Aluminum based alloy powders are revolutionizing the manufacturing landscape, offering a versatile and innovative approach to creating complex, lightweight, and high-performance components. Imagine having a metallic building block, akin to grains of sand, but engineered to possess specific properties that can be shaped and fused together to create intricate objects. That’s the magic of aluminum based alloy powders!
the Composition of Aluminum based alloy powders
Aluminum itself is a remarkable metal, prized for its lightness, strength, and excellent conductivity. But when alloyed with other elements like silicon, magnesium, copper, and lithium, its properties can be tailored to specific needs. Aluminum based alloy powders capture this essence, offering a spectrum of material compositions designed to meet diverse engineering challenges.
Here’s a breakdown of some prominent aluminum based alloy powder types and their key elements:
Alloy Powder Type | Key Alloying Elements | Description |
---|---|---|
AlSi10Mg (LM6) | Silicon (10%), Magnesium (0.3%) | A workhorse material, AlSi10Mg offers a good balance of strength, ductility, and castability. Its high silicon content enhances fluidity during printing, making it ideal for intricate geometries. |
AlSi7Mg0.3 (A356) | Silicon (7%), Magnesium (0.3%) | Another popular choice, AlSi7Mg0.3 boasts good mechanical properties and excellent castability. Compared to AlSi10Mg, it offers slightly less silicon, resulting in a bit less fluidity but potentially improved strength. |
AlSi9Cu3 (319) | Silicon (9%), Copper (3%) | Looking for enhanced strength and wear resistance? AlSi9Cu3 steps up to the plate. The addition of copper elevates its mechanical properties, making it suitable for components under higher stress. |
Al-Cu (2017) | Copper (4%) | When superior strength is paramount, Al-Cu takes center stage. With a higher copper content, it boasts impressive strength but may require specific printing techniques to manage its slightly lower crack resistance. |
AlMgSc (AA4047) | Magnesium (0.3%), Scandium (0.3-0.4%) | Lightweight and high-performance? AlMgSc delivers. The addition of scandium refines its microstructure, leading to exceptional strength-to-weight ratio and excellent weldability. |
AlLi (2090) | Lithium (2-3%) | Shedding weight is the name of the game for AlLi. Lithium’s low density makes it the lightest of the bunch, perfect for aerospace applications where every gram counts. |
NiAl (INCONEL 625) | Nickel (60-62%) | High-temperature applications demand exceptional resistance. Enter NiAl, a unique aluminum-nickel alloy powder that thrives in harsh environments due to its outstanding oxidation resistance. |
TiAl (Ti-6Al-4V) | Titanium (Al 6%, V 4%) | Strength and heat resistance come together in TiAl. This aluminum-titanium alloy powder offers a compelling option for components operating at elevated temperatures and under significant stress. |
AlSiMgMn (AA6XXX Series) | Silicon (varying), Magnesium (varying), Manganese (varying) | The AA6XXX series represents a diverse family of aluminum based alloy powders formulated for specific applications. The varying ratios of silicon, magnesium, and manganese allow for customization of strength, corrosion resistance, and workability. |
AlZnMgCu (AA7XXX Series) | Zinc (varying), Magnesium (varying), Copper (varying) | Similar to the AA6XXX series, the AA7XXX family offers a spectrum of aluminum based alloy powders with tailored properties. Zinc additions enhance strength and wear resistance, making them suitable for high-stress components. |
This list just scratches the surface of the possibilities. With advancements in metallurgy, new and even more specialized aluminum based alloy powders are continually being developed to cater to ever-evolving engineering needs.
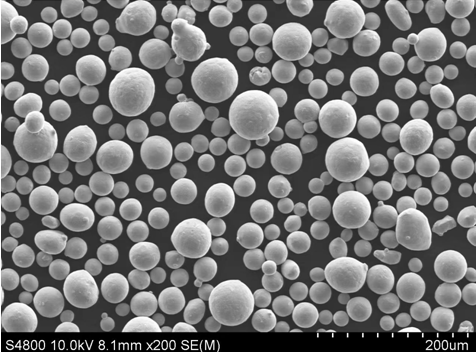
Applications of Aluminum Based Alloy Powders Shine
The versatility of aluminum based alloy powders translates into a vast array of applications across various industries. Here are some key areas where these innovative materials are making a significant impact:
Application Area | Specific Use Cases | Advantages of Aluminum Based Alloy Powders |
---|---|---|
Aerospace | Lightweight aircraft components, rocket engine parts, satellite structures | High strength-to-weight ratio, excellent mechanical properties, good weldability |
Automotive | Customizable car parts, intricate engine components, lightweight wheels | Design flexibility, weight reduction for improved fuel efficiency, ability to create |
Aluminum based alloy powders offer more than just a diverse composition; they boast a remarkable range of properties that make them truly stand out in the manufacturing world. Let’s delve deeper into some of their key characteristics:
- High Strength-to-Weight Ratio: One of the most celebrated properties of aluminum based alloy powders is their ability to be incredibly strong while remaining lightweight. This unique combination makes them ideal for applications like aerospace components and automotive parts, where minimizing weight is crucial for performance and efficiency.
Imagine an airplane wing – traditionally crafted from heavy metals – being redesigned using aluminum based alloy powders. The lighter weight translates to lower fuel consumption, increased range, and potentially even higher payload capacity. This advantage extends to cars as well, where lighter components can contribute to improved fuel economy and overall performance.
- Excellent Mechanical Properties: Beyond just strength, aluminum based alloy powders offer a spectrum of mechanical properties depending on their composition. AlSi10Mg, for instance, excels in castability, while Al-Cu boasts superior strength. This allows engineers to select the perfect powder for the specific demands of the application.
- Design Flexibility: Unlike traditional manufacturing methods that rely on subtractive processes (removing material from a solid block), additive manufacturing with aluminum based alloy powders utilizes a layered, additive approach. This opens doors to incredible design freedom. Complex geometries, intricate lattice structures, and even internal channels can be readily produced, pushing the boundaries of what’s possible.
Think of a lightweight prosthetic limb – with aluminum based alloy powders, intricate internal structures can be incorporated to mimic the strength and flexibility of natural bone, leading to more comfortable and functional prosthetics.
- Near-Net-Shape Manufacturing: Traditional manufacturing often generates significant scrap material. Aluminum based alloy powders, however, promote near-net-shape manufacturing, a process that minimizes waste. This not only reduces material costs but also aligns with sustainable manufacturing practices.
- Potential for Mass Customization: The digital nature of additive manufacturing using aluminum based alloy powders allows for easy customization. Imagine a scenario where a single printer can produce a batch of personalized car parts, each tailored to the specific needs of the vehicle. This opens doors for mass customization, a concept that was previously limited by traditional production methods.
However, it’s important to remember that no material is perfect. Aluminum based alloy powders also come with some limitations:
- Powder Handling and Storage: Aluminum based alloy powders can be susceptible to moisture and oxidation, requiring careful handling and storage procedures to maintain their quality.
- Surface Roughness: The additive manufacturing process can sometimes result in a slightly rougher surface finish compared to traditional methods. Post-processing techniques like machining or polishing might be necessary to achieve a desired surface texture.
- Limited Material Selection: While the range of aluminum based alloy powders is expanding, it’s still not as vast as some other materials used in traditional manufacturing. Research and development are ongoing to broaden the selection and cater to an even wider range of applications.
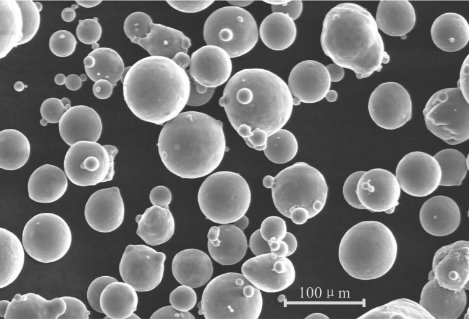
Specifications, Sizes, Grades, and Standards: Demystifying the Details
Selecting the right aluminum based alloy powder for a specific project requires an understanding of the available specifications, sizes, grades, and relevant standards. Here’s a breakdown to help you navigate this information:
Aluminum Based Alloy Powder Specifications:
These specifications typically include details like:
- Chemical Composition: The exact percentages of each element present in the powder.
- Particle Size Distribution: The range of sizes of the individual powder particles, which can influence printability and final product properties.
- Flowability: A measure of how easily the powder flows, impacting its suitability for different additive manufacturing processes.
- Apparent Density: The bulk density of the powder, which can affect material usage and cost calculations.
Aluminum Based Alloy Powder Sizes:
Aluminum based alloy powders come in a range of sizes, typically measured in micrometers (μm). Common sizes include:
- D10: Represents the size at which 10% of the powder particles are smaller.
- D50: Represents the median particle size, where 50% of the particles are smaller and 50% are larger.
- D90: Represents the size at which 90% of the powder particles are smaller.
The choice of particle size depends on the desired features of the final product. For instance, finer powders can generate smoother surface finishes but may require specific printing techniques to ensure proper flow.
Aluminum Based Alloy Powder Grades:
Aluminum based alloy powders are often categorized into grades based on their mechanical properties and intended applications. Some common grading systems include:
- American Society for Testing and Materials (ASTM) International: ASTM provides various standards for aluminum based alloy powders, such as ASTM B29 and ASTM F3444.
Aluminum Based Alloy Powder Suppliers and Pricing
With the growing demand for aluminum based alloy powders, a diverse range of suppliers has emerged. Here are some key factors to consider when choosing a supplier:
- Product Portfolio: Does the supplier offer the specific aluminum based alloy powder composition you require for your project?
- Powder Quality: Look for suppliers with a reputation for producing high-quality powders with consistent properties. Certifications like ISO 9001 can indicate a commitment to quality control.
- Pricing: Aluminum based alloy powder pricing can vary depending on the specific composition, particle size, and order quantity. It’s wise to compare prices from multiple suppliers to find the most competitive offer.
- Technical Support: Having access to knowledgeable technical support from the supplier can be invaluable, especially for those new to additive manufacturing with aluminum based alloy powders.
Here’s a table outlining some prominent aluminum based alloy powder suppliers, but it’s important to note that this is not an exhaustive list, and new players are continually entering the market:
Supplier | Location | Product Portfolio | Highlights |
---|---|---|---|
LPW | United Kingdom | Wide range of aluminum based alloy powders, including AlSi10Mg, AlSi7Mg0.3, AlSi9Cu3, and specialty powders | Renowned for high-quality powders and extensive application expertise |
SLM Solutions | Germany | Offers aluminum based alloy powders for various additive manufacturing platforms | Focuses on advanced materials and parameter development for optimal printing performance |
EOS GmbH | Germany | Provides aluminum based alloy powders compatible with their EOS additive manufacturing systems | Known for user-friendly powder handling solutions and a commitment to sustainability |
Höganäs AB | Sweden | Offers aluminum based alloy powders for metal injection molding (MIM) alongside additive manufacturing applications | Extensive experience in metal powder production and a strong focus on innovation |
AMetal | United States | Caters to various additive manufacturing technologies with a diverse aluminum based alloy powder portfolio | Emphasizes close collaboration with customers to select the optimal powder for their needs |
Pricing for aluminum based alloy powders can fluctuate based on market conditions and specific material properties. However, here’s a general range to provide some perspective:
- Metal Powder Cost: $20 – $100 per kilogram (kg)
- Additional Costs: Factors like shipping, handling, and minimum order quantities can influence the final price.
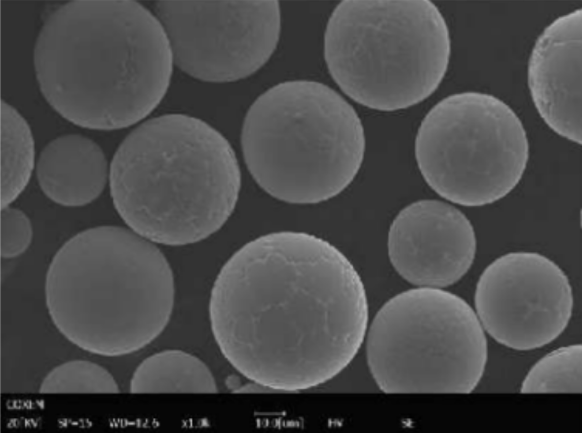
Pros and Cons of Aluminum Based Alloy Powders
Like any material, aluminum based alloy powders come with both advantages and limitations. Here’s a breakdown to help you make an informed decision:
Pros:
- High Strength-to-Weight Ratio: Aluminum based alloy powders offer exceptional strength while remaining lightweight, ideal for weight-sensitive applications.
- Excellent Mechanical Properties: The properties of aluminum based alloy powders can be tailored through composition, making them suitable for diverse engineering needs.
- Design Flexibility: Additive manufacturing with aluminum based alloy powders unlocks incredible design freedom, enabling the creation of complex geometries and intricate structures.
- Near-Net-Shape Manufacturing: This process minimizes waste and promotes sustainable manufacturing practices.
- Potential for Mass Customization: The digital nature of additive manufacturing allows for easy customization of components using aluminum based alloy powders.
Cons:
- Powder Handling and Storage: Proper handling and storage are crucial to maintain the quality of aluminum based alloy powders due to their susceptibility to moisture and oxidation.
- Surface Roughness: The additive manufacturing process might result in a slightly rougher surface finish compared to traditional methods. Post-processing techniques might be required for a desired surface texture.
- Limited Material Selection: While the selection of aluminum based alloy powders is expanding, it’s not as vast as some other materials used in traditional manufacturing.
Applications Beyond Imagination
Aluminum based alloy powders are not just revolutionizing current manufacturing processes; they hold immense potential for the future. Here are some exciting possibilities on the horizon:
- Biomedical Implants: The ability to create lightweight, biocompatible implants with intricate structures using aluminum based alloy powders has the potential to transform the field of biomedical engineering.
- Aerospace Innovation: With the ever-increasing demand for lightweight and high-performance components in the aerospace industry, aluminum based alloy powders are poised to play a key role in the development of next-generation aircraft and spacecraft.
- Sustainable Manufacturing: The near-net-shape nature of additive manufacturing using aluminum based alloy powders minimizes waste and promotes resource conservation, aligning with sustainable manufacturing practices.
- Mass Customization on Demand: The potential for on-demand, personalized production using aluminum based alloy powders could transform various industries, from automotive to consumer goods.
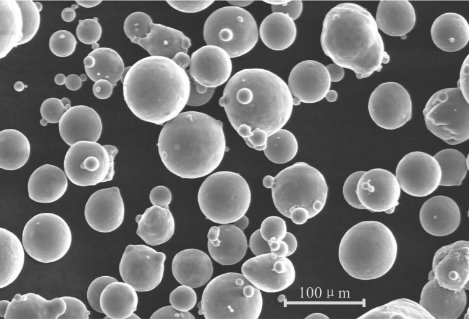
FAQ
1. What are the advantages of using aluminum based alloy powders compared to traditional manufacturing methods?
Aluminum based alloy powders offer several advantages over traditional methods like machining, casting, and forging:
- Design Flexibility: Additive manufacturing with these powders allows for the creation of complex geometries and intricate internal structures that would be challenging or impossible to achieve with traditional techniques.
- Weight Reduction: The high strength-to-weight ratio of aluminum based alloy powders translates to lighter components, crucial for applications like aerospace and automotive where weight reduction is critical for performance and efficiency.
- Material Efficiency: Near-net-shape manufacturing with aluminum based alloy powders minimizes waste compared to subtractive processes used in traditional methods.
- Mass Customization: The digital nature of additive manufacturing allows for easier customization of components, potentially leading to on-demand, personalized production.
2. What are some of the challenges associated with using aluminum based alloy powders?
While aluminum based alloy powders offer exciting possibilities, there are some challenges to consider:
- Powder Handling and Storage: These powders can be susceptible to moisture and oxidation, requiring careful handling and storage procedures to maintain their quality.
- Surface Roughness: The additive manufacturing process might result in a slightly rougher surface finish compared to traditional methods. Post-processing techniques like machining or polishing might be necessary depending on the desired surface texture.
- Limited Material Selection: The range of aluminum based alloy powders available is still expanding, and it’s not as vast as some other materials used in traditional manufacturing. However, research and development are ongoing to broaden the selection for even wider application.
3. What safety precautions should be taken when working with aluminum based alloy powders?
Aluminum based alloy powders can be flammable and pose inhalation risks. Here are some safety precautions to follow:
- Always wear appropriate personal protective equipment (PPE) like gloves, safety glasses, and a respirator when handling the powder.
- Work in a well-ventilated area to avoid inhaling powder particles.
- Store aluminum based alloy powders in a cool, dry place away from heat and ignition sources.
- Dispose of waste powder according to local regulations.
4. How much do aluminum based alloy powders cost?
The cost of aluminum based alloy powders can vary depending on several factors, including:
- Specific composition: Specialty powders with unique alloying elements might be more expensive than common varieties.
- Particle size: Finer powders might command a premium compared to coarser ones.
- Order quantity: Bulk purchases often come with discounted pricing compared to smaller orders.
As a general estimate, the metal powder cost itself can range from $20 to $100 per kilogram (kg). Additional costs like shipping, handling, and minimum order quantities can influence the final price. It’s recommended to reach out to potential suppliers and request quotes for specific aluminum based alloy powder needs.
5. Where can I find more information about aluminum based alloy powders?
Several resources can provide you with detailed information about aluminum based alloy powders:
- Industry Associations: Organizations like the American Society for Testing and Materials (ASTM) International and the Aluminum Association (AA) publish standards and specifications related to aluminum based alloy powders.
- Metal Powder Manufacturers: Websites of reputable metal powder manufacturers like LPW, SLM Solutions, EOS GmbH, Höganäs AB, and AMetal often contain valuable information about different aluminum based alloy powder offerings, their properties, and applications.
- Technical Publications and Research Papers: Scientific journals and industry publications frequently publish articles on advancements and applications of aluminum based alloy powders.
By exploring these resources, you can gain a deeper understanding of this versatile material and its potential to revolutionize manufacturing across diverse industries.