Tungsten is a rare and refractory metal with a melting point of 3,655 K. Tungsten and its alloys have excellent properties such as high density, high temperature strength, high melting point, good heat and corrosion resistance and high hardness, and are widely used in many fields such as atomic energy, medical, defence, military and aerospace. In manufacturing, tungsten and its alloys are often prepared using traditional powder metallurgy processes, i.e. through the forming, sintering and post-treatment of tungsten powder. The morphology, particle size and size distribution, fluidity and bulk density of the tungsten powder have a significant impact on the performance of the pressed billet and therefore the performance of the final tungsten product. Spherical tungsten powders are spherical or nearly spherical in shape and are characterised by good flowability and high bulk density. This makes it easy to uniformly fill the mould cavity, and the size of the billet can be easily controlled under pressure, resulting in a uniform density distribution and low elastic after-effects.
With the rapid development of 3D printing technology, porous materials, high-density powder coating and injection moulding, the demand for high quality spherical tungsten powder is increasing. High-quality spherical tungsten powder not only has good flowability, good sphericity, high loose packing density and vibrational density, but also low oxygen content.
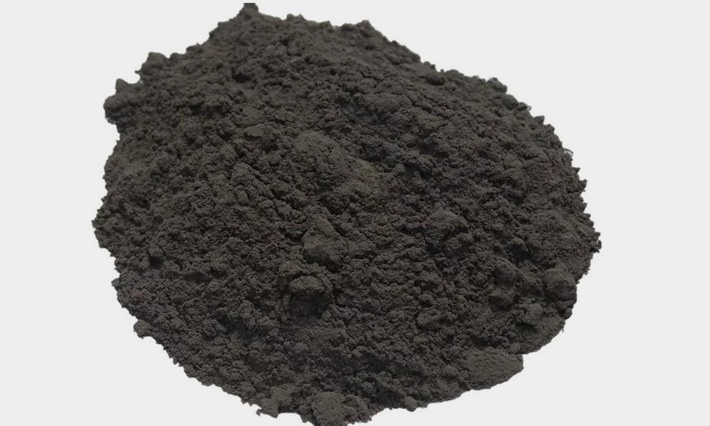
Plasma Spheroidisation of Tungsten Powder
Plasma, with its high temperature, high enthalpy and high chemical reactivity, meets the demand for a heat source for tungsten powder spheroidisation in the tungsten powder spheroidisation process. Plasma spheroidisation technology involves the spraying of irregularly shaped particles by a carrier gas through a charging gun into a plasma arc. Under the action of heat transfer mechanisms such as radiation, convection and conduction, the powder is rapidly heated to whole or partial melting, and the molten particles rapidly solidify and shrink under surface tension to form a dense spherical powder. The advantages of plasma spheroidised tungsten powder are the high concentration of energy, the large temperature gradient, the ability to precisely control the energy input by controlling the process parameters and the thermal energy utilisation of up to 75%. After plasma spheroidisation, the fluidity of the tungsten powder is improved and the loose packing density and vibrational density of the powder are increased. The most commonly used method for the preparation of spherical tungsten powder is RF plasma, which uses the induction of the RF electromagnetic field to produce plasma by induction heating of various gases, with a significant increase in electrical conductivity and high energy Joule heating under the action of the alternating induction electric field. It is a good way to prepare high quality spherical tungsten powders as it not only has the characteristics of a normal plasma, but also has low RF plasma speed, long arc area, long plasma torch life, no electrode discharge, low pollution, and a power range from 0.5 kW to 1.0 MW.
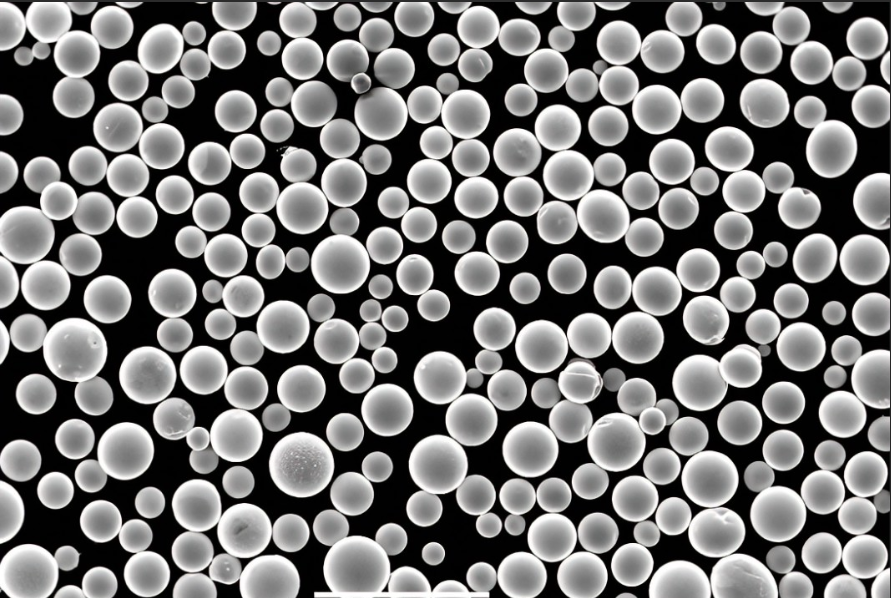
As the most important consumable for 3D printed tungsten products, spherical tungsten powder has its unique advantages to replace conventional tungsten powder. Halogenation, tungsten powder reoxidation- reduction methods have low spherification rate, low yield and The microwave single cavity method of spheroidizing tungsten powder is not sufficient as a heat source, and the powder can be made into a spherical powder. The microwave single cavity method of spheroidizing tungsten powder has insufficient heat source, and the performance of the tungsten powder produced is unstable and poorly consistent.
At present, the spherical tungsten powder prepared in China still suffers from a wide particle size distribution, low yield, poor uniformity, and a high degree of stability. The research and development of spherical tungsten powder is still in the development stage. The research and development of spherical tungsten powder is still in the development stage, and the preparation process, technology and procedure still need to be further studied. The research and development of spherical tungsten powder is still in the development stage, and the preparation process, technology and procedure still need further study.
The plasma spheroidization technology is characterized by high energy consumption, gas consumption high energy consumption, gas consumption, large investment in equipment, high operating costs, immature technology development and other problems. However, the high energy of the plasma and the controllable reaction atmosphere enable the preparation of other The plasma spheroidisation technique has the problems of high energy consumption, high equipment investment, high operating costs and mature technology development. The prepared The prepared spherical tungsten powder has good sphericity, uniform particle size distribution, high densities and good fluidity. The whole preparation process is fast and continuous. Therefore, plasma spheroidization will be an alternative for the preparation of spherical tungsten powder. Therefore, plasma spheroidization is an alternative for the preparation of spherical tungsten powder. In combination with numerical simulations, the process parameters can be The process parameters can be optimised quickly by combining numerical simulations. With the continuous improvement of plasma spheroidisation technology, the reduction of production costs and the optimization of powder parameters With the continuous improvement of plasma spheronization technology, the reduction of production cost and the increase of powder yield, plasma spheronization technology will play an important role in the production of tungsten powder. The plasma spheroidisation technology will have a bright future in the industrial production of tungsten powder spheroidisation.