1. Introduction
Titanium alloy 3D printing is an advanced manufacturing process that utilizes titanium alloys to create three-dimensional objects. This innovative technique has gained significant attention in recent years due to its numerous advantages and potential applications. In this article, we will explore the world of titanium alloy 3D printing, its applications, advancements, challenges, and future trends.
2. Applications of Titanium Alloy 3D Printing
Titanium alloy 3D printing finds applications in various industries, owing to the unique properties of titanium and the design freedom offered by 3D printing technology.
- Aerospace industry: The aerospace industry has embraced titanium alloy 3D printing for the production of lightweight yet durable components for aircraft and spacecraft. The ability to create complex geometries and optimize part designs allows for improved fuel efficiency, reduced weight, and enhanced performance.
- Medical industry: In the medical field, titanium alloy 3D printing has revolutionized the manufacturing of implants and prosthetics. The biocompatibility, corrosion resistance, and mechanical strength of titanium alloys make them ideal for applications such as dental implants, orthopedic implants, and customized medical devices.
- Automotive industry: The automotive industry is leveraging titanium alloy 3D printing to develop high-performance parts that improve vehicle efficiency, reduce weight, and enhance overall performance. Components such as engine parts, exhaust systems, and suspension parts can benefit from the lightweight and strong nature of titanium alloys.
- Industrial manufacturing: Titanium alloy 3D printing has also found applications in industrial manufacturing, where it enables the production of complex and customized parts with reduced lead times. This technology offers manufacturers the flexibility to create prototypes, jigs, and fixtures, optimizing production processes and reducing costs.
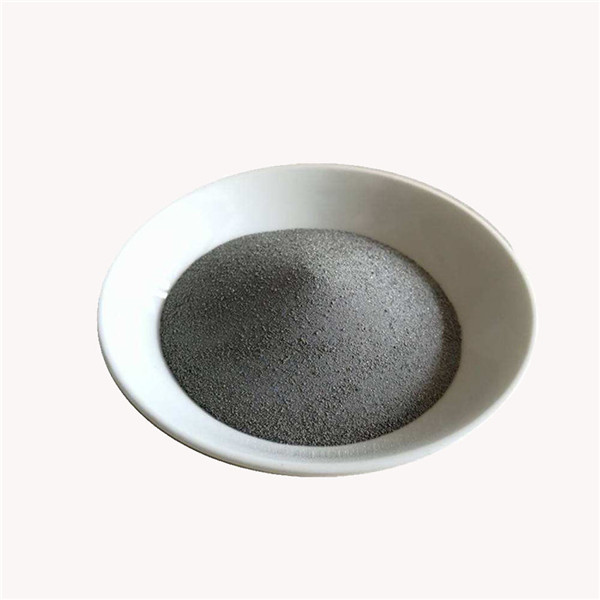
3. Advancements in Titanium Alloy 3D Printing
Over the years, titanium alloy 3D printing has witnessed significant advancements, leading to improved capabilities and enhanced performance.
- Improved printing techniques: New printing techniques, such as selective laser melting (SLM) and electron beam melting (EBM), have emerged, allowing for more precise and efficient production of titanium alloy parts. These techniques offer greater control over the printing process, resulting in improved part quality and reduced defects.
- Enhanced material properties: Researchers and engineers have been continuously working on developing new titanium alloys with improved material properties specifically tailored for 3D printing. These alloys exhibit increased strength, better heat resistance, and enhanced corrosion resistance, making them suitable for demanding applications.
- Increased production speed: Advancements in printing technology, such as faster scanning speeds and optimized laser parameters, have led to significant improvements in production speed. This allows for quicker manufacturing of titanium alloy parts, reducing lead times and increasing overall productivity.
- Cost reduction: As the technology matures and becomes more widely adopted, the cost of titanium alloy 3D printing has been decreasing. This is due to advancements in material availability, improved printing efficiency, and economies of scale. The reduction in production costs makes titanium alloy 3D printing more accessible to a broader range of industries and applications.
4. Challenges and Limitations of Titanium Alloy 3D Printing
While titanium alloy 3D printing holds immense promise, it also faces certain challenges and limitations that need to be addressed.
- High production costs: Currently, titanium alloys are more expensive than traditional manufacturing materials. The high cost of raw materials, coupled with the complex printing process and post-processing requirements, contributes to the overall production cost. However, ongoing research and developments are expected to reduce costs in the future.
- Limited material availability: Compared to other metals, the availability of titanium alloys for 3D printing is relatively limited. This can pose challenges in terms of material sourcing and lead to increased costs. However, as the demand for titanium alloy 3D printing grows, the availability of suitable materials is expected to improve.
- Post-processing requirements: After the printing process, titanium alloy parts often require extensive post-processing to achieve the desired surface finish and mechanical properties. This includes removing support structures, heat treatment, and surface polishing. These additional steps add to the production time and cost, but ongoing research aims to streamline and automate post-processing procedures.
- Design limitations: Despite the design freedom offered by 3D printing, there are still certain design limitations when it comes to titanium alloy parts. Factors such as overhangs, unsupported structures, and heat dissipation need to be carefully considered during the design phase. Design optimization and software advancements can help overcome some of these limitations.
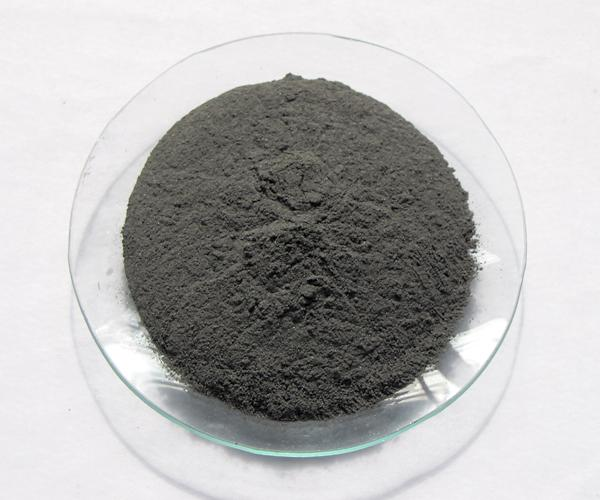
5. Future Trends and Innovations in Titanium Alloy 3D Printing
The future of titanium alloy 3D printing looks promising, with several trends and innovations on the horizon.
- Development of new titanium alloys: Researchers continue to explore and develop new titanium alloys specifically tailored for 3D printing. These alloys aim to further enhance the material properties, printability, and cost-effectiveness, opening doors to a wider range of applications.
- Integration with other manufacturing technologies: The integration of titanium alloy 3D printing with other manufacturing technologies, such as CNC machining and post-processing techniques, is expected to increase efficiency and expand the capabilities of additive manufacturing. This hybrid approach will enable the production of complex, high-quality parts with improved accuracy and surface finish.
- Increased adoption in consumer products: As the technology becomes more accessible and cost-effective, we can expect to see increased adoption of titanium alloy 3D printing in consumer products. This includes items such as jewelry, fashion accessories, and personalized consumer goods. The ability to create customized, one-of-a-kind products will cater to the growing demand for unique and personalized items.
- Customization and personalization: With titanium alloy 3D printing, customization and personalization of products become easier and more viable. From tailored medical implants to custom-fit automotive parts, the technology allows for the creation of products that perfectly match individual requirements, leading to improved functionality and user satisfaction.
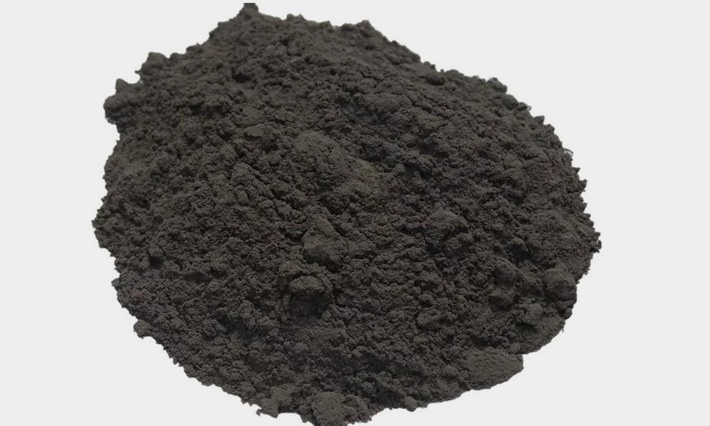
6. Conclusion
Titanium alloy 3D printing is revolutionizing the manufacturing industry, offering numerous advantages and possibilities across various sectors. The ability to create complex geometries, optimize designs, and leverage the exceptional properties of titanium alloys makes this technology a game-changer. While there are challenges to overcome, ongoing research and advancements are paving the way for cost reductions, improved material availability, and streamlined post-processing techniques.
As we look to the future, the development of new titanium alloys specifically designed for 3D printing holds great potential. These alloys will further enhance the material properties, printability, and cost-effectiveness of titanium alloy 3D printing. Integration with other manufacturing technologies, such as CNC machining, will enhance the overall efficiency and capabilities of additive manufacturing.
We can anticipate an increased adoption of titanium alloy 3D printing in consumer products, as the technology becomes more accessible and cost-effective. Customization and personalization will become key drivers, allowing individuals to obtain tailored products that meet their specific needs and preferences.
In conclusion, titanium alloy 3D printing is a groundbreaking technology that is transforming the manufacturing landscape. Its applications in industries such as aerospace, medical, automotive, and industrial manufacturing are revolutionizing the way we design and produce complex parts. With ongoing advancements and innovations, the future of titanium alloy 3D printing looks promising, offering endless possibilities for customization, improved efficiency, and cost-effectiveness.
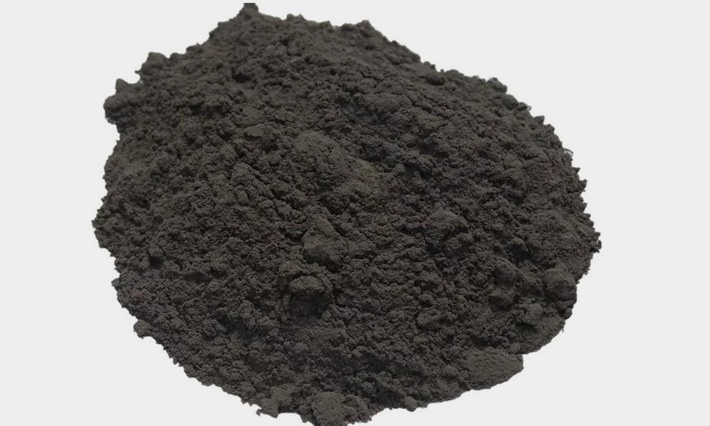
7. FAQs
- What is titanium alloy 3D printing? Titanium alloy 3D printing is an advanced manufacturing process that utilizes titanium alloys to create three-dimensional objects. It involves the layer-by-layer deposition of titanium alloy powder, which is selectively melted using laser or electron beams.
- What are the advantages of using titanium alloy in 3D printing? Titanium alloys offer several advantages in 3D printing, including high strength-to-weight ratio, excellent corrosion resistance, biocompatibility, and the ability to create complex geometries and customized designs.
- What industries benefit from titanium alloy 3D printing? Titanium alloy 3D printing finds applications in industries such as aerospace, medical, automotive, and industrial manufacturing, where the unique properties of titanium alloys and the design freedom of 3D printing are highly advantageous.
- What are the challenges of titanium alloy 3D printing? Some challenges of titanium alloy 3D printing include high production costs, limited material availability, post-processing requirements, and design limitations. However, ongoing research and developments are addressing these challenges.
- What can we expect in the future of titanium alloy 3D printing? In the future, we can expect the development of new titanium alloys, integration with other manufacturing technologies, increased adoption in consumer products, and a focus on customization and personalization to drive the advancements in titanium alloy 3D printing.
Frequently Asked Questions (Supplemental)
1) What powder specifications are ideal for titanium alloy 3D printing?
- For LPBF/SLM, use spherical Ti‑6Al‑4V or Ti‑6Al‑4V ELI powder with D10–D90 ≈ 15–45 μm, low satellite content, Hall flow <20 s/50 g, apparent density ≥2.2 g/cm³, and low interstitials (O, N, H) per grade. For EBM, slightly coarser PSD (45–105 μm) is common.
2) How do LPBF and EBM differ for titanium alloys?
- LPBF yields finer surface finish and higher detail; requires low chamber O2 (≤100–300 ppm). EBM runs at elevated temperatures in vacuum, reducing residual stress and support needs but producing rougher surfaces. Both can meet aerospace/medical requirements after post‑processing.
3) What post‑processing is typical for titanium alloy 3D printing?
- Stress relief or anneal (per AMS 2801/2802 practice), HIP to close porosity and improve fatigue, support removal, machining/EDM, surface finishing (grit blasting, polishing, electropolishing), and for medical parts, cleaning and validation per ISO 10993.
4) How does powder reuse affect quality?
- Controlled reuse with sieving and blend‑back is feasible if PSD, chemistry (O/N/H), flow, and morphology are monitored. Set reuse limits by property drift and in‑situ quality metrics; many operations qualify 5–10 cycles before full refresh.
5) Which titanium alloys are most used and why?
- Ti‑6Al‑4V (Grade 5) and Ti‑6Al‑4V ELI (Grade 23) dominate due to strength‑to‑weight, weldability, and biocompatibility. Beta alloys (e.g., Ti‑5553) and Ti‑6Al‑2Sn‑4Zr‑6Mo appear in high‑temperature or fatigue‑critical aerospace parts, often with tighter process control.
2025 Industry Trends and Data
- Qualification at scale: Digital powder passports and AI‑assisted in‑situ monitoring are increasingly required in aerospace and medical RFQs for titanium alloy 3D printing.
- Throughput gains: Multi‑laser LPBF, scan path optimization, and improved gas flow cut build times 15–30% vs. 2023 for Ti‑6Al‑4V.
- Fatigue performance: HIP plus optimized surface finishing delivers wrought‑like HCF/LCF on standardized coupons; shot peen or chemical milling used to reduce surface‑initiated cracks.
- Sustainability: Closed‑loop argon recirculation and expanded powder reuse lower cost and environmental footprint; more suppliers report recycled content and EPDs.
- Dental/ortho growth: Patient‑specific implants and porous lattice structures scale with streamlined validation workflows.
KPI (Titanium Alloy 3D Printing), 2025 | 2023 Baseline | 2025 Typical/Target | Why it matters | Sources/Notes |
---|---|---|---|---|
LPBF Ti‑6Al‑4V relative density (post‑HIP) | 99.6–99.8% | 99.8–99.95% | Fatigue, leak‑tightness | OEM/peer‑reviewed data |
Chamber oxygen (LPBF, ppm) | ≤500 | 100–300 | Oxidation, alpha‑case | Machine vendor guidance |
Surface roughness upskin (Ra, μm) | 8–15 | 5–10 (contouring) | Fatigue initiation | Vendor app notes |
Build rate improvement (multi‑laser) | — | +15–30% | Productivity | AMUG/Formnext 2024–2025 |
Powder reuse (qualified cycles) | 4–6 | 6–10 | Cost, sustainability | Plant case studies |
AI in‑situ anomaly detection | Pilot | Common on new systems | QA efficiency | OEM releases |
Dental/implant AM adoption | Growing | Mainstream | Personalization, fit | Market briefs |
Authoritative resources:
- ISO/ASTM 52907 (metal powder characterization) and 52904 (LPBF of metals): https://www.iso.org
- ASTM F2924 (Ti‑6Al‑4V by PBF), ASTM F3001 (Ti‑6Al‑4V ELI), ASTM F3302 (AM process control): https://www.astm.org
- AMS 2801/2802 (heat treatment/cleanliness guidance for titanium), AMS 4999/4998 (powder specs): https://www.sae.org
- NIST AM Bench datasets: https://www.nist.gov/ambench
- ASM Handbook, Additive Manufacturing and Titanium Alloys: https://dl.asminternational.org
Latest Research Cases
Case Study 1: HIP‑Enhanced LPBF Ti‑6Al‑4V Lattice Implants with Improved Fatigue (2025)
- Background: A medical device OEM sought higher fatigue life and consistent pore architecture for acetabular cups.
- Solution: Employed spherical Grade 23 powder (15–45 μm, O ≤0.13 wt%), in‑situ layer imaging with AI scoring, optimized gas flow, HIP at 920°C/100 MPa/2 h, and electropolishing of articulating surfaces.
- Results: CT density 99.90%; push‑out strength +20% vs. 2023 baseline; HCF endurance limit +18%; first‑pass yield +8%; pore size CV reduced from 12% to 6%.
Case Study 2: EBM Ti‑6Al‑4V Brackets with Reduced Distortion via Thermal Modeling (2024)
- Background: An aerospace Tier‑1 faced distortion and support overuse on thin‑wall brackets.
- Solution: Introduced thermo‑mechanical simulation to tune beam strategies and support volumes; validated with in‑situ thermography; applied targeted stress‑relief.
- Results: Distortion −35%; support mass −28%; machining time −22%; coupon tensile met AMS specs with Cpk ≥1.33.
Expert Opinions
- Dr. Todd Palmer, Professor of Materials Science, Penn State
- Viewpoint: “For titanium alloy 3D printing, controlling oxygen and microstructure via HIP and heat treatment is pivotal to achieving wrought‑like fatigue performance.”
- Prof. Ian Gibson, Additive Manufacturing Scholar, University of Texas at Arlington
- Viewpoint: “Technology selection—LPBF for fine features versus EBM for stress‑tolerant builds—should be driven by downstream finishing and qualification pathways.”
- Dr. Martina Zimmermann, Head of Additive Materials, Fraunhofer IWM
- Viewpoint: “AI‑assisted in‑situ monitoring coupled with digital powder passports is becoming a de facto requirement for regulated aerospace and medical titanium parts.”
Affiliation links:
- Penn State CIMP-3D: https://www.cimp-3d.psu.edu
- University of Texas at Arlington: https://www.uta.edu
- Fraunhofer IWM: https://www.iwm.fraunhofer.de
Practical Tools/Resources
- Standards: ASTM F2924, F3001, F3302; ISO/ASTM 52904, 52907
- Design/simulation: nTopology (lattice/poro design), Ansys Additive and Simufact Additive (distortion/scan strategy), Autodesk Netfabb
- QA/monitoring: Melt‑pool imaging and layer cameras (EOS, SLM Solutions, Renishaw); CT scanning; LECO O/N/H (https://www.leco.com)
- Medical compliance: ISO 10993 biocompatibility; FDA AM guidance documents for patient‑specific implants
- Data/benchmarks: NIST AM Bench; Senvol Database (https://senvol.com/database); MatWeb for Ti‑6Al‑4V properties (https://www.matweb.com)
Last updated: 2025-08-22
Changelog: Added 5 supplemental FAQs; introduced 2025 trends with KPI table and references; provided two case studies (HIP‑enhanced LPBF implants and EBM brackets via thermal modeling); included expert viewpoints with affiliations; compiled practical standards, simulation, QA, and regulatory resources for titanium alloy 3D printing.
Next review date & triggers: 2026-02-01 or earlier if ASTM/ISO standards change, major OEMs publish new oxygen/reuse limits or AI in‑situ acceptance criteria, or new clinical/aerospace fatigue datasets for AM Ti‑6Al‑4V are released.