Haynes 25, also known as L605, is a cobalt-based alloy that’s renowned for its exceptional high-temperature strength and oxidation resistance. Whether you’re involved in aerospace engineering, gas turbine production, or any high-stress application, you’ve likely come across Haynes 25 powder. But how exactly does it perform, and what makes it so unique? In this article, we’ll dive deep into all aspects of Haynes 25 powder, from its composition and characteristics to its applications, benefits, and limitations. We’ll also compare it to similar metal powders, guide you through its specifications, and answer some frequently asked questions.
Overview of Haynes 25 (L605) Powder
Haynes 25 powder is primarily composed of cobalt, chromium, tungsten, and nickel, designed to withstand extreme heat and stress. What sets it apart from other metal powders is its ability to maintain mechanical properties even at temperatures exceeding 1800°F (982°C). This makes it a top choice in industries where high-temperature performance and corrosion resistance are critical, such as aerospace, medical devices, and industrial gas turbines.
Key Features of Haynes 25 (L605) Powder:
- High-Temperature Strength: Retains its strength and toughness at elevated temperatures.
- Corrosion Resistance: Resistant to oxidation, scaling, and corrosive environments, especially in high-temperature conditions.
- Wear Resistance: Exhibits excellent wear resistance, making it suitable for demanding environments.
- Formability: Can be fabricated into different forms, including powder, wire, sheets, and plates, for a variety of applications.
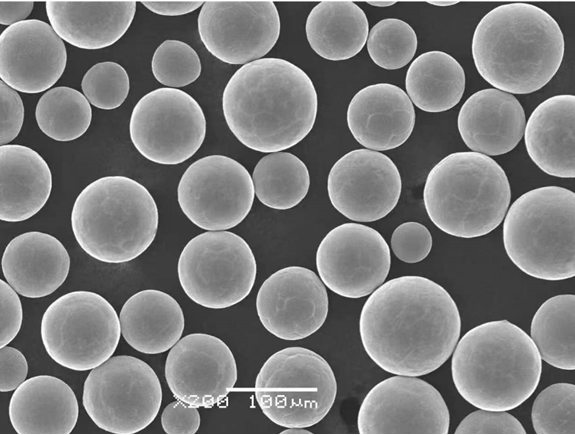
Composition of Haynes 25 (L605) Powder
The unique properties of Haynes 25 powder are a result of its carefully designed chemical composition. Let’s break down its key elements and what they contribute to the alloy.
Element | Percentage Composition | Role in the Alloy |
---|---|---|
Cobalt (Co) | 50-55% | Provides the base of the alloy, contributing to its high-temperature strength. |
Chromium (Cr) | 19-21% | Enhances corrosion and oxidation resistance. |
Tungsten (W) | 14-16% | Improves strength at high temperatures. |
Nickel (Ni) | 9-11% | Adds to toughness and overall strength. |
Carbon (C) | 0.05-0.15% | Aids in hardening and wear resistance. |
Manganese (Mn) | 1-2% | Improves formability and oxidation resistance. |
Silicon (Si) | 0.4% max | Enhances oxidation resistance. |
Each of these elements plays a critical role in giving Haynes 25 powder its unique set of properties. The balance between these materials is finely tuned to ensure that the alloy can perform in extreme conditions without sacrificing durability or functionality.
Characteristics of Haynes 25 (L605) Powder
Now, let’s take a closer look at what makes Haynes 25 powder stand out in terms of its mechanical, thermal, and chemical properties. Each of these factors is crucial for its performance in high-stress, high-temperature environments.
Mechanical Properties:
Property | Value |
---|---|
Density | 9.13 g/cm³ |
Tensile Strength (at 70°F) | 135 ksi (930 MPa) |
Yield Strength (at 70°F) | 55 ksi (380 MPa) |
Elongation | 42% |
Hardness | 250-280 HB |
Creep Resistance | High creep strength at temperatures up to 1800°F (982°C). |
Thermal Properties:
Property | Value |
---|---|
Melting Range | 1330°C – 1410°C (2426°F – 2570°F) |
Thermal Conductivity | 11.2 W/m·K at 70°F |
Specific Heat | 0.097 Btu/lb-°F |
Thermal Expansion Coefficient | 12.7 μin/in°F |
Corrosion Resistance:
Haynes 25 offers exceptional corrosion resistance in both oxidizing and reducing environments. Its high chromium content ensures that it forms a protective oxide layer, which prevents further corrosion. The addition of tungsten further enhances this property by improving its strength and stability at elevated temperatures.
Applications of Haynes 25 (L605) Powder
Haynes 25 powder’s unique combination of strength, corrosion resistance, and heat tolerance makes it an essential material across various industries. From aerospace to medical applications, let’s explore where Haynes 25 powder is most commonly used.
Industry | Common Applications |
---|---|
Aerospace | Turbine blades, combustion chamber liners, afterburners. |
Medical | Prosthetics, surgical instruments, dental implants. |
Gas Turbines | Industrial gas turbine parts, such as nozzles and vanes. |
Power Generation | Heat exchangers, high-temperature furnace components. |
Automotive | Engine components requiring wear and corrosion resistance. |
Oil & Gas | Valves, drilling equipment, and other high-stress parts. |
In each of these industries, Haynes 25 powder is valued for its ability to perform reliably in extreme conditions. For example, in aerospace applications, it is often used in jet engines, where components must endure both high heat and mechanical stress.
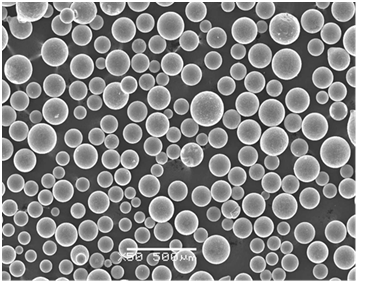
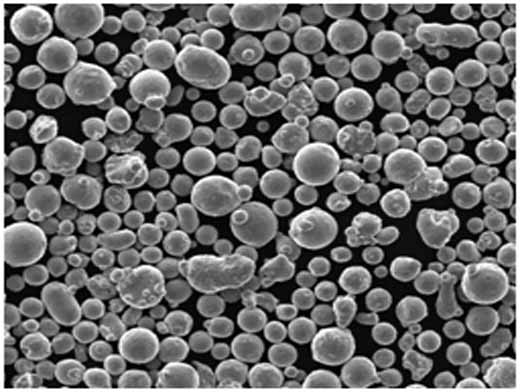
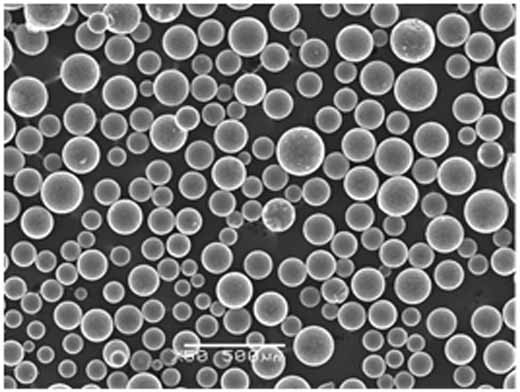
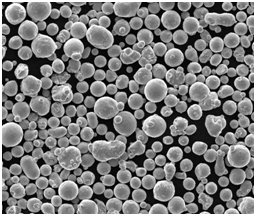
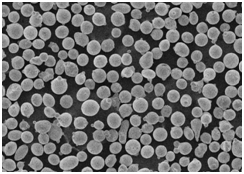
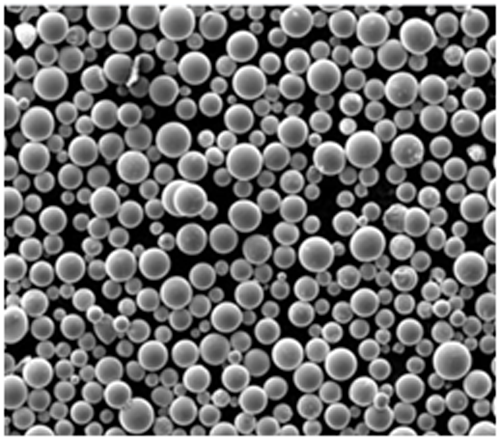
Specific Models of Haynes 25 (L605) Powder
There are several models or variants of Haynes 25 powder, each tailored for specific uses. Here’s a look at some popular models and their respective applications:
- Haynes 25 Powder for Additive Manufacturing
Specially formulated for 3D printing and additive manufacturing. It ensures uniform particle size and high flowability, making it ideal for precise aerospace components. - Haynes 25 Powder for Laser Cladding
Designed for laser cladding applications, offering excellent bonding strength and minimal oxidation during the process. - Haynes 25 Powder for HIP (Hot Isostatic Pressing)
This variant is optimized for HIP applications, where materials are subjected to high pressure and temperature to eliminate voids and increase density. - Haynes 25 Ultra-Fine Powder
Ultra-fine powder for applications requiring precise layering, often used in high-resolution 3D printing and detailed surface coatings. - Haynes 25 High-Temperature Powder
Tailored for high-temperature environments such as turbine blades and engine components, where extreme heat tolerance is required. - Haynes 25 Powder for Plasma Spraying
Suitable for plasma spraying applications, providing a protective coating that resists wear and corrosion. - Haynes 25 Powder for Cold Spray Applications
This variant is ideal for cold spray technology, where particles are accelerated to high velocities to create dense coatings at low temperatures. - Haynes 25 Powder for Aerospace Components
Specifically designed for manufacturing critical aerospace components that demand superior strength, heat resistance, and durability. - Haynes 25 Powder for Medical Implants
Medical-grade powder designed for use in surgical implants and instruments due to its excellent biocompatibility and corrosion resistance. - Haynes 25 Powder for High-Wear Applications
Optimized for parts subjected to extreme wear and tear, such as drilling equipment and valve seats in the oil and gas industry.
Advantages of Haynes 25 (L605) Powder
Let’s take a closer look at why Haynes 25 powder is often preferred over other materials in its category.
Strength at High Temperatures
Unlike many other alloys that weaken when exposed to heat, Haynes 25 powder remains strong and stable at temperatures as high as 1800°F (982°C). This makes it ideal for use in high-stress, high-temperature environments like jet engines or industrial turbines.
Corrosion Resistance
Haynes 25 excels in both oxidizing and reducing environments, thanks to its high chromium content. It forms a protective oxide layer, which shields it from corrosion, even in harsh environments like gas turbines or chemical processing equipment.
Wear Resistance
The addition of tungsten and carbon contributes to the alloy’s exceptional wear resistance. This property is particularly valuable in applications where components are subject to friction and mechanical stress, such as valve seats and drilling equipment.
Formability
Despite its strength and toughness, Haynes 25 is relatively easy to fabricate. It can be processed using conventional methods such as welding, machining, and forming, making it versatile in terms of manufacturing options.
Limitations of Haynes 25 (L605) Powder
While Haynes 25 powder offers many benefits, it’s not without its limitations. Here are a few considerations to keep in mind:
Cost
Cobalt-based alloys like Haynes 25 tend to be more expensive compared to other metal powders. The cost can be a limiting factor for applications where budget constraints are a concern.
Density
Haynes 25 has a relatively high density (9.13 g/cm³), which may not be suitable for
applications where weight is a critical factor, such as aerospace components designed for fuel efficiency.
Machinability
Although Haynes 25 can be machined, its hardness makes it more challenging compared to softer alloys. Specialized equipment and techniques may be required to process this material effectively.
Specifications, Sizes, Grades, and Standards of Haynes 25 (L605) Powder
When selecting Haynes 25 powder for specific applications, it’s crucial to understand the available specifications, sizes, and standards. Here’s a breakdown of the key details:
Specification | Details |
---|---|
Particle Size Range | 15 – 45 µm, 45 – 106 µm |
Grade | ASTM F75, AMS 5796, UNS R30605 |
Standards | ASME Code Case N-540, ISO 5832-5 |
Typical Forms | Powder, wire, sheet, plate |
Melting Point | 1330°C – 1410°C (2426°F – 2570°F) |
These specifications help manufacturers choose the right variant of Haynes 25 powder for their intended applications. Different particle sizes, grades, and standards ensure that the material meets the specific requirements of each industry.
Comparison: Haynes 25 (L605) Powder vs Other Metal Powders
How does Haynes 25 powder compare to other high-performance alloys? Let’s put it up against some competitors.
Property | Haynes 25 (L605) Powder | Inconel 625 Powder | Hastelloy X Powder |
---|---|---|---|
Temperature Resistance | 1800°F (982°C) | 1200°F (649°C) | 1600°F (871°C) |
Corrosion Resistance | Excellent | Very Good | Excellent |
Wear Resistance | Superior | Good | Good |
Machinability | Moderate | Easier | Moderate |
Cost | Higher | Lower | Moderate |
As shown, Haynes 25 excels in high-temperature and wear resistance compared to other popular alloys like Inconel 625 and Hastelloy X. However, it comes with a higher cost and slightly lower machinability.
Suppliers and Pricing of Haynes 25 (L605) Powder
Finding a reliable supplier for Haynes 25 powder is crucial for ensuring material quality and consistency. Here’s a look at some key suppliers and estimated pricing.
Supplier | Location | Price (per kg) |
---|---|---|
Advanced Powders & Coatings | USA | $200 – $300 |
Kennametal | Germany | $220 – $320 |
Carpenter Technology | USA | $250 – $350 |
Aubert & Duval | France | $210 – $330 |
ATI Specialty Materials | USA | $230 – $340 |
Prices may vary depending on factors such as particle size, order quantity, and supplier location.
Pros and Cons of Haynes 25 (L605) Powder
Here’s a quick summary of the pros and cons to help you weigh the benefits and drawbacks of Haynes 25 powder.
Pros | Cons |
---|---|
Superior high-temperature strength | Higher cost compared to other alloys |
Excellent wear and corrosion resistance | High density may not suit weight-sensitive applications |
Good formability and machinability | Requires specialized equipment for machining |
Versatile across industries | Limited availability in some regions |
FAQs
Question | Answer |
---|---|
What is Haynes 25 powder used for? | Haynes 25 powder is used in aerospace, gas turbines, medical devices, and high-temperature applications due to its excellent heat resistance and corrosion resistance. |
Can Haynes 25 be 3D printed? | Yes, Haynes 25 powder can be used in additive manufacturing, including 3D printing for precision parts. |
How does Haynes 25 compare to Inconel 625? | Haynes 25 has better high-temperature strength and wear resistance than Inconel 625, but it is more expensive. |
What is the melting point of Haynes 25? | The melting range of Haynes 25 is 1330°C – 1410°C (2426°F – 2570°F). |
Where can I buy Haynes 25 powder? | You can purchase Haynes 25 powder from suppliers like Advanced Powders & Coatings, Kennametal, Carpenter Technology, and more. |