Introduction
Gas atomized powder is a finely divided material that finds extensive use in various industries, including metal additive manufacturing, powder metallurgy, and thermal spray coatings. It is produced through the gas atomization process, which involves melting a metal or alloy and dispersing it into small droplets using a high-pressure gas stream. This article explores the gas atomization technique, its advantages, applications, quality control methods, and future developments in the field.
What is Gas Atomized Powder?
Gas atomized powder refers to a type of powdered material produced by atomizing molten metal or alloy using a gas stream. In this process, the metal or alloy is heated until it reaches its melting point and is then subjected to a high-pressure gas, which breaks it down into small droplets. These droplets rapidly solidify into fine particles, resulting in the formation of gas atomized powder.
The Gas Atomization Process
The gas atomization process begins with the melting of the metal or alloy in a crucible or furnace. Once the material reaches the desired temperature, a high-pressure gas, such as nitrogen, argon, or helium, is injected into the melt. The gas breaks up the molten metal into small droplets, which solidify rapidly as they are carried away by the gas stream. The solidified particles are then collected and further processed to obtain the desired powder characteristics.
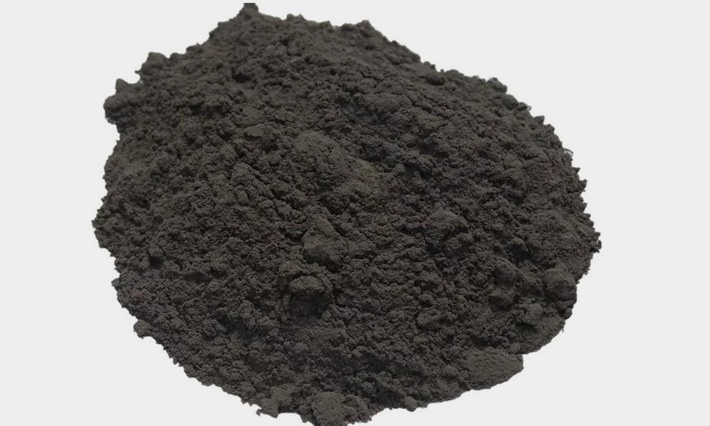
Advantages of Gas Atomized Powder
Gas atomized powder offers several advantages over other powder production methods, making it a preferred choice in various applications. Some of the key advantages include:
- High Purity and Homogeneity: Gas atomization results in powders with high purity and excellent chemical homogeneity. The rapid solidification process prevents the formation of impurities and segregations, leading to uniform powder particles.
- Improved Flowability and Packing Density: Gas atomized powders exhibit enhanced flowability and packing density due to their spherical particle shape. This property is crucial for efficient powder handling, transportation, and processing.
- Enhanced Powder Properties: Gas atomization enables the production of powders with tailored properties, such as controlled particle size distribution, composition, and microstructure. This flexibility allows for the customization of powders to meet specific application requirements.
- Wide Range of Applications: Gas atomized powders find applications in diverse industries, including aerospace, automotive, energy, and medical. They are utilized in processes such as metal additive manufacturing, powder metallurgy, thermal spray coatings, and surface modification.
Gas Atomization Techniques
Gas atomization can be performed using different techniques depending on the specific requirements of the powder. Some commonly used gas atomization techniques include:
- Water Atomization: In water atomization, the high-pressure gas is injected into the molten metal, which is then atomized by a water spray. This technique is suitable for producing large quantities of fine powder.
- Gas Atomization with Nitrogen or Argon: Nitrogen or argon gas is used to atomize the molten metal in this technique. It is a versatile method suitable for a wide range of materials and can produce powders with excellent flowability and particle size control.
- Vacuum Gas Atomization: Vacuum gas atomization involves atomizing the molten metal in a vacuum chamber. The absence of air reduces the oxidation and contamination of the powder, resulting in high-purity materials.
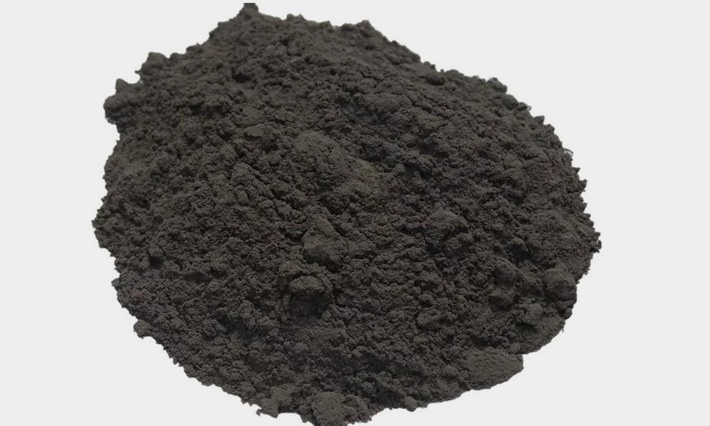
Applications of Gas Atomized Powder
Gas atomized powders are extensively utilized in various industries due to their unique properties. Some notable applications of gas atomized powder include:
- Metal Additive Manufacturing: Gas atomized powders are commonly used as feedstock materials in metal additive manufacturing processes, such as powder bed fusion and directed energy deposition. They enable the production of complex geometries and high-performance metal parts.
- Powder Metallurgy: Gas atomized powders serve as the raw material in powder metallurgy, where they are compacted and sintered to form solid components. The controlled particle size distribution and composition of gas atomized powders enhance the density, strength, and performance of the final products.
- Thermal Spray Coatings: Gas atomized powders are employed in thermal spray coating processes to provide protective or functional coatings on various surfaces. These coatings offer improved wear resistance, corrosion protection, and thermal insulation.
- Surface Modification: Gas atomized powders can be used for surface modification treatments, such as laser cladding, plasma spraying, and cold spraying. These processes enhance the surface properties of materials, such as hardness, wear resistance, and chemical resistance.
- Sintering and Consolidation: Gas atomized powders are crucial in the sintering and consolidation of powdered materials. They enable the formation of dense and fully consolidated components with controlled microstructures and properties.
Quality Control and Characterization of Gas Atomized Powder
To ensure the quality and consistency of gas atomized powders, various characterization techniques and quality control measures are employed. Some common methods include:
- Particle Size Distribution Analysis: Particle size distribution analysis helps determine the range and distribution of particle sizes in the gas atomized powder. Techniques such as laser diffraction and microscopy are commonly used for this purpose.
- Chemical Composition Analysis: Chemical composition analysis ensures that the gas atomized powder meets the desired specifications. Techniques like optical emission spectroscopy and X-ray fluorescence spectroscopy are used to analyze the elemental composition of the powder.
- Microstructural Analysis: Microstructural analysis techniques, such as scanning electron microscopy and transmission electron microscopy, provide insights into the internal structure and morphology of gas atomized powder particles.
- Powder Flow and Rheology Testing: Powder flow and rheology testing evaluate the flow properties and behavior of gas atomized powders. These tests help assess the powder’s ability to flow, pack, and fill molds or containers.
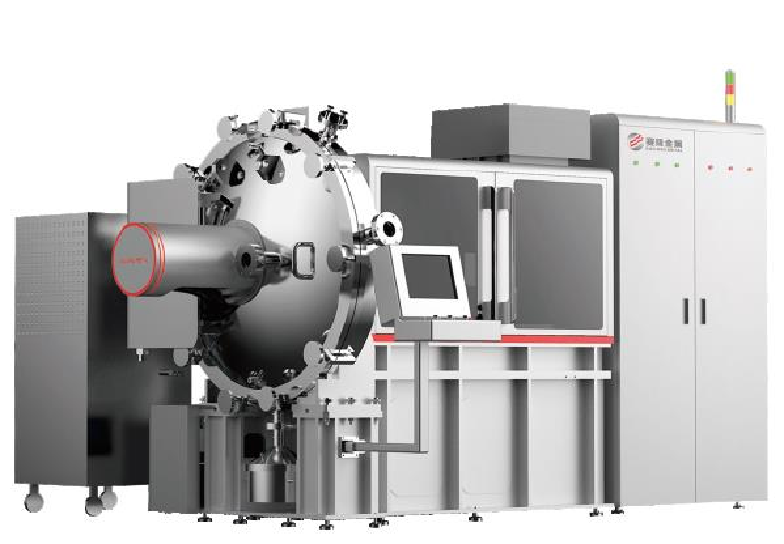
Challenges and Future Developments in Gas Atomization
Gas atomization is a well-established process, but it still faces certain challenges and offers opportunities for future developments. Some key areas of focus include:
- Process Optimization: Continued research and development aim to optimize the gas atomization process parameters, such as gas velocity, atomization pressure, and melt temperature, to further improve powder quality, yield, and efficiency.
- Particle Size Control: Achieving precise control over particle size distribution is a crucial aspect of gas atomization. Ongoing research focuses on developing advanced atomization techniques and nozzle designs to produce powders with narrower size ranges and tailored particle sizes.
- Alloy Development: Gas atomization allows for the production of a wide range of alloys with unique compositions and properties. Future advancements aim to expand the alloy repertoire and develop novel materials with enhanced performance for specific applications, such as high-temperature alloys, lightweight alloys, and advanced functional materials.
- Sustainability and Environmental Impact: As sustainability becomes increasingly important, efforts are being made to reduce the environmental impact of gas atomization processes. This includes optimizing energy consumption, minimizing waste generation, and exploring alternative gas sources or recycling methods.
Conclusion
Gas atomized powder is a versatile and valuable material widely used in industries such as metal additive manufacturing, powder metallurgy, and thermal spray coatings. Its production through the gas atomization process ensures high purity, homogeneity, and improved powder properties. Gas atomized powders find applications in diverse fields and offer numerous advantages, including enhanced flowability, tailored properties, and excellent packing density. Quality control measures and characterization techniques ensure consistent powder quality. Challenges and future developments in gas atomization focus on process optimization, particle size control, alloy development, and sustainability. The continuous advancement of gas atomization techniques and materials will drive innovation and broaden the range of applications for gas atomized powders.
FAQs
1. Can gas atomized powder be used in 3D printing?
Yes, gas atomized powder is commonly used as feedstock material in metal 3D printing processes, such as powder bed fusion and directed energy deposition. Its spherical particle shape, controlled particle size distribution, and excellent flowability make it ideal for achieving high-quality and complex printed parts.
2. How is the particle size distribution of gas atomized powder controlled?
The particle size distribution of gas atomized powder can be controlled by adjusting various process parameters such as gas velocity, melt temperature, and atomization pressure. Additionally, the design of atomization nozzles and the choice of gas medium play a significant role in achieving the desired particle size distribution.
3. What are the advantages of gas atomized powder in powder metallurgy applications?
Gas atomized powder offers several advantages in powder metallurgy applications. It provides improved density, strength, and performance in the final products due to its uniform composition, controlled particle size distribution, and enhanced flowability. These characteristics result in better sintering and consolidation behavior during the manufacturing process.
4. How is the quality of gas atomized powder ensured?
The quality of gas atomized powder is ensured through rigorous quality control measures. This includes analyzing the particle size distribution, conducting chemical composition analysis, examining microstructural properties, and evaluating powder flow and rheology characteristics. These tests and analyses help maintain consistent powder quality and performance.
5. What are the environmental considerations in gas atomization processes?
Environmental considerations in gas atomization processes involve optimizing energy consumption, minimizing waste generation, and reducing the overall environmental impact. Researchers and industry professionals are exploring energy-efficient techniques, alternative gas sources, and recycling methods to make gas atomization processes more sustainable and environmentally friendly.