Introduction
In recent years, the field of additive manufacturing has witnessed groundbreaking advancements, opening up new possibilities for design and production across various industries. Among the innovative technologies that have emerged, Electron Beam Melting (EBM) stands out as a powerful method for fabricating complex and high-quality metal parts. In this article, we will delve into the working principle of Electron Beam Melting, explore its advantages, applications, challenges, and future prospects.
What is Electron Beam Melting (EBM)?
Electron Beam Melting is an additive manufacturing technique that uses an electron beam to selectively melt and fuse metal powder to create intricate three-dimensional objects layer by layer. Developed by Arcam AB (now a part of GE Additive), electron beam melting working principle has gained popularity due to its ability to produce fully dense metal components with excellent mechanical properties.
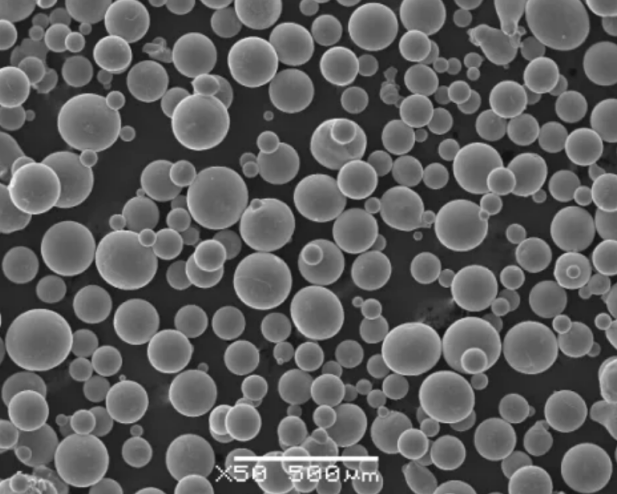
The Working Principle of Electron Beam Melting
Electron Beam Generation
The EBM process starts with the generation of an electron beam. Electrons are accelerated to high velocities using electromagnetic fields, forming a focused and precise beam that acts as the heat source during the melting process.
Electron Beam Focusing
The focused electron beam is then directed onto the build platform, where the metal powder is located. The beam’s energy is concentrated on specific areas, causing the powder particles to rapidly heat up and fuse together.
Build Platform and Powder Bed
The build platform is an essential component of the EBM system. It positions and controls the height of the metal powder bed. As each layer is melted, the platform gradually lowers, allowing a new layer of powder to be spread on top for the next pass of the electron beam.
The Melting Process
As the electron beam sweeps over the metal powder bed, it selectively melts the particles, fusing them together and solidifying the layer. This layer-by-layer process continues until the entire object is fabricated with the desired dimensions and complexity.
Advantages of Electron Beam Melting
EBM offers numerous advantages over traditional manufacturing methods, making it a preferred choice for various applications. Some of the key advantages include:
Complex Geometries
EBM enables the production of complex geometries that would be challenging or impossible to achieve with conventional methods. This freedom of design allows engineers to create lightweight yet robust components with internal structures optimized for specific functions.
Material Diversity
With EBM, a wide range of metals and metal alloys can be processed, including titanium, stainless steel, aluminum, and nickel-based alloys. This versatility opens up opportunities for using materials with exceptional properties tailored for specific applications.
Reduced Material Waste
Traditional subtractive manufacturing methods often result in significant material waste. EBM, on the other hand, is an additive process, which means it only uses the necessary amount of material to create the final product, minimizing waste and optimizing material usage.
High Precision and Accuracy
EBM boasts exceptional precision and accuracy, allowing for the fabrication of parts with tight tolerances. This level of precision is critical in industries such as aerospace and healthcare, where the smallest deviations can have significant consequences.
Rapid Prototyping and Manufacturing
Additive manufacturing techniques like EBM offer faster prototyping and production times, reducing the lead time from design to finished product. This speed advantage is particularly beneficial for industries where time-to-market is crucial.
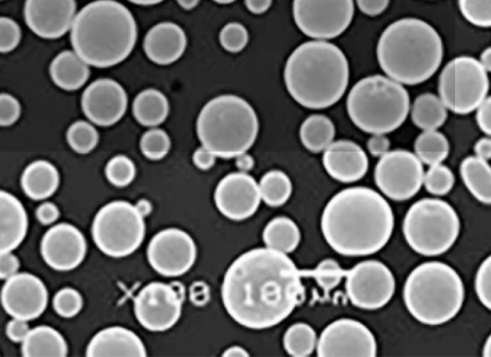
Applications of Electron Beam Melting
The capabilities of EBM have made it a valuable technology in several industries. Some of the prominent applications include:
Aerospace Industry
In the aerospace sector, where weight reduction and high-performance materials are paramount, EBM is utilized to fabricate complex components for aircraft and spacecraft. Its ability to produce lightweight parts with intricate geometries contributes to improved fuel efficiency and overall performance.
Medical and Dental Implants
EBM has revolutionized the production of medical and dental implants. By using biocompatible materials like titanium, personalized implants can be created, tailored to match each patient’s unique anatomy, leading to better patient outcomes.
Automotive Components
In the automotive industry, EBM is employed to manufacture lightweight and durable components, contributing to enhanced vehicle efficiency and safety. The technology allows for the integration of multiple parts into a single component, reducing assembly complexity.
Custom Jewelry
Jewelry designers leverage EBM to craft intricate and personalized pieces, pushing the boundaries of creativity. The ability to create intricate lattice structures and unique designs has opened up new opportunities in the jewelry industry.
Challenges and Limitations of Electron Beam Melting
As with any manufacturing process, EBM comes with its set of challenges and limitations, including:
Residual Stress and Distortion
During the melting and solidification process, residual stresses can build up within the part, leading to distortion or warping. Proper process optimization and post-processing techniques are required to mitigate these issues.
Post-Processing Requirements
After the fabrication process, parts often require post-processing steps such as heat treatment or machining to achieve the desired mechanical properties and surface finish. These additional steps can add time and cost to the overall manufacturing process.
Equipment Cost and Maintenance
The initial investment in EBM equipment can be significant, and regular maintenance is essential to ensure consistent and reliable performance. However, as the technology advances, the costs are expected to reduce over time.
Powder Handling and Contamination
Metal powders used in EBM must be carefully handled to avoid contamination, as impurities can affect the integrity of the final product. Specialized equipment and controlled environments are necessary to maintain the quality and consistency of the powder.
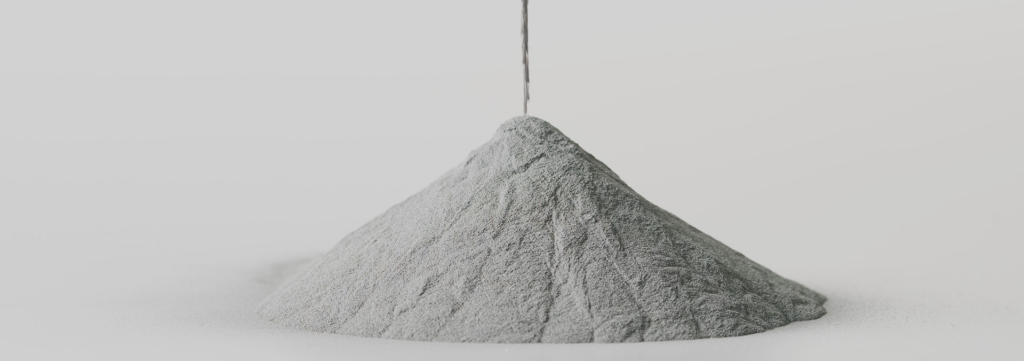
Future Prospects of Electron Beam Melting
Despite the challenges, Electron Beam Melting continues to evolve, and ongoing research and development are paving the way for exciting future prospects:
Advancements in Materials
Researchers are continuously exploring new materials suitable for EBM, including high-temperature alloys, composites, and biomaterials. As material options expand, the range of applications for EBM is set to grow, impacting industries beyond the current scope.
Process Optimization
To address challenges like residual stress and distortion, optimization techniques are being developed to enhance the EBM process. By fine-tuning parameters and optimizing scan strategies, manufacturers can further improve part quality and reduce post-processing requirements.
Integration with Other Technologies
EBM is not a standalone manufacturing technique. Integration with other additive and subtractive processes is being explored to combine the strengths of different methods. Hybrid manufacturing approaches can offer even more possibilities for complex and functional parts.
Conclusion
Electron Beam Melting has revolutionized the world of additive manufacturing, offering a unique combination of design freedom, material diversity, and precision. From aerospace and healthcare to automotive and jewelry, EBM is transforming various industries by enabling the creation of complex and high-performance components. As the technology continues to advance and overcome its limitations, we can expect even more exciting developments in the future, opening up new possibilities for innovation and application.
FAQs
What is the difference between Electron Beam Melting and Selective Laser Melting?
Electron Beam Melting (EBM) and Selective Laser Melting (SLM) are both additive manufacturing techniques that use energy sources to fuse metal powder. The main difference lies in the heat source: EBM uses an electron beam, while SLM employs a laser. The choice between the two methods depends on the specific application, material, and desired properties of the final product.
Can Electron Beam Melting be used for large-scale production?
Yes, Electron Beam Melting can be used for large-scale production. As the technology improves and becomes more cost-effective, it is increasingly adopted for industrial-scale manufacturing. Large EBM machines with multiple electron beam sources can significantly increase production capacity.
What materials can be used in Electron Beam Melting?
EBM is compatible with various metals and metal alloys, including titanium, stainless steel, aluminum, nickel-based alloys, and more. The choice of material depends on the application and the desired properties of the final product.
How does Electron Beam Melting compare to traditional manufacturing methods?
Compared to traditional manufacturing methods like casting and machining, Electron Beam Melting offers several advantages. It allows for the fabrication of complex geometries, reduces material waste, and enables the use of advanced materials. However, it may have certain limitations, such as post-processing requirements and initial equipment cost.
Is Electron Beam Melting environmentally friendly?
EBM is considered relatively environmentally friendly compared to traditional manufacturing methods. Its additive nature minimizes material waste, and the use of advanced materials can lead to lighter and more fuel-efficient products, contributing to sustainability efforts in industries like aerospace and automotive. However, it’s essential to manage the energy consumption and disposal of metal powders responsibly to ensure environmental impact remains minimal.