From powering advanced electronics to enhancing the performance of industrial machinery, copper alloys powder has emerged as a critical material in various industries. This article explores the world of copper alloys powder, delving into its properties, applications, production methods, and safety considerations.
Understanding Copper Alloys Powder
Copper alloys powder is a finely divided form of metals derived from copper and other elements. These alloys are meticulously engineered to leverage the advantageous properties of both copper and the alloying elements. The result is a versatile material with improved strength, thermal conductivity, and corrosion resistance.
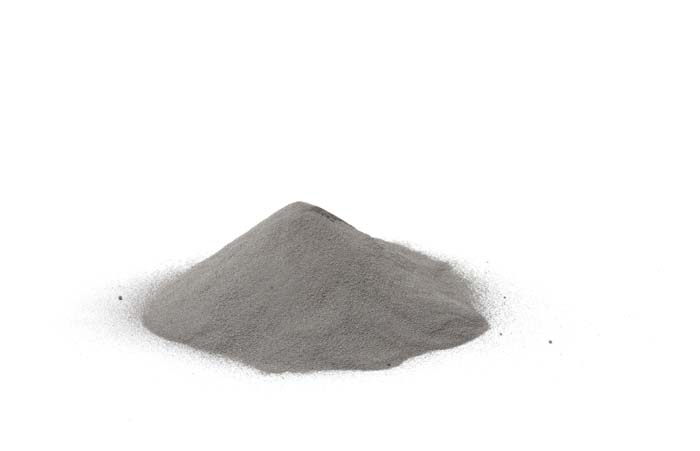
Advantages of Copper Alloys Powder
Enhanced Strength and Durability
Copper alloys powder significantly boosts the mechanical properties of the materials it’s mixed with. Through careful formulation, manufacturers can tailor the strength and durability of the final product, making it suitable for various load-bearing applications.
Excellent Thermal Conductivity
One of copper’s inherent qualities is its exceptional thermal conductivity. When this property is harnessed in powder form, it becomes an invaluable component in heat exchangers, electronic devices, and other heat-sensitive applications.
Corrosion Resistance
Copper alloys powder possesses inherent corrosion resistance, making it a prime choice for environments where exposure to moisture and chemicals is a concern. This property extends the lifespan of components and reduces maintenance requirements.
Common Applications
Electronics Industry
Copper alloys powder plays a pivotal role in the miniaturization of electronic devices. Its high electrical conductivity ensures optimal performance in intricate circuits and connectors.
Automotive Sector
In automotive manufacturing, copper alloys powder finds its way into brake pads, bearings, and even engine components. Its wear resistance and thermal properties contribute to the efficiency and safety of vehicles.
Aerospace Applications
Aerospace engineers utilize copper alloys powder for its lightweight yet robust characteristics. From critical structural parts to electrical connections, this material withstands the demanding conditions of space travel.
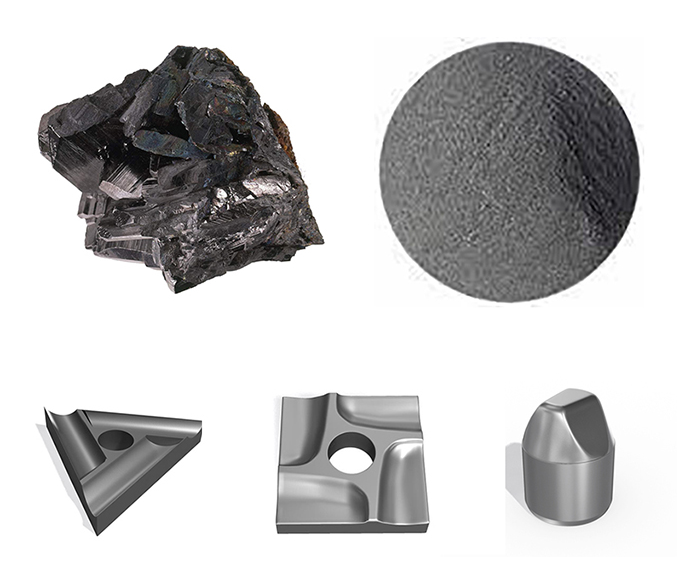
Types of Copper Alloys Powder
Bronze Powders
Combining copper with elements like tin and aluminum results in bronze powders. These powders find application in artistic casting, bearings, and self-lubricating parts.
Brass Powders
Zinc is the key addition in brass powders, yielding materials suitable for decorative applications, corrosion-resistant coatings, and musical instruments.
Copper-Nickel Powders
Copper-nickel powders excel in marine environments due to their resistance to seawater corrosion. They are vital in naval architecture and offshore industries.
Production Methods
Atomization
Atomization involves spraying molten metal through a nozzle to create fine droplets that solidify into powder upon contact with air. This method produces spherical particles with uniform properties.
Electrolysis
Electrolysis deposits metal onto a cathode in powder form, yielding materials with controlled particle sizes and shapes.
Reduction Process
A reduction reaction produces copper alloys powder by reducing metal compounds using hydrogen or other reducing agents.
Factors Affecting Powder Characteristics
Particle Size Distribution
Particle size influences the powder’s flowability, packing density, and sintering behavior. Different applications demand specific particle size ranges.
Chemical Composition
The selection of alloying elements and their proportions directly impacts the final properties of the copper alloys powder.
Production Parameters
Variables like temperature, pressure, and gas composition during production affect the powder’s purity and morphology.
Handling and Safety Considerations
Dust Control Measures
Powder handling requires proper ventilation and dust control to minimize exposure risks.
Personal Protective Equipment (PPE)
Workers must use appropriate PPE to prevent skin and respiratory contact with powders.
Future Trends and Developments
As technology advances, copper alloys powder is poised to find new applications in emerging fields such as 3D printing, where its material properties can be harnessed for intricate designs and functional prototypes.
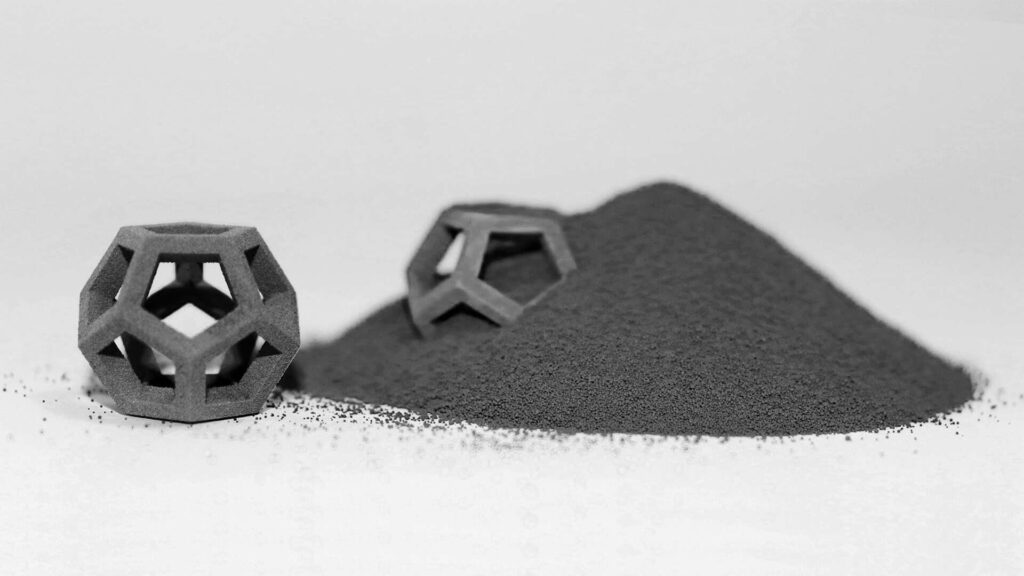
Conclusion
Copper alloys powder stands as a testament to the remarkable synergy of science and engineering. Its widespread applications, from electronics to aerospace, underscore its vital role in modern industry. As research continues and new production techniques emerge, the possibilities for this remarkable material are boundless.
FAQs
- Is copper alloys powder flammable? Copper alloys powder is not flammable, but precaution should be taken to prevent dust explosions.
- Can copper alloys powder be recycled? Yes, copper alloys powder can be recycled through suitable processes.
- Are there health risks associated with copper alloys powder? Prolonged inhalation of copper alloys powder dust can lead to health issues; thus, proper safety measures are essential.
- How are the properties of copper alloys powder tailored for specific applications? By carefully selecting alloying elements and controlling production parameters, manufacturers customize the powder’s properties.
- What role does copper alloys powder play in sustainable development? Copper alloys powder’s durability and recyclability contribute to sustainability by extending the lifespan of products and reducing waste.