Welcome to the comprehensive guide on powder making equipment process! Whether you’re a novice in the field or a seasoned professional, this article aims to provide in-depth insights into the intricacies of powder making, from the types of equipment used to the specific processes involved. So, buckle up as we dive deep into the world of powder making!
Overview of Powder Making Equipment Process
The powder making process involves converting solid materials into fine particles or powders. This process is essential in various industries, including pharmaceuticals, metallurgy, ceramics, and food processing. The equipment used in powder making is designed to handle different materials and achieve specific particle sizes, ensuring the final product meets the required standards.
Key Components of Powder Making Equipment:
- Grinding Mills: Reduce the size of materials through mechanical means.
- Mixers: Blend different powders to achieve a uniform composition.
- Spray Dryers: Convert liquid slurries into dry powders.
- Granulators: Form larger, uniform particles from powders.
- Classifiers: Separate particles based on size.
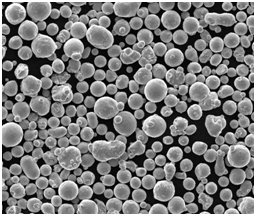
Types of Powder Making Equipment
To understand the powder making process, it’s essential to know the different types of equipment involved. Here’s a detailed look at the primary types:
Grinding Mills
Ball Mill: Utilizes balls as grinding media to break down materials.
Jet Mill: Uses high-speed jets of gas to grind materials.
Hammer Mill: Employs rotating hammers to pulverize materials.
Mixers
Ribbon Blender: Mixes powders in a U-shaped trough with a ribbon agitator.
V-Blender: Utilizes a V-shaped container for gentle blending.
Double Cone Blender: Combines materials by rotating a double cone container.
Spray Dryers
Centrifugal Spray Dryer: Uses a rotating disc to atomize liquids into fine droplets.
Pressure Spray Dryer: Forces liquid through a nozzle to create fine droplets.
Granulators
Fluid Bed Granulator: Fluidizes powder particles and binds them with a granulating liquid.
High Shear Granulator: Uses high-speed blades to mix and granulate powders.
Classifiers
Air Classifier: Separates particles based on size using a high-speed air stream.
Vibrating Classifier: Utilizes vibration to sort particles by size.
Composition of Powder Making Equipment Process
The composition of the powder making equipment process is crucial as it determines the efficiency and quality of the final product. Here’s a breakdown of the primary components:
Equipment Type | Main Components | Functionality |
---|---|---|
Grinding Mills | Grinding media, rotating drum | Size reduction through impact and attrition |
Mixers | Mixing blades, motor, mixing chamber | Homogenizing different powders |
Spray Dryers | Atomizer, drying chamber, cyclone | Drying liquid slurries into powders |
Granulators | Mixing blades, granulating liquid | Forming larger particles from powders |
Classifiers | Airflow system, sieves | Particle size separation |
Applications of Powder Making Equipment
Powder making equipment is used across various industries, each with unique applications. Here’s a look at some of the common uses:
Industry | Application |
---|---|
Pharmaceuticals | Producing medicinal powders |
Metallurgy | Creating metal powders for sintering |
Ceramics | Making ceramic powders |
Food Processing | Producing powdered food products |
Chemical | Manufacturing powdered chemicals |
Specifications, Sizes, Grades, Standards
When selecting powder making equipment, it’s essential to consider the specifications, sizes, grades, and standards to ensure optimal performance and compliance with industry requirements.
Equipment Type | Specifications | Sizes | Grades | Standards |
---|---|---|---|---|
Grinding Mills | Speed, capacity, power | Small to large | Industrial, laboratory | ASTM, ISO, DIN |
Mixers | Speed, volume, material | Various | Industrial, laboratory | FDA, GMP, ISO |
Spray Dryers | Temperature, capacity | Various | Industrial, laboratory | CE, ISO, ASME |
Granulators | Speed, capacity, size | Various | Industrial, laboratory | cGMP, FDA, EMA |
Classifiers | Size range, capacity | Various | Industrial, laboratory | ASTM, ISO |
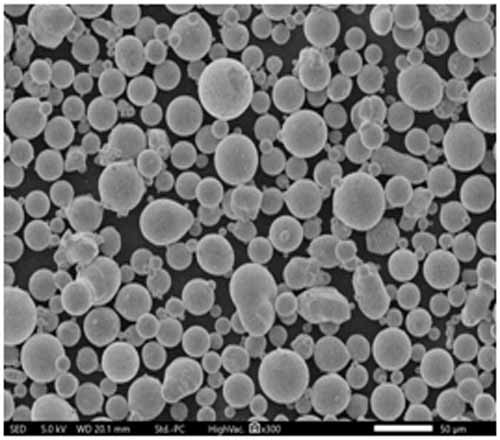
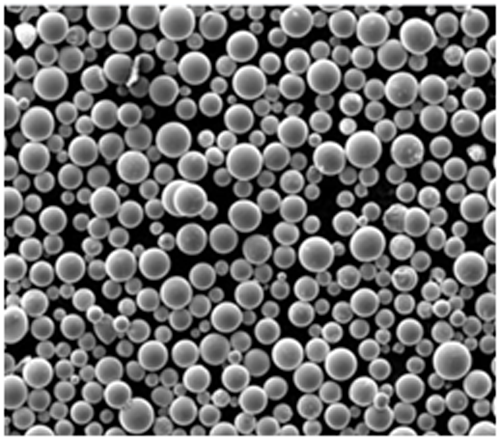
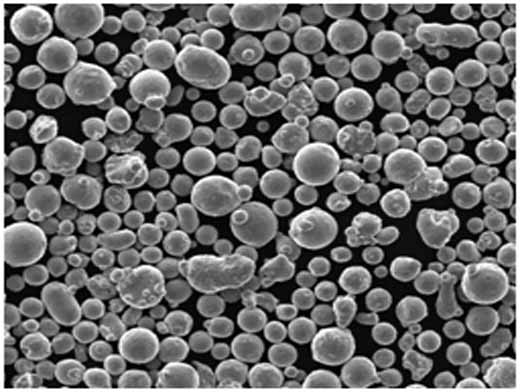
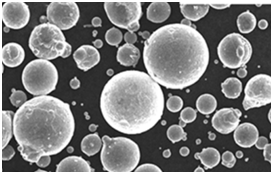
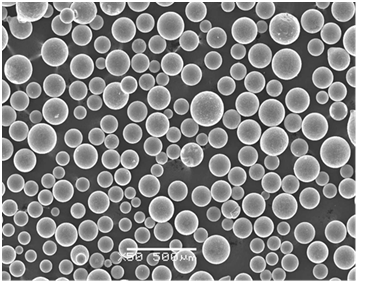
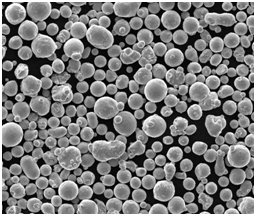
Suppliers and Pricing Details
Finding the right supplier and understanding the pricing structure is crucial for making an informed decision. Here’s a table with some notable suppliers and indicative pricing:
Equipment Type | Supplier | Price Range (USD) | Location |
---|---|---|---|
Grinding Mills | Hosokawa Micron | 10,000 – 150,000 | USA, Japan |
Mixers | Patterson Kelley | 5,000 – 100,000 | USA |
Spray Dryers | GEA Group | 50,000 – 500,000 | Germany, USA |
Granulators | Glatt GmbH | 20,000 – 200,000 | Germany |
Classifiers | Prater Industries | 10,000 – 100,000 | USA |
Comparing Pros and Cons of Powder Making Equipment
Choosing the right powder making equipment involves weighing the pros and cons of each type. Here’s a comparison to help you make an informed decision:
Equipment Type | Advantages | Disadvantages |
---|---|---|
Grinding Mills | Efficient size reduction, versatile | High energy consumption, noise |
Mixers | Homogeneous mixing, various types | Possible contamination, maintenance |
Spray Dryers | High efficiency, consistent output | High cost, large footprint |
Granulators | Uniform particle size, scalable | Complex process, expensive |
Classifiers | Accurate separation, adjustable | Can be complex to set up, costly |
In-Depth Look at Specific Metal Powder Models
Now, let’s explore some specific metal powder models, detailing their unique features and applications:
1. Iron Powder (ASC100.29)
Description: ASC100.29 is a high-purity iron powder used extensively in metallurgy and chemical applications. It offers excellent compressibility and sintering properties.
Applications: Automotive parts, magnetic materials, chemical reagents.
2. Aluminum Powder (Alpoco)
Description: Alpoco produces high-quality aluminum powder known for its lightweight and high reactivity. It’s used in various applications, including pyrotechnics and additive manufacturing.
Applications: Aerospace components, fireworks, 3D printing.
3. Copper Powder (Cu-1599)
Description: Cu-1599 is a finely ground copper powder used in electrical and thermal conductivity applications. It’s prized for its high purity and consistent particle size.
Applications: Electrical contacts, conductive inks, metallurgy.
4. Titanium Powder (Ti-6Al-4V)
Description: Ti-6Al-4V is a titanium alloy powder renowned for its high strength-to-weight ratio and corrosion resistance. It’s widely used in aerospace and medical implants.
Applications: Aerospace components, medical devices, high-performance engineering.
5. Stainless Steel Powder (316L)
Description: 316L stainless steel powder is known for its excellent corrosion resistance and mechanical properties, making it ideal for demanding environments.
Applications: Surgical instruments, marine applications, 3D printing.
6. Nickel Powder (Ni-1234)
Description: Ni-1234 nickel powder is used in applications requiring high-temperature resistance and excellent corrosion properties.
Applications: Battery electrodes, superalloys, electroplating.
7. Zinc Powder (Zn-2456)
Description: Zn-2456 is a high-purity zinc powder used in galvanizing and battery production. It’s known for its excellent reactivity and fine particle size.
Applications: Battery anodes, galvanizing, chemical synthesis.
8. Cobalt Powder (Co-3301)
Description: Co-3301 cobalt powder is used in high-performance alloys and magnetic materials, valued for its strength and magnetic properties.
Applications: Superalloys, permanent magnets, rechargeable batteries.
9. Tungsten Powder (W-2000)
Description: W-2000 tungsten powder is characterized by its high density and melting point, making it suitable for extreme applications.
Applications: Electrical contacts, radiation shielding, high-temperature components.
10. Molybdenum Powder (Mo-7650)
Description: Mo-7650 molybdenum powder is used in applications requiring high strength and resistance to high temperatures and corrosion.
Applications: Alloying agent, electronics, high-temperature furnaces.
Characteristics of Powder Making Equipment Process
Understanding the characteristics of the powder making process is essential for selecting the right equipment and optimizing production.
Characteristic | Description |
---|---|
Particle Size Distribution | Ensures consistency and quality of the final product |
Purity | High purity powders are essential for specific applications |
Flowability | Influences the ease of handling and processing |
Compressibility | Affects the ability to form solid parts from powders |
Sintering Properties | Determines the efficiency of the sintering process |
Grades of Powder Making Equipment Process
Different grades of powders are produced to meet various industry standards and requirements. Here’s a look at the
common grades:
Grade | Application | Characteristics |
---|---|---|
Pharmaceutical | Medicinal powders | High purity, fine particle size |
Industrial | Metallurgy, manufacturing | High strength, uniform particle size |
Food | Food processing | Safe, contaminant-free, consistent quality |
Chemical | Chemical synthesis | Reactive, high purity |
Optimizing the Powder Making Equipment Process
Optimizing the powder making process involves fine-tuning various parameters to achieve the desired product quality and efficiency. Here are some key strategies:
- Control Particle Size: Adjust grinding and classification parameters to achieve the desired particle size distribution.
- Ensure Purity: Implement stringent quality control measures to maintain high purity levels.
- Enhance Flowability: Use additives or modify particle shapes to improve powder flow characteristics.
- Optimize Sintering: Fine-tune temperature and time settings to enhance sintering properties.
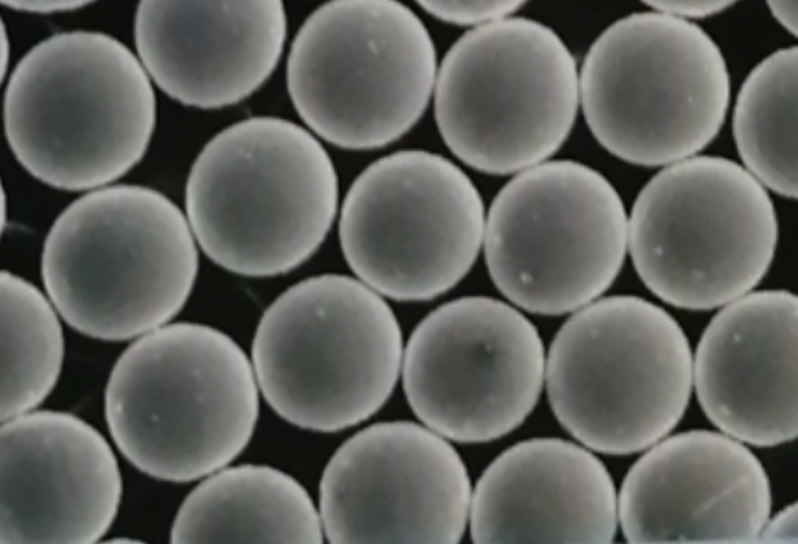
FAQs
What is the primary purpose of powder making equipment?
Answer: The primary purpose of powder making equipment is to convert solid materials into fine powders, ensuring the final product meets the required specifications for various applications.
What factors should be considered when selecting powder making equipment?
Answer: Key factors include the type of material, desired particle size, production capacity, purity requirements, and specific application needs.
How do grinding mills differ from mixers in the powder making process?
Answer: Grinding mills are used to reduce the size of materials through mechanical means, while mixers blend different powders to achieve a uniform composition.
What are the advantages of using spray dryers in the powder making process?
Answer: Spray dryers offer high efficiency, consistent output, and the ability to convert liquid slurries into fine powders.
What is the role of classifiers in the powder making process?
Answer: Classifiers separate particles based on size, ensuring the final powder has a uniform particle size distribution.
How can the purity of powders be maintained in the powder making process?
Answer: Purity can be maintained through stringent quality control measures, proper equipment maintenance, and using high-purity raw materials.
What industries commonly use powder making equipment?
Answer: Industries such as pharmaceuticals, metallurgy, ceramics, food processing, and chemicals commonly use powder making equipment.
What are the challenges associated with the powder making process?
Answer: Challenges include controlling particle size distribution, maintaining purity, ensuring consistent quality, and optimizing production efficiency.
How does the choice of grinding media affect the powder making process?
Answer: The choice of grinding media affects the efficiency of the size reduction process, the final particle size, and the purity of the powder.
What is the significance of particle size distribution in the powder making process?
Answer: Particle size distribution is crucial for ensuring the consistency, quality, and performance of the final powder in its intended application.
Can powder making equipment be customized for specific applications?
Answer: Yes, powder making equipment can be customized to meet specific application requirements, such as desired particle size, production capacity, and purity standards.
And there you have it! A detailed, SEO-optimized guide on the powder making equipment process. This article provides a comprehensive overview, delves into the types and characteristics of the equipment, and explores specific metal powder models, ensuring you have all the information needed to understand this intricate process. Whether you’re looking to enhance your knowledge or make informed decisions in your field, this guide has got you covered.