The centrifugal atomization process is a fascinating and intricate technique used to produce fine metal powders with a high degree of precision and uniformity. If you’ve ever wondered how those perfectly spherical metal powders are made, or if you’re curious about the nitty-gritty details of the process, then you’re in the right place. Buckle up, because we’re diving deep into the world of centrifugal atomization, exploring its ins and outs, and uncovering the secrets behind this remarkable technology.
Overview of Centrifugal Atomization Process
Centrifugal atomization is a metal powder production method where molten metal is transformed into fine droplets by a spinning disc or cup. These droplets solidify as they are flung outward, resulting in spherical metal powders. The process is highly controlled, allowing for the production of powders with specific characteristics, such as particle size distribution and purity.
Key Details
- Technology: Centrifugal atomization
- Primary Use: Production of metal powders
- Core Mechanism: Spinning disc or cup
- Result: Fine, spherical metal powders
- Applications: Additive manufacturing, powder metallurgy, coatings, and more
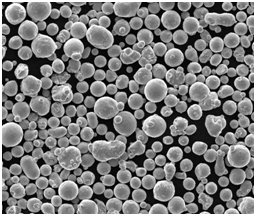
Composition of Centrifugal Atomization Process
Understanding the composition of the centrifugal atomization process is essential for grasping how it works and why it’s so effective.
Component | Description |
---|---|
Molten Metal | The raw material, typically metals like aluminum, titanium, steel, or nickel alloys. |
Spinning Device | A disc or cup that spins at high speeds to disperse the molten metal. |
Cooling Medium | Often an inert gas or air that cools and solidifies the metal droplets. |
Collection Chamber | Area where the solidified metal powders are collected. |
Control Systems | Systems for monitoring and adjusting temperature, speed, and other parameters. |
Types of Metals Used
Different metals and alloys can be processed through centrifugal atomization, each with unique properties and applications.
Metal/Alloy | Properties | Applications |
---|---|---|
Aluminum Alloys | Lightweight, corrosion-resistant | Aerospace, automotive, consumer electronics |
Titanium Alloys | High strength-to-weight ratio, biocompatible | Medical implants, aerospace |
Stainless Steel | Corrosion-resistant, durable | Medical devices, industrial equipment |
Nickel Alloys | Heat-resistant, corrosion-resistant | Turbines, high-temperature environments |
Copper Alloys | Conductive, malleable | Electrical components, heat exchangers |
Properties and Characteristics of Centrifugal Atomization Process
The properties of powders produced by centrifugal atomization are crucial for their application in various industries. Let’s break down the main characteristics.
Property | Description |
---|---|
Particle Size | Typically ranges from a few micrometers to several hundred micrometers, depending on the process parameters. |
Shape | Predominantly spherical, which enhances flowability and packing density. |
Purity | High purity due to controlled environment and minimal contamination. |
Density | Uniform density, which is critical for applications requiring consistent material properties. |
Surface Finish | Smooth surface finish, beneficial for applications in additive manufacturing and coatings. |
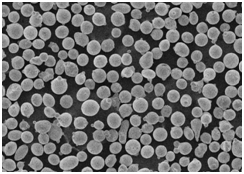
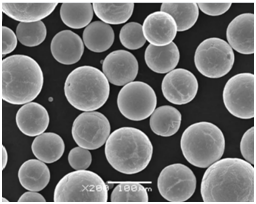
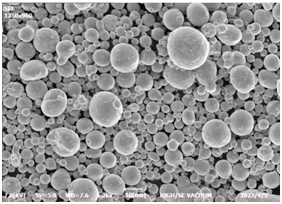

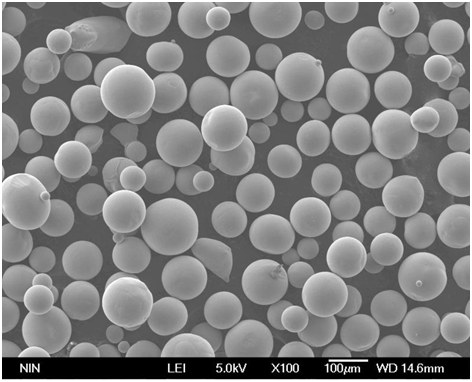
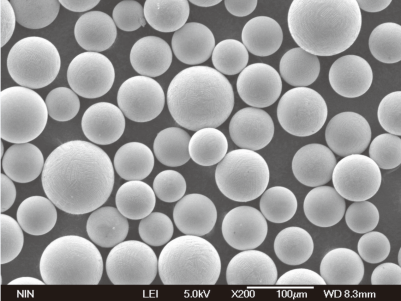
Grades and Standards of Centrifugal Atomization Process
Different grades and standards ensure that the metal powders produced meet the specific needs of various applications.
Grade | Standard | Description |
---|---|---|
Grade A | ASTM B330 | High purity, suitable for aerospace and medical applications. |
Grade B | ISO 9001 | Standard quality, used in general industrial applications. |
Grade C | AMS 4999 | High strength and durability, often used in automotive and structural applications. |
Grade D | MIL-STD-3021 | Military standard, ensuring reliability under extreme conditions. |
Grade E | JIS Z8901 | Japanese industrial standard, widely used in electronics and precision equipment. |
Applications of Centrifugal Atomization Process
The versatility of metal powders produced by centrifugal atomization opens the door to a wide array of applications.
Application | Description |
---|---|
Additive Manufacturing | Used in 3D printing for creating complex geometries with high precision and minimal waste. |
Powder Metallurgy | Utilized in forming metal parts with intricate shapes and excellent mechanical properties. |
Thermal Spraying | Employed in coating surfaces to enhance wear resistance, corrosion resistance, and thermal protection. |
MIM (Metal Injection Molding) | Enables the production of small, intricate parts with high density and strength. |
Electronics | Used in manufacturing components like capacitors, inductors, and heat sinks. |
Specific Metal Powder Models
Let’s delve into specific metal powder models produced through centrifugal atomization, highlighting their unique properties and applications.
1. Aluminum Alloy Powder (AlSi10Mg)
- Properties: Lightweight, high strength, good corrosion resistance
- Applications: Aerospace components, automotive parts, high-performance electronics
2. Titanium Alloy Powder (Ti6Al4V)
- Properties: Excellent biocompatibility, high strength-to-weight ratio, corrosion-resistant
- Applications: Medical implants, aerospace parts, high-performance sporting goods
3. Stainless Steel Powder (316L)
- Properties: Corrosion-resistant, durable, good mechanical properties
- Applications: Medical devices, food processing equipment, chemical processing
4. Nickel Alloy Powder (Inconel 718)
- Properties: High temperature and corrosion resistance, good mechanical properties
- Applications: Turbine blades, high-temperature aerospace components, oil and gas industry
5. Copper Alloy Powder (CuSn10)
- Properties: Excellent electrical and thermal conductivity, corrosion-resistant
- Applications: Electrical components, heat exchangers, bearings
6. Cobalt-Chromium Alloy Powder (CoCrMo)
- Properties: High wear resistance, biocompatibility, excellent mechanical properties
- Applications: Dental implants, orthopedic implants, aerospace components
7. Tool Steel Powder (H13)
- Properties: High hardness, excellent wear resistance, good thermal stability
- Applications: Injection molds, die-casting dies, high-temperature tooling
8. Magnesium Alloy Powder (AZ91D)
- Properties: Lightweight, good mechanical properties, corrosion-resistant
- Applications: Automotive parts, aerospace components, lightweight structures
9. Bronze Powder (Cu10Sn)
- Properties: Good wear resistance, corrosion-resistant, high conductivity
- Applications: Bearings, bushings, electrical contacts
10. High-Speed Steel Powder (M2)
- Properties: High hardness, excellent wear resistance, good toughness
- Applications: Cutting tools, drill bits, industrial knives
Suppliers and Pricing Details
Choosing the right supplier and understanding pricing is crucial for sourcing metal powders. Here’s a look at some prominent suppliers and their pricing details.
Supplier | Metal Powder | Pricing (per kg) | Notes |
---|---|---|---|
Höganäs AB | Aluminum Alloy (AlSi10Mg) | $50 – $70 | High-quality powders for additive manufacturing. |
Sandvik Osprey | Titanium Alloy (Ti6Al4V) | $150 – $200 | Premium grade, suitable for medical and aerospace applications. |
Carpenter Technology | Stainless Steel (316L) | $60 – $80 | Widely used in industrial and medical applications. |
AMETEK Specialty Metal Products | Nickel Alloy (Inconel 718) | $200 – $250 | High-performance powders for extreme environments. |
GKN Hoeganaes | Copper Alloy (CuSn10) | $30 – $50 | High conductivity powders for electrical applications. |
Kennametal | Tool Steel (H13) | $80 – $100 | Reliable supplier for high-strength tooling materials. |
LPW Technology | High-Speed Steel (M2) | $100 – $150 | Leading provider of high-quality metal powders for cutting tools. |
AP&C (a GE Additive company) | Cobalt-Chromium (CoCrMo) | $300 – $350 | Premium grade for medical and aerospace applications. |
Praxair Surface Technologies | Magnesium Alloy (AZ91D) | $40 – $60 | Lightweight powders for automotive and aerospace applications. |
Royal Metal Powders | Bronze Powder (Cu10Sn) | $20 – $40 | Cost-effective powders for industrial applications. |
Pros and Cons of Centrifugal Atomization Process
Every technology has its strengths and weaknesses. Let’s compare the advantages and limitations of the centrifugal atomization process.
Advantages
- High Purity: The controlled environment minimizes contamination, resulting in high-purity powders.
- Uniform Particle Size: The process produces powders with consistent particle size distribution.
- Spherical Particles: The spherical shape of particles enhances flowability and packing density.
- Versatility: Suitable for a wide range of metals and alloys.
- Scalability: Can be scaled up for industrial production.
Limitations
- Cost: High initial investment in equipment and technology.
- Complexity: Requires precise control of process parameters.
- Material Limitations: Not all materials are suitable for centrifugal atomization.
- Energy Consumption: High energy usage due to the need for melting and spinning metals at high speeds.
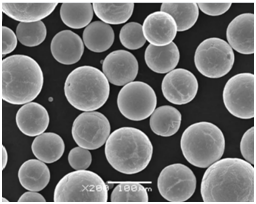
FAQs
Question | Answer |
---|---|
What is centrifugal atomization? | It’s a process where molten metal is spun rapidly to produce fine, spherical metal powders. |
What metals can be used? | Common metals include aluminum, titanium, stainless steel, nickel alloys, and copper. |
What are the applications of metal powders? | Applications include additive manufacturing, powder metallurgy, thermal spraying, and electronics. |
What are the benefits of spherical particles? | Spherical particles have better flowability, packing density, and uniformity. |
How is particle size controlled? | Particle size is controlled by adjusting the speed of the spinning device and cooling rates. |
Why is purity important? | High purity ensures better performance and reliability in critical applications. |
What is the cost range for metal powders? | Costs can vary widely, from $20 per kg for common alloys to $350 per kg for high-performance materials. |
How do I choose a supplier? | Consider factors like quality, reliability, cost, and the specific requirements of your application. |
Conclusion
The centrifugal atomization process is a marvel of modern engineering, offering a highly controlled method for producing fine metal powders with unparalleled precision and quality. From the aerospace and automotive industries to medical applications and beyond, the metal powders produced through this process are indispensable in today’s advanced manufacturing landscape. Whether you’re a seasoned engineer, a curious hobbyist, or someone in between, understanding this process provides valuable insights into the world of material science and technology.
Remember, while the process itself might seem complex, its applications are far-reaching and its impact, truly transformative. So next time you hold a piece of 3D printed metal or a high-performance turbine blade, you’ll know the remarkable journey it undertook from molten metal to precision-crafted powder.