Additive manufacturing has taken the world by storm, and the powder for PBF technique is a significant player in this revolution. This article dives deep into the world of metal powders used in PBF, exploring their types, compositions, characteristics, applications, and more. Whether you’re a seasoned professional or a curious beginner, this comprehensive guide will provide valuable insights and practical knowledge.
Overview of Powder for PBF Technique
Powder Bed Fusion (PBF) is a category of additive manufacturing that includes various technologies like Selective Laser Melting (SLM) and Electron Beam Melting (EBM). PBF involves fusing layers of powdered material to create complex and precise parts. The choice of metal powder is crucial as it directly affects the quality, strength, and performance of the final product.
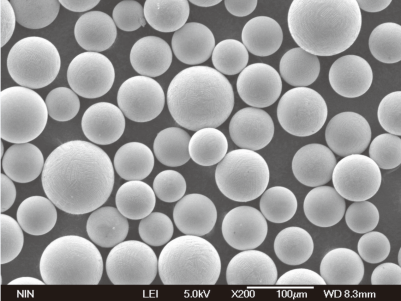
Types of Powder for PBF Technique
To better understand the landscape of metal powders used in PBF, let’s dive into specific models and their detailed descriptions.
Metal Powder | Composition | Properties | Applications |
---|---|---|---|
Ti-6Al-4V | Titanium alloy (90% Ti, 6% Al, 4% V) | High strength, low weight, corrosion-resistant | Aerospace, medical implants, automotive |
316L Stainless Steel | Iron alloy (16-18% Cr, 10-14% Ni, 2-3% Mo) | Corrosion-resistant, good mechanical properties | Medical devices, food processing equipment |
AlSi10Mg | Aluminum alloy (90% Al, 10% Si, 0.3-0.5% Mg) | Lightweight, good thermal properties | Automotive, aerospace, consumer goods |
Inconel 718 | Nickel alloy (50-55% Ni, 17-21% Cr, 4.75-5.5% Nb) | High temperature resistance, good weldability | Aerospace, energy, automotive |
Maraging Steel 1.2709 | Iron alloy (18% Ni, 9% Co, 5% Mo, 0.2% Ti) | High strength, hardness, and toughness | Tooling, aerospace, automotive |
CoCrMo | Cobalt alloy (60% Co, 27-30% Cr, 5-7% Mo) | Wear-resistant, biocompatible | Medical implants, dental applications |
Copper C18150 | Copper alloy (99.85% Cu, 0.15% Zr) | High thermal and electrical conductivity | Electrical components, thermal management |
AlSi12 | Aluminum alloy (87-89% Al, 10-12% Si) | High strength-to-weight ratio, good casting properties | Automotive, aerospace |
Hastelloy X | Nickel alloy (47-50% Ni, 20-23% Cr, 8-10% Mo) | Oxidation and corrosion-resistant at high temperatures | Aerospace, chemical processing |
Tool Steel H13 | Iron alloy (0.4% C, 5% Cr, 1.3% Mo, 1% V) | High wear resistance, thermal stability | Tooling, molds, dies |
Composition of Powder for PBF Technique
Understanding the composition of these metal powders is essential for selecting the right material for your project. Each powder’s unique blend of elements imparts specific properties that make it suitable for different applications.
Metal Powder | Main Elements | Secondary Elements | Impurities |
---|---|---|---|
Ti-6Al-4V | Titanium, Aluminum, Vanadium | Iron, Oxygen | Carbon, Nitrogen |
316L Stainless Steel | Iron, Chromium, Nickel | Molybdenum, Manganese, Silicon | Phosphorus, Sulfur |
AlSi10Mg | Aluminum, Silicon, Magnesium | Iron, Copper | Titanium, Zinc |
Inconel 718 | Nickel, Chromium, Niobium | Molybdenum, Titanium, Aluminum | Carbon, Cobalt |
Maraging Steel 1.2709 | Iron, Nickel, Cobalt, Molybdenum | Titanium, Aluminum | Carbon, Silicon |
CoCrMo | Cobalt, Chromium, Molybdenum | Nickel, Iron | Manganese, Silicon |
Copper C18150 | Copper, Zirconium | – | Iron, Lead |
AlSi12 | Aluminum, Silicon | Iron, Copper | Manganese, Zinc |
Hastelloy X | Nickel, Chromium, Molybdenum | Iron, Cobalt | Manganese, Silicon |
Tool Steel H13 | Iron, Chromium, Molybdenum, Vanadium | Carbon, Silicon, Manganese | Phosphorus, Sulfur |
Characteristics of Powder for PBF Technique
Each type of metal powder used in PBF has distinct characteristics that make it suitable for specific applications. Here, we explore these properties in detail.
Metal Powder | Density (g/cm³) | Melting Point (°C) | Tensile Strength (MPa) | Elongation (%) | Hardness (HV) |
---|---|---|---|---|---|
Ti-6Al-4V | 4.43 | 1660 | 900-1100 | 10-15 | 330 |
316L Stainless Steel | 7.99 | 1375-1400 | 480-620 | 30-40 | 200 |
AlSi10Mg | 2.68 | 570-580 | 300-350 | 5-10 | 120 |
Inconel 718 | 8.19 | 1260-1336 | 965-1241 | 10-20 | 330 |
Maraging Steel 1.2709 | 8.0 | 1413 | 2000-2500 | 5-10 | 500 |
CoCrMo | 8.29 | 1330-1390 | 900-1300 | 10-20 | 500 |
Copper C18150 | 8.96 | 1083 | 350-410 | 20-30 | 110 |
AlSi12 | 2.68 | 570-580 | 200-300 | 5-10 | 80 |
Hastelloy X | 8.22 | 1260-1350 | 700-1000 | 30-40 | 200 |
Tool Steel H13 | 7.80 | 1425-1530 | 1000-1200 | 10-15 | 600 |
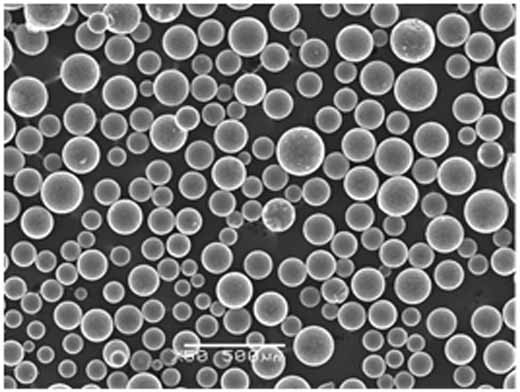
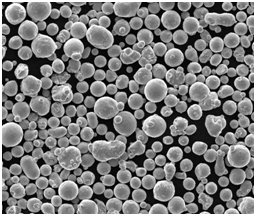
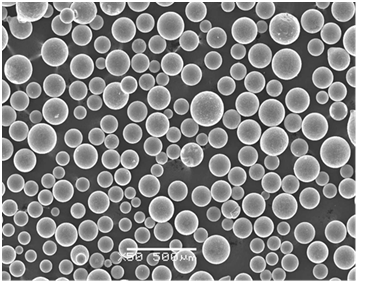
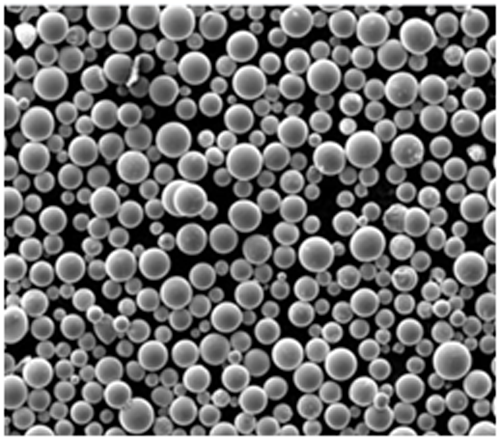
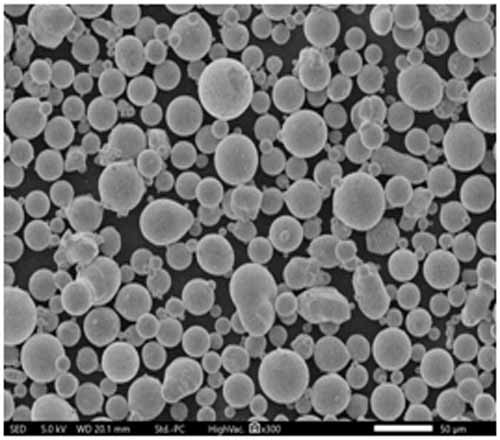
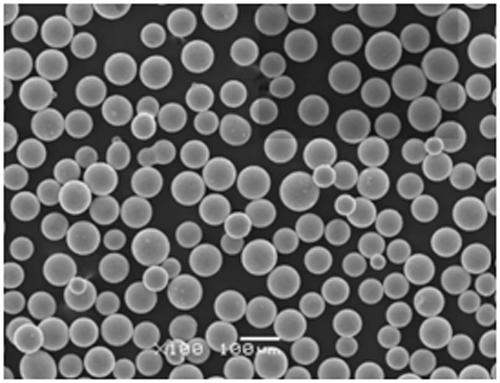
Applications of Powder for PBF Technique
Metal powders for PBF have diverse applications across various industries. Here’s a closer look at where each type of powder excels.
Metal Powder | Industry | Specific Applications |
---|---|---|
Ti-6Al-4V | Aerospace, Medical | Aircraft components, implants |
316L Stainless Steel | Medical, Food | Surgical instruments, food processing equipment |
AlSi10Mg | Automotive, Aerospace | Lightweight parts, prototypes |
Inconel 718 | Aerospace, Energy | Turbine blades, rocket engines |
Maraging Steel 1.2709 | Tooling, Aerospace | High-strength tools, structural components |
CoCrMo | Medical, Dental | Joint replacements, dental prosthetics |
Copper C18150 | Electrical, Thermal | Electrical connectors, heat exchangers |
AlSi12 | Automotive, Aerospace | Engine components, brackets |
Hastelloy X | Aerospace, Chemical | Combustion chambers, chemical reactors |
Tool Steel H13 | Tooling, Molding | Injection molds, die casting dies |
Grades of Powder for PBF Technique
Different grades of metal powders ensure the right material is chosen for specific applications. Here are some of the available grades for commonly used powders.
Metal Powder | Grades | Description |
---|---|---|
Ti-6Al-4V | Grade 5, Grade 23 | Standard and extra-low interstitial versions |
316L Stainless Steel | 316L, 316LVM | Low carbon and vacuum melted versions |
AlSi10Mg | Standard | Commonly used grade |
Inconel 718 | AMS 5662, AMS 5663 | Aerospace and high-temperature grades |
Maraging Steel 1.2709 | Standard | Commonly used grade |
CoCrMo | F75, F1537 | Medical implant grades |
Copper C18150 | Standard | Commonly used grade |
AlSi12 | Standard | Commonly used grade |
Hastelloy X | AMS 5754, UNS N06002 | High-temperature and corrosion-resistant grades |
Tool Steel H13 | Standard, H13 ESR | Common and electro-slag refined versions |
Specifications, Sizes, and Standards
Each type of metal powder comes with specific standards and sizes to meet industry requirements.
Metal Powder | Particle Size (µm) | Standards | Supplier | Price (per kg) |
---|---|---|---|---|
Ti-6Al-4V | 15-45 | ASTM B348, ASTM F2924 | EOS, Arcam, AP&C | $300 – $500 |
316L Stainless Steel | 15-45 | ASTM A276, ASTM F138 | GKN, Sandvik, Carpenter | $100 – $150 |
AlSi10Mg | 20-63 | DIN EN 1706, ASTM B361 | SLM Solutions, EOS | $80 – $120 |
Inconel 718 | 15-45 | AMS 5662, AMS 5663 | Praxair, Sandvik, LPW | $150 – $250 |
Maraging Steel 1.2709 | 15-45 | AMS 6512 | Carpenter, Sandvik | $200 – $300 |
CoCrMo | 20-63 | ASTM F75, ASTM F1537 | Carpenter, EOS | $200 – $400 |
Copper C18150 | 15-45 | ASTM B124, ASTM B152 | Sandvik, Carpenter | $50 – $100 |
AlSi12 | 20-63 | DIN EN 1706 | EOS, SLM Solutions | $70 – $110 |
Hastelloy X | 15-45 | AMS 5754, UNS N06002 | Praxair, Sandvik | $200 – $300 |
Tool Steel H13 | 20-63 | ASTM A681 | Carpenter, Sandvik | $100 – $200 |
Pros and Cons of Powder for PBF Technique
When choosing the right metal powder, it’s essential to weigh the advantages and disadvantages of each option.
Metal Powder | Pros | Cons |
---|---|---|
Ti-6Al-4V | High strength-to-weight ratio, corrosion-resistant | Expensive, challenging to process |
316L Stainless Steel | Excellent corrosion resistance, biocompatible | Lower strength compared to some alloys |
AlSi10Mg | Lightweight, good thermal conductivity | Lower strength and hardness |
Inconel 718 | High-temperature resistance, good weldability | Expensive, difficult to machine |
Maraging Steel 1.2709 | Extremely high strength, good machinability | Expensive, requires heat treatment |
CoCrMo | High wear resistance, biocompatible | Expensive, challenging to process |
Copper C18150 | Excellent thermal and electrical conductivity | Soft, prone to wear |
AlSi12 | Good casting properties, lightweight | Lower strength and hardness |
Hastelloy X | Excellent oxidation and corrosion resistance | Expensive, difficult to machine |
Tool Steel H13 | High wear resistance, thermal stability | Expensive, requires heat treatment |
Choosing the Right Powder for PBF
Selecting the right powder involves considering several factors including material properties, application requirements, and cost. Here’s a comparison to help you decide.
Factor | Ti-6Al-4V | 316L Stainless Steel | AlSi10Mg | Inconel 718 | Maraging Steel 1.2709 | CoCrMo | Copper C18150 | AlSi12 | Hastelloy X | Tool Steel H13 |
---|---|---|---|---|---|---|---|---|---|---|
Strength | High | Medium | Medium | High | Very High | High | Medium | Medium | High | High |
Weight | Low | Medium | Low | Medium | Medium | High | High | Low | High | Medium |
Corrosion Resistance | High | Very High | Medium | High | Medium | Very High | Low | Medium | Very High | Medium |
Thermal Conductivity | Medium | Low | High | Medium | Low | Low | Very High | High | Medium | Low |
Cost | High | Medium | Low | High | High | High | Low | Low | High | Medium |
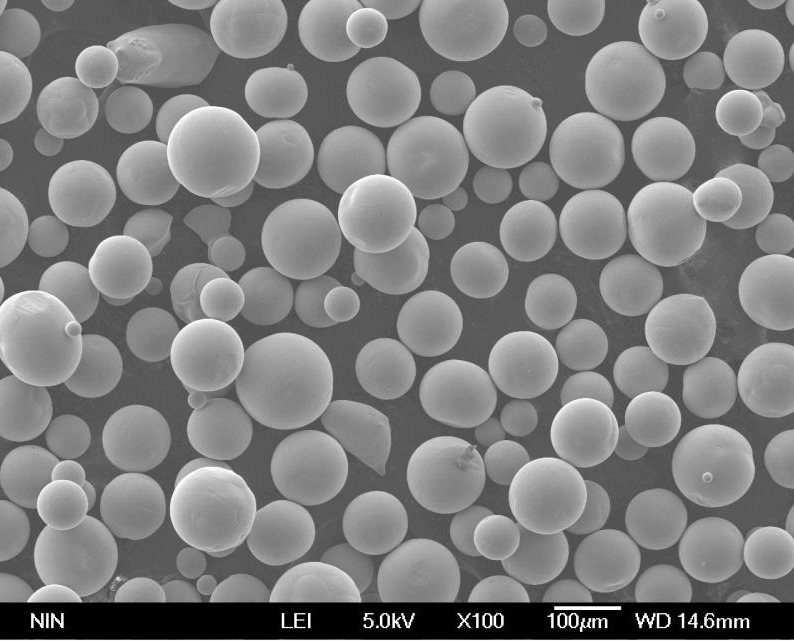
FAQs
Question | Answer |
---|---|
What is PBF in additive manufacturing? | PBF (Powder Bed Fusion) is a type of additive manufacturing where a heat source, such as a laser or electron beam, fuses powdered material layer by layer to create a 3D object. |
What are the main types of PBF? | The main types of PBF are Selective Laser Melting (SLM) and Electron Beam Melting (EBM). SLM uses a laser as the heat source, while EBM uses an electron beam. |
Why is the choice of powder important? | The choice of powder affects the mechanical properties, surface finish, and overall quality of the printed part. Different powders offer varying levels of strength, thermal conductivity, corrosion resistance, and other properties that are crucial for specific applications. |
How is powder quality controlled? | Powder quality is controlled through various measures such as particle size distribution, chemical composition, and purity. Manufacturers use standards like ASTM and ISO to ensure consistency and reliability in their powders. |
Can different powders be mixed? | Generally, mixing different powders is not recommended as it can lead to inconsistent properties and poor part quality. However, in some research and experimental setups, tailored blends may be used to achieve specific properties. |
What are the common challenges with PBF? | Common challenges include powder recycling, controlling porosity, achieving consistent layer bonding, and managing residual stresses. Advanced techniques and careful process control are essential to overcome these challenges. |
How is powder recycled in PBF? | Unused powder can be collected and reused in subsequent builds, but it must be carefully sieved and tested to ensure it meets quality standards. Over time, recycled powder may degrade, requiring fresh powder to be mixed in to maintain quality. |
What are the environmental impacts? | PBF techniques can be more sustainable than traditional manufacturing methods due to reduced material waste and the ability to recycle powder. However, the energy consumption of the machines and the need for inert gas environments (in some cases) can have environmental impacts that need to be managed. |
Which industries benefit the most from PBF? | Aerospace, medical, and automotive industries benefit significantly from PBF due to the ability to produce complex, high-strength, and lightweight parts that are difficult or impossible to make using traditional manufacturing methods. |
How do I choose the right powder for my project? | Consider the specific requirements of your application, such as mechanical properties, thermal conductivity, corrosion resistance, and cost. Review material data sheets and consult with powder suppliers or experts to make an informed decision. |
Conclusion
Navigating the world of metal powders for the PBF technique can be complex, but understanding the types, compositions, characteristics, and applications of these powders is crucial. By weighing the pros and cons and considering the specific needs of your project, you can make an informed decision that ensures the success of your additive manufacturing endeavors. The future of manufacturing is undoubtedly bright with the continuous advancements in PBF technology and metal powder development.