Overview of Powder for Large Format Printing
Large format printing has revolutionized industries, from advertising to architectural modeling, allowing for the creation of detailed and vibrant images on a grand scale. But did you know that one of the key elements in this process is the type of powder used? Whether you’re a seasoned professional or just curious about how large format printing works, understanding the role of powder can significantly impact the quality and durability of your prints. In this guide, we’ll dive deep into the world of powders used in large format printing, focusing on metal powders and their specific applications.
We’ll explore various metal powder models, their compositions, characteristics, and the advantages they offer. With a thorough understanding of these materials, you can make informed decisions that enhance your printing projects. Ready to dive in? Let’s get started!
What is Powder for Large Format Printing?
In large format printing, the use of powder is crucial to achieving the desired print quality, texture, and durability. Powders are finely milled particles that are applied in layers, often through a process called selective laser sintering (SLS) or binder jetting. These powders can be composed of various materials, including metals, ceramics, and polymers, each offering unique properties suited to different applications.
In this article, we will focus specifically on metal powders, which are essential for creating strong, durable, and intricate prints. Metal powders are particularly favored in industries like aerospace, automotive, and medical devices due to their ability to produce high-strength components with complex geometries.
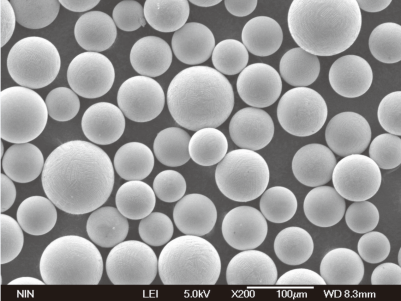
Types of Metal Powders for Large Format Printing
Choosing the right type of metal powder is critical for achieving optimal results in large format printing. Below, we outline some of the most popular metal powder models, highlighting their composition, properties, and suitable applications.
Metal Powder | Composition | Properties | Applications |
---|---|---|---|
Stainless Steel 316L | Iron, Chromium, Nickel | High corrosion resistance, excellent mechanical properties | Aerospace, medical devices, automotive parts |
Inconel 718 | Nickel, Chromium, Iron | High strength, heat resistance, oxidation resistance | Turbine blades, rocket engines, high-temperature environments |
Aluminum AlSi10Mg | Aluminum, Silicon, Magnesium | Lightweight, good thermal conductivity, high strength-to-weight ratio | Automotive, aerospace, lightweight components |
Titanium Ti64 | Titanium, Aluminum, Vanadium | High strength, low weight, biocompatibility | Medical implants, aerospace components, high-performance sports equipment |
Copper | Pure Copper | Excellent electrical conductivity, high thermal conductivity | Electrical components, heat exchangers, decorative elements |
Tool Steel H13 | Iron, Carbon, Chromium, Molybdenum, Vanadium | High hardness, wear resistance, heat resistance | Injection molds, die-casting tools, cutting tools |
Cobalt-Chrome (CoCr) | Cobalt, Chromium, Molybdenum | High wear resistance, biocompatibility, corrosion resistance | Dental implants, orthopedic implants, aerospace components |
Bronze | Copper, Tin | Good wear resistance, aesthetically pleasing finish | Sculptures, architectural features, bearings |
Nickel Alloy 625 | Nickel, Chromium, Molybdenum, Niobium | High strength, excellent fatigue and thermal fatigue resistance | Marine applications, chemical processing, nuclear reactors |
Maraging Steel (MS1) | Iron, Nickel, Cobalt, Molybdenum | High strength, excellent machinability, dimensional stability | Tooling, aerospace, high-strength components |
Composition of Powder for Large Format Printing
The composition of the powder is a crucial factor that determines its suitability for specific applications. Different compositions offer varying levels of strength, flexibility, and resistance to environmental factors like heat, corrosion, and wear.
Metal Powder | Primary Elements | Additives | Properties Derived from Composition |
---|---|---|---|
Stainless Steel 316L | Iron, Chromium, Nickel | Manganese, Silicon | Enhanced corrosion resistance, toughness |
Inconel 718 | Nickel, Chromium, Iron | Molybdenum, Niobium | Superior high-temperature strength and corrosion resistance |
Aluminum AlSi10Mg | Aluminum, Silicon, Magnesium | Copper | Improved strength-to-weight ratio, good casting properties |
Titanium Ti64 | Titanium, Aluminum, Vanadium | Iron | High strength, low density, biocompatibility |
Copper | Pure Copper | – | Excellent electrical and thermal conductivity |
Tool Steel H13 | Iron, Carbon, Chromium | Molybdenum, Vanadium | Enhanced hardness and heat resistance |
Cobalt-Chrome (CoCr) | Cobalt, Chromium | Molybdenum | High wear resistance, biocompatibility |
Bronze | Copper, Tin | Zinc, Lead | Good machinability, wear resistance |
Nickel Alloy 625 | Nickel, Chromium | Molybdenum, Niobium | Excellent fatigue resistance, high strength |
Maraging Steel (MS1) | Iron, Nickel, Cobalt | Molybdenum, Titanium | High toughness, age-hardening capabilities |
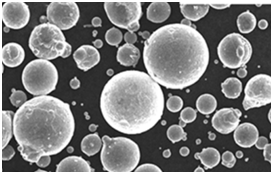
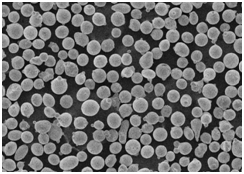
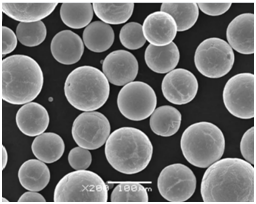
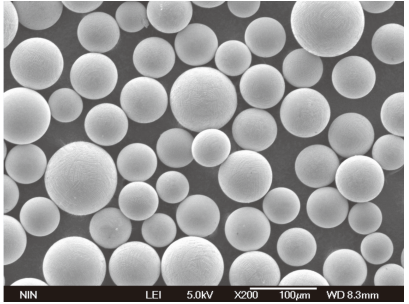
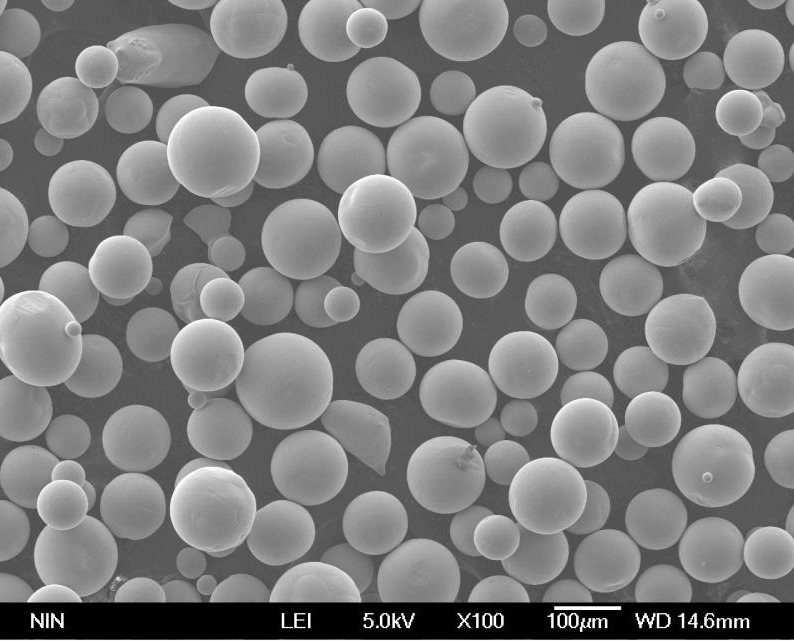
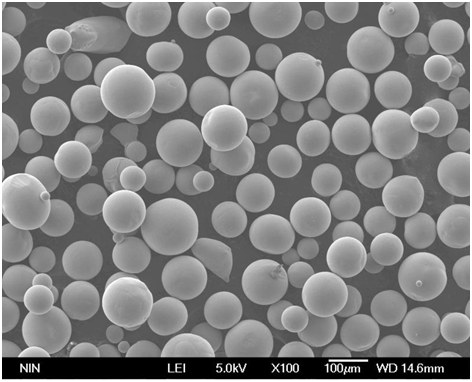
Characteristics of Powder for Large Format Printing
Understanding the characteristics of different powders is essential for selecting the right material for your printing needs. Characteristics such as particle size, shape, and flowability can affect the quality and consistency of the final print.
Characteristic | Importance in Printing | Metal Powder Example | Details |
---|---|---|---|
Particle Size | Affects surface finish and detail resolution | Stainless Steel 316L | Finer particles produce smoother surfaces |
Particle Shape | Influences powder flowability and packing density | Aluminum AlSi10Mg | Spherical particles enhance flowability |
Flowability | Impacts the uniformity of powder layers | Titanium Ti64 | Good flowability ensures consistent layer deposition |
Purity | Determines the mechanical properties and performance | Inconel 718 | High purity powders lead to better mechanical properties |
Density | Affects the weight and structural integrity of the print | Maraging Steel (MS1) | Higher density powders produce stronger parts |
Oxidation Resistance | Critical for applications in harsh environments | Nickel Alloy 625 | High oxidation resistance extends component life |
Thermal Conductivity | Important for heat dissipation in components | Copper | High thermal conductivity ideal for heat exchangers |
Applications of Powder for Large Format Printing
Metal powders are used in a wide range of applications, from aerospace and automotive to medical and decorative arts. The table below highlights some of the most common applications for the various metal powders used in large format printing.
Application | Metal Powder | Why It’s Used |
---|---|---|
Aerospace Components | Titanium Ti64, Inconel 718 | High strength, lightweight, heat resistance |
Medical Implants | Cobalt-Chrome (CoCr), Titanium Ti64 | Biocompatibility, corrosion resistance |
Automotive Parts | Aluminum AlSi10Mg, Stainless Steel 316L | Lightweight, high strength, corrosion resistance |
Tooling | Tool Steel H13, Maraging Steel (MS1) | High hardness, wear resistance, durability |
Electrical Components | Copper | Excellent electrical conductivity |
Heat Exchangers | Copper, Nickel Alloy 625 | High thermal conductivity, corrosion resistance |
Sculptures and Decorative Arts | Bronze | Aesthetic finish, good wear resistance |
Turbine Blades | Inconel 718, Nickel Alloy 625 | High strength, oxidation resistance |
Die-Casting Tools | Tool Steel H13 | High heat resistance, durability |
Sporting Goods | Titanium Ti64 | Lightweight, high performance |
Specifications, Sizes, and Standards
When selecting metal powders for large format printing, it’s essential to consider the specifications, sizes, and standards to ensure compatibility with your printing equipment and application requirements.
Metal Powder | Specifications | Particle Size Range (µm) | Standards |
---|---|---|---|
Stainless Steel 316L | ASTM A276 | 15-45 | ISO 5832-1 |
Inconel 718 | AMS 5662 | 20-63 | ASTM B637 |
Aluminum AlSi10Mg | ASTM B209 | 20-60 | ISO 3522 |
Titanium Ti64 | ASTM F136 | 15-45 | ISO 5832-3 |
Copper | ASTM B170 | 10-50 | ISO 1338 |
Tool Steel H13 | ASTM A681 | 15-53 | ISO 4957 |
Cobalt-Chrome (CoCr) | ASTM F1537 | 15-45 | ISO 5832-4 |
Bronze | ASTM B22 | 20-63 | ISO 19701 |
Nickel Alloy 625 | AMS 5666 | 20-45 | ASTM B443 |
Maraging Steel (MS1) | AMS 6512 | 15-53 | ISO 4957 |
Suppliers and Pricing Details
The market for metal powders is vast, with numerous suppliers offering various grades and specifications. Pricing can vary depending on factors such as purity, particle size, and quantity purchased.
Supplier | Metal Powder | Price Range ($ per kg) | Comments |
---|---|---|---|
Sandvik Osprey | Stainless Steel 316L | $70 – $100 | High-quality powder, consistent particle size |
Höganäs | Inconel 718 | $150 – $200 | Excellent high-temperature performance |
LPW Technology | Aluminum AlSi10Mg | $90 – $120 | Well-suited for lightweight applications |
AP&C | Titanium Ti64 | $200 – $250 | High purity, biocompatible |
Tekna | Copper | $80 – $110 | Ideal for electrical and thermal applications |
Carpenter Technology | Tool Steel H13 | $100 – $130 | Superior hardness and heat resistance |
EOS | Cobalt-Chrome (CoCr) | $180 – $220 | High wear resistance, biocompatibility |
GKN Additive | Bronze | $50 – $70 | Affordable, good wear resistance |
Velo3D | Nickel Alloy 625 | $140 – $180 | Excellent fatigue resistance |
Advanced Powders & Coatings | Maraging Steel (MS1) | $120 – $160 | High strength, easy machinability |
Comparing Pros and Cons of Metal Powders
Each metal powder has its advantages and limitations, depending on the application. Here’s a comparison of some of the key pros and cons of the metal powders discussed.
Metal Powder | Advantages | Disadvantages |
---|---|---|
Stainless Steel 316L | High corrosion resistance, good mechanical properties | Relatively heavy, lower thermal conductivity |
Inconel 718 | High strength at elevated temperatures, oxidation resistance | Expensive, difficult to machine |
Aluminum AlSi10Mg | Lightweight, good thermal conductivity | Lower strength compared to other metals |
Titanium Ti64 | High strength-to-weight ratio, biocompatibility | Expensive, challenging to work with |
Copper | Excellent electrical and thermal conductivity | Prone to oxidation, relatively soft |
Tool Steel H13 | High hardness, wear resistance | Brittle at low temperatures, expensive |
Cobalt-Chrome (CoCr) | High wear resistance, biocompatibility | Difficult to machine, expensive |
Bronze | Good wear resistance, aesthetically pleasing | Relatively low strength, prone to tarnishing |
Nickel Alloy 625 | Excellent fatigue and corrosion resistance | Expensive, heavy |
Maraging Steel (MS1) | High strength, excellent machinability | Expensive, susceptible to corrosion in certain environments |
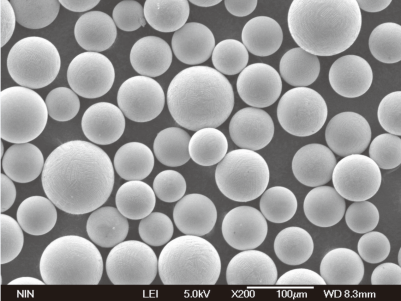
FAQ
What is the most commonly used metal powder for large format printing?
Stainless Steel 316L is one of the most commonly used metal powders due to its excellent corrosion resistance, mechanical properties, and relative affordability. It’s widely used in industries such as aerospace, automotive, and medical devices.
Why is Titanium Ti64 preferred in medical applications?
Titanium Ti64 is preferred in medical applications due to its high strength-to-weight ratio, biocompatibility, and corrosion resistance, making it ideal for implants and other medical devices that require a durable, lightweight material.
Can I use multiple types of metal powders in a single printing project?
Yes, it’s possible to use multiple types of metal powders in a single project, especially in advanced applications where different properties are required in different sections of the print. However, this requires sophisticated printing equipment and careful management of the printing process to avoid contamination between powders.
How does particle size affect the quality of the print?
Smaller particle sizes generally produce smoother surfaces and finer details, but they may also result in lower flowability, which can affect the consistency of the powder layers. Larger particles, on the other hand, can improve flowability but might lead to a rougher surface finish.
Is it possible to recycle metal powders after printing?
Yes, metal powders can often be recycled and reused after printing, although their properties may degrade slightly with each use. The recyclability depends on the specific type of powder and the printing process used.
What is the typical shelf life of metal powders?
The shelf life of metal powders can vary depending on the material and storage conditions. In general, metal powders should be stored in a dry, cool environment and used within a year to maintain optimal performance.