Gas atomization might sound like something straight out of a sci-fi novel, but it’s actually a cutting-edge technology that’s revolutionizing the production of metal powders. Whether you’re a seasoned engineer, a curious student, or just someone with a keen interest in advanced manufacturing techniques, this guide is for you. We’ll dive deep into the process, its applications, and everything in between, ensuring you walk away with a solid understanding of gas atomization. Ready to explore? Let’s get started!
Overview of Gas Atomization
Gas atomization is a process used to produce fine metal powders. By using high-pressure gas to disintegrate molten metal into tiny droplets, which then solidify into fine powders, this technique offers precision and control that other methods can’t match. These powders are crucial for various industries, including aerospace, automotive, and even medicine, due to their superior properties and uniformity.
Key Details of Gas Atomization:
- Process: Disintegration of molten metal using high-pressure gas
- Output: Fine, spherical metal powders
- Applications: Aerospace, automotive, additive manufacturing, pharmaceuticals
- Advantages: High purity, controlled particle size, spherical shape
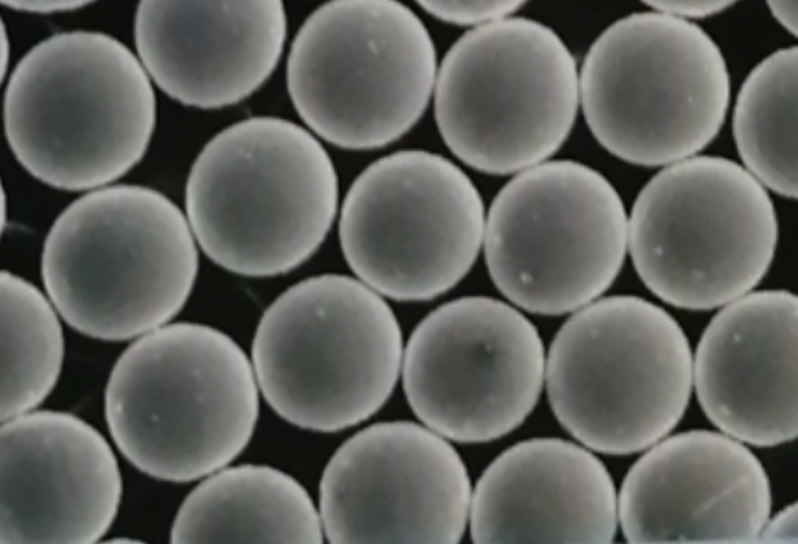
Types and Composition of Gas Atomized Metal Powders
Let’s break down some of the most commonly used metal powders produced by gas atomization. Each type has its own unique properties and applications.
Metal Powder | Composition | Properties | Applications |
---|---|---|---|
Aluminum Alloys | Al, Mg, Si, Cu | Lightweight, corrosion-resistant | Aerospace, automotive |
Stainless Steel | Fe, Cr, Ni, Mo | High strength, corrosion-resistant | Medical devices, food processing equipment |
Titanium Alloys | Ti, Al, V | High strength-to-weight ratio, corrosion-resistant | Aerospace, medical implants |
Nickel Alloys | Ni, Cr, Mo, Fe | High temperature resistance, corrosion-resistant | Turbines, chemical processing |
Copper Alloys | Cu, Zn, Sn | Excellent electrical conductivity, corrosion-resistant | Electrical components, heat exchangers |
Cobalt-Chromium Alloys | Co, Cr, Mo | Wear-resistant, biocompatible | Medical implants, dental applications |
Tool Steels | Fe, C, Cr, V, W | High hardness, wear-resistant | Cutting tools, molds |
Precious Metals | Au, Ag, Pt | High conductivity, corrosion-resistant | Electronics, jewelry |
High Entropy Alloys | Varies | Exceptional mechanical properties, thermal stability | Research, advanced engineering |
Iron Alloys | Fe, C, Mn, Si | High strength, magnetic properties | Automotive, construction |
Detailed Descriptions:
Aluminum Alloys
Aluminum alloys produced by gas atomization are known for their lightweight and high strength. They are often used in the aerospace and automotive industries due to their excellent corrosion resistance and good mechanical properties.
Stainless Steel
Stainless steel powders are valued for their high strength and corrosion resistance. These powders are essential in medical devices and food processing equipment, where hygiene and durability are paramount.
Titanium Alloys
Titanium alloys offer an exceptional strength-to-weight ratio and are highly corrosion-resistant, making them ideal for aerospace applications and medical implants. Their biocompatibility further extends their use in the medical field.
Nickel Alloys
Nickel-based powders are known for their high temperature resistance and corrosion-resistant properties. These are crucial in turbine engines and chemical processing industries, where extreme conditions are the norm.
Copper Alloys
Copper alloys stand out for their excellent electrical conductivity and corrosion resistance. They are widely used in electrical components and heat exchangers, playing a vital role in various electronic devices and cooling systems.
Cobalt-Chromium Alloys
Cobalt-chromium alloys are wear-resistant and biocompatible, making them perfect for medical implants and dental applications. Their durability ensures long-lasting performance in demanding environments.
Tool Steels
Tool steels are renowned for their high hardness and wear resistance. These properties make them indispensable in the manufacturing of cutting tools and molds, where precision and durability are critical.
Precious Metals
Precious metal powders like gold, silver, and platinum are highly conductive and corrosion-resistant. These powders are commonly used in electronics and jewelry, where their unique properties are highly valued.
High Entropy Alloys
High entropy alloys are a newer class of materials with exceptional mechanical properties and thermal stability. They are still primarily used in research and advanced engineering applications, where their unique characteristics are being explored.
Iron Alloys
Iron alloys, including various grades of steel, are essential for their high strength and magnetic properties. They are widely used in the automotive and construction industries, contributing to the strength and integrity of countless structures and components.
Applications of Gas Atomized Metal Powders
Gas atomized metal powders are versatile and find applications across various industries. Here’s a detailed look at where and how these powders are used.
Industry | Application | Benefits |
---|---|---|
Aerospace | Turbine blades, structural components | High strength, lightweight, corrosion-resistant |
Automotive | Engine parts, gears, bearings | Durability, precision, improved fuel efficiency |
Medical | Implants, prosthetics, surgical instruments | Biocompatibility, corrosion-resistant, high strength |
Additive Manufacturing | 3D printing of prototypes and parts | Customizability, precision, material efficiency |
Electronics | Conductive inks, connectors, heat sinks | High conductivity, miniaturization, thermal management |
Tool Manufacturing | Cutting tools, molds, dies | High hardness, wear resistance, precision |
Jewelry | Fine jewelry, decorative items | Aesthetics, corrosion-resistant, high value |
Chemical Processing | Catalysts, filters, reaction vessels | Corrosion-resistant, high temperature stability |
Construction | Structural components, reinforcing materials | High strength, durability, magnetic properties |
Research and Development | Material science, advanced engineering | Unique properties, innovation, experimental applications |
Aerospace
In aerospace, gas atomized powders are essential for producing high-performance turbine blades and structural components. Their lightweight nature and high strength ensure efficiency and safety in aircraft and spacecraft.
Automotive
The automotive industry leverages these powders for engine parts, gears, and bearings, enhancing durability and precision. This results in improved fuel efficiency and performance in vehicles.
Medical
Medical applications include implants, prosthetics, and surgical instruments, where biocompatibility and corrosion resistance are crucial. These powders ensure high strength and longevity in medical devices.
Additive Manufacturing
Gas atomized powders are pivotal in 3D printing, enabling the creation of custom prototypes and parts with high precision. This technology allows for material efficiency and innovative design possibilities.
Electronics
In the electronics industry, these powders are used for conductive inks, connectors, and heat sinks. Their high conductivity and thermal management capabilities support the development of compact and efficient electronic devices.
Tool Manufacturing
Tool manufacturing benefits from the high hardness and wear resistance of gas atomized powders. Cutting tools, molds, and dies made from these powders ensure precision and durability in various industrial processes.
Jewelry
In jewelry making, precious metal powders are used to create fine jewelry and decorative items. Their aesthetic appeal, corrosion resistance, and high value make them ideal for crafting beautiful and durable pieces.
Chemical Processing
Chemical processing industries utilize these powders for catalysts, filters, and reaction vessels. Their corrosion resistance and high-temperature stability ensure efficient and safe chemical reactions.
Construction
In construction, gas atomized powders are used for structural components and reinforcing materials. Their high strength and durability contribute to the integrity and longevity of buildings and infrastructure.
Research and Development
Researchers and engineers use these powders to explore new materials and applications. The unique properties of gas atomized powders drive innovation and experimentation in material science and advanced engineering.
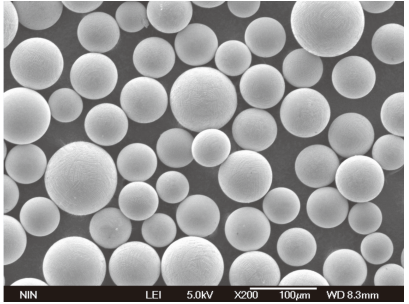
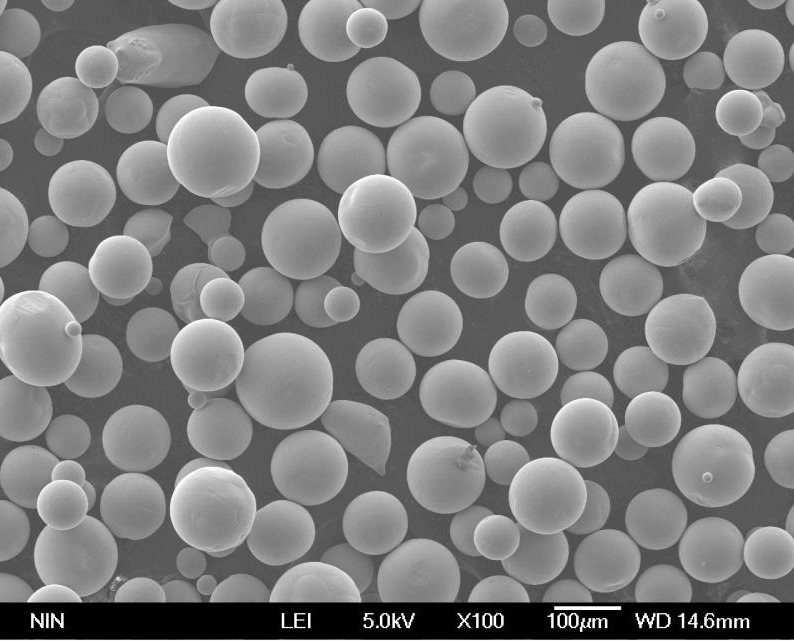
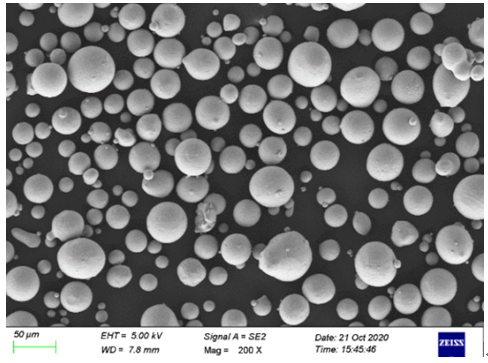
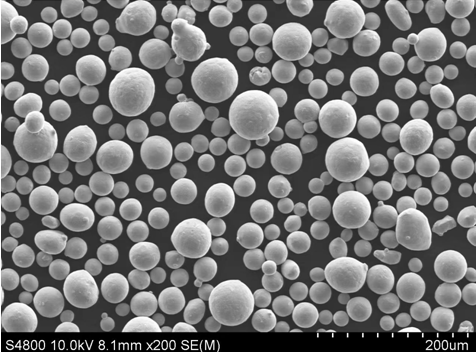
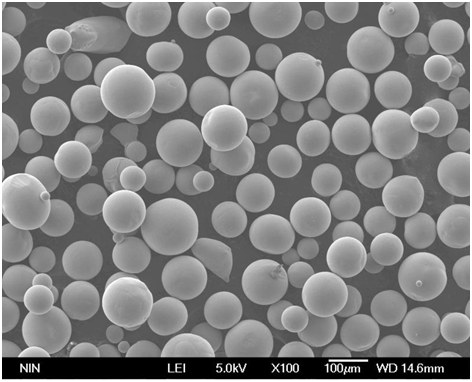
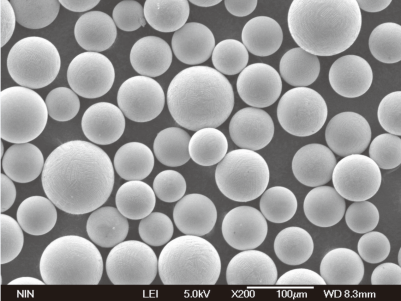
Specifications, Sizes, Grades, and Standards
When it comes to gas atomized metal powders, there are various specifications, sizes, grades, and standards to consider. These factors determine the suitability of the powders for different applications.
Parameter | Details |
---|---|
Particle Size | Typically ranges from 10 µm to 150 µm |
Purity | High purity levels, often exceeding 99.9% |
Shape | Spherical for uniform flow and packing density |
Grades | Vary based on alloy composition and intended application |
Standards | ASTM, ISO, and other industry-specific standards |
Particle Size
The particle size of gas atomized powders typically ranges from 10 µm to 150 µm. This wide range allows for the customization of powders for specific applications, ensuring optimal performance.
Purity
High purity levels are a hallmark of gas atomized powders, often exceeding 99.9%. This ensures that the powders meet the stringent requirements of various industries, including aerospace and medical.
Shape
The spherical shape of gas atomized powders ensures uniform flow and packing density. This characteristic is crucial for applications such as additive manufacturing, where consistent material distribution is essential.
Grades
Different grades of powders are available based on their alloy composition and intended application. These grades ensure that the powders meet specific performance criteria for various uses.
Standards
Gas atomized powders must adhere to industry-specific standards such as ASTM and ISO. These standards ensure that the powders meet the necessary quality and performance benchmarks.
Suppliers and Pricing Details
Finding the right supplier for gas atom
ized powders is crucial for ensuring quality and reliability. Here’s a list of some notable suppliers and their pricing details.
Supplier | Location | Products | Pricing |
---|---|---|---|
Carpenter Technology | USA | Stainless steel, titanium alloys | Varies by product and quantity |
Höganäs AB | Sweden | Iron and steel powders | Custom quotes based on order |
GKN Powder Metallurgy | Global | Various metal powders | Competitive pricing, bulk discounts |
Sandvik | Sweden | Nickel and cobalt alloys | Price upon request |
AP&C (GE Additive) | Canada | Titanium and aluminum alloys | Premium pricing for high purity |
Praxair Surface Technologies | USA | Specialty alloys | Quotation based on specifications |
Tekna Plasma Systems | Canada | Spherical metal powders | Price based on particle size and quantity |
Epson Atmix | Japan | Magnetic powders, high-performance alloys | Competitive pricing, volume discounts |
AMETEK Specialty Metal Products | USA | High purity metal powders | Custom quotes, premium pricing |
Advanced Powders & Coatings (AP&C) | Canada | Titanium and other advanced alloys | Price varies, typically high for precision powders |
Carpenter Technology
Based in the USA, Carpenter Technology offers a wide range of stainless steel and titanium alloy powders. Pricing varies by product and quantity, with custom quotes available upon request.
Höganäs AB
Höganäs AB, a Swedish company, specializes in iron and steel powders. They offer custom quotes based on order specifics, ensuring tailored solutions for their customers.
GKN Powder Metallurgy
With a global presence, GKN Powder Metallurgy provides various metal powders. They offer competitive pricing and bulk discounts, making them a popular choice for large-scale projects.
Sandvik
Sandvik, another Swedish company, supplies nickel and cobalt alloy powders. Pricing is provided upon request, ensuring that customers receive a tailored quote based on their needs.
AP&C (GE Additive)
AP&C, a subsidiary of GE Additive in Canada, specializes in titanium and aluminum alloys. They offer premium pricing for their high-purity powders, reflecting their superior quality.
Praxair Surface Technologies
Based in the USA, Praxair Surface Technologies offers a range of specialty alloys. Pricing is available upon request, ensuring that customers receive a quote based on their specific requirements.
Tekna Plasma Systems
Tekna Plasma Systems in Canada produces spherical metal powders. Their pricing is based on particle size and quantity, allowing for customized solutions for various applications.
Epson Atmix
Epson Atmix, a Japanese company, offers magnetic powders and high-performance alloys. They provide competitive pricing and volume discounts, catering to a wide range of customers.
AMETEK Specialty Metal Products
Based in the USA, AMETEK Specialty Metal Products supplies high-purity metal powders. They offer custom quotes and premium pricing, ensuring top-quality products for demanding applications.
Advanced Powders & Coatings (AP&C)
Another Canadian company, AP&C, specializes in titanium and other advanced alloys. Their pricing varies, typically on the higher end for precision powders, reflecting their commitment to quality.
Advantages and Limitations of Gas Atomization
Gas atomization offers numerous advantages, but it also has some limitations. Let’s compare the pros and cons to get a clearer picture.
Advantages | Limitations |
---|---|
High purity | High production cost |
Controlled particle size | Energy-intensive process |
Spherical shape | Limited to certain metals and alloys |
Uniform distribution | Requires specialized equipment |
Versatile applications | Powder handling challenges |
High production rates | Potential for contamination |
Advantages
High Purity
Gas atomization produces powders with high purity, often exceeding 99.9%. This is crucial for applications that require materials free from impurities, such as in aerospace and medical devices.
Controlled Particle Size
The process allows for precise control over particle size, ensuring that the powders meet specific requirements for different applications. This level of control is essential for achieving optimal performance in various industries.
Spherical Shape
The spherical shape of the powders ensures uniform flow and packing density, which is particularly beneficial for additive manufacturing and other processes that require consistent material distribution.
Uniform Distribution
Gas atomization results in uniform distribution of particles, enhancing the performance and reliability of the final product. This uniformity is critical for applications where consistency is key.
Versatile Applications
The versatility of gas atomized powders makes them suitable for a wide range of applications, from aerospace and automotive to medical and electronics.
High Production Rates
Gas atomization can produce large quantities of powders efficiently, making it a viable option for industrial-scale production.
Limitations
High Production Cost
The process is relatively expensive due to the high costs associated with the equipment and energy required. This can be a significant barrier for small-scale operations.
Energy-Intensive Process
Gas atomization is energy-intensive, which can contribute to higher operational costs and environmental impact.
Limited to Certain Metals and Alloys
Not all metals and alloys can be processed using gas atomization, limiting its applicability to certain materials.
Requires Specialized Equipment
The process requires specialized equipment, which can be costly to acquire and maintain. This can be a limiting factor for some manufacturers.
Powder Handling Challenges
Handling and storing fine metal powders can be challenging due to their potential for contamination and the need for careful management to prevent oxidation and other issues.
Potential for Contamination
Despite its high purity, there is always a risk of contamination during the production process. Ensuring a controlled environment is essential to maintain the quality of the powders.
Comparing Gas Atomized Metal Powders: Performance and Features
Let’s take a closer look at how different gas atomized metal powders compare in terms of performance and features.
Metal Powder | Strength | Corrosion Resistance | Temperature Stability | Biocompatibility | Cost |
---|---|---|---|---|---|
Aluminum Alloys | High | Moderate | Moderate | Low | 1.15 |
Stainless Steel | Very High | High | High | Moderate | 40 |
Titanium Alloys | Very High | Very High | High | High | 1000 |
Nickel Alloys | High | Very High | Very High | Low | 53 |
Copper Alloys | Moderate | High | Low | Low | 37 |
Cobalt-Chromium Alloys | High | Very High | High | High | 440 |
Tool Steels | Very High | Moderate | Moderate | Low | 172 |
Precious Metals | Moderate | Very High | Low | Moderate | 2400 |
High Entropy Alloys | Very High | High | High | Low | 3000 |
Iron Alloys | High | Moderate | Low | Low | 30 |
Strength
- Aluminum Alloys: High strength, ideal for lightweight applications.
- Stainless Steel: Very high strength, suitable for demanding environments.
- Titanium Alloys: Exceptional strength, perfect for aerospace and medical applications.
- Nickel Alloys: High strength, excellent for high-temperature applications.
- Copper Alloys: Moderate strength, suitable for electrical components.
- Cobalt-Chromium Alloys: High strength, ideal for medical implants.
- Tool Steels: Very high strength, essential for cutting tools and molds.
- Precious Metals: Moderate strength, valued for aesthetics and conductivity.
- High Entropy Alloys: Very high strength, emerging applications in advanced engineering.
- Iron Alloys: High strength, widely used in construction and automotive industries.
Corrosion Resistance
- Aluminum Alloys: Moderate corrosion resistance, suitable for outdoor use.
- Stainless Steel: High corrosion resistance, ideal for harsh environments.
- Titanium Alloys: Very high corrosion resistance, perfect for medical and aerospace.
- Nickel Alloys: Very high corrosion resistance, excellent for chemical processing.
- Copper Alloys: High corrosion resistance, ideal for electrical and heat exchange applications.
- Cobalt-Chromium Alloys: Very high corrosion resistance, suitable for medical implants.
- Tool Steels: Moderate corrosion resistance, essential for tool longevity.
- Precious Metals: Very high corrosion resistance, perfect for jewelry and electronics.
- High Entropy Alloys: High corrosion resistance, potential in extreme environments.
- Iron Alloys: Moderate corrosion resistance, suitable for construction and automotive.
Temperature Stability
- Aluminum Alloys: Moderate temperature stability, suitable for general applications.
- Stainless Steel: High temperature stability, ideal for high-heat environments.
- Titanium Alloys: High temperature stability, perfect for aerospace and high-temperature applications.
- Nickel Alloys: Very high temperature stability, crucial for turbine engines and chemical processing.
- Copper Alloys: Low temperature stability, best for electrical applications.
- Cobalt-Chromium Alloys: High temperature stability, suitable for medical and dental applications.
- Tool Steels: Moderate temperature stability, essential for cutting tools.
- Precious Metals: Low temperature stability, valued for conductivity and aesthetics.
- High Entropy Alloys: High temperature stability, emerging applications in advanced engineering.
- Iron Alloys: Low temperature stability, widely used in automotive and construction.
Biocompatibility
- Aluminum Alloys: Low biocompatibility, not suitable for medical implants.
- Stainless Steel: Moderate biocom
patibility, used in medical devices.
- Titanium Alloys: High biocompatibility, perfect for medical implants.
- Nickel Alloys: Low biocompatibility, suitable for high-temperature applications.
- Copper Alloys: Low biocompatibility, ideal for electrical components.
- Cobalt-Chromium Alloys: High biocompatibility, suitable for medical implants.
- Tool Steels: Low biocompatibility, essential for industrial tools.
- Precious Metals: Moderate biocompatibility, valued in electronics and jewelry.
- High Entropy Alloys: Low biocompatibility, potential in advanced engineering.
- Iron Alloys: Low biocompatibility, widely used in construction and automotive.

FAQ
Question | Answer |
---|---|
What is gas atomization? | Gas atomization is a process used to produce fine metal powders by disintegrating molten metal with high-pressure gas. |
What are the benefits of gas atomized powders? | High purity, controlled particle size, spherical shape, and uniform distribution. |
Which industries use gas atomized powders? | Aerospace, automotive, medical, additive manufacturing, electronics, tool manufacturing, jewelry, chemical processing, construction, and research. |
What metals can be atomized? | Aluminum, stainless steel, titanium, nickel, copper, cobalt-chromium, tool steels, precious metals, high entropy alloys, and iron. |
How are gas atomized powders used in 3D printing? | They provide precise control and consistency for creating custom prototypes and parts. |
What are the challenges of gas atomization? | High production cost, energy-intensive process, limited to certain metals, requires specialized equipment, powder handling challenges, potential for contamination. |
How do gas atomized powders compare to other types? | They offer higher purity, better control over particle size, and superior properties for specific applications. |
Where can I buy gas atomized powders? | Suppliers include Carpenter Technology, Höganäs AB, GKN Powder Metallurgy, Sandvik, AP&C (GE Additive), Praxair Surface Technologies, Tekna Plasma Systems, Epson Atmix, AMETEK Specialty Metal Products, and Advanced Powders & Coatings (AP&C). |
What standards do gas atomized powders adhere to? | They adhere to industry-specific standards such as ASTM and ISO. |
Why is particle size important in gas atomized powders? | Particle size affects the performance and suitability of powders for different applications, ensuring optimal results. |
Conclusion
Gas atomization is a fascinating and highly effective process for producing fine metal powders. Its applications span across numerous industries, from aerospace and automotive to medical and electronics. Despite its challenges, the benefits of high purity, controlled particle size, and spherical shape make it an invaluable technology in advanced manufacturing. Whether you’re a professional in the field or simply curious about the technology, understanding gas atomization opens up a world of possibilities in modern engineering and materials science.