Overview
Ceramic-lined induction crucibles are essential components in the metallurgical industry, particularly for melting and casting various metals and alloys. These crucibles offer a combination of superior thermal resistance, chemical inertness, and durability, making them indispensable for high-temperature applications. This article delves into the intricacies of ceramic-lined induction crucibles, exploring their composition, properties, applications, and the specific metal powders used in conjunction with them.
What are Ceramic-Lined Induction Crucibles?
Ceramic-lined induction crucibles are specially designed containers used in induction furnaces. The lining of these crucibles is made from advanced ceramic materials, providing excellent resistance to high temperatures and chemical reactions. These properties make them ideal for melting and holding molten metals without contaminating them.
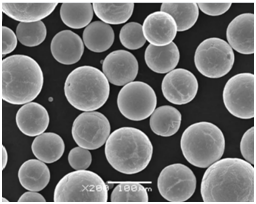
Composition of Ceramic-Lined Induction Crucibles
The composition of ceramic-lined induction crucibles is critical to their performance. The primary materials used in the lining include:
Material | Description |
---|---|
Alumina (Al₂O₃) | High melting point, excellent thermal shock resistance, and chemical inertness. |
Silicon Carbide (SiC) | High thermal conductivity, durability, and resistance to wear and corrosion. |
Zirconia (ZrO₂) | Exceptional thermal insulation, high melting point, and resistance to molten metals. |
Magnesia (MgO) | High refractory properties, resistance to slag, and chemical stability. |
Characteristics of Ceramic-Lined Induction Crucibles
Ceramic-lined induction crucibles exhibit a range of characteristics that make them suitable for industrial use:
- Thermal Stability: Withstand high temperatures without deformation.
- Chemical Inertness: Resist reactions with molten metals.
- Durability: Long service life due to high wear and corrosion resistance.
- Thermal Shock Resistance: Handle rapid temperature changes without cracking.
Applications of Ceramic-Lined Induction Crucibles
Ceramic-lined induction crucibles find applications in various industries:
Industry | Applications |
---|---|
Metallurgy | Melting and casting of ferrous and non-ferrous metals. |
Electronics | Production of semiconductor materials. |
Aerospace | Fabrication of high-performance metal alloys. |
Automotive | Manufacturing of engine components and other metal parts. |
Jewelry | Melting and refining precious metals. |
Specifications, Sizes, Grades, and Standards
Ceramic-lined induction crucibles come in various specifications to meet diverse industrial needs:
Specification | Detail |
---|---|
Sizes | Ranges from small laboratory sizes to large industrial sizes. |
Grades | Vary based on the material composition and intended application. |
Standards | Comply with international standards like ISO, ASTM, and DIN. |
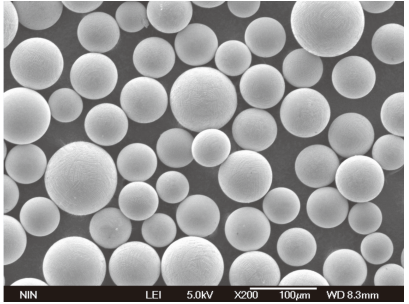
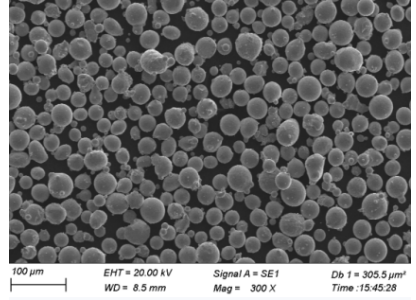
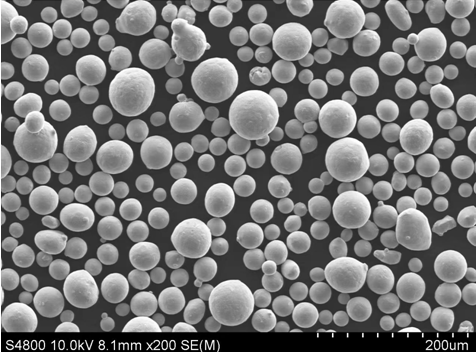
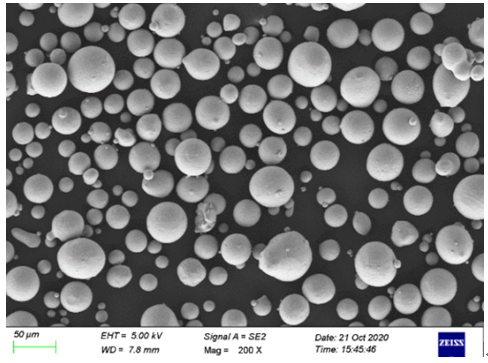
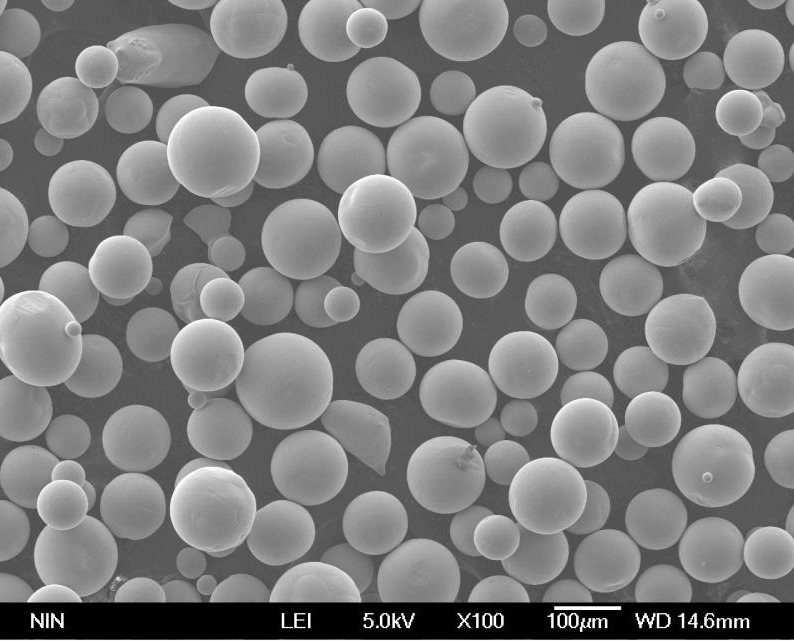
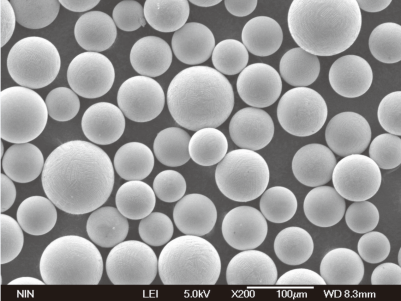
Suppliers and Pricing Details
Several suppliers offer ceramic-lined induction crucibles, with pricing varying based on size, material, and grade:
Supplier | Product Range | Price Range |
---|---|---|
Morgan Advanced Materials | High-performance ceramic crucibles. | $100 – $5000 per unit. |
Saint-Gobain | Wide range of sizes and materials. | $200 – $6000 per unit. |
RHI Magnesita | Industrial-grade crucibles for heavy-duty use. | $150 – $5500 per unit. |
CeramTec | Customized crucibles for specific applications. | $250 – $7000 per unit. |
Comparing Metal Powder Models for Use with Ceramic-Lined Induction Crucibles
Using specific metal powders with ceramic-lined induction crucibles enhances their performance. Here are some notable metal powders:
1. Aluminum Alloy Powder
Composition: Primarily aluminum with traces of silicon, magnesium, and copper.
Properties: Lightweight, high thermal conductivity, excellent corrosion resistance.
Applications: Aerospace components, automotive parts, and electronic enclosures.
2. Copper Powder
Composition: Pure copper or copper alloys.
Properties: Excellent electrical and thermal conductivity, high ductility.
Applications: Electrical contacts, heat exchangers, and printed circuit boards.
3. Nickel Powder
Composition: Pure nickel or nickel alloys.
Properties: High melting point, corrosion resistance, magnetic properties.
Applications: Battery electrodes, catalysts, and superalloys for high-temperature applications.
4. Titanium Powder
Composition: Pure titanium or titanium alloys.
Properties: High strength-to-weight ratio, excellent corrosion resistance, biocompatibility.
Applications: Medical implants, aerospace components, and sporting goods.
5. Stainless Steel Powder
Composition: Iron, chromium, nickel, and molybdenum.
Properties: Corrosion resistance, high strength, good machinability.
Applications: Automotive parts, kitchenware, and medical instruments.
6. Cobalt-Chrome Powder
Composition: Cobalt, chromium, and molybdenum.
Properties: High wear resistance, excellent corrosion resistance, biocompatibility.
Applications: Dental implants, orthopedic implants, and turbine blades.
7. Magnesium Powder
Composition: Pure magnesium or magnesium alloys.
Properties: Lightweight, high strength-to-weight ratio, good machinability.
Applications: Aerospace components, automotive parts, and electronic devices.
8. Tungsten Powder
Composition: Pure tungsten or tungsten alloys.
Properties: High melting point, high density, good thermal conductivity.
Applications: Electrical contacts, heat sinks, and radiation shielding.
9. Iron Powder
Composition: Pure iron or iron alloys.
Properties: High strength, good magnetic properties, cost-effective.
Applications: Automotive parts, magnetic materials, and sintered components.
10. Zirconium Powder
Composition: Pure zirconium or zirconium alloys.
Properties: High corrosion resistance, excellent thermal properties, biocompatibility.
Applications: Nuclear reactors, medical implants, and aerospace components.
Comparison of Metal Powders
Metal Powder | Advantages | Disadvantages |
---|---|---|
Aluminum Alloy | Lightweight, good thermal conductivity. | Lower melting point compared to other metals. |
Copper | Excellent conductivity, ductility. | Prone to oxidation, relatively heavy. |
Nickel | High melting point, corrosion resistant. | Expensive, magnetic properties may be undesirable. |
Titanium | High strength-to-weight ratio, biocompatible. | Expensive, difficult to machine. |
Stainless Steel | Corrosion resistant, strong. | Heavier than some alternatives, expensive. |
Cobalt-Chrome | Wear and corrosion resistant, biocompatible. | Very expensive, difficult to machine. |
Magnesium | Lightweight, good machinability. | Highly reactive, prone to oxidation. |
Tungsten | High melting point, dense. | Very difficult to machine, expensive. |
Iron | Strong, cost-effective. | Prone to rust, relatively heavy. |
Zirconium | Corrosion resistant, biocompatible. | Expensive, difficult to source. |
Choosing the Right Metal Powder
Selecting the appropriate metal powder for use with ceramic-lined induction crucibles depends on the intended application and specific requirements such as melting point, thermal conductivity, corrosion resistance, and cost. Each metal powder offers unique properties that make it suitable for different industrial applications.
Advantages and Limitations of Ceramic-Lined Induction Crucibles
Advantages | Limitations |
---|---|
High thermal resistance | Higher initial cost compared to some alternatives. |
Chemical inertness | Requires careful handling to avoid damage. |
Durability and long service life | Not suitable for all types of metals. |
Thermal shock resistance | Specialized manufacturing process required. |
Factors to Consider When Using Ceramic-Lined Induction Crucibles
When selecting and using ceramic-lined induction crucibles, consider the following factors:
- Type of Metal: Ensure compatibility between the crucible material and the metal being melted.
- Operating Temperature: Choose a crucible that can withstand the required temperature range.
- Chemical Reactions: Consider the potential for chemical reactions between the crucible and molten metal.
- Size and Shape: Select a crucible that fits the furnace and meets the volume requirements.
- Cost: Balance the initial cost with the expected service life and performance benefits.
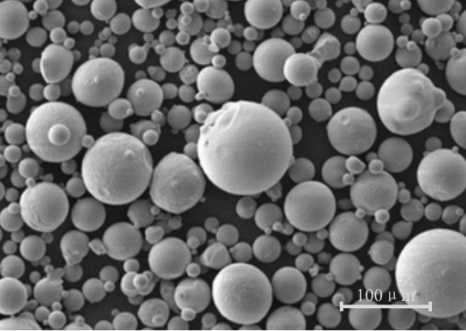
FAQs
What are the main benefits of using ceramic-lined induction crucibles?
Ceramic-lined induction crucibles offer high thermal resistance, chemical inertness, durability, and excellent thermal shock resistance. These properties make them ideal for high-temperature metal melting applications, ensuring longevity and consistent performance.
What is a ceramic-lined induction crucible?
A ceramic-lined induction crucible is a container used for melting metals at high temperatures. It features a ceramic inner lining that provides excellent heat resistance and chemical inertness, crucial for many molten metal applications. The outer shell is typically made of metal and houses an induction coil that generates heat through electromagnetic induction.
What are the advantages of using a ceramic-lined induction crucible?
High-temperature resistance: Ceramic linings can withstand extremely high temperatures, allowing for melting of various metals.
What are some disadvantages of using a ceramic-lined induction crucible?
Chemical inertness: The ceramic material resists reactions with many molten metals, reducing contamination.
Clean and efficient melting: Induction heating minimizes energy loss and provides a clean, controlled heating process.
Improved pouring characteristics: The smooth ceramic lining can enhance metal flow during pouring.
Fragility: Compared to metal crucibles, the ceramic lining is more susceptible to cracking or chipping if mishandled.
Thermal shock resistance: Sudden temperature changes can damage the ceramic lining. Proper preheating and cooldown procedures are essential.
Cost: Ceramic-lined crucibles can be more expensive than some traditional crucibles.