Overview of Metal Injection Molding (MIM)
Metal Injection Molding (MIM) is a groundbreaking manufacturing process that merges the versatility of plastic injection molding with the strength and integrity of metal. It’s a technology that has revolutionized the production of small, complex metal parts by providing a cost-effective, high-precision solution.
Imagine the convenience of producing intricate components that typically require multiple machining processes, all in a single step. That’s the magic of MIM. This process is particularly useful in industries such as aerospace, medical devices, automotive, and consumer electronics, where precision, consistency, and performance are non-negotiable.
But what exactly is Metal Injection Molding? How does it work? What are the materials used, and why is it gaining popularity across various industries? Let’s dive deeper into the world of MIM to uncover the intricacies of this innovative technology.
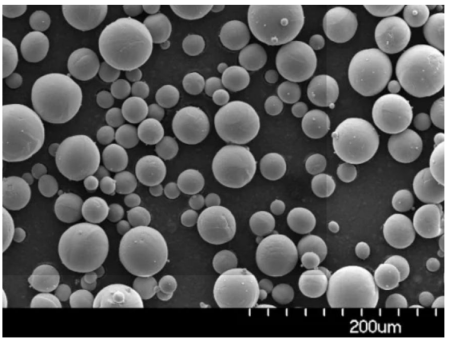
The Metal Injection Molding Process Explained
Before we get into the nitty-gritty details, let’s break down the MIM process into digestible chunks:
- Feedstock Preparation: The process begins with the preparation of the feedstock. Metal powders are mixed with a thermoplastic binder to form a homogeneous mixture. This mixture is then granulated into pellets that can be fed into the injection molding machine.
- Injection Molding: The feedstock pellets are heated and injected into a mold cavity, where they take the shape of the desired part. This stage is very similar to traditional plastic injection molding, but with the added challenge of maintaining the integrity of metal powders.
- Debinding: After the part is molded, the binder, which holds the metal particles together, must be removed. This is done through a process called debinding, where the part is heated in a controlled environment to evaporate or dissolve the binder.
- Sintering: The final stage involves sintering the debound part at high temperatures to fuse the metal particles together, resulting in a dense, solid metal component. The sintering process causes the part to shrink, which is carefully accounted for during the design phase to ensure the final dimensions are accurate.
- Post-Processing: Depending on the application, the sintered parts may undergo additional processes like machining, surface treatment, or heat treatment to enhance their properties or finish.
Advantages of Metal Injection Molding
So, why is MIM becoming the go-to process for many manufacturers? Here are some compelling reasons:
- Complexity and Precision: MIM allows for the production of highly complex geometries with tight tolerances that would be difficult or impossible to achieve with traditional metalworking methods.
- Material Variety: A wide range of metal powders can be used in MIM, including stainless steels, tool steels, titanium, and superalloys. This flexibility allows manufacturers to select the best material for their specific application.
- Cost-Effective for High Volumes: While the upfront costs for tooling and feedstock preparation are high, MIM becomes highly cost-effective when producing large quantities of parts. The ability to produce multiple parts in a single molding cycle further reduces costs.
- Minimal Waste: MIM is a near-net-shape process, meaning that the parts require little to no additional machining. This results in minimal material waste, making it an environmentally friendly option.
- Enhanced Mechanical Properties: MIM parts often exhibit superior mechanical properties compared to those made through other manufacturing methods, thanks to the fine microstructure achieved during sintering.
Types of Metal Powders Used in MIM
The choice of metal powder is crucial in the MIM process, as it directly influences the mechanical properties, surface finish, and overall performance of the final part. Here are some of the most commonly used metal powders in MIM:
Metal Powder | Composition | Properties | Applications |
---|---|---|---|
316L Stainless Steel | Fe-Cr-Ni-Mo | High corrosion resistance, good mechanical strength | Medical devices, watch components, food processing equipment |
17-4 PH Stainless Steel | Fe-Cr-Ni-Cu | High strength, excellent corrosion resistance, good hardness | Aerospace, firearms, surgical instruments |
440C Stainless Steel | Fe-Cr-C | High hardness, good wear resistance, moderate corrosion resistance | Bearings, knives, valves |
M2 Tool Steel | Fe-Cr-Mo-W-V | High hardness, excellent wear resistance, high temperature stability | Cutting tools, dies, molds |
Inconel 718 | Ni-Cr-Fe-Nb-Mo-Ti | High temperature resistance, excellent mechanical strength | Aerospace, turbine blades, nuclear reactors |
Titanium Ti-6Al-4V | Ti-Al-V | High strength-to-weight ratio, excellent corrosion resistance, biocompatibility | Medical implants, aerospace, marine applications |
Copper (C11000) | Cu | High electrical conductivity, good thermal conductivity, excellent malleability | Electrical connectors, heat exchangers, plumbing |
Kovar (FeNiCo) | Fe-Ni-Co | Low thermal expansion, good magnetic properties | Electronics, glass-to-metal seals, semiconductor packaging |
Tungsten (W) | W | High density, high melting point, good thermal and electrical conductivity | Radiation shielding, high-temperature furnaces, aerospace components |
Cobalt-Chromium (Co-Cr) | Co-Cr-Mo | High wear resistance, excellent biocompatibility, good mechanical properties | Orthopedic implants, dental prosthetics, turbine blades |
These metal powders are selected based on their compatibility with the MIM process and the specific requirements of the final part. For example, stainless steels are popular for their corrosion resistance, while tool steels are chosen for their hardness and wear resistance.
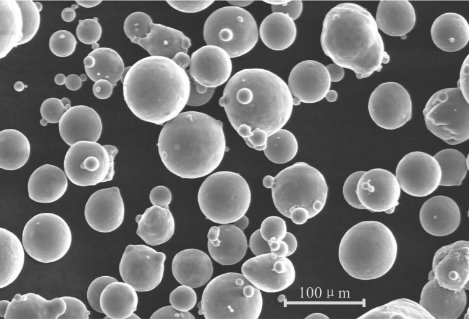
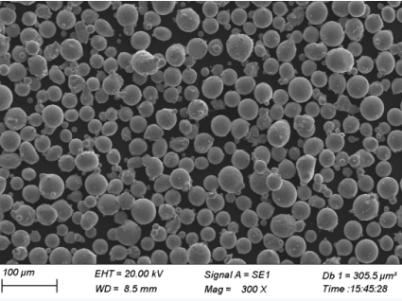
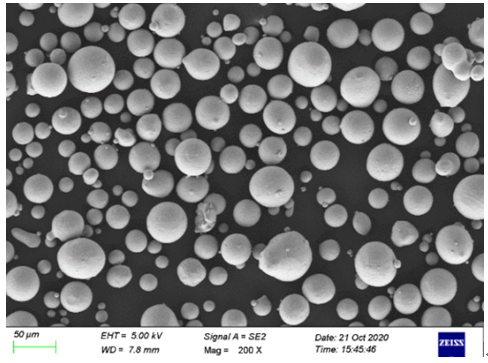
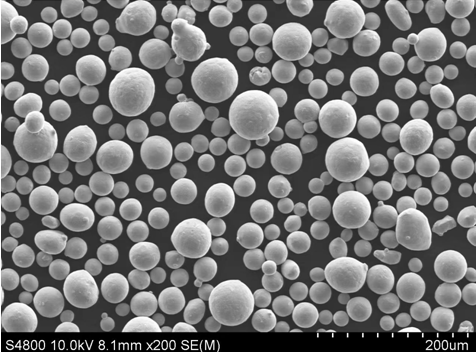
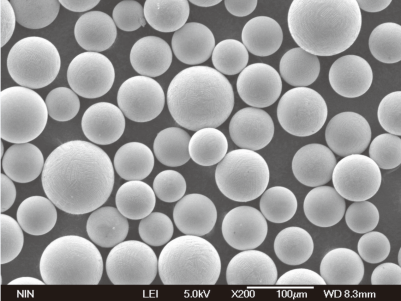
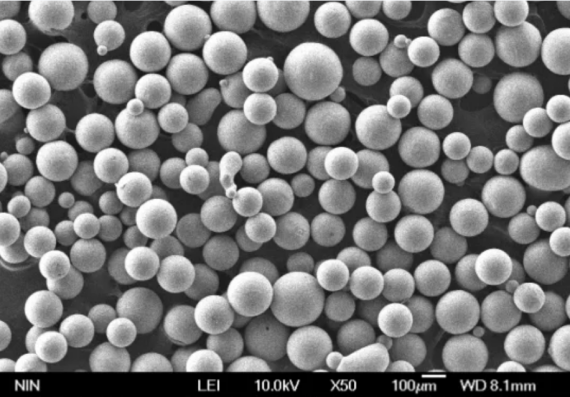
Composition and Characteristics of MIM Materials
The composition of the metal powder and binder mixture plays a critical role in determining the properties of the final MIM part. Here’s a closer look at the key characteristics of MIM materials:
Characteristic | Description |
---|---|
Particle Size | Fine powders with particle sizes typically in the range of 2-20 microns are used in MIM. Smaller particles provide better sinterability but may require more complex debinding processes. |
Binder System | The binder system is usually a mixture of polymers and waxes that hold the metal powder together during molding. The binder must be carefully formulated to ensure it can be removed without damaging the part. |
Sintering Behavior | The sintering temperature and time are crucial parameters that influence the final density, grain size, and mechanical properties of the part. Different metals require different sintering conditions. |
Density | MIM parts typically achieve densities between 95% and 99% of the theoretical density of the base metal. Higher densities result in better mechanical properties. |
Shrinkage | Parts typically shrink by 15-20% during sintering. Accurate prediction and control of shrinkage are essential for achieving the desired final dimensions. |
Mechanical Properties | MIM parts can achieve mechanical properties comparable to wrought materials, including high tensile strength, hardness, and ductility. |
Surface Finish | The surface finish of MIM parts is generally smooth, with typical roughness values (Ra) in the range of 1-5 microns. Post-processing can further improve the finish. |
Applications of Metal Injection Molding
MIM is a versatile technology with applications across various industries. Here’s a look at some of the most common uses:
Industry | Application | Examples |
---|---|---|
Aerospace | High-strength, lightweight components | Turbine blades, fuel nozzles, fasteners |
Medical | Biocompatible implants and surgical tools | Orthopedic implants, dental braces, endoscopic instruments |
Automotive | Precision components for engines and transmissions | Gears, sensors, fuel injectors |
Consumer Electronics | Small, complex parts with high durability | Smartphone components, camera lenses, connectors |
Firearms | High-strength components with tight tolerances | Triggers, hammers, slide releases |
Industrial | Wear-resistant tools and machinery parts | Cutting tools, pump components, bearings |
Jewelry | Complex, decorative pieces | Watch cases, clasps, intricate designs |
Specifications, Sizes, Grades, and Standards in MIM
When it comes to MIM, there are specific standards and specifications that manufacturers must adhere to, ensuring that the final products meet industry requirements. Here’s a summary:
Specification/Standard | Description | Applicable Materials |
---|---|---|
MPIF Standard 35 | Provides guidelines for mechanical properties of MIM parts | Various stainless steels, tool steels, and superalloys |
ASTM B883 | Standard specification for MIM parts used in medical devices | Titanium, stainless steel |
ISO 22068 | International standard for the testing of MIM parts | All MIM materials |
ASME B31.3 | Standards for MIM parts used in high-pressure environments | Stainless steel, nickel alloys |
DIN 17440 | European standard for MIM parts in automotive applications | Tool steels, stainless steels |
Comparison of Metal Injection Molding with Other Manufacturing Processes
How does Metal Injection Molding stack up against other manufacturing methods like traditional powder metallurgy, CNC machining, or casting? Let’s explore:
Parameter | MIM | Traditional Powder Metallurgy | CNC Machining | Casting |
---|---|---|---|---|
Complexity | High complexity achievable | Moderate complexity | High complexity, but with higher costs | High complexity, but limited by mold design |
Material Waste | Minimal waste (near-net-shape) | Low waste | High waste (chip formation) | Moderate waste |
Production Volume | Best suited for high volumes | Suitable for moderate volumes | Cost-effective for low volumes | Suitable for high volumes |
Tolerances | Tight tolerances achievable | Less precise than MIM | Very tight tolerances | Depends on mold precision |
Surface Finish | Smooth finish | Rough finish, requires secondary operations | Excellent finish | Varies, but generally rough |
Cost | High initial cost, low per-part cost | Moderate cost | High cost, especially for complex parts | Moderate to high cost |
Suppliers and Pricing of Metal Injection Molding Services
Choosing the right supplier for MIM services is crucial, as it directly impacts the quality, cost, and lead time of the final parts. Here’s a look at some of the leading suppliers and their pricing:
Supplier | Location | Specialties | Pricing (per part) |
---|---|---|---|
Advanced Powder Products | USA | Medical devices, aerospace components | $5 – $50 |
ARC Group Worldwide | USA | Automotive, firearms, industrial applications | $1 – $30 |
Indo-MIM | India | High-volume production, diverse materials | $0.50 – $20 |
Parmaco | Switzerland | Precision components, small parts | $2 – $40 |
Elnik Systems | Germany | Tooling, custom alloys | $10 – $100 |
ATW Companies | USA | Medical, automotive, consumer products | $3 – $25 |
CMG Technologies | UK | Custom MIM solutions, prototyping | $2 – $35 |

FAQs
Question | Answer |
---|---|
What are the typical lead times for MIM parts? | Lead times can vary depending on the complexity of the part and the volume required. Generally, it takes about 8-12 weeks from design to production for a new part. |
Can MIM be used for low-volume production? | While MIM is more cost-effective for high-volume production, it can still be used for low-volume runs if the part complexity and material requirements justify the upfront costs. |
What are the limitations of MIM? | MIM is not suitable for very large parts due to the high shrinkage during sintering. It’s also less effective for parts that require extremely tight tolerances without post-processing. |
How does MIM compare to additive manufacturing (3D printing)? | MIM offers better material properties and is more cost-effective for high-volume production compared to additive manufacturing, which is better suited for prototyping and low-volume, highly customized parts. |
What materials cannot be used in MIM? | Materials with very high melting points or those that cannot be effectively sintered, such as pure tungsten or certain ceramics, are not suitable for MIM. |