1. Introduction
Inconel, a family of nickel-based superalloys, has garnered significant attention in the manufacturing industry due to its exceptional properties and performance in extreme conditions. With the emergence of additive manufacturing, also known as 3D printing, the production of complex and high-performance components using Inconel has become more accessible and efficient. This article explores the world of Inconel additive manufacturing, delving into its advantages, applications, challenges, technological advances, and future prospects.
2. What is Inconel?
Before diving into Inconel additive manufacturing, it is crucial to understand what Inconel is and why it holds such significance in various industries. Inconel is a trademarked name for a group of nickel-chromium-based superalloys known for their outstanding resistance to corrosion, heat, and high mechanical stress. These alloys are commonly used in extreme environments, including aerospace, chemical processing, and marine applications. Inconel alloys offer excellent strength, oxidation resistance, and creep resistance at elevated temperatures, making them ideal for critical applications.
3. Additive Manufacturing: A Brief Overview
Additive manufacturing, often referred to as 3D printing, is a transformative technology that enables the creation of three-dimensional objects layer by layer. Unlike traditional subtractive manufacturing methods, such as machining or casting, additive manufacturing builds up a component from scratch, using computer-aided design (CAD) models as a blueprint. This innovative approach offers numerous advantages, including design freedom, reduced waste, and increased customization.
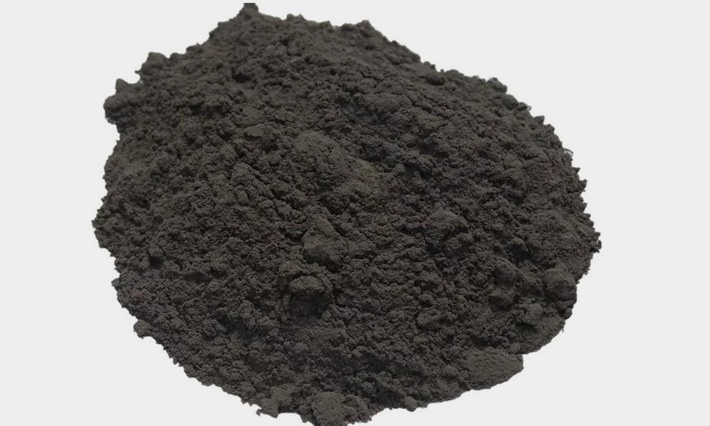
4. Inconel Additive Manufacturing: Advantages and Applications
Inconel additive manufacturing has opened up new avenues for the production of complex components that were previously challenging or impossible to manufacture using conventional methods. Let’s explore some of the key advantages and applications of Inconel additive manufacturing.
4.1 Aerospace Industry
The aerospace industry has been quick to embrace Inconel additive manufacturing due to its ability to produce lightweight, high-strength components with intricate geometries. Additive manufacturing allows for the production of complex turbine blades, fuel nozzles, and structural components with reduced weight and improved performance. The ability to consolidate multiple parts into a single component enhances overall efficiency and reduces assembly time.
4.2 Automotive Industry
Inconel additive manufacturing also finds applications in the automotive industry, particularly in high-performance and racing vehicles. By utilizing additive manufacturing techniques, manufacturers can produce exhaust systems, turbocharger components, and engine parts with superior heat resistance and mechanical properties. The lightweight nature of Inconel alloys aids in improving fuel efficiency and overall performance.
4.3 Medical Sector
The medical sector has witnessed remarkable advancements with the integration of Inconel additive manufacturing. Customized implants, prosthetics, and surgical instruments can be tailored to individual patients’ needs, offering improved functionality and patient outcomes. Additionally, Inconel’s biocompatibility and corrosion resistance make it an excellent choice for medical applications.
4.4 Oil and Gas Industry
Inconel alloys have long been utilized in the oil and gas industry due to their ability to withstand harsh operating conditions. With additive manufacturing, the production of corrosion-resistant downhole tools, heat exchangers, and valves becomes more efficient. The ability to rapidly manufacture spare parts on-demand reduces downtime and maintenance costs.
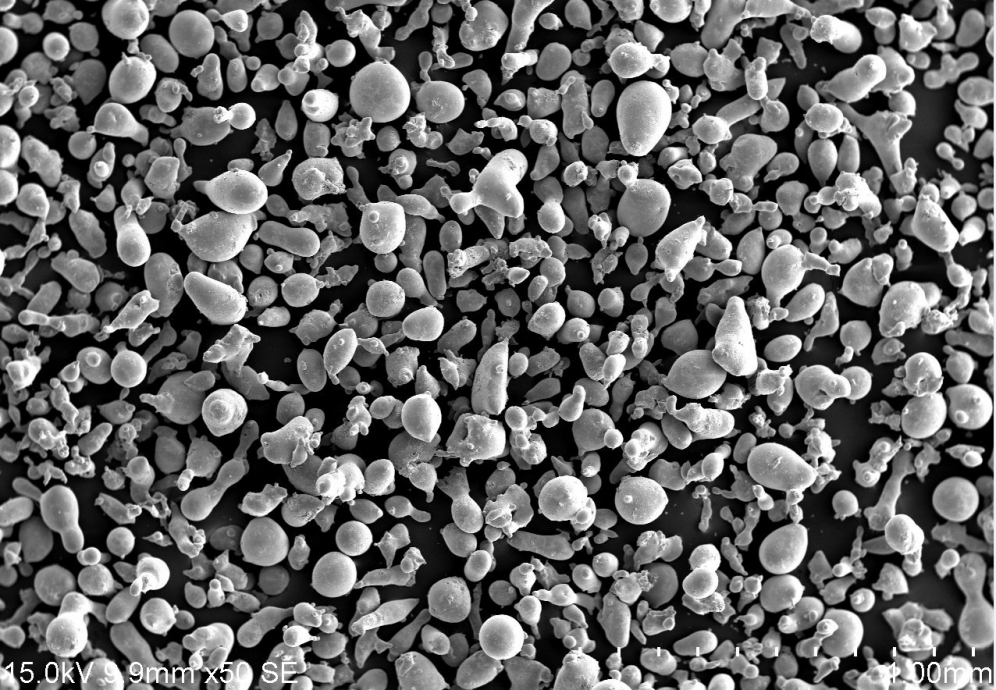
5. Challenges and Limitations of Inconel Additive Manufacturing
While Inconel additive manufacturing offers numerous advantages, it also presents several challenges and limitations that need to be addressed for wider adoption.
5.1 Material Properties
Inconel alloys possess unique material properties, including high melting points and thermal expansion coefficients, which can pose challenges during the additive manufacturing process. Optimizing parameters such as laser power, scanning speed, and powder bed temperature is critical to achieve desirable material properties in the final component.
5.2 Process Complexity
Additive manufacturing of Inconel components involves complex thermal cycles, rapid solidification, and potential microstructural defects. Understanding and controlling these intricate process dynamics require expertise and advanced process monitoring techniques. Process optimization and parameter selection play a crucial role in ensuring the quality and reliability of the manufactured parts.
5.3 Quality Control
Maintaining quality control in Inconel additive manufacturing is essential to meet industry standards and certification requirements. Inspecting and validating complex geometries, internal structures, and surface finishes demand innovative non-destructive testing methods. Ensuring consistent quality throughout the manufacturing process is imperative to avoid component failure and ensure safety.
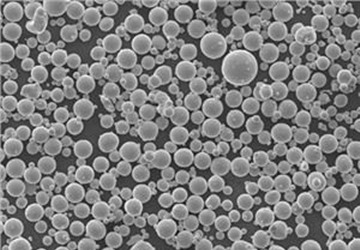
6. Advances in Inconel Additive Manufacturing Technologies
To overcome the challenges mentioned earlier, researchers and industry experts have made significant strides in advancing Inconel additive manufacturing technologies. Let’s explore some of the prominent techniques utilized in the production of Inconel components.
6.1 Laser Powder Bed Fusion (LPBF)
Laser Powder Bed Fusion, also known as Selective Laser Melting (SLM), is a widely adopted technique for Inconel additive manufacturing. It involves selectively melting a layer of powdered Inconel using a laser beam, followed by the addition of subsequent layers until the desired part is fully formed. LPBF offers excellent precision, control, and the ability to produce intricate geometries.
6.2 Electron Beam Melting (EBM)
Electron Beam Melting utilizes an electron beam instead of a laser to selectively melt the powdered Inconel. EBM offers advantages such as faster build rates, reduced residual stress, and improved part density. This technique is well-suited for large-scale components and finds applications in the aerospace and power generation industries.
6.3 Directed Energy Deposition (DED)
Directed Energy Deposition employs a focused energy source, such as a laser or electron beam, to melt the Inconel powder as it is being deposited. This technique enables the manufacturing of near-net-shape components, repair of existing parts, and the ability to incorporate multiple materials within a single build. DED offers flexibility and versatility in terms of component size and complexity.
7. Future Trends and Potential Developments
The future of Inconel additive manufacturing looks promising, with ongoing research and development efforts focusing on addressing the existing limitations and exploring new applications. Some potential developments include the use of hybrid manufacturing techniques, improved process simulation tools, and advancements in post-processing and surface finishing. As technology continues to evolve, we can expect Inconel additive manufacturing to revolutionize various industries further.
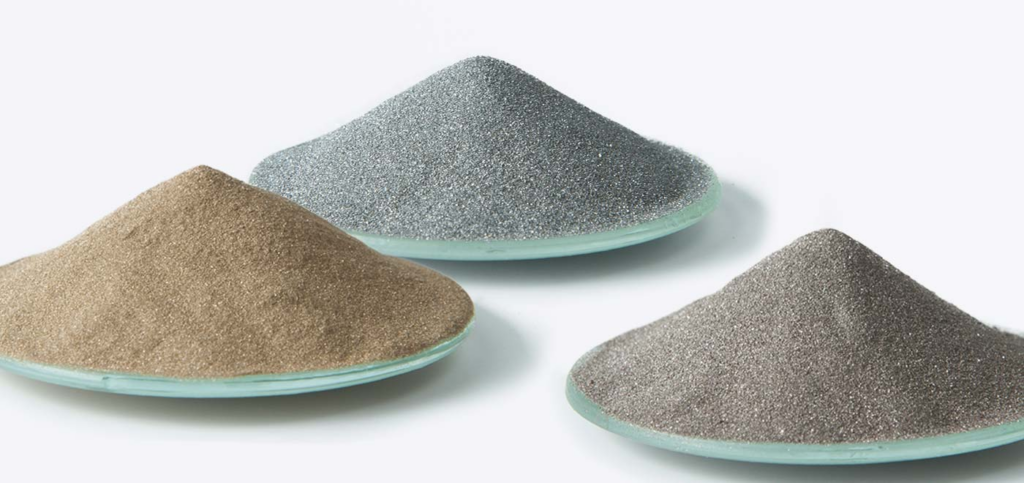
8. Conclusion
Inconel additive manufacturing has revolutionized the production of complex components with exceptional material properties and performance. With its advantages in the aerospace, automotive, medical, and oil and gas sectors, Inconel additive manufacturing is enabling manufacturers to create lightweight, high-strength parts with intricate geometries. Despite the challenges posed by material properties, process complexity, and quality control, advancements in Inconel additive manufacturing technologies, such as Laser Powder Bed Fusion (LPBF), Electron Beam Melting (EBM), and Directed Energy Deposition (DED), have paved the way for more efficient and reliable production.
Looking ahead, the future of Inconel additive manufacturing holds exciting possibilities. Researchers and industry experts are actively working on overcoming the current limitations and exploring new applications. Hybrid manufacturing techniques, improved process simulation tools, and advancements in post-processing and surface finishing are among the areas of focus. As these developments continue to unfold, Inconel additive manufacturing is expected to bring about further advancements and transformations across industries.
FAQs
1. What is Inconel additive manufacturing? Inconel additive manufacturing refers to the process of using 3D printing technology to fabricate components using Inconel alloys. It enables the production of complex, high-performance parts with exceptional material properties.
2. What are the advantages of Inconel additive manufacturing? Some advantages of Inconel additive manufacturing include the ability to produce lightweight, high-strength components, design freedom, reduced waste, increased customization, and improved efficiency in various industries.
3. What industries benefit from Inconel additive manufacturing? Inconel additive manufacturing finds applications in industries such as aerospace, automotive, medical, and oil and gas. It is particularly beneficial for producing components that require high strength, heat resistance, and corrosion resistance.
4. What are the challenges of Inconel additive manufacturing? Challenges in Inconel additive manufacturing include optimizing material properties, managing process complexity, and ensuring quality control. The unique characteristics of Inconel alloys require careful parameter selection and advanced monitoring techniques.
5. What are the future trends in Inconel additive manufacturing? Future trends in Inconel additive manufacturing involve hybrid manufacturing techniques, improved process simulation tools, and advancements in post-processing and surface finishing. These developments aim to overcome limitations and expand the range of applications.