Introduction
Effect of adding Mo on laser cladding of high entropy alloy
The laser cladding technology has the advantages of short maintenance cycle, low costand is highly practical. The superior design flexibility of high-entropy alloys, combined with the convenience of LC technology, has great application potential. The effect of Mo addition in laser cladding on the formation characteristics and metallurgical process of(FeCoNiCr)-Mo high entropy alloy coating was investigated.
This studyfocuses on FeCoNiCr HEA, which is of great interest in the aerospace, transportation and marine engineering fields, to investigate the feasibility of LC HEAs coatings. In order to meet the requirements of laser utilization efficiency and corrosion resistance, Mo element is introduced into FeCoNiCr HEA alloy.
The addition of Mo element has the advantages of higher melting point and increased energy absorption in the LC process, which has the potential to improve the efficiency of laser utilization. In addition, according to the existing literature, Mo addition can improve the corrosion resistance of high-entropy alloys.
Materials and methods
1.4091 duplex stainless steel (Table 1) is the base material. Prior to the experiment, the substrate surface was cleaned by ultrasonic waves in an alcohol solution. (FeCoNiCr)-Mohigh entropy alloy (Table 2) was prepared by gas atomizing using pure metals of cobalt, chromium, iron, nickel and molybdenum (minimum content 99.9 wt%).

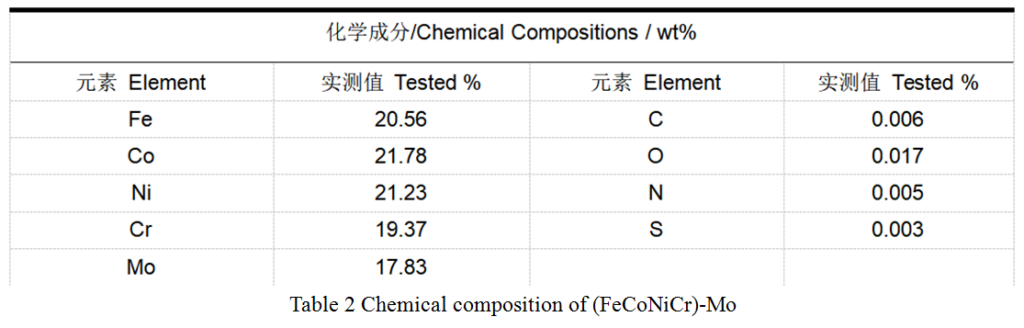
Results and discussion
Figure 1 depicts the comparison of macroscopic morphology and dimensional characteristics of LC FeCoNiCr (its chemical composition in Table 3) and (FeCoNiCr)-Mo coating. The interface of (FeCoNiCr)-Mo coating between LC coating and substrate is clear and obvious, indicating strong metallurgical bonding. The addition of Mo will definitely affect the molding quality of (FeCoNiCr)-Mo HEA coating. As shown in Figure 1a, the forming quality of FeCoNiCr LC coating is poor without the addition of Mo. When Mo is added, the (FeCoNiCr)-Mo LC coating is more complete in appearance and more visually intuitive, as shown in Figure 1b.
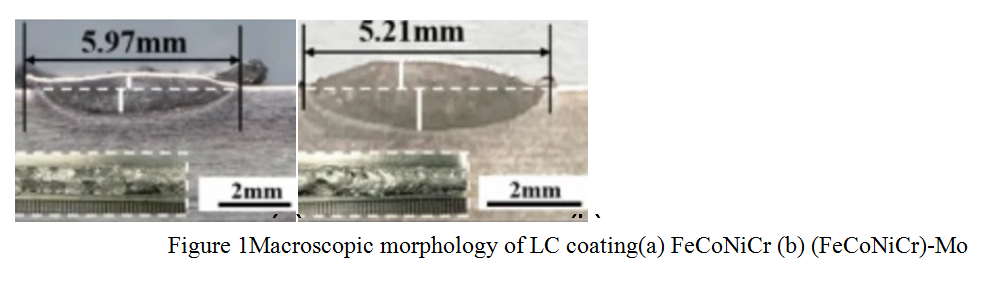

The metallographic structure of FeCoNiCr and (FeCoNiCr)-Mo coating is shown in Figure 2. The LC coating is mainly composed of columnar dendrites and equiaxial dendrites.The top region of the LC coating exhibits an irregular orientation. In the middle area of the coating, away from the water interface and the substrate, columnar crystal regions with dense tissue are formed. At the bottom of the coating area, the supercooling temperature promotes the preferential growth of the columnar crystals:
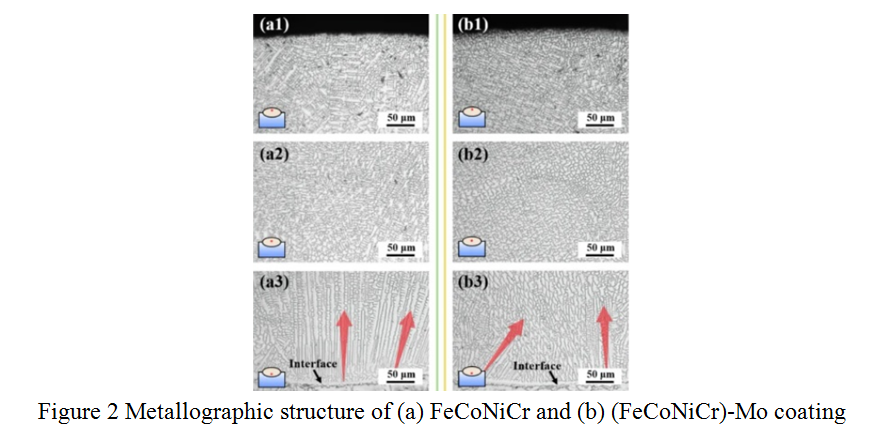
Table 4 lists the corrosion potential (Ecorr), corrosion current density (Icorr), critical corrosion potential (Epit), and passivation potential (ΔEpit = EPit-Ecorr) for each coating.The passivation zone of (FeCoNiCr)-Mo LC coating is the wider, while the passivation zone of FeCoNiCr is the narrower, which indicates that the introduction of Mo element effectively improves corrosion resistance.
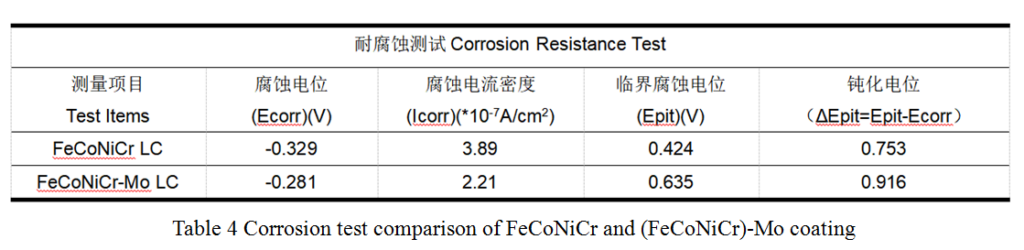
Conclusion
The effects of molybdenumin HEA FeCoNiCr alloy on the forming, microstructure and corrosion properties of LC coating were studied. It is concluded that the adding of molybdenum on gas atomized FeCoNiCr powder improved the metallurgical bonding and its corrosion resistance of LC coating of HEA FeCoNiCr alloy.