If you’ve ever wondered how the various metal powders used in manufacturing are made, then you’re in the right place. This article delves into the fascinating world of powder making devices. From understanding what these devices are, to exploring the different models available, and uncovering their unique properties and uses, this comprehensive guide will provide you with all the insights you need. So, let’s dive right in!
Overview of Powder Making Devices
Powder making devices are sophisticated machines designed to produce fine metal powders from raw materials. These powders are essential in various industries, including aerospace, automotive, electronics, and medical devices. The process of powder making involves atomization, mechanical comminution, and chemical reduction, among other techniques. Each method offers distinct advantages depending on the type of metal powder being produced and its intended application.
Types of Powder Making Devices
To understand the diversity of powder making devices, let’s break down some of the primary types and methods used in the industry:
- Atomization Devices: These machines use high-pressure gas or water jets to break molten metal into fine droplets, which then solidify into powders.
- Mechanical Comminution Devices: These use mechanical force to crush, grind, or shear solid metal into fine powders.
- Chemical Reduction Devices: These machines utilize chemical reactions to reduce metal oxides into fine metal powders.
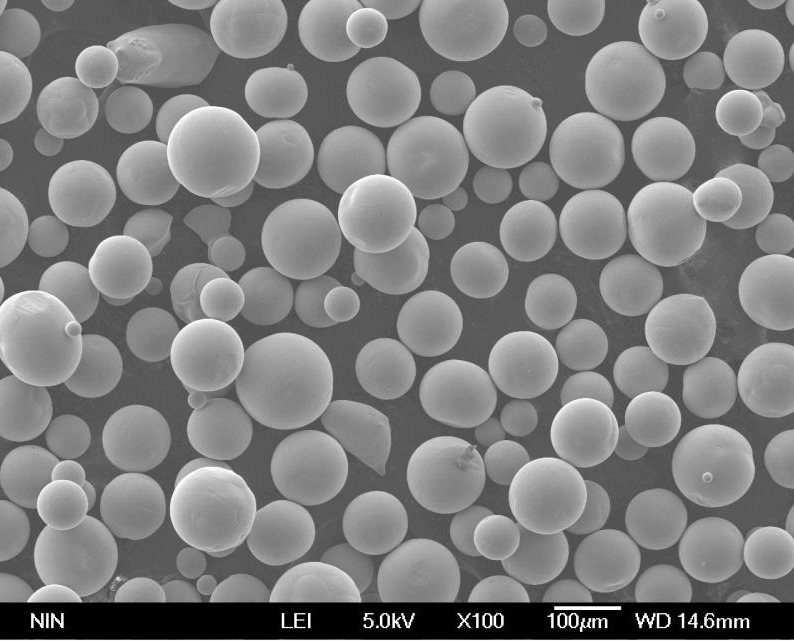
Key Characteristics of Powder Making Devices
Characteristic | Description |
---|---|
Powder Size | Ranges from nanometers to micrometers, depending on the device and process used. |
Production Rate | Varies significantly; some devices produce a few grams per hour, while others can produce several tons per day. |
Energy Consumption | Energy efficiency is crucial; some methods, like atomization, are more energy-intensive than others, like chemical reduction. |
Cost | Initial investment and operational costs vary widely based on the technology and scale of production. |
Material Compatibility | Different devices are compatible with various metals and alloys, from common ones like steel and aluminum to more exotic ones like titanium and nickel-based superalloys. |
Purity and Quality | The purity of the produced powder and its physical and chemical properties are critical for specific applications, requiring stringent control and monitoring. |
Environmental Impact | Some processes generate more waste and emissions than others, necessitating careful consideration of environmental regulations and sustainability practices. |
Metal Powder Models
Let’s explore ten specific metal powder models, each with its unique properties and applications.
1. Model X500: Aluminum Powder Device
Description: The Model X500 is an advanced atomization device specifically designed for producing high-quality aluminum powders.
Key Features:
- Powder Size: 10-50 micrometers
- Production Rate: Up to 500 kg/day
- Energy Efficiency: Moderate
- Applications: Aerospace components, automotive parts, and electronics.
2. Titanium T1000: Titanium Powder Device
Description: Ideal for creating fine titanium powders, this model uses advanced atomization technology to ensure high purity and consistent quality.
Key Features:
- Powder Size: 5-25 micrometers
- Production Rate: Up to 200 kg/day
- Energy Efficiency: High
- Applications: Medical implants, aerospace components, and high-performance automotive parts.
3. Steel S750: Stainless Steel Powder Device
Description: The Steel S750 is a robust device for producing stainless steel powders through mechanical comminution.
Key Features:
- Powder Size: 20-100 micrometers
- Production Rate: Up to 750 kg/day
- Energy Efficiency: Moderate
- Applications: Industrial tools, 3D printing, and construction materials.
4. Nickel N900: Nickel-Based Alloy Powder Device
Description: Specially designed for nickel-based superalloys, the Nickel N900 utilizes chemical reduction methods to produce high-purity powders.
Key Features:
- Powder Size: 10-40 micrometers
- Production Rate: Up to 300 kg/day
- Energy Efficiency: High
- Applications: Turbine blades, jet engines, and heat-resistant components.
5. Copper C550: Copper Powder Device
Description: The Copper C550 employs a combination of atomization and chemical reduction to produce high-quality copper powders.
Key Features:
- Powder Size: 15-70 micrometers
- Production Rate: Up to 500 kg/day
- Energy Efficiency: High
- Applications: Electrical components, heat sinks, and conductive inks.
6. Iron I800: Iron Powder Device
Description: This device uses mechanical comminution to produce iron powders suitable for various industrial applications.
Key Features:
- Powder Size: 20-100 micrometers
- Production Rate: Up to 800 kg/day
- Energy Efficiency: Moderate
- Applications: Magnetic materials, welding, and powder metallurgy.
7. Zinc Z450: Zinc Powder Device
Description: Utilizing advanced atomization, the Zinc Z450 is perfect for producing fine zinc powders.
Key Features:
- Powder Size: 10-50 micrometers
- Production Rate: Up to 450 kg/day
- Energy Efficiency: Moderate
- Applications: Galvanizing, battery production, and anti-corrosion coatings.
8. Magnesium M700: Magnesium Powder Device
Description: Designed for high-purity magnesium powders, the Magnesium M700 employs a combination of mechanical comminution and chemical reduction.
Key Features:
- Powder Size: 5-30 micrometers
- Production Rate: Up to 700 kg/day
- Energy Efficiency: High
- Applications: Aerospace components, automotive parts, and lightweight materials.
9. Cobalt C600: Cobalt Powder Device
Description: The Cobalt C600 uses chemical reduction to produce fine cobalt powders with excellent purity.
Key Features:
- Powder Size: 10-40 micrometers
- Production Rate: Up to 600 kg/day
- Energy Efficiency: High
- Applications: Battery electrodes, magnetic materials, and superalloys.
10. Silicon S1000: Silicon Powder Device
Description: This advanced device uses atomization to create fine silicon powders for high-tech applications.
Key Features:
- Powder Size: 1-10 micrometers
- Production Rate: Up to 1000 kg/day
- Energy Efficiency: Moderate
- Applications: Semiconductors, solar cells, and electronics.
Composition of Powder Making Devices
Understanding the composition of these devices is crucial for grasping their functionality and capabilities. Here’s a breakdown of the core components typically found in powder making devices.
Component | Function |
---|---|
Atomizer Nozzle | Used in atomization devices to create fine droplets of molten metal. |
Grinding Mill | Found in mechanical comminution devices, this component crushes and grinds solid metal into powders. |
Reduction Chamber | Used in chemical reduction devices to convert metal oxides into fine metal powders. |
Cooling System | Essential for solidifying metal droplets in atomization devices and controlling temperature in other devices. |
Feeder System | Ensures a consistent supply of raw material into the device. |
Collection Chamber | Where the produced metal powder is gathered and stored. |
Control Panel | Allows operators to monitor and adjust the device’s parameters, such as temperature, pressure, and feed rate. |
Filter System | Removes impurities and ensures the purity of the produced powder. |
Safety Mechanisms | Includes various safety features to prevent accidents and ensure smooth operation. |
Applications and Uses of Metal Powders
Metal powders produced by these devices have a wide range of applications across various industries. Here’s a look at some of the key uses:
Industry | Application |
---|---|
Aerospace | Manufacturing of lightweight components, turbine blades, and heat-resistant parts. |
Automotive | Production of high-performance parts, such as gears, bearings, and engine components. |
Medical Devices | Creation of biocompatible implants and surgical instruments. |
Electronics | Production of conductive inks, semiconductors, and other electronic components. |
Construction | Manufacturing of durable and corrosion-resistant building materials. |
Energy | Production of battery electrodes, solar cells, and fuel cells. |
Industrial Tools | Creation of cutting tools, abrasives, and other high-strength tools. |
3D Printing | Development of metal powders for additive manufacturing, enabling complex and custom designs. |
Magnetic Materials | Production of powders for magnetic applications, such as motors and transformers. |
Coatings | Creation of anti-corrosion, thermal barrier, and decorative coatings. |
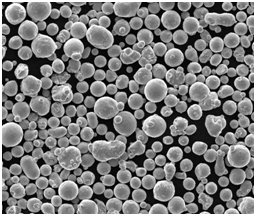
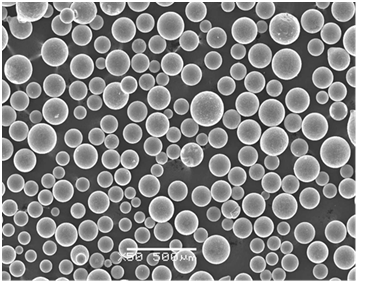
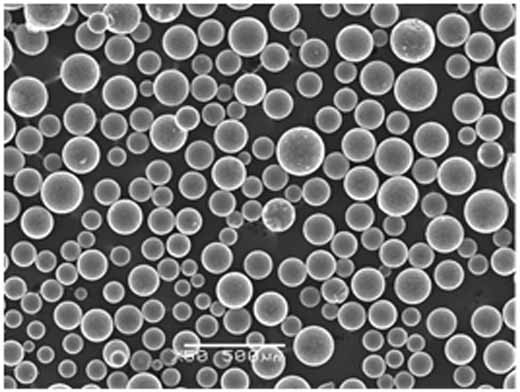
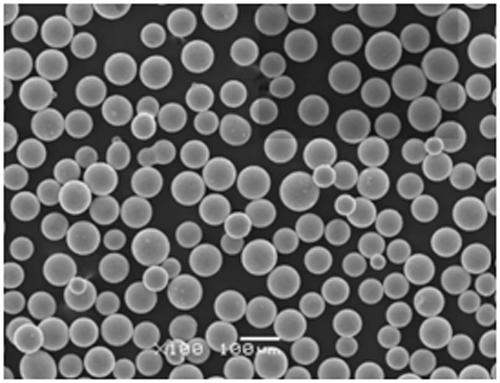
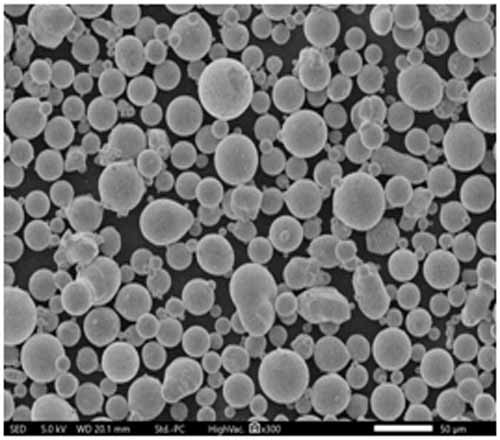
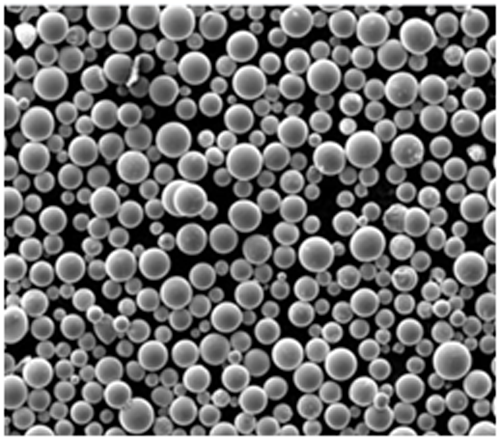
Specifications, Sizes, Grades, and Standards for Powder Making Devices
When it comes to powder making devices, there are numerous specifications and standards that define their performance and suitability for different applications. Here’s a detailed breakdown of these factors.
Specifications and Sizes of Powder Making Devices
Specification | Description |
---|---|
Powder Size Range | From nanometers to millimeters, depending on the device and process. |
Production Capacity | Varies from a few kilograms per day to several tons per day. |
Energy Requirements | Typically measured in kilowatts; varies based on the process and scale. |
Operational Temperature | Ranges from room temperature to several thousand degrees Celsius. |
Pressure Requirements | Some devices operate under high pressure; ranges from atmospheric to several hundred bars. |
Material Types | Metals, alloys, ceramics, and composites. |
Powder Purity | Ranges from standard grades to high purity for specialized applications. |
Grades of Metal Powders
Metal Powder | Common Grades | Characteristics |
---|---|---|
Aluminum | 6061, 7075, 2024 | High strength, lightweight, good corrosion resistance. |
Titanium | Ti-6Al-4V, Ti-5Al-2.5Sn | High strength-to-weight ratio, excellent corrosion resistance. |
Stainless Steel | 304, 316, 430 | Corrosion-resistant, durable, and versatile. |
Nickel | 200, 201, 600, 625 | High strength, resistant to high temperatures and oxidation. |
Copper | C11000, C26000, C86500 | High electrical and thermal conductivity, malleable. |
Iron | Fe, Fe3C, D2 | High tensile strength, versatile for various industrial uses. |
Zinc | Zn, ZnAl | Good corrosion resistance, used in galvanizing and batteries. |
Magnesium | AZ31, AZ91 | Lightweight, high strength-to-weight ratio. |
Cobalt | CoCr, CoNi | High temperature stability, used in superalloys and magnets. |
Silicon | 99.99%, 99.999% | Semiconductor properties, used in electronics and solar cells. |
Standards for Metal Powders
Standard | Description |
---|---|
ASTM B212 | Standard Specification for Atomized Aluminum Powder. |
ASTM B330 | Standard Specification for Titanium and Titanium Alloy Powders. |
ASTM B809 | Standard Specification for Stainless Steel Powder for Metal Injection Molding. |
ASTM B964 | Standard Specification for Nickel and Nickel Alloy Powders. |
ASTM B700 | Standard Specification for Copper Powder for Electrical Contacts. |
ASTM B243 | Standard Specification for Iron Powders for Powder Metallurgy Applications. |
ASTM B898 | Standard Specification for Zinc Powders. |
ASTM B660 | Standard Specification for Magnesium Powders. |
ASTM B809 | Standard Specification for Cobalt-based Alloys and Powders. |
ASTM B741 | Standard Specification for Silicon Powders. |
Suppliers and Pricing Details for Powder Making Devices
Choosing the right supplier for your powder making devices can be crucial to getting the best quality product at a reasonable price. Here’s a look at some leading suppliers and the price ranges for their devices.
Top Suppliers of Powder Making Devices
Supplier | Device Models | Price Range | Website |
---|---|---|---|
Höganäs AB | X500, S750 | $150,000 – $300,000 | Höganäs |
Atomizing Systems | T1000, C550 | $200,000 – $400,000 | Atomizing Systems |
LPW Technology | N900, S1000 | $120,000 – $250,000 | LPW Technology |
Heraeus | M700, Z450 | $180,000 – $350,000 | Heraeus |
Arcam EBM | Cobalt C600, Iron I800 | $300,000 – $600,000 | Arcam EBM |
Sandvik | Titanium T1000, Silicon S1000 | $250,000 – $500,000 | Sandvik |
Metal Powder Industries Federation (MPIF) | Various models | Varies by manufacturer | MPIF |
Praxis | Aluminum Powder Devices, Magnesium M700 | $100,000 – $250,000 | Praxis |
3D Systems | Powder Production for 3D Printing | $150,000 – $350,000 | 3D Systems |
Renishaw | Various Models for Advanced Applications | $200,000 – $450,000 | Renishaw |
Pros and Cons of Different Powder Making Devices
When selecting a powder making device, it’s important to weigh the advantages and disadvantages of each technology. Here’s a comparison of different methods and devices.
Advantages and Disadvantages of Powder Making Devices
Method/Device | Pros | Cons |
---|---|---|
Atomization | High purity powders, precise size control, scalable. | High energy consumption, expensive setup costs. |
Mechanical Comminution | Cost-effective, good for large-scale production. | Lower purity, less control over particle size. |
Chemical Reduction | Produces high-purity powders, suitable for advanced alloys. | Complex process, can be hazardous, requires precise conditions. |
Aluminum Powder Devices | Lightweight, high production rates. | Limited to aluminum and aluminum alloys. |
Titanium Powder Devices | High strength and purity, excellent for specialized applications. | High cost, energy-intensive. |
Stainless Steel Powder Devices | Versatile applications, strong and durable powders. | Limited to stainless steel, moderate cost. |
Nickel Powder Devices | High performance for demanding applications. | Expensive, can have environmental impacts. |
Copper Powder Devices | High conductivity, widely used in electronics. | Lower purity, less efficient for high-volume production. |
Iron Powder Devices | Cost-effective, versatile uses. | Lower performance in high-tech applications. |
Zinc Powder Devices | Good for corrosion resistance, versatile uses. | Limited to zinc powders, moderate cost. |
Magnesium Powder Devices | Lightweight, used in high-tech applications. | High cost, sensitive to environmental conditions. |
Cobalt Powder Devices | High temperature resistance, high performance. | Expensive, limited to specific applications. |
Silicon Powder Devices | Essential for electronics, high-tech applications. | Requires specialized processes, high cost. |
FAQ
Question | Answer |
---|---|
How do atomization devices work? | Atomization devices melt metal and then use gas or water jets to break it into fine droplets that solidify into powders. |
What types of metal powders can be produced? | Metal powders include aluminum, titanium, stainless steel, nickel, copper, and many more. |
How do mechanical comminution devices differ from chemical reduction devices? | Mechanical comminution involves physically breaking down metal, while chemical reduction uses chemical reactions. |
What factors influence the cost of powder making devices? | Factors include the production capacity, energy requirements, and the technology used in the device. |
Are there any environmental concerns with these devices? | Yes, some processes are energy-intensive and generate waste, requiring careful management and compliance with regulations. |
Can these devices be used for small-scale production? | Yes, there are models designed for both small-scale and large-scale production. |
Conclusion
In summary, powder making devices play a critical role in the production of metal powders used across various high-tech and industrial applications. From understanding the different types
of devices and their specifications, to exploring specific metal powder models and their applications, this guide provides a thorough overview of the field.
Choosing the right powder making device depends on numerous factors including the type of metal powder you need, the scale of production, and your budget. By considering the advantages and disadvantages of different methods and devices, you can make an informed decision that best meets your needs.
Whether you’re interested in high-purity titanium powders for aerospace applications or cost-effective iron powders for industrial use, there’s a device out there that’s perfect for the job. We hope this guide has been helpful in illuminating the fascinating world of powder making devices!
Feel free to reach out with more questions or dive deeper into any of the topics discussed here. Happy powder making.