Copper, a metal cherished for millennia for its remarkable electrical conductivity and malleability, takes on a whole new dimension in the realm of copper based alloy powders. These finely ground metallic particles, often invisible to the naked eye, are revolutionizing various industries with their unique properties and ever-expanding applications. Buckle up, because we’re diving deep into the fascinating world of copper based alloy powders!
Characteristics of Copper Based Alloy Powders
Imagine copper, the quintessential conductor, miniaturized into a powder form. That’s essentially what copper based alloy powders are. But here’s the twist: By introducing other elements like tin, zinc, or nickel, we unlock a whole spectrum of properties beyond pure copper.
Key characteristics to consider:
- Composition: The magic lies in the specific mix. Copper forms the base, but the addition of other elements like tin (bronze), zinc (brass), or nickel (cupronickel) dramatically alters the properties. Think of it like a recipe – a dash of tin adds strength, a sprinkle of zinc enhances machinability, and a pinch of nickel boosts corrosion resistance.
- Particle size and morphology: The size and shape of the powder particles significantly impact the final product. Finer powders, measured in microns, create smoother surfaces after processes like 3D printing, while coarser particles might be used for applications like friction welding. Imagine building with tiny Lego bricks versus chunky building blocks – the finer the powder, the more intricate the final form can be.
- Flowability: Just like pouring sand versus rocks, the ease with which the powder flows is crucial for various manufacturing techniques. Powders with good flowability are ideal for processes like metal injection molding (MIM), where the powder needs to move freely to fill intricate molds.
A diverse range of copper based alloy powders, each with a unique combination of:
- Electrical conductivity: While generally lower than pure copper, some copper alloys like copper-tin (bronze) still offer excellent conductivity, making them suitable for electrical components.
- Strength and wear resistance: The addition of certain elements like tin or nickel significantly boosts the strength and wear resistance of copper. Imagine a copper pot – soft and easily dented. Now, add some tin, and you’ve got a bronze frying pan, tough enough to handle your toughest culinary creations.
- Corrosion resistance: Certain copper alloys, like copper-nickel, exhibit superior resistance to corrosion, making them ideal for marine applications or environments with harsh chemicals. Think of a shiny copper penny turning green with age. Now, picture a gleaming nickel, standing strong against the elements.
- Machinability: The ease with which the powder can be shaped is crucial. For instance, brass powders offer excellent machinability, making them perfect for intricate components requiring precise shaping.
By understanding these characteristics, manufacturers can select the perfect copper based alloy powder for their specific needs.
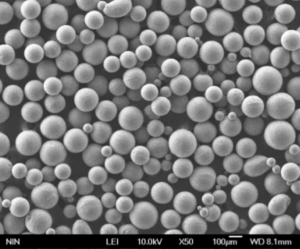
The Manufacturing Method of Copper Based Alloy Powders
How do these tiny metallic marvels come to be? There are several methods for producing copper based alloy powders, each with its own advantages and applications:
- Atomization: This method involves molten metal being disintegrated into fine droplets using high-pressure gas or water jets. Imagine a molten metal firework exploding into a cloud of tiny metallic droplets that solidify into a fine powder. This method is suitable for producing a wide range of powder sizes and compositions.
- Electrolysis: In this process, an electric current is used to dissolve the metal alloy into an electrolyte solution. The metal ions are then deposited as a fine powder on a cathode. Think of a metallic battery, where the copper alloy is broken down and reformed into a new structure – the powder. This method offers high purity and good control over particle size.
- Chemical reduction: Here, a chemical reaction is used to convert a metal compound into a powder form. Imagine a complex chemical handshake between different compounds, resulting in the formation of the desired copper based alloy powder. This method is suitable for producing specific alloys with unique properties.
The choice of manufacturing method depends on factors like the desired powder characteristics, production volume, and cost.
Applications of Copper Based Alloy Powders
Copper based alloy powders are revolutionizing various industries with their versatility and unique properties. Here are some key application areas:
- Additive Manufacturing (3D Printing): Copper based alloy powders are opening doors for 3D printing of complex metallic components. Imagine printing a intricate heat sink or a customized electrical connector directly from a digital file. Compared to traditional subtractive manufacturing techniques (think milling or machining), 3D printing offers greater design freedom and reduced waste.
- Metal Injection Molding (MIM) (continued): Imagine a mold being filled with copper based alloy powder mixed with a binder, and then shaped under high pressure. Once the shape is formed, the binder is removed, leaving behind a complex metallic part. MIM is ideal for mass-producing small, intricate components with excellent dimensional accuracy and surface finish. Compared to traditional casting techniques, MIM offers higher production volumes and tighter tolerances.
- Friction Welding: Copper based alloy powders are finding increasing use in friction welding. In this process, the powder is used as an intermediate layer between two components. Friction and heat cause the powder to melt and fuse the components together. Think of using tiny copper particles like metallic glue to create strong, permanent welds. Friction welding offers several advantages over traditional welding techniques, such as minimal heat distortion and the ability to join dissimilar materials.
- Electrical Components: Due to their good electrical conductivity and ability to be shaped into intricate forms, copper based alloy powders are used in various electrical components. Imagine tiny copper particles forming the intricate pathways for electricity to flow. Examples include electrical connectors, heat sinks for managing thermal dissipation in electronic devices, and even components in high-performance transformers. Here, copper-tin (bronze) and copper-silver alloys are popular choices due to their balance of conductivity and other properties.
- Brush Industry: Copper based alloy powders are used in the production of industrial brushes. The specific alloy chosen depends on the desired properties. For instance, copper-tin (bronze) bristles offer good electrical conductivity and spark resistance, making them ideal for use in hazardous environments. On the other hand, copper-zinc (brass) bristles provide a good balance of stiffness and conductivity, suitable for general cleaning applications.
- Bearings: Copper based alloy powders are finding their way into the world of bearings. By incorporating lubricating elements into the powder mix, manufacturers can create self-lubricating bearings. Imagine tiny copper particles embedded with lubricant, reducing friction and wear. This eliminates the need for external lubrication, reducing maintenance costs and improving performance in harsh environments.
These are just a few examples of the ever-expanding applications of copper based alloy powders. As technology advances and new powder production methods emerge, we can expect even more innovative uses for these metallic marvels in the years to come.
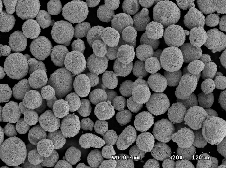
Considerations When Choosing Copper Based Alloy Powders
With such a diverse range of copper based alloy powders available, selecting the right one for your application is crucial. Here are some key factors to consider:
- Desired Properties: What are the essential properties you need? Is it high electrical conductivity, exceptional strength, or superior corrosion resistance? Understanding your priorities will help narrow down your choices.
- Manufacturing Technique: The chosen manufacturing method (3D printing, MIM, etc.) might influence the ideal powder characteristics. For instance, 3D printing might favor finer powders for smooth finishes, while MIM might work well with slightly coarser particles.
- Cost: Copper based alloy powders can vary significantly in cost depending on the composition, manufacturing method, and particle size. Finding the right balance between cost and desired properties is essential.
- Availability: Not all copper based alloy powders are readily available. Some exotic compositions or very fine particle sizes might require special orders or lead times.
Consulting with a qualified supplier who understands your specific needs and the intricacies of copper based alloy powders is highly recommended. They can guide you towards the optimal powder choice for your application.
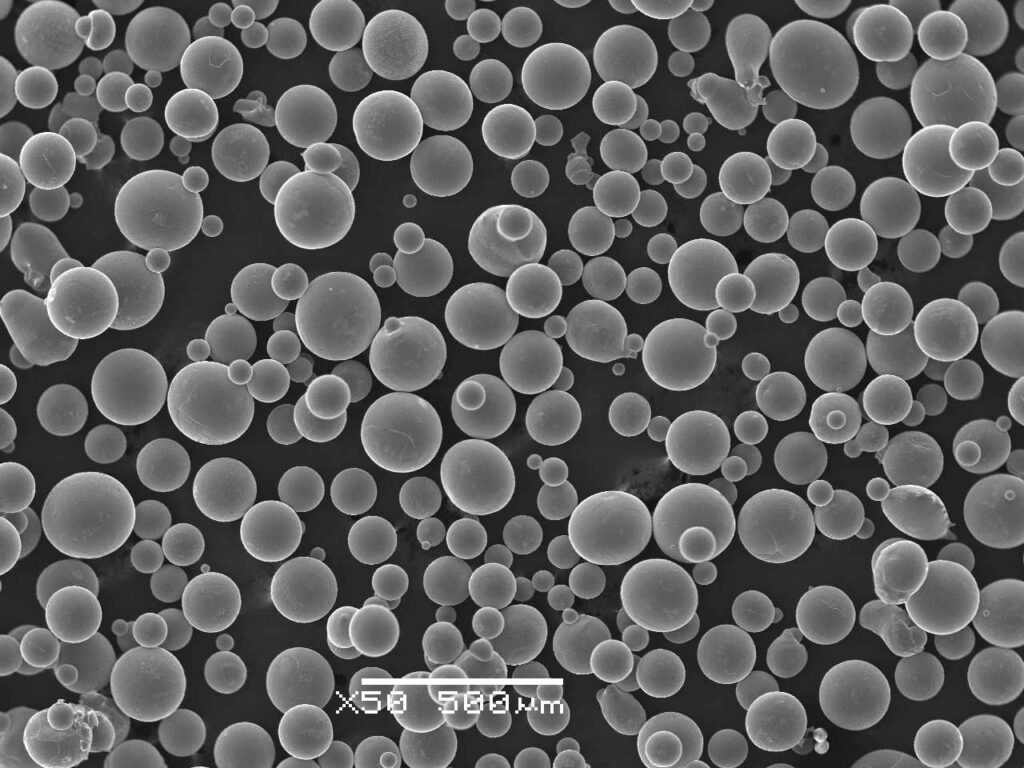
FAQ
Here are some frequently asked questions regarding copper based alloy powders, answered in a clear and concise format:
Question | Answer |
---|---|
What are the advantages of using copper based alloy powders compared to traditional solid copper? | Copper based alloy powders offer several advantages: greater design freedom with 3D printing, ability to create intricate near-net-shape parts with MIM, suitability for applications requiring specific properties like high strength or corrosion resistance. |
What are some disadvantages of using copper based alloy powders? | Some potential drawbacks include: higher cost compared to bulk copper, limitations in available powder compositions or particle sizes, the need for specialized manufacturing techniques and equipment. |
Are copper based alloy powders safe to handle? | Generally, copper based alloy powders are not hazardous in their raw form. However, some alloys might contain elements with specific safety considerations. Always consult the safety data sheet (SDS) for the specific powder you are using and follow recommended handling procedures. |
What is the future outlook for copper based alloy powders? | The future of copper based alloy powders is bright! As technology advances, we can expect to see even finer powders, new and innovative compositions, and more efficient manufacturing methods. |