Overview of Vacuum Induction Melting
Ever wondered how some of the most sophisticated metal components are made? Vacuum Induction Melting (VIM) is a critical process in the manufacturing of high-purity metal alloys. This technique involves melting metals in a vacuum environment using electromagnetic induction. The vacuum environment reduces contamination and ensures high-purity results, making it indispensable in industries that demand superior quality materials, such as aerospace, medical devices, and advanced manufacturing.
In this article, we’ll dive deep into the world of VIM. We’ll cover everything from the basics to the technical details, including the types of metal powders produced, their compositions, properties, applications, specifications, and much more. So, buckle up and get ready for an in-depth exploration of Vacuum Induction Melting!
What is Vacuum Induction Melting?
Vacuum Induction Melting (VIM) is a metallurgical process used to produce high-quality metal alloys by melting metals in a vacuum using induction heating. The vacuum environment minimizes oxidation and contamination from gases, resulting in purer and more consistent alloys. This process is especially important for producing materials that require stringent control over composition and microstructure.
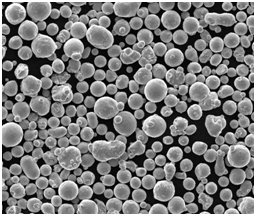
Why Vacuum Induction Melting?
Why do we use Vacuum Induction Melting instead of other melting methods? The answer lies in its ability to produce exceptionally pure and homogeneous metals. The vacuum reduces the presence of unwanted gases like oxygen and nitrogen, which can form undesirable compounds and inclusions. This makes VIM ideal for applications requiring high-performance materials, such as turbine blades, medical implants, and high-strength components.
Types of Metal Powders Produced by Vacuum Induction Melting
One of the primary outputs of VIM is metal powders used in various applications. Here are some specific metal powder models produced through this process:
- Inconel 718
- Composition: Nickel, Chromium, Iron, Molybdenum
- Properties: High strength, corrosion resistance, good weldability
- Applications: Aerospace components, gas turbine blades, nuclear reactors
- Titanium Alloy (Ti-6Al-4V)
- Composition: Titanium, Aluminum, Vanadium
- Properties: High strength-to-weight ratio, excellent corrosion resistance
- Applications: Biomedical implants, aerospace structures, automotive parts
- Cobalt-Chromium Alloy (CoCrMo)
- Composition: Cobalt, Chromium, Molybdenum
- Properties: Wear resistance, biocompatibility, high strength
- Applications: Dental implants, orthopedic implants, industrial wear parts
- Maraging Steel (18Ni-300)
- Composition: Nickel, Cobalt, Molybdenum, Titanium
- Properties: Ultra-high strength, toughness, good machinability
- Applications: Aerospace components, tooling, high-strength fasteners
- Aluminum Alloy (AlSi10Mg)
- Composition: Aluminum, Silicon, Magnesium
- Properties: Lightweight, good thermal conductivity, corrosion resistance
- Applications: Automotive parts, aerospace components, electronics
- Stainless Steel 316L
- Composition: Iron, Chromium, Nickel, Molybdenum
- Properties: Corrosion resistance, good mechanical properties, biocompatibility
- Applications: Medical devices, chemical processing equipment, marine applications
- Hastelloy X
- Composition: Nickel, Chromium, Iron, Molybdenum
- Properties: High-temperature strength, oxidation resistance
- Applications: Gas turbines, aerospace components, chemical processing
- Tool Steel (H13)
- Composition: Chromium, Molybdenum, Vanadium, Carbon
- Properties: High toughness, wear resistance, thermal fatigue resistance
- Applications: Die casting molds, extrusion tools, hot forging
- Nickel Alloy 625
- Composition: Nickel, Chromium, Molybdenum, Niobium
- Properties: Corrosion resistance, high strength, weldability
- Applications: Marine engineering, chemical processing, aerospace
- Copper Alloy (CuCrZr)
- Composition: Copper, Chromium, Zirconium
- Properties: High electrical conductivity, good mechanical properties
- Applications: Electrical contacts, welding electrodes, heat exchangers
Composition of Metal Powders
Metal Powder | Composition | Properties | Applications |
---|---|---|---|
Inconel 718 | Nickel, Chromium, Iron, Molybdenum | High strength, corrosion resistance | Aerospace, gas turbines, nuclear reactors |
Titanium Alloy (Ti-6Al-4V) | Titanium, Aluminum, Vanadium | High strength-to-weight ratio | Biomedical implants, aerospace |
Cobalt-Chromium Alloy (CoCrMo) | Cobalt, Chromium, Molybdenum | Wear resistance, biocompatibility | Dental implants, orthopedic implants |
Maraging Steel (18Ni-300) | Nickel, Cobalt, Molybdenum, Titanium | Ultra-high strength, toughness | Aerospace, tooling, fasteners |
Aluminum Alloy (AlSi10Mg) | Aluminum, Silicon, Magnesium | Lightweight, good thermal conductivity | Automotive, aerospace, electronics |
Stainless Steel 316L | Iron, Chromium, Nickel, Molybdenum | Corrosion resistance, biocompatibility | Medical devices, chemical processing, marine |
Hastelloy X | Nickel, Chromium, Iron, Molybdenum | High-temperature strength | Gas turbines, aerospace, chemical processing |
Tool Steel (H13) | Chromium, Molybdenum, Vanadium, Carbon | High toughness, wear resistance | Die casting molds, extrusion tools, forging |
Nickel Alloy 625 | Nickel, Chromium, Molybdenum, Niobium | Corrosion resistance, high strength | Marine engineering, chemical processing |
Copper Alloy (CuCrZr) | Copper, Chromium, Zirconium | High electrical conductivity | Electrical contacts, welding electrodes |
Characteristics of Vacuum Induction Melting
VIM is characterized by several unique features:
- Vacuum Environment: Reduces contamination by gases, ensuring high purity.
- Induction Heating: Provides efficient and uniform melting.
- Controlled Atmosphere: Allows precise control of alloy composition.
- Flexibility: Suitable for a wide range of metals and alloys.
- Homogeneity: Produces materials with uniform microstructure.
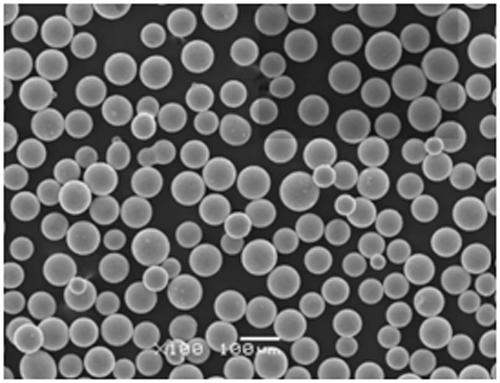
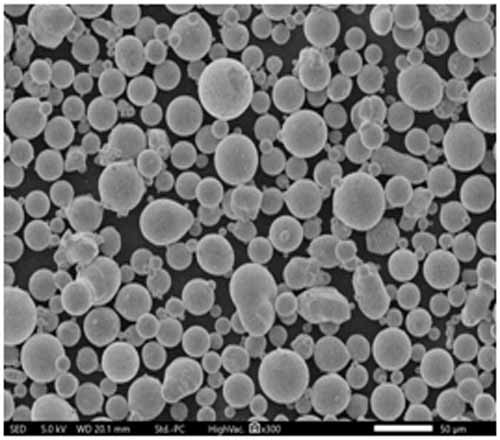
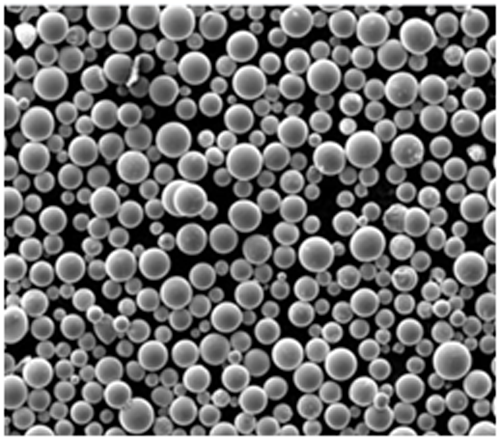
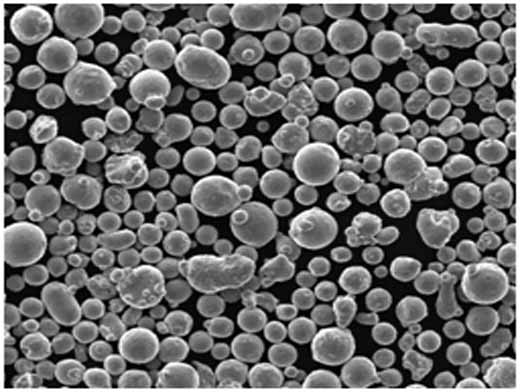
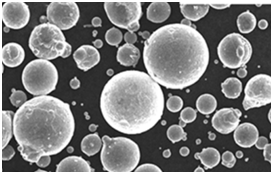
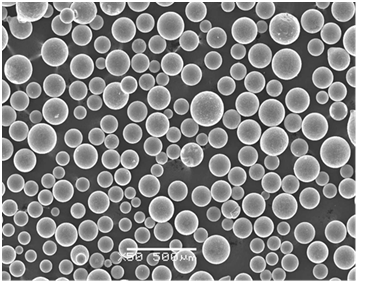
Applications of Vacuum Induction Melting
VIM finds applications across various industries, including:
Industry | Applications |
---|---|
Aerospace | Turbine blades, structural components, fasteners |
Medical Devices | Implants, surgical instruments |
Automotive | Engine components, lightweight structures |
Electronics | Conductive materials, heat sinks |
Industrial | Tooling, wear-resistant parts, chemical processing |
Marine | Corrosion-resistant components, propeller shafts |
Specifications, Sizes, Grades, and Standards
When it comes to specifications, sizes, grades, and standards, VIM-produced metal powders adhere to strict criteria to meet industry requirements. Below is a detailed overview:
Metal Powder | Specifications | Sizes | Grades | Standards |
---|---|---|---|---|
Inconel 718 | ASTM B637, AMS 5662 | 5-45 µm, 15-45 µm | Grade 1, Grade 2 | ASTM, AMS |
Titanium Alloy (Ti-6Al-4V) | ASTM F136, AMS 4907 | 5-25 µm, 15-53 µm | Grade 5, Grade 23 | ASTM, AMS |
Cobalt-Chromium Alloy (CoCrMo) | ASTM F75, ISO 5832-4 | 10-45 µm, 20-63 µm | Grade 1, Grade 2 | ASTM, ISO |
Maraging Steel (18Ni-300) | ASTM A538, AMS 6514 | 5-45 µm, 15-45 µm | Grade 300, Grade 350 | ASTM, AMS |
Aluminum Alloy (AlSi10Mg) | ISO 3522, AMS 4289 | 10-45 µm, 20-63 µm | Grade A, Grade B | ISO, AMS |
Stainless Steel 316L | ASTM A276, ISO 5832-1 | 10-45 µm, 20-63 µm | Grade L | ASTM, ISO |
Hastelloy X | ASTM B572, AMS 5536 | 5-45 µm, 15-45 µm | Grade 1, Grade 2 | ASTM, AMS |
Tool Steel (H13) | ASTM A681, SAE J438 | 10-45 µm, 20-63 µm | Grade A, Grade B | ASTM, SAE |
Nickel Alloy 625 | ASTM B446, AMS 5666 | 5-45 µm, 15-45 µm | Grade 1, Grade 2 | ASTM, AMS |
Copper Alloy (CuCrZr) | ASTM B422, DIN 17670 | 10-45 µm, 20-63 µm | Grade A, Grade B | ASTM, DIN |
Suppliers and Pricing Details
When sourcing metal powders produced through VIM, it’s essential to know the leading suppliers and their pricing. Here’s a snapshot:
Supplier | Metal Powder | Price Range (per kg) |
---|---|---|
Carpenter Technology | Inconel 718, Titanium Alloy | $200 – $400 |
Praxair Surface Technologies | Cobalt-Chromium Alloy, Maraging Steel | $250 – $450 |
LPW Technology | Aluminum Alloy, Stainless Steel 316L | $150 – $350 |
Oerlikon Metco | Hastelloy X, Tool Steel | $300 – $500 |
Sandvik Additive Manufacturing | Nickel Alloy 625, Copper Alloy | $220 – $420 |
Pros and Cons: Vacuum Induction Melting
Let’s weigh the advantages and limitations of VIM:
Pros | Cons |
---|---|
High purity and reduced contamination | High operational costs |
Precise control over alloy composition | Complex equipment and maintenance |
Uniform microstructure | Limited to specific metals and alloys |
Flexibility in producing a wide range of alloys | Requires skilled operators and stringent process control |
Reduced inclusion formation | Vacuum requirements can be challenging |
In-Depth Look: Metal Powders Produced by Vacuum Induction Melting
Inconel 718: Strength and Versatility
Inconel 718 is a nickel-chromium alloy known for its high strength, corrosion resistance, and excellent weldability. It’s widely used in the aerospace industry for turbine blades and other high-temperature applications. The addition of molybdenum enhances its mechanical properties, making it suitable for nuclear reactors and other demanding environments.
Titanium Alloy (Ti-6Al-4V): Light and Strong
Ti-6Al-4V, also known as Grade 5 titanium, is a workhorse alloy in the aerospace and biomedical industries. Its high strength-to-weight ratio and excellent corrosion resistance make it ideal for aircraft structures and medical implants. The alloy’s biocompatibility ensures that it integrates well with human tissues, making it a top choice for prosthetics and orthopedic devices.
Cobalt-Chromium Alloy (CoCrMo): Durability and Biocompatibility
Cobalt-Chromium alloys, particularly CoCrMo, are renowned for their wear resistance and biocompatibility. These properties make them perfect for dental implants, orthopedic implants, and industrial wear parts. The alloy’s ability to withstand harsh environments and maintain its mechanical integrity under stress is unmatched.
Maraging Steel (18Ni-300): High Strength and Toughness
Maraging steels like 18Ni-300 are ultra-high-strength materials used in aerospace, tooling, and high-strength fasteners. They undergo a unique aging process that enhances their mechanical properties without compromising toughness. This makes them ideal for applications where both strength and ductility are crucial.
Aluminum Alloy (AlSi10Mg): Lightweight and Conductive
AlSi10Mg is an aluminum alloy with excellent thermal conductivity and lightweight properties. It’s widely used in the automotive and aerospace industries for components that require good mechanical properties and low weight. The addition of silicon and magnesium enhances its castability and mechanical strength.
Stainless Steel 316L: Corrosion Resistant and Biocompatible
Stainless Steel 316L is a low-carbon variant of 316 stainless steel, known for its corrosion resistance and biocompatibility. It’s commonly used in medical devices, chemical processing equipment, and marine applications. The alloy’s resistance to pitting and crevice corrosion in chloride environments makes it a reliable choice for harsh conditions.
Hastelloy X: High-Temperature Strength
Hastelloy X is a nickel-based superalloy with exceptional high-temperature strength and oxidation resistance. It’s used in gas turbines, aerospace components, and chemical processing. The alloy’s ability to maintain its mechanical properties at elevated temperatures ensures its reliability in demanding applications.
Tool Steel (H13): Tough and Wear-Resistant
H13 is a chromium-molybdenum-vanadium alloyed tool steel known for its high toughness and wear resistance. It’s used in die casting molds, extrusion tools, and hot forging applications. The alloy’s thermal fatigue resistance makes it suitable for high-temperature tooling.
Nickel Alloy 625: Corrosion Resistant and Weldable
Nickel Alloy 625 is renowned for its corrosion resistance, high strength, and excellent weldability. It’s used in marine engineering, chemical processing, and aerospace applications. The alloy’s resistance to pitting and crevice corrosion makes it a top choice for harsh environments.
Copper Alloy (CuCrZr): Conductive and Durable
CuCrZr is a copper alloy with high electrical conductivity and good mechanical properties. It’s used in electrical contacts, welding electrodes, and heat exchangers. The addition of chromium and zirconium enhances its strength and durability, making it suitable for high-performance electrical applications.
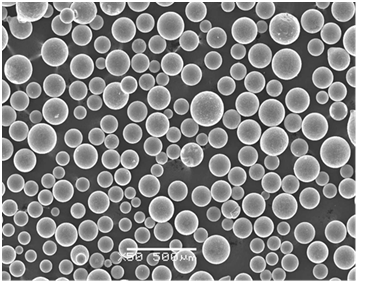
FAQ
Question | Answer |
---|---|
What is Vacuum Induction Melting (VIM)? | VIM is a process of melting metals in a vacuum using induction heating to produce high-purity metal alloys. |
Why use VIM over other melting methods? | VIM offers reduced contamination, precise control over composition, and high-purity results. |
What industries use VIM? | Aerospace, medical devices, automotive, electronics, industrial, and marine industries. |
What are the benefits of VIM? | High purity, precise control, uniform microstructure, and reduced contamination. |
Are there any limitations to VIM? | High operational costs, complex equipment, limited to specific metals, and requires skilled operators. |
What metals can be melted using VIM? | A wide range including nickel alloys, titanium alloys, cobalt-chromium alloys, maraging steel, and more. |
How does VIM ensure high purity? | The vacuum environment reduces contamination by gases, ensuring minimal impurities in the final alloy. |
Can VIM be used for large-scale production? | Yes, but it is more commonly used for high-value, high-purity applications due to its cost and complexity. |
What are the key properties of VIM metals? | High strength, corrosion resistance, biocompatibility, and high-temperature stability. |
Who are the leading suppliers of VIM powders? | Carpenter Technology, Praxair Surface Technologies, LPW Technology, Oerlikon Metco, Sandvik Additive Manufacturing. |
Conclusion
Vacuum Induction Melting is a vital process in the production of high-quality metal alloys. Its ability to produce pure and homogeneous materials makes it indispensable in industries that demand superior performance. From aerospace components to medical implants, the applications of VIM are vast and varied. By understanding the intricacies of this process, you can appreciate the precision and care that goes into creating some of the most advanced materials in the world.
In this guide, we’ve explored the depths of VIM, from its basic principles to the specific metal powders it produces. We’ve covered their compositions, properties, applications, and even the leading suppliers and pricing. Whether you’re a professional in the field or simply curious about advanced manufacturing techniques, we hope this comprehensive guide has provided valuable insights into the fascinating world of Vacuum Induction Melting.