Overview of CoCrW Powder
CoCrW (Cobalt-Chromium-Tungsten) powder is a highly specialized metal alloy powder commonly used in industries requiring superior wear resistance, strength, and corrosion resistance. It’s most recognized for its applications in high-temperature environments like aerospace, gas turbines, medical devices, and additive manufacturing. This guide dives deep into the intricate world of CoCrW powder, its various grades, and its critical role across industries.
This comprehensive article provides insights into the types, composition, properties, applications, and pricing of various CoCrW powder models. It also compares the pros and cons of each variant and answers common questions related to its use.
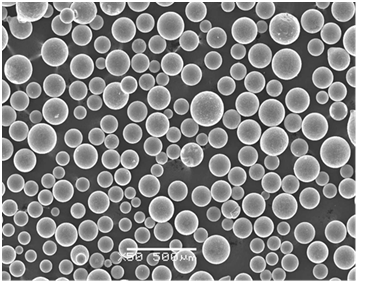
Composition of CoCrW Powder
The CoCrW alloy is defined by its unique blend of Cobalt (Co), Chromium (Cr), and Tungsten (W), though exact percentages can vary across different grades and applications. The general composition gives this powder excellent mechanical properties, especially in high-temperature environments.
Typical Composition Breakdown
Element | Percentage Range | Function in the Alloy |
---|---|---|
Cobalt (Co) | 50-65% | Acts as the base metal, providing strength, toughness, and wear resistance, especially at high temperatures. |
Chromium (Cr) | 20-30% | Enhances corrosion resistance, particularly in harsh environments, and contributes to surface hardening. |
Tungsten (W) | 5-10% | Increases high-temperature strength, and improves wear resistance and hardness without making the alloy too brittle. |
Carbon (C) | 0.1-1% | Forms carbides that further improve wear resistance and hardness, but must be balanced to avoid making the alloy too brittle. |
Silicon (Si) | 0.2-1% | Improves oxidation resistance and promotes machinability. |
Manganese (Mn) | 0.5-2% | Acts as a deoxidizer and enhances the toughness of the alloy, while also contributing to corrosion resistance. |
Characteristics of CoCrW Powder
What makes CoCrW powder unique is its outstanding combination of mechanical properties and thermal stability. Let’s take a deeper look at its defining characteristics:
Property | Details |
---|---|
High-Temperature Strength | The powder retains its mechanical integrity even at elevated temperatures exceeding 800°C. |
Wear Resistance | The alloy exhibits exceptional resistance to wear and tear, making it ideal for cutting tools and turbines. |
Corrosion Resistance | Thanks to the high chromium content, CoCrW powder resists oxidation and corrosion, even in hostile environments like saltwater or acidic conditions. |
Hardness | The alloy maintains a high hardness level, typically between 500 and 700 HV (Vickers Hardness). |
Thermal Fatigue Resistance | With its excellent thermal stability, it withstands repeated heating and cooling cycles without significant degradation. |
Applications of CoCrW Powder
CoCrW powders are used in a variety of industrial applications, especially in environments that demand durability, heat resistance, and minimal wear.
Common Applications of CoCrW Powder
Industry | Application |
---|---|
Aerospace | Jet engines, turbine blades, and other high-temperature components due to their wear resistance and ability to maintain strength at high temperatures. |
Medical Devices | Artificial joints, dental implants, and other biomedical implants because of the alloy’s biocompatibility and corrosion resistance. |
Gas Turbines | Hot section components that need to maintain mechanical integrity at high temperatures and resist corrosion from combustion gases. |
Automotive | Turbochargers, exhaust valves, and other high-temperature automotive components that require strong resistance to wear and heat fatigue. |
Additive Manufacturing | Used in 3D printing to create custom, high-performance parts for the aerospace, medical, and energy sectors. |
Energy | Components in nuclear reactors or energy systems that experience extreme temperatures and corrosive environments. |
Cutting Tools | Drill bits, saw blades, and other tools exposed to intense wear conditions, where long-lasting durability is required. |
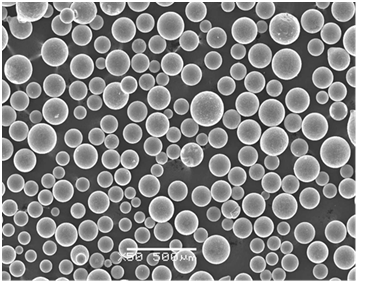
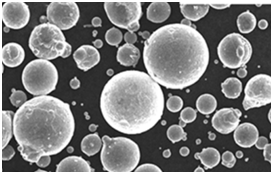
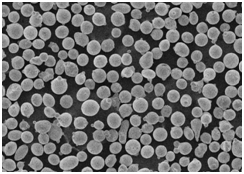
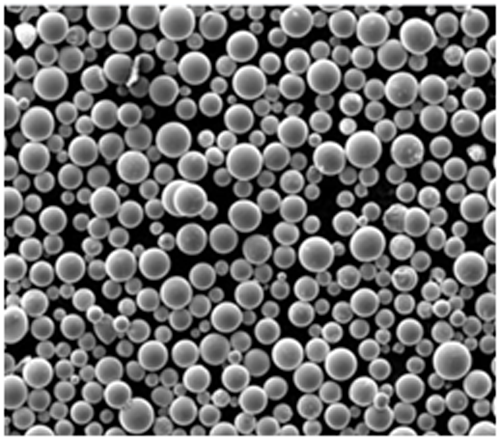
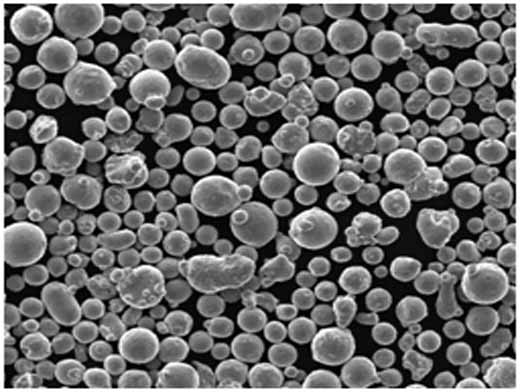
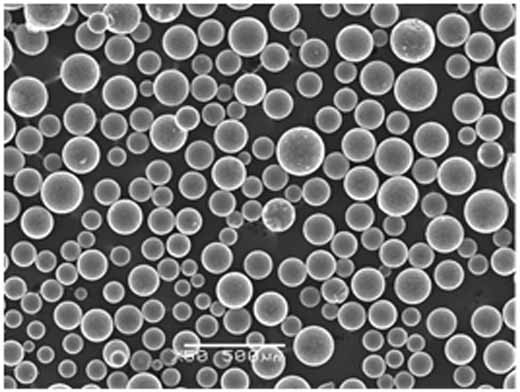
Top CoCrW Powder Models: Detailed Overview
Here, we break down some of the top CoCrW powder models available on the market, highlighting their unique properties and typical uses.
Model | Composition | Key Properties | Typical Application |
---|---|---|---|
Stellite 6 | Co-28Cr-4W-1.2C | Excellent wear and corrosion resistance, high hardness (450-500 HV) | Cutting tools, valve seats, and medical implants |
Stellite 21 | Co-27Cr-5Mo-0.25C | Superior resistance to galling, good corrosion resistance | Turbine components, exhaust valves |
MetcoClad 6250 | Co-29Cr-8.5W-1.5C | High oxidation and wear resistance | Hot section turbine components |
Haynes 188 | Co-22Cr-14W-0.1C | High temperature strength, oxidation resistance | Gas turbine blades, exhaust valves |
CoCrMo F-75 | Co-28Cr-6Mo-0.3C | Biocompatible, excellent wear resistance | Medical implants, dental applications |
Tribaloy T-400 | Co-8Cr-28Mo-1.2C | Exceptional wear and corrosion resistance in high-temperature applications | Pump seals, bearings |
Ultimet | Co-26Cr-9Mo-2W | Combines good toughness and corrosion resistance | Chemical processing equipment |
CoCrW Alloy L605 | Co-20Cr-15W-10Ni | Outstanding high-temperature oxidation resistance | Jet engines, nuclear applications |
Duron-25 | Co-25Cr-7W-1Mo | Extreme hardness and corrosion resistance | Wear plates, hard-facing applications |
CoCr Alloy MP35N | Co-21Cr-9Mo-10Ni-1.2Ti | Excellent fatigue strength and corrosion resistance | Medical devices, aerospace applications |
Specifications, Sizes, and Standards for CoCrW Powder
CoCrW powder comes in different sizes, depending on its intended use. Below are some common sizes, specifications, and standards used to assess the quality of the powder for different applications.
Specification | Typical Range | Details |
---|---|---|
Particle Size (µm) | 15-53 µm, 45-105 µm | Fine powders are used for 3D printing, while larger sizes are more suitable for hard-facing and thermal spraying applications. |
Hardness (HV) | 450-700 HV | Depending on the alloy, CoCrW powders exhibit high hardness, which makes them ideal for wear applications. |
Standards | ASTM F75, ISO 5832-4, AMS 5796 | These are industry-recognized standards for biomedical, aerospace, and wear-resistant applications of CoCrW alloys. |
CoCrW Powder Pricing and Suppliers
Pricing of CoCrW powder can vary significantly depending on the alloy composition, quantity purchased, and supplier. Below is a general comparison of suppliers and pricing details:
Supplier | Pricing (per kg) | Notable Features |
---|---|---|
Höganäs AB | $200 – $300 | Known for producing high-quality powder for additive manufacturing |
Sandvik Osprey | $250 – $400 | Offers a wide range of CoCrW powders for various industrial applications |
Carpenter Technology | $220 – $350 | Focuses on aerospace and medical applications |
Kennametal Stellite | $180 – $290 | Specializes in wear-resistant powders for tools and equipment |
Oerlikon Metco | $230 – $380 | Renowned for its high-performance alloys for gas turbines |
Advantages and Limitations of CoCrW Powder
Choosing the right material for a given application often involves weighing the pros and cons. Below are some of the advantages and limitations of CoCrW powder:
Advantages | Limitations |
---|---|
High wear and corrosion resistance | Higher cost compared to standard steels or other alloys |
Excellent high-temperature performance | Requires specialized handling and processing equipment |
Biocompatibility for medical uses | Hardness may make it difficult to machine |
Long lifespan in high-stress environments | Brittleness at very high carbon content levels |
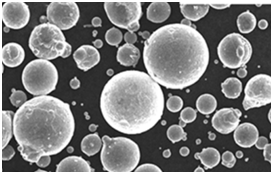
FAQs
Question | Answer |
---|---|
What are the main benefits of using CoCrW powders in manufacturing? | CoCrW powders offer superior wear resistance, corrosion resistance, and high-temperature performance, making them ideal for challenging environments like aerospace and medical applications. |
How does CoCrW compare to stainless steel? | While stainless steel is less expensive, CoCrW offers far better wear resistance and performance at high temperatures, though it can be more challenging to machine. |
Can CoCrW powder be used for 3D printing? | Yes, certain grades of CoCrW powder, like Stellite 6, are commonly used in additive manufacturing to create high-performance parts with complex geometries. |
Is CoCrW biocompatible? | Yes, many CoCrW alloys, particularly those with low carbon content like CoCrMo F-75, are used in medical implants because of their excellent biocompatibility and wear resistance. |
What industries most commonly use CoCrW powders? | CoCrW powders are widely used in aerospace, medical devices, energy, and tool manufacturing, especially in applications that require high durability and heat resistance. |
How is CoCrW powder typically processed? | Common processing methods include thermal spraying, additive manufacturing (3D printing), and hard-facing. |
Conclusion
CoCrW powder is a premium material highly valued for its exceptional performance in extreme conditions, such as high temperatures and corrosive environments. Its versatility makes it suitable for applications ranging from jet engines to medical implants. Whether you’re considering it for additive manufacturing, gas turbines, or wear-resistant components, CoCrW powder offers a reliable solution that is both durable and effective.
By thoroughly exploring its characteristics, applications, and suppliers, you can make an informed decision about how best to incorporate CoCrW into your next project.