Understanding Atomized Metal Powder Production
Atomized metal powder is a finely divided form of metal particles that are produced through the atomization process. Atomization involves converting molten metal into droplets, which solidify into powder upon cooling. This method ensures a uniform particle size distribution and eliminates impurities, resulting in enhanced powder properties. The process involves the following steps:
Step | Description |
---|---|
1 | Melting: The metal is melted using methods such as induction heating or electric arc furnaces. |
2 | Atomization: The molten metal is forced through a nozzle or an atomizing gas, usually nitrogen or argon, which breaks it into droplets. |
3 | Cooling: The droplets solidify into fine particles as they travel through a cooling chamber. |
4 | Collection: The atomized powder is collected and may undergo further processing or sizing. |
Atomized metal powder offers numerous benefits, including improved flowability, compressibility, and sintering behavior, making it highly desirable for various applications.
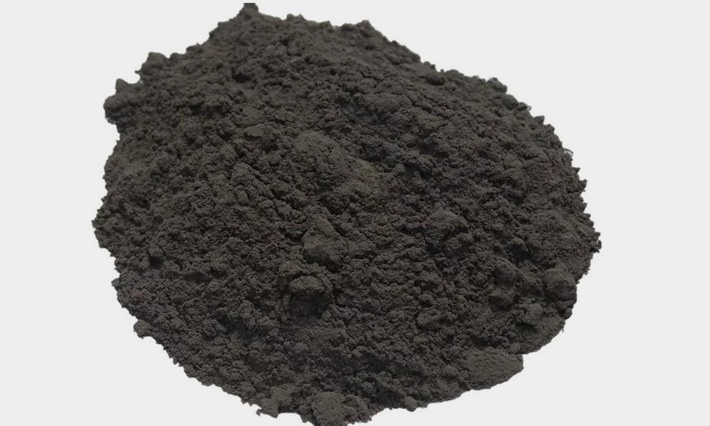
Advantages of Atomized Metal Powder in Manufacturing
Uniformity and Consistency
Atomization ensures a controlled and uniform particle size distribution, resulting in consistent material properties. This uniformity translates into products with predictable and reliable characteristics, reducing variability in the manufacturing process.
Enhanced Material Properties
The atomization process eliminates impurities and segregations that can occur in traditional metal powders. As a result, atomized metal powder exhibits improved density, strength, and mechanical properties, making it an ideal choice for applications demanding superior performance.
Reduced Porosity
The absence of impurities and the controlled solidification process contribute to reduced porosity in atomized metal powders. This characteristic leads to enhanced material integrity, minimizing the risk of defects and ensuring optimal structural strength.
Optimized Flowability and Compressibility
Atomized metal powders exhibit superior flowability and compressibility compared to traditional powders. This property simplifies manufacturing processes such as powder compaction and injection molding, resulting in more efficient production.
Tailored Particle Size and Composition
Manufacturers can fine-tune the particle size and composition of atomized metal powder to meet specific application requirements. This customization capability allows for precise control over material characteristics and performance.
High Surface Area and Reactivity
The fine particle size of atomized metal powder increases its surface area, enhancing reactivity and facilitating uniform mixing during alloying and sintering processes. This property is particularly advantageous for achieving homogenous material properties in complex manufacturing operations.
Versatility Across Industries
Atomized metal powder finds applications across a wide range of industries, including automotive, aerospace, medical, energy, and electronics. Its adaptability and superior properties make it a versatile material for various components and products.
Cost-Efficiency
Although the initial production cost of atomized metal powder may be higher than traditional powders, its uniformity and enhanced properties often lead to improved process efficiency and reduced wastage. This cost-effectiveness can offset the initial investment.
Advanced Manufacturing Techniques
Atomized metal powder is well-suited for advanced manufacturing methods such as additive manufacturing (3D printing) and powder metallurgy. Its consistent particle size and reactivity contribute to the production of intricate and precisely engineered components.
Environmental Considerations
Atomized metal powder’s efficiency in production, reduced wastage, and recyclability align with sustainable manufacturing practices, contributing to reduced environmental impact and resource conservation.
Applications of Atomized Metal Powder Across Industries
Automotive Industry
Atomized metal powders are extensively used in the automotive sector for producing high-strength components with precision. These powders contribute to the manufacturing of engine parts, transmission gears, and brake components, enhancing durability and performance while reducing weight.
Aerospace and Aviation
In the aerospace industry, atomized metal powder is employed to manufacture lightweight yet robust parts for aircraft and spacecraft. These powders contribute to fuel efficiency, structural integrity, and overall performance of critical components.
Medical and Healthcare
The medical field utilizes atomized metal powder to create biocompatible implants, surgical instruments, and dental prosthetics. The high purity and tailored properties of these powders ensure safety and optimal functionality in medical applications.
Energy Generation and Storage
Atomized metal powders play a crucial role in renewable energy technologies such as fuel cells, solar cells, and battery electrodes. Their high surface area and reactivity contribute to efficient energy conversion and storage.
Electronics and Electrical Engineering
Atomized metal powders find application in electronics for manufacturing conductive inks, pastes, and coatings. These materials are essential for producing printed circuit boards, sensors, and other electronic components.
Additive Manufacturing (3D Printing)
Atomized metal powders are a cornerstone of additive manufacturing processes, enabling the creation of complex and intricate metal parts with enhanced mechanical properties. Industries ranging from aerospace to jewelry design benefit from this technology.
Precision Engineering
The precision engineering sector utilizes atomized metal powders to produce finely detailed and intricate components for various applications, including watches, jewelry, and specialized machinery.
Powder Metallurgy
Atomized metal powders play a significant role in conventional powder metallurgy processes, producing a wide range of components such as gears, bearings, and cutting tools. Their controlled properties enhance the quality and performance of these products.
Construction and Architecture
Atomized metal powders contribute to architectural and construction applications through the production of specialized coatings, paints, and additives that enhance corrosion resistance and durability of building materials.
Defense and Military
In the defense sector, atomized metal powders are used for manufacturing components of weapons, vehicles, and protective gear. Their strength, reliability, and precision make them essential for critical defense applications.
Chemical and Catalysis
Atomized metal powders serve as catalysts in chemical reactions, enabling the production of chemicals and fuels. Their high surface area and reactivity enhance catalytic efficiency.
Environmental and Sustainable Technologies
Atomized metal powders contribute to technologies aimed at environmental protection and sustainability, including water purification, air filtration, and pollution control.
Comparing Atomized and Traditional Metal Powders
Particle Shape and Structure
Atomized Powders: Atomized metal powders typically have spherical or nearly spherical particle shapes. This consistent morphology enhances flowability, compaction, and sintering behavior, resulting in uniform and dense final products.
Traditional Powders: Traditional metal powders can have irregular, angular, or dendritic particle shapes. These shapes may hinder flowability and compaction, leading to uneven distribution during processing.
Purity and Impurities
Atomized Powders: The atomization process inherently reduces impurities and segregation, resulting in higher purity powders with fewer defects. This purity contributes to improved material properties and performance.
Traditional Powders: Traditional powder production methods may introduce impurities due to crushing, grinding, or other mechanical processes. These impurities can affect the final product’s quality.
Particle Size Distribution
Atomized Powders: Atomization allows precise control over particle size distribution, leading to a narrower and more consistent range of particle sizes. This control is crucial for achieving desired material properties.
Traditional Powders: Particle size distribution in traditional powders can be broader and less controlled, potentially leading to variations in final product characteristics.
Material Properties
Atomized Powders: Atomized metal powders often exhibit enhanced material properties, including higher density, improved mechanical strength, and better surface finish. These properties contribute to better performance in applications.
Traditional Powders: Traditional powders may have lower density, inferior mechanical properties, and less predictable performance due to variations in particle size and impurity content.
Processing Efficiency
Atomized Powders: The uniformity and controlled characteristics of atomized powders lead to improved processing efficiency. They flow more smoothly, compact more consistently, and sinter evenly, resulting in higher-quality end products.
Traditional Powders: Irregular particle shapes and wider particle size distributions in traditional powders can lead to processing challenges, such as uneven compaction and sintering.
Surface Area and Reactivity
Atomized Powders: The smaller particle size and spherical shape of atomized powders result in higher surface area and enhanced reactivity. This property is beneficial for applications such as catalysis and alloying.
Traditional Powders: Larger and irregular particle shapes in traditional powders may result in lower surface area and reduced reactivity, limiting their effectiveness in certain processes.
Application Diversity
Atomized Powders: Atomized metal powders are favored for applications requiring precise material properties and uniformity, such as aerospace components, medical implants, and additive manufacturing.
Traditional Powders: Traditional powders may find use in less demanding applications where exact material properties are not critical, such as certain bulk metal forming processes.
Impact of Particle Size on Atomized Metal Powder Applications
Surface Finish and Coating Uniformity
Fine Powders: Smaller particle sizes contribute to smoother surface finishes when atomized metal powders are used for coatings and surface treatments. The fine particles can densely pack together, creating a more uniform and refined appearance.
Coarse Powders: Larger particles may result in textured or rougher surfaces in coatings. Coarser powders can lead to distinctive surface patterns, which can be desirable in certain decorative applications.
Mechanical Strength and Structural Integrity
Fine Powders: In applications where mechanical strength is critical, such as aerospace components, finer atomized powders are often preferred. The small particle size promotes better particle bonding and densification during sintering, resulting in enhanced structural integrity.
Coarse Powders: Coarser atomized powders may be suitable for applications where structural integrity is less crucial, as they may not achieve the same level of density and strength as finer powders.
Porosity and Density
Fine Powders: Fine atomized powders tend to have lower porosity due to their ability to densely pack during processing. This property is advantageous in applications requiring minimal porosity, such as medical implants or critical mechanical parts.
Coarse Powders: Coarser powders can lead to higher porosity in sintered parts. While this can be advantageous for certain applications like filters or porous components, it may not be suitable for load-bearing or high-stress applications.
Powder Flowability and Compaction Behavior
Fine Powders: Fine atomized powders often exhibit better flowability and can compact more easily in molds or dies. This characteristic is valuable in powder metallurgy and injection molding processes.
Coarse Powders: Coarser powders might be more challenging to flow and compact, potentially requiring additional processing steps to achieve the desired shape and density.
Additive Manufacturing (3D Printing)
Fine Powders: Additive manufacturing techniques, such as 3D printing, often utilize finer atomized powders to achieve intricate and precise details in printed objects. The small particle size allows for accurate layering and complex geometries.
Coarse Powders: Coarser powders might be less suitable for fine-detail printing but could find applications in larger-scale additive manufacturing processes.
Conductivity and Electrical Properties
Fine Powders: Smaller particles can contribute to improved electrical conductivity in applications such as printed electronics or conductive inks.
Coarse Powders: Coarser powders may have lower conductivity due to reduced particle-to-particle contact, which can impact electrical performance.
Challenges and Considerations with Atomized Metal Powder Usage
Oxidation and Surface Contamination
Rapid Cooling: The atomization process involves rapid cooling of molten metal droplets, which can lead to surface oxidation. Oxidized particles may have altered properties that affect material performance and final product quality.
Surface Sensitivity: Some atomized powders are more sensitive to oxidation than others, depending on the metal composition. Protecting powders from exposure to air during handling and storage is crucial to maintain their desired properties.
Particle Agglomeration and Flowability
Fine Particle Agglomeration: Fine atomized powders can be prone to agglomeration due to strong interparticle forces. Agglomerates may lead to poor flowability, uneven distribution, and challenges during processing.
Flowability Optimization: Ensuring consistent and controlled flow characteristics requires careful design of processing equipment and, in some cases, the addition of flow-enhancing additives.
Production Costs and Economics
Atomization Equipment: Setting up and maintaining atomization equipment can involve significant capital investment. The initial production cost of atomized metal powder may be higher compared to traditional powder production methods.
Cost-Benefit Analysis: Manufacturers must perform a thorough cost-benefit analysis to determine the economic viability of using atomized metal powder in specific applications.
Safety Considerations
Inhalation Risk: Fine atomized powders pose inhalation hazards, as they can become airborne and be inhaled by workers. Inhalation of metal particles may have health implications.
Skin Contact: Direct skin contact with atomized powders may lead to skin irritation or sensitization, particularly if the powder contains toxic or reactive elements.
Protective Measures: Adequate ventilation, personal protective equipment (PPE), and proper training are essential to mitigate these risks and ensure worker safety.
Powder Handling and Storage
Moisture and Contamination: Atomized metal powders are susceptible to moisture absorption and contamination, which can affect their properties and suitability for processing.
Storage Conditions: Powders should be stored in dry and controlled environments to prevent oxidation, agglomeration, and other degradation issues.
Powder Homogeneity and Mixing
Uniform Dispersion: Achieving uniform dispersion of atomized powders in a matrix material can be challenging, particularly when creating alloys or composite materials.
Mixing Techniques: Specialized mixing techniques and equipment may be required to ensure even distribution of atomized powders in composite formulations.
Sintering Behavior and Densification
Sintering Variability: The sintering behavior of atomized powders can vary based on particle size, shape, and composition. Achieving consistent densification across a sintered part may require careful process control.
Powder Contaminants and Impurities
Trapped Gases: During atomization, gases can become trapped within powder particles, leading to porosity and affecting material properties.
Residual Solids: Residual traces of crucible or atomization nozzle material can become incorporated into atomized powders, potentially impacting material performance.
Post-Processing Treatments for Atomized Metal Powder
Sintering
Sintering is a widely used post-processing technique for atomized metal powders. It involves heating the powder particles to a controlled temperature below their melting point. During sintering, the particles bond and fuse together, leading to densification and improved mechanical properties. This treatment is crucial for achieving the desired strength, hardness, and dimensional stability in sintered components.
Alloying
Atomized metal powders offer a unique advantage for alloying due to their uniform particle size distribution and high surface reactivity. Different atomized powders can be blended to create alloys with specific compositions and properties. Alloying enhances material performance, enabling manufacturers to tailor materials for applications ranging from automotive components to aerospace structures.
Surface Treatment and Coating
Atomized metal powders can undergo surface treatments or coatings to modify their surface characteristics. Techniques like chemical or physical vapor deposition can be used to apply thin coatings that enhance properties such as corrosion resistance, wear resistance, and biocompatibility. These treatments expand the range of potential applications for atomized powders.
Size Classification
Atomized powders may undergo size classification to separate particles into different size fractions. This allows manufacturers to create powders with specific particle size distributions tailored to unique processing or performance requirements.
Cold Isostatic Pressing (CIP)
Cold isostatic pressing involves compacting atomized powders in a flexible mold under high pressure. This process improves powder density and homogeneity, enhancing the quality of the final sintered product.
Heat Treatment
Heat treatment processes, such as annealing, tempering, or quenching, can be applied to atomized powders to influence their microstructure and mechanical properties. Heat treatment can alleviate residual stresses, refine grain structures, and optimize material behavior.
Surface Modification
Atomized powders’ high surface reactivity makes them ideal candidates for surface modification techniques. Treatments like shot peening or laser surface melting can alter surface properties, improving wear resistance, fatigue strength, or thermal conductivity.
Infiltration
Infiltration involves impregnating porous sintered parts with another material, such as a metal or polymer. This process enhances the part’s density, strength, and even electrical or thermal conductivity.
Machining and Finishing
After sintering, atomized metal components may undergo machining and finishing processes to achieve precise dimensions, surface smoothness, and intricate geometries.
Quality Control and Testing
Post-processing treatments often involve quality control steps, such as microstructure analysis, mechanical testing, and non-destructive testing, to ensure that the final product meets the desired specifications and performance criteria.
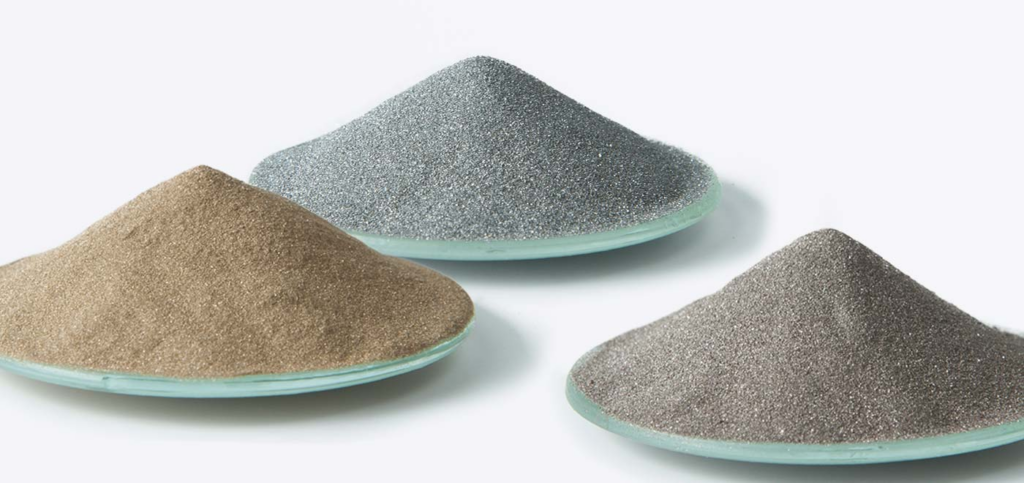
Safety Measures when Handling Atomized Metal Powder
Personal Protective Equipment (PPE):
Wear appropriate PPE, including a lab coat or coveralls, safety goggles or face shield, gloves, and a dust mask or respirator specifically designed for handling metal powders.
Ensure that PPE is properly fitted and in good condition to provide adequate protection.
Ventilation:
Work in a well-ventilated area, preferably under a fume hood or in a dedicated powder handling booth.
Use local exhaust ventilation systems to capture and remove airborne particles.
Containment:
Use airtight containers to store and transport metal powders to minimize the potential for particle dispersion.
Avoid transferring powders between containers in open air.
Minimize Dust Generation:
Handle powders gently to avoid generating dust.
Use tools and equipment that are designed to minimize dust creation.
Consider using anti-static materials and equipment to prevent powder adherence.
No Open Flames or Sparks:
Avoid working near open flames, sparks, or sources of ignition, as metal powders can be flammable or explosive under certain conditions.
Grounding:
Ground equipment and containers to prevent static electricity buildup, which could lead to sparks and ignition.
Training and Education:
Ensure that personnel handling atomized metal powders are properly trained in safe handling procedures, emergency response, and the use of protective equipment.
Emergency Procedures:
Establish clear procedures for handling spills, leaks, or other incidents involving metal powders.
Have appropriate fire extinguishing equipment nearby and ensure personnel know how to use it.
Hygiene Practices:
Wash hands and exposed skin thoroughly after handling metal powders.
Do not eat, drink, or smoke in the work area to prevent ingestion of particles.
Waste Disposal:
Dispose of waste materials containing metal powders according to local regulations and guidelines.
Risk Assessment:
Conduct a risk assessment to identify potential hazards associated with specific metal powders and processes, and implement additional safety measures as needed.
Regular Maintenance:
Maintain and inspect ventilation systems, PPE, and equipment regularly to ensure they are functioning properly.
Atomized Metal Powder and Sustainable Manufacturing
Resource Efficiency: Atomization involves converting molten metal into fine powder particles through rapid cooling. This process is inherently efficient as it minimizes material waste. Unlike traditional methods, such as casting or machining, atomization produces near-net-shape powders that require less material removal, thus conserving resources.
Energy Savings: Atomized metal powder production often requires less energy compared to other manufacturing techniques. The quick cooling process reduces the need for prolonged heating, leading to energy savings and reduced greenhouse gas emissions.
Material Utilization: Atomized powders can be tailored to specific compositions, enabling manufacturers to use alloys and materials that exhibit optimal properties for desired applications. This customization leads to enhanced product performance, reduced material consumption, and minimized environmental impact.
Lightweighting: Atomized metal powders are frequently used in the production of lightweight components, particularly in industries such as aerospace and automotive. Lightweight materials contribute to fuel efficiency, lower emissions, and reduced energy consumption over the lifecycle of products.
Additive Manufacturing (3D Printing): Atomized metal powders are widely employed in additive manufacturing processes like metal 3D printing. Additive manufacturing enables the creation of complex geometries with reduced material waste, shorter production cycles, and localized production, leading to significant sustainability benefits.
Reduced Emissions and Waste: Atomization technology helps reduce emissions of pollutants and hazardous materials compared to traditional manufacturing processes. It also minimizes waste generated during manufacturing due to its precise and controlled nature.
Recyclability: Atomized metal powders can often be recycled and reused in various applications, contributing to a circular economy. This reduces the need for raw material extraction and promotes sustainable resource management.
Improved Product Performance: Atomized powders can enhance the mechanical, thermal, and chemical properties of materials, leading to longer-lasting and more durable products. This longevity reduces the need for frequent replacements, further minimizing resource consumption.
Localized Production: Atomized powders enable localized production of components, reducing the need for extensive transportation and associated carbon emissions. This is particularly relevant in industries where customized or small-batch production is required.
Innovation and Design Flexibility: The versatility of atomized powders allows for the development of innovative designs and products that optimize performance while considering sustainability aspects.
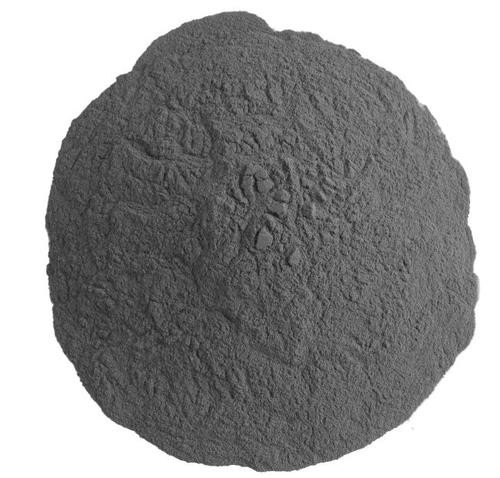
Table Summary
Step | Title |
---|---|
2 | Atomized Metal Powder Production |
3 | Advantages of Atomized Metal Powder in Manufacturing |
4 | Applications of Atomized Metal Powder Across Industries |
5 | Comparing Atomized and Traditional Metal Powders |
6 | Impact of Particle Size on Atomized Metal Powder |
7 | Challenges and Considerations with Atomized Metal Powder |
8 |
FAQ about Atomized Metal Powder
1. What is atomized metal powder?
Atomized metal powder is a finely divided form of metal particles produced through the atomization process, where molten metal is converted into droplets that solidify into powder upon cooling.
2. How is atomized metal powder produced?
Atomized metal powder is produced through a multi-step process involving melting the metal, atomizing it into droplets using a gas, cooling the droplets, and collecting the resulting powder.
3. What are the advantages of using atomized metal powder in manufacturing?
Atomized metal powder offers benefits such as uniformity, enhanced properties, reduced porosity, cost savings, and versatility, making it ideal for various manufacturing applications.
4. What industries utilize atomized metal powder?
Atomized metal powder finds applications in industries like automotive, aerospace, medical, energy, and additive manufacturing, due to its superior properties and versatility.
5. What are the differences between atomized and traditional metal powders?
Atomized metal powders have spherical particles, higher purity, controlled particle size distribution, and improved performance compared to traditional powders.