description: Corrosion and oxidation-resistant nickel alloy.
- Applications: Exhaust systems, heat exchangers.
- Nickel Alloy 625 Powder
- Description: High strength and resistance to severe environments.
- Applications: Fuel nozzles, turbine blades.
- Tool Steel H13 Powder
- Description: High toughness and wear resistance.
- Applications: High-temperature components, nozzles.
- Maraging Steel Powder
- Description: Ultra-high strength with good toughness.
- Applications: Structural components, gears.
Comparison of Metal Powder Models
Model | Strength | Corrosion Resistance | Temperature Resistance | Applications |
---|---|---|---|---|
Inconel 718 | High | High | Very High | Fuel nozzles, turbine blades |
Ti-6Al-4V | Moderate | Moderate | High | Compressor blades, casings |
Stainless Steel 316L | Moderate | High | Moderate | Air manifolds, control valves |
Hastelloy X | High | Very High | Very High | Combustion liners, turbine discs |
CoCr | Moderate | Very High | High | Turbine blades, combustion chambers |
Aluminum 7075 | High | Low | Low | Air manifolds, structural components |
Inconel 625 | High | Very High | Very High | Exhaust systems, heat exchangers |
Nickel Alloy 625 | High | High | Very High | Fuel nozzles, turbine blades |
Tool Steel H13 | Very High | Low | High | High-temperature components, nozzles |
Maraging Steel | Very High | Moderate | Moderate | Structural components, gears |
FAQs
Q1: What is the primary purpose of an atomizing air system in gas turbines?
The primary purpose is to improve fuel combustion by breaking the fuel into fine droplets, ensuring efficient mixing with air and complete combustion.
Q2: What materials are commonly used in gas turbine atomizing air systems?
Common materials include stainless steel, Inconel, titanium, aluminum, and various high-strength alloys to withstand extreme conditions.
Q3: How does an atomizing air system reduce emissions?
By ensuring more complete combustion, the system reduces the amount of unburned fuel and decreases the production of pollutants like NOx and CO.
Q4: Can atomizing air systems be used in all types of gas turbines?
Yes, atomizing air systems are versatile and can be adapted for use in various types of gas turbines across different industries.
Q5: What are the main factors affecting the performance of an atomizing air system?
Key factors include air pressure, flow rates, the precision of control systems, and the quality of materials used in the components.
Q6: How often should maintenance be performed on an atomizing air system?
Regular maintenance is essential and should be performed based on manufacturer recommendations, typically every few months to ensure optimal performance.
Q7: What are the cost implications of installing a high-pressure atomizing air system?
High-pressure systems are generally more expensive due to their complexity and the high-quality materials required, but they offer better performance and efficiency.
Q8: Are there any environmental benefits to using atomizing air systems in gas turbines?
Yes, improved combustion efficiency leads to lower emissions of harmful pollutants, contributing to reduced environmental impact.
Q9: What advancements are being made in atomizing air systems technology?
Ongoing research focuses on improving control systems, developing new materials for higher durability, and enhancing overall efficiency and emission reductions.
Q10: How do electronic control systems compare to pneumatic control systems in atomizing air systems?
Electronic systems offer more precise control and better performance but are generally more expensive and complex compared to pneumatic systems, which are simpler and more reliable.
Conclusion
Gas turbine atomizing air systems are critical for efficient and clean combustion in various industrial applications. By understanding their components, characteristics, applications, and the specifics of different metal powders used, you can appreciate the complexity and importance of these systems. As technology advances, these systems will continue to evolve, offering even greater efficiency and lower environmental impact. Whether you’re involved in designing, maintaining, or simply learning about gas turbines, this comprehensive guide provides valuable insights into the fascinating world of atomizing air systems.