Nickel-chromium alloys are integral in various industrial applications, particularly due to their superior resistance to heat, corrosion, and wear. The NiCr 80/20 Powder, consisting of 80% nickel and 20% chromium, stands out as a popular choice in this category for its wide-ranging capabilities. But why is it so highly regarded? Let’s dive into a comprehensive look at the world of NiCr 80/20 Powder.
Overview of NiCr 80/20 Powder
NiCr 80/20 Powder is a metal alloy powder composed primarily of nickel (80%) and chromium (20%). Its distinct properties, such as excellent oxidation resistance, high melting point, and superior mechanical strength, make it an essential material in industries ranging from aerospace to electronics.
The composition of NiCr 80/20 enables it to withstand extreme temperatures and corrosive environments, making it ideal for demanding applications like thermal spraying, manufacturing of heating elements, and gas turbine components.
What Makes NiCr 80/20 Powder Special?
When you think about material innovation, NiCr 80/20 represents a perfect balance of durability and versatility. Nickel brings corrosion resistance and toughness to the table, while chromium provides the alloy with heat resistance and stability. Whether used in harsh environments or extreme heat, this alloy shows resilience, making it a go-to material for numerous high-performance tasks.
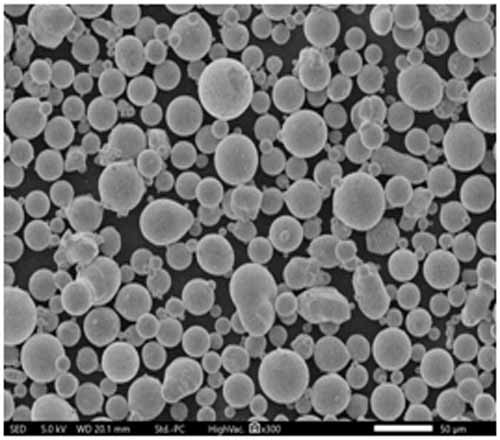
Composition of NiCr 80/20 Powder
To understand the science behind NiCr 80/20 Powder, let’s start by looking at its composition. As its name suggests, it contains 80% nickel and 20% chromium, but that’s not all. Other trace elements may also play a role in enhancing specific properties, making this alloy a highly versatile material.
Component | Percentage |
---|---|
Nickel (Ni) | 80% |
Chromium (Cr) | 20% |
Other Elements | <0.2% |
This combination produces a material that exhibits remarkable resistance to oxidation and corrosion, as well as high mechanical strength, even at elevated temperatures.
Characteristics of NiCr 80/20 Powder
The NiCr 80/20 Powder offers a variety of properties that make it ideal for numerous applications. Below are the primary characteristics that define its performance.
Property | Details |
---|---|
Oxidation Resistance | Exceptional resistance to oxidation at high temperatures, up to 1200°C. |
Thermal Conductivity | Moderately high thermal conductivity, making it suitable for thermal applications. |
Mechanical Strength | Maintains strength and durability, even under mechanical stress. |
Corrosion Resistance | Resilient against corrosive gases and chemicals. |
Electrical Resistivity | High electrical resistivity, making it valuable in electric heating applications. |
This wide range of properties sets NiCr 80/20 apart from other metal powders, making it a highly sought-after material in industries requiring high performance under extreme conditions.
Top NiCr 80/20 Powder Models
When selecting a specific model of NiCr 80/20 Powder, it’s essential to consider both the application and the desired outcome. Below are ten popular models of NiCr 80/20 Powder, each offering slightly different properties tailored to various industries and uses.
Model | Description |
---|---|
NiCr 80/20 T-80 | Standard version used for thermal spray coating. Offers optimal resistance to wear and oxidation. |
NiCr 80/20 S-45 | Specially designed for wire and strip form. Ideal for high-temperature heating elements. |
NiCr 80/20 X-100 | High-performance powder with superior electrical resistivity for electric heating applications. |
NiCr 80/20 P-75 | Preferred in the aerospace industry due to its durability in extreme environments. |
NiCr 80/20 F-300 | Fine-grained powder for precision thermal spray applications. |
NiCr 80/20 C-200 | Highly corrosion-resistant, suited for marine and chemical plant environments. |
NiCr 80/20 A-50 | Excellent thermal and electrical properties, making it a top choice for automotive and power generation industries. |
NiCr 80/20 G-500 | Offers increased mechanical strength at high temperatures, designed for gas turbine applications. |
NiCr 80/20 H-60 | Noted for high resistance to thermal fatigue, often used in heat exchanger systems. |
NiCr 80/20 M-90 | Optimal for additive manufacturing and 3D printing applications, where fine precision is required. |
Each model caters to specific industrial needs, whether it’s superior corrosion resistance, high mechanical strength, or enhanced conductivity. The right model depends on your specific application.
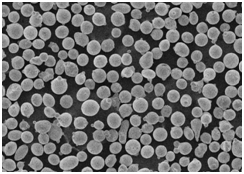
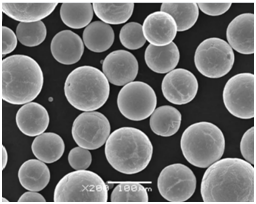
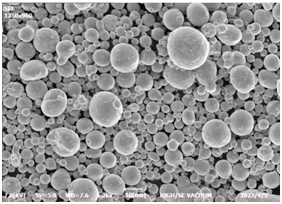
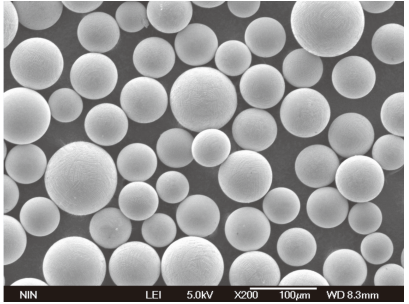
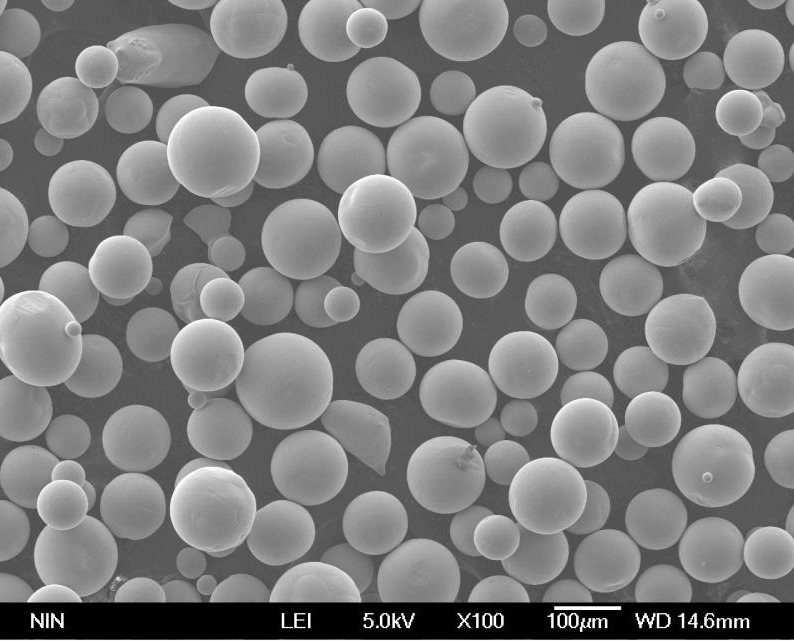
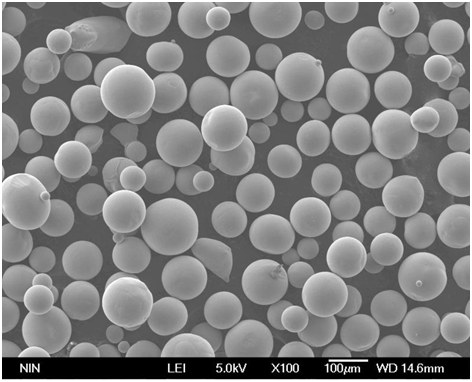
Applications of NiCr 80/20 Powder
NiCr 80/20 Powder’s unique composition and properties make it suitable for a vast array of industrial applications. Here’s a closer look at some common uses.
Industry | Applications |
---|---|
Aerospace | Used in gas turbines, aircraft engines, and exhaust systems. |
Electronics | Employed in the production of electric resistors and heating elements. |
Automotive | Widely used in catalytic converters, sensors, and exhaust systems. |
Marine | Provides corrosion resistance for marine vessels and offshore platforms. |
Chemical Processing | Utilized in the manufacturing of chemical plant components like reactors. |
Power Generation | Key material in the construction of heat exchangers and power station equipment. |
Thermal Spraying | Applied to coat surfaces with protective layers for wear and corrosion resistance. |
Specifications, Sizes, and Grades of NiCr 80/20 Powder
NiCr 80/20 Powder comes in various specifications, sizes, and grades depending on the application requirements. Below is a comprehensive table of these specifications:
Specification | Details |
---|---|
Powder Size | 15-150 microns |
Grade | Industrial-grade, Aerospace-grade |
Melting Point | 1350°C – 1400°C |
Density | 8.4 g/cm³ |
Standards | ASTM B23, AMS 5662, ISO 9001:2015 certified |
Particle Shape | Spherical |
Purity | ≥99% purity |
Depending on your requirements, the grade and size of the NiCr 80/20 Powder you choose can significantly impact its performance in your particular application.
Comparison of NiCr 80/20 Powder with Other Metal Powders
When choosing the right metal powder for your needs, understanding how NiCr 80/20 compares to other metal powders is crucial. Let’s break down the pros and cons of NiCr 80/20 versus other alternatives.
Metal Powder | Advantages | Limitations |
---|---|---|
NiCr 80/20 Powder | Excellent heat resistance, corrosion resistance | Higher cost compared to common alloys |
316 Stainless Steel | Lower cost, good corrosion resistance | Less effective at high temperatures |
Inconel 625 | Superior strength and corrosion resistance | More expensive than NiCr 80/20 |
Aluminum Powder | Lightweight, cost-effective | Poor performance at high temperatures |
Titanium Powder | High strength-to-weight ratio, excellent corrosion resistance | Expensive and harder to process |
As you can see, NiCr 80/20 Powder excels in applications that demand heat resistance and durability. However, if cost or weight is a primary concern, you might consider alternatives like aluminum or stainless steel.
Suppliers and Pricing of NiCr 80/20 Powder
There are several reliable suppliers of NiCr 80/20 Powder across the globe. Here’s a breakdown of some of the top suppliers, including pricing details.
Supplier | Price Range | Location | Notes |
---|---|---|---|
Höganäs AB | $50-$120 per kg | Sweden | Known for high-quality, consistent supply |
Sandvik Materials | $60-$130 per kg | United States | Offers aerospace-grade powder |
AMETEK SMP | $55-$125 per kg | United Kingdom | Specializes in additive manufacturing |
LPW Technology | $48-$115 per kg | Germany | Provides various particle sizes |
Tekna Plasma Systems | $52-$122 per kg | Canada | Known for uniform particle distribution |
Prices may vary depending on quantity, grade, and the specific model you’re purchasing.
Advantages of NiCr 80/20 Powder
The advantages of NiCr 80/20 Powder go beyond just heat and corrosion resistance. Here are some key benefits:
- Durability in Extreme Conditions: Whether it’s high heat or corrosive environments, NiCr 80/20 can handle the challenge.
- Electrical Resistivity: Ideal for heating elements in various applications.
- Oxidation Resistance: Perfect for applications that face prolonged exposure to oxygen at elevated temperatures.
- Versatile Applications: From aerospace to electronics, it serves a multitude of industries.
Limitations of NiCr 80/20 Powder
While it’s an exceptional material, it does have its limitations:
- Cost: More expensive compared to common alloys like stainless steel.
- Machinability: NiCr 80/20 Powder can be harder to process, especially in additive manufacturing.
- Weight: Compared to aluminum or titanium, it is relatively heavy, which might limit its use in weight-sensitive applications.
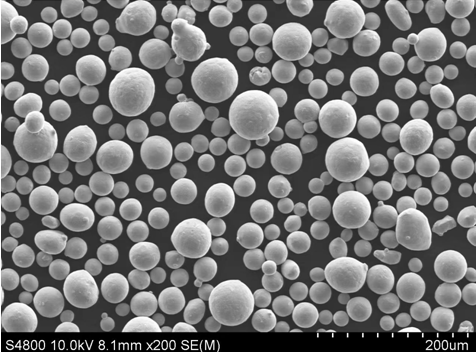
FAQs
Question | Answer |
---|---|
What is NiCr 80/20 Powder primarily used for? | It is primarily used for high-temperature applications such as heating elements, thermal spray coatings, and gas turbines. |
Is NiCr 80/20 Powder expensive compared to other alloys? | Yes, it tends to be more expensive than common alloys but is cost-effective when performance at high temperatures is required. |
Can NiCr 80/20 Powder be used in marine applications? | Yes, it offers excellent corrosion resistance, making it suitable for marine and chemical processing environments. |
How is NiCr 80/20 Powder manufactured? | It is typically produced through atomization processes, ensuring fine and uniform particle size for various industrial applications. |
Is NiCr 80/20 Powder available for additive manufacturing? | Yes, certain models like NiCr 80/20 M-90 are specifically designed for additive manufacturing and 3D printing applications. |
Conclusion
NiCr 80/20 Powder stands out for its versatility, durability, and superior resistance to heat and corrosion. Whether you’re working in aerospace, automotive, or chemical processing, this alloy offers a reliable solution for even the most demanding applications. While it may come at a higher cost compared to other alloys, its performance in extreme conditions justifies the investment. When selecting the right metal powder for your needs, understanding the pros and cons of different materials is critical—and NiCr 80/20 Powder often comes out on top when it comes to high-performance applications.