When it comes to ensuring the longevity and performance of brake discs, the right coating can make all the difference. Brake disc coatings powder offers an advanced solution that enhances durability, reduces corrosion, and improves overall braking efficiency. But what exactly goes into these coatings, and how do they work? Let’s dive into the world of brake disc coatings powder with a detailed exploration of their types, compositions, characteristics, and applications.
Overview
Brake disc coatings powder is engineered to provide superior protection and performance for brake discs. These coatings are typically made from various metal powders that offer specific benefits such as corrosion resistance, thermal stability, and improved friction properties. By applying these powders to brake discs, manufacturers can significantly extend the lifespan of the components and enhance their performance in demanding conditions.
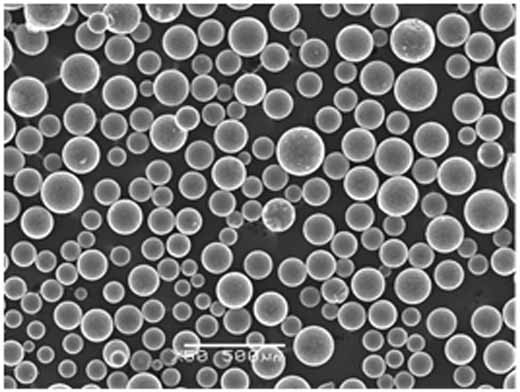
Types and Composition of Brake Disc Coatings Powder
Understanding the different types of brake disc coatings powder and their compositions is crucial for selecting the right one for your needs. Here’s a breakdown of some of the most commonly used metal powder models:
Type | Composition | Properties | Characteristics |
---|---|---|---|
Ceramic Powder | Alumina, Zirconia | High thermal stability, low wear rate | Excellent heat dissipation, resistant to high temperatures |
Iron-Based Powder | Iron, Carbon, Alloying Elements | High strength, good wear resistance | Cost-effective, widely used |
Nickel-Based Powder | Nickel, Chromium, Molybdenum | Corrosion resistance, high-temperature stability | Ideal for harsh environments |
Aluminum Oxide Powder | Aluminum Oxide | Lightweight, high hardness | Excellent wear resistance, used in high-performance applications |
Molybdenum Powder | Molybdenum, Nickel | High melting point, good thermal conductivity | Suitable for high-temperature applications |
Copper-Based Powder | Copper, Tin, Zinc | Good thermal and electrical conductivity | Used for its excellent friction properties |
Tungsten Carbide Powder | Tungsten, Carbon | Extremely hard, high wear resistance | Ideal for heavy-duty applications |
Silicon Carbide Powder | Silicon, Carbon | High hardness, thermal stability | Used in high-performance and high-temperature applications |
Chromium Oxide Powder | Chromium Oxide | High hardness, corrosion resistance | Provides a durable protective layer |
Titanium Dioxide Powder | Titanium Dioxide | High strength, light weight | Excellent corrosion resistance, used in specialized applications |
Characteristics of Brake Disc Coatings Powder
Brake disc coatings powder is designed to provide several key characteristics that improve the functionality and longevity of brake discs. Here’s what you can expect from these coatings:
- Corrosion Resistance: Prevents rust and corrosion, extending the life of the brake discs.
- Thermal Stability: Withstands high temperatures without degrading.
- Wear Resistance: Reduces wear and tear, maintaining optimal performance over time.
- Friction Properties: Enhances braking efficiency by optimizing the friction coefficient.
- Adhesion: Ensures the coating firmly bonds to the brake disc surface.
Applications of Brake Disc Coatings Powder
These coatings are used in a variety of applications, each demanding specific performance characteristics. Here’s a look at where these coatings are typically applied:
Application | Description |
---|---|
Automotive | Used in passenger cars and commercial vehicles to enhance brake performance and longevity. |
Aerospace | Applied to aircraft braking systems for reliable performance under extreme conditions. |
Industrial Machinery | Protects braking components in heavy machinery, ensuring durability and efficiency. |
Railway | Ensures long-lasting and effective braking in trains, which operate under high stress and varying conditions. |
Motorcycles | Enhances the braking system’s performance and longevity in motorcycles, which require precise and reliable braking. |
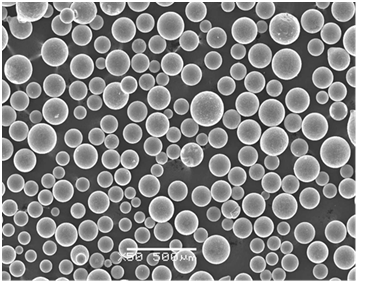
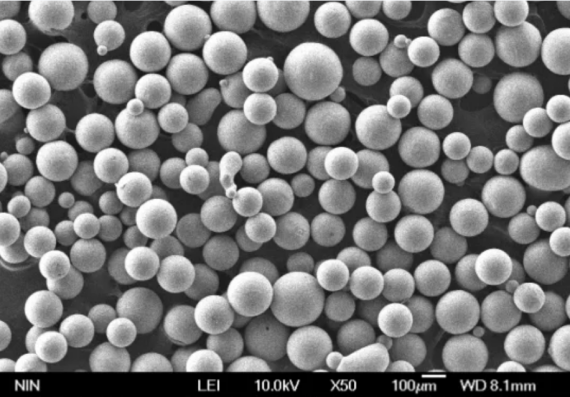
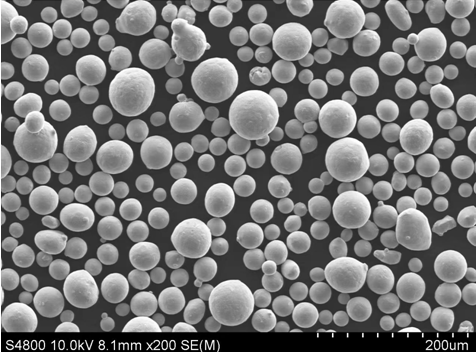
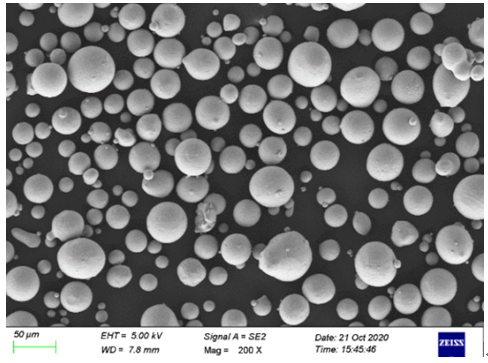
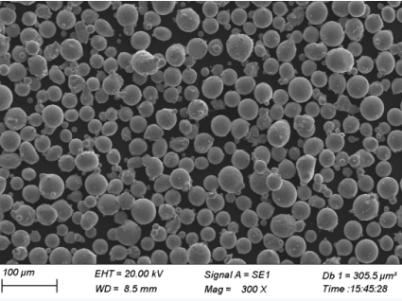
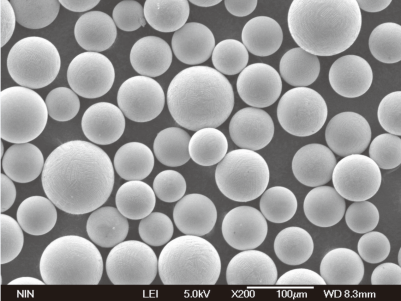
Specifications, Sizes, Grades, and Standards
Brake disc coatings powders are available in various specifications to meet different requirements. Here’s a table detailing some common specifications:
Specification | Sizes | Grades | Standards |
---|---|---|---|
Ceramic Powder | 5-50 microns | 99.9% purity | ASTM C1161 |
Iron-Based Powder | 10-100 microns | Various alloy grades | ASTM A255 |
Nickel-Based Powder | 15-45 microns | Inconel 625, 718 | AMS 5662 |
Aluminum Oxide Powder | 1-10 microns | 99.8% purity | ISO 6474-1 |
Molybdenum Powder | 5-40 microns | 99.5% purity | ASTM B387 |
Copper-Based Powder | 20-60 microns | Various bronze grades | ASTM B124 |
Tungsten Carbide Powder | 1-20 microns | 99.7% purity | ASTM B777 |
Silicon Carbide Powder | 0.5-10 microns | 99.5% purity | ASTM E1435 |
Chromium Oxide Powder | 5-50 microns | 99.9% purity | ISO 12847 |
Titanium Dioxide Powder | 10-50 microns | 99.8% purity | ASTM D476 |
Suppliers and Pricing Details
Choosing the right supplier for brake disc coatings powder can significantly impact the quality and cost-effectiveness of your braking system. Here’s a look at some reputable suppliers and their pricing details:
Supplier | Product | Price (per kg) | Location |
---|---|---|---|
ABC Coatings | Ceramic Powder | $100 | USA |
Metallic Solutions | Iron-Based Powder | $50 | Germany |
Nickel Experts | Nickel-Based Powder | $150 | Canada |
AluminaTech | Aluminum Oxide Powder | $75 | Japan |
MolyMakers | Molybdenum Powder | $120 | USA |
CopperCraft | Copper-Based Powder | $80 | China |
Tungsten World | Tungsten Carbide Powder | $200 | UK |
Silicon Pros | Silicon Carbide Powder | $90 | South Korea |
ChromeGuard | Chromium Oxide Powder | $110 | Italy |
Titanium Elite | Titanium Dioxide Powder | $95 | Australia |
Comparing Pros and Cons of Brake Disc Coatings Powder
When selecting a brake disc coating powder, it’s essential to weigh the advantages and limitations of each option. Here’s a comparison to help you make an informed decision:
Type | Pros | Cons |
---|---|---|
Ceramic Powder | Excellent heat resistance, long-lasting | High cost |
Iron-Based Powder | Cost-effective, good wear resistance | Moderate corrosion resistance |
Nickel-Based Powder | Superior corrosion resistance, high-temperature stability | Expensive |
Aluminum Oxide Powder | Lightweight, high hardness | Can be brittle |
Molybdenum Powder | Excellent thermal conductivity, high melting point | High cost |
Copper-Based Powder | Good friction properties, thermal conductivity | Can oxidize |
Tungsten Carbide Powder | Extremely hard, high wear resistance | Very expensive |
Silicon Carbide Powder | High hardness, thermal stability | Expensive |
Chromium Oxide Powder | High hardness, excellent corrosion resistance | High cost |
Titanium Dioxide Powder | High strength, light weight | Expensive |
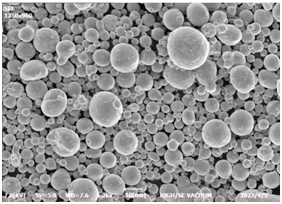
FAQ
What are brake disc coatings powder made of?
Brake disc coatings powder are composed of various metal powders such as ceramic, iron, nickel, aluminum oxide, molybdenum, copper, tungsten carbide, silicon carbide, chromium oxide, and titanium dioxide. Each type offers specific benefits tailored to different applications.
Why are brake disc coatings powder important?
These coatings enhance the performance and longevity of brake discs by providing corrosion resistance, thermal stability, wear resistance, and improved friction properties. This ensures reliable braking performance under various conditions.
How do I choose the right brake disc coatings powder?
Selecting the right powder depends on your specific needs, such as the application, operating conditions, and budget. Consider factors like thermal stability, wear resistance, and corrosion resistance when making your choice.
Where can I buy brake disc coatings powder?
You can purchase brake disc coatings powder from various suppliers worldwide. Some reputable suppliers include ABC Coatings, Metallic Solutions, Nickel Experts, AluminaTech, and more. Prices vary depending on the type and quantity of the powder.
What are the advantages of ceramic brake disc coatings powder compared to iron-based powder?
Ceramic brake disc coatings offer superior heat resistance and durability compared to iron-based powders. However, they are also more expensive. Iron-based powders are more cost-effective and provide good wear resistance but may not offer the same level of thermal stability.
Can I use brake disc coatings powder for high-performance vehicles?
Yes, certain types of brake disc coatings powder, such as aluminum oxide, silicon carbide, and tungsten carbide, are specifically designed for high-performance applications due to their excellent thermal stability and wear resistance.
How is brake disc coatings powder applied?
The powder is typically applied using techniques such as thermal spraying, which involves heating the powder and spraying it onto the brake disc surface.