Overview of Multi Material Jetting (MMJ)
Welcome to the fascinating world of Multi Material Jetting (MMJ)! If you’re here, you’re probably curious about what makes MMJ a standout technology in the realm of 3D printing and additive manufacturing. Picture this: you have a printer, but instead of ink, it jets out tiny droplets of different materials to build complex structures layer by layer. Cool, right? MMJ offers unparalleled versatility and precision, making it a game-changer in industries ranging from aerospace to healthcare.
So, what exactly is Multi Material Jetting? Essentially, it’s a type of 3D printing that involves the simultaneous deposition of multiple materials. This technology allows for the creation of intricate parts with varied properties, combining metals, polymers, and ceramics in a single build process. It’s like having the ability to paint with a palette of materials, each adding its unique touch to the final masterpiece.
Introduction to Multi Material Jetting (MMJ)
Before we dive into the technical nitty-gritty, let’s set the stage. Multi Material Jetting is not just a futuristic technology; it’s already revolutionizing how we design and manufacture products. By enabling the combination of multiple materials in a single process, MMJ allows for the creation of parts with complex geometries and tailored properties. This means you can have a part that’s both flexible and rigid, or one that combines conductive and insulating materials, all created in one seamless process.
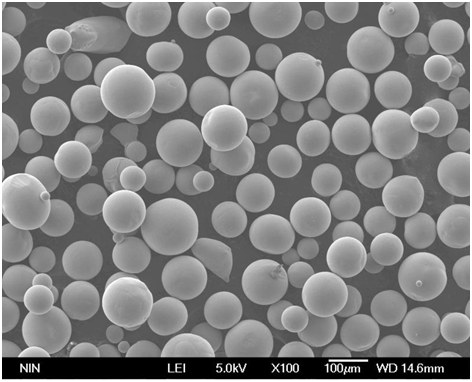
Composition of Multi Material Jetting (MMJ)
When we talk about MMJ, the composition of the materials used is crucial. Here’s a breakdown of the primary materials:
Material Type | Composition | Properties |
---|---|---|
Metals | Stainless steel, titanium, aluminum alloys | High strength, conductivity, thermal stability |
Polymers | ABS, PLA, photopolymers | Flexibility, biocompatibility, ease of processing |
Ceramics | Alumina, zirconia | Hardness, thermal resistance, electrical insulation |
Composites | Metal-polymer blends, ceramic-polymer blends | Enhanced mechanical properties, tailored conductivity and flexibility |
Each material brings something unique to the table. Metals offer robustness and durability, polymers provide flexibility and ease of use, while ceramics are perfect for high-temperature applications.
Characteristics of Multi Material Jetting (MMJ)
Understanding the characteristics of MMJ helps us appreciate its versatility and potential. Here are some key features:
- Precision and Accuracy: MMJ can achieve high-resolution prints with layer thicknesses as fine as 16 microns.
- Material Versatility: The ability to combine different materials in a single process opens up endless possibilities for creating multi-functional parts.
- Surface Finish: MMJ parts typically have a smooth surface finish, reducing the need for post-processing.
- Complex Geometries: Intricate designs that would be impossible with traditional manufacturing methods can be easily achieved.
Applications of Multi Material Jetting (MMJ)
The applications of MMJ span a wide range of industries. Let’s take a look at some of the most prominent ones:
Industry | Application | Examples |
---|---|---|
Healthcare | Prosthetics, dental implants, medical devices | Custom-fit prosthetics, biocompatible implants |
Aerospace | Lightweight components, complex assemblies | Jet engine parts, lightweight structural components |
Automotive | Prototyping, functional parts | Custom dashboards, ergonomic seats |
Consumer Goods | Customized products, high-detail models | Personalized jewelry, intricate miniatures |
Electronics | Printed circuit boards, wearable devices | Flexible PCBs, smartwatches |
Each industry benefits from the unique capabilities of MMJ, whether it’s creating lightweight yet strong aerospace components or highly detailed and personalized consumer goods.
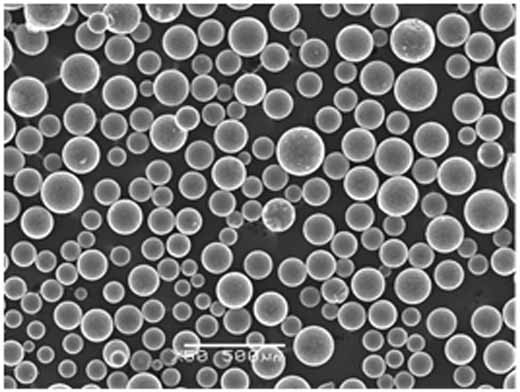
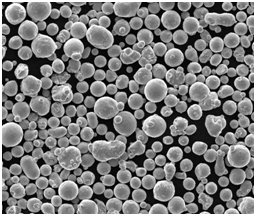
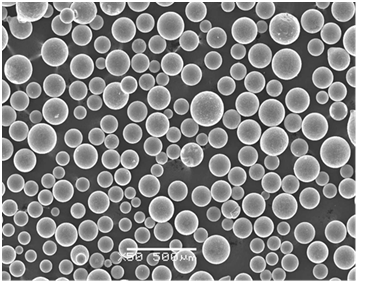
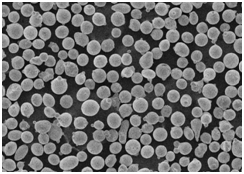
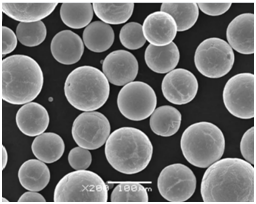
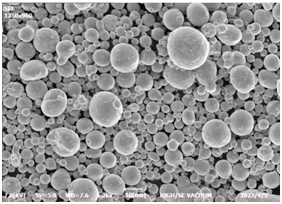
Specifications and Standards in Multi Material Jetting (MMJ)
When it comes to MMJ, adhering to specifications and standards is crucial for ensuring quality and consistency. Here’s a look at some of the key specifications and standards:
Parameter | Specification | Details |
---|---|---|
Layer Thickness | 16-32 microns | Determines the resolution and surface finish of the part |
Build Volume | Up to 1000 x 800 x 500 mm | Maximum size of the printable object |
Material Tolerance | ±0.1% | Precision in material deposition |
Printing Speed | 10-30 mm/hour | Varies based on material and part complexity |
Standards | ISO/ASTM 52900, ASTM F2792 | Standard guidelines for additive manufacturing processes |
Suppliers and Pricing Details for Multi Material Jetting (MMJ)
Finding the right supplier and understanding the costs involved is essential for anyone looking to utilize MMJ technology. Here’s a table with some prominent suppliers and pricing details:
Supplier | Materials Available | Pricing | Contact Information |
---|---|---|---|
Stratasys | Polymers, metals, composites | Starting at $50/kg | www.stratasys.com |
3D Systems | Polymers, metals | Starting at $70/kg | www.3dsystems.com |
HP | Polymers | Starting at $60/kg | www.hp.com |
Materialise | Polymers, ceramics, metals | Custom pricing | www.materialise.com |
EOS | Metals, polymers | Starting at $100/kg | www.eos.info |
Prices can vary based on material type, quantity, and supplier. It’s always a good idea to request quotes and compare options before making a decision.
Comparing Pros and Cons of Multi Material Jetting (MMJ)
Every technology has its strengths and weaknesses. Let’s compare the pros and cons of MMJ:
Aspect | Advantages | Disadvantages |
---|---|---|
Material Versatility | Can print with multiple materials simultaneously | Limited by material compatibility |
Precision | High resolution and accuracy | Slower printing speed compared to single-material printing |
Complexity | Capable of producing intricate geometries and multi-functional parts | Requires advanced software and expertise |
Surface Finish | Smooth finish reduces post-processing needs | May still require some finishing depending on the application |
Cost | Cost-effective for producing complex, low-volume parts | Initial setup and material costs can be high |
Detailed Descriptions of Metal Powder Models
Now, let’s dive into some specific metal powder models used in MMJ, highlighting their unique properties and applications:
- Stainless Steel 316L: Known for its corrosion resistance and strength, 316L is ideal for medical implants and food processing equipment.
- Titanium Ti6Al4V: Lightweight and strong, this alloy is commonly used in aerospace and biomedical applications.
- Inconel 718: A nickel-chromium alloy with excellent high-temperature properties, perfect for turbine blades and rocket engines.
- Aluminum AlSi10Mg: This alloy combines light weight with good mechanical properties, making it suitable for automotive and aerospace parts.
- Cobalt Chrome (CoCr): Known for its wear resistance and biocompatibility, CoCr is used in dental and orthopedic implants.
- Maraging Steel (MS1): This high-strength steel is used in tooling and high-stress components.
- Nickel Alloy 625: Resistant to corrosion and high temperatures, this alloy is used in chemical processing and marine applications.
- Copper (Cu): With excellent thermal and electrical conductivity, copper is used in electronics and heat exchangers.
- Tool Steel H13: Known for its hardness and resistance to thermal fatigue, H13 is used in die casting and molding.
- Gold (Au): Beyond its aesthetic appeal, gold is used in electronics and medical devices for its conductivity and biocompatibility.
Each metal powder model has its specific uses and advantages, making MMJ a versatile technology for various industries.
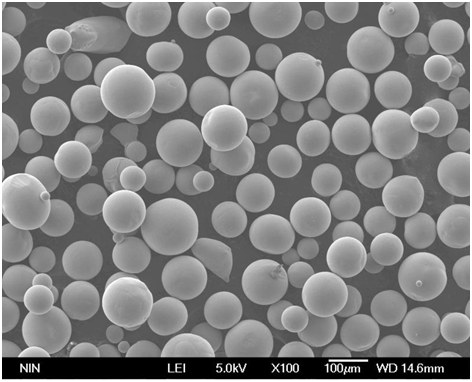
FAQ
Question | Answer |
---|---|
What is Multi Material Jetting (MMJ)? | MMJ is a 3D printing technology that deposits multiple materials simultaneously to create complex parts. |
What materials can be used in MMJ? | Metals, polymers, ceramics, and composites can all be used in MMJ. |
What are the benefits of MMJ? | High precision, material versatility, smooth surface finish, and the ability to create complex geometries. |
What are the limitations of MMJ? | High initial setup costs, slower printing speeds, and material compatibility issues. |
What industries benefit from MMJ? | Healthcare, aerospace, automotive, consumer goods, and electronics. |
How does MMJ compare to other 3D printing methods? | MMJ offers greater material versatility and precision but can be more complex and costly. |
What is the typical build volume for MMJ? | Up to 1000 x 800 x 500 mm, depending on the machine. |
Are there standard guidelines for MMJ? | Yes, ISO/ASTM 52900 and ASTM F2792 provide guidelines for additive manufacturing processes. |
How do I choose a supplier for MMJ materials? | Compare material availability, pricing, and supplier reputation. Request quotes for the best deal. |
What are the typical applications of MMJ? | Custom-fit prosthetics, lightweight aerospace components, functional automotive parts, and more. |